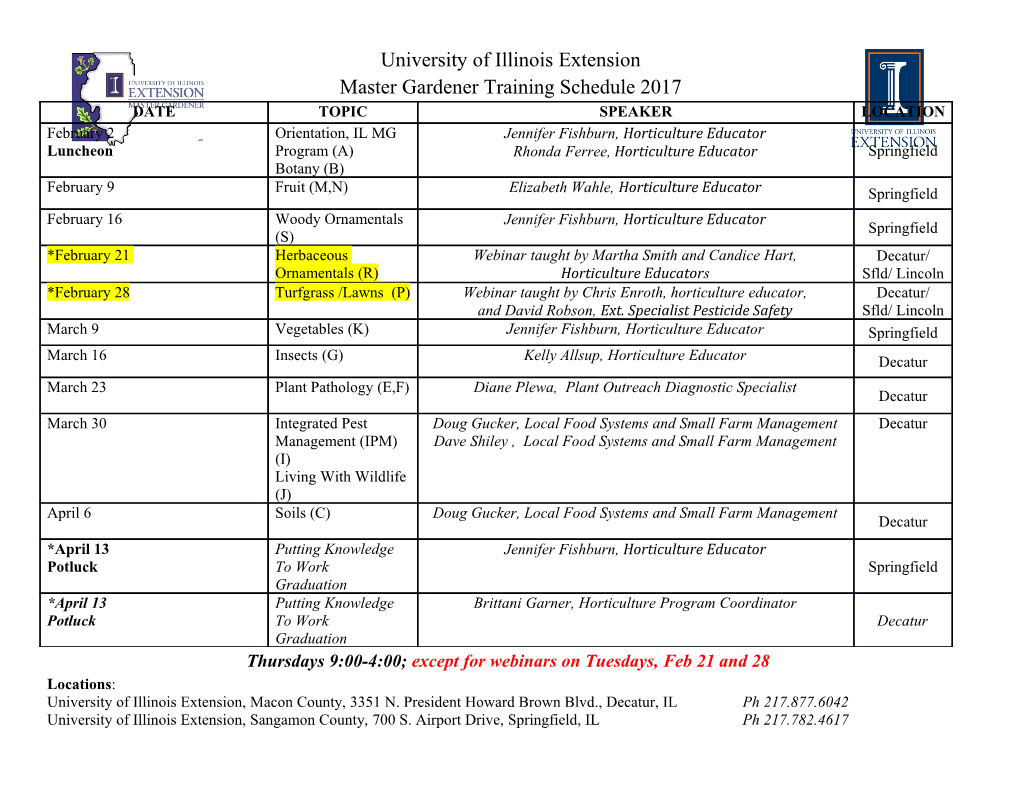
MODELLING OF IRON LOSSES OF PERMANENT MAGNET SYNCHRONOUS MOTORS Chunting Mi A thesis submitted in confollILity with the requirements for the Degree of Doctor of Philosophy in the Department of EIectncal and Computer Engineering University of Toronto O Copyright by Chunting Mi, 200 1 The author has pteda non- L'auteur a accordé une Licence non exclusive licence dowing the exclusive permettant à la National Li* of Canada to Bibliothèque nationde du Canada de reproduce, Ioan, distnbute or sell reproduire, prêter, distriilmer ou copies of this thesis in microform, vendre des copies de cette thèse sous paper or eIectronic formats. la forme de microfiche/film, de reproduction sur papier ou sur format electronique. The author retains ownership of the L'auteur conserve la propriété du copyright in this thesis. Neither the droit d'auteur qai protège cette thèse. thesis nor substantial extracts fiom it Ni la thèse ni des extraits substantiels may be printed or otherwise de celle-ci ne doivent être imprimés reprodnced without the author's ou autrement reproduits sans son pdssi01l. autorisation. MODELLING OF IRûN LOSSES OF PERMANENT MAGNET SYNCHRONOUS MOTORS Chunting Mi A thesis submitted in conformity with the requUements for the De- of Doctor of Philosophy in the Department of Electrical and Computer Engineering University of Toronto @ Copyright by Chunting Mi, 200 1 ABSTRACT This thesis proposes a refïned approach to evaluate iron losses of surface-mounted permanent magnet (PM) synchronous motors. PM synchronous moton have higher efficiency than induction machines with the same &me and same power ratnigs. However, in PM synchronous motors, iron Iosses form a larger portion of the total losses than in induction machines. Therefore, accurate calculation and .* - muimuzation of iron losses is ofparticular importance in the design of PM synchronous motors. Aithough time-stepped FEM can provide good estimations of iron Iosses, it requires hi& effort and is very time-consmning for most designs and particularly for optimidons. Besides, FEM anaiysis can oniy be performed afta the machine geometrical dimensions have .* Tl been detexmined. In contras appmximate anaiyticai loss mode1 yields qyick insight while requiring much les computation time and are readily available du~gthe prelhinary stage when the motor design is being iterated. Therefore, it is desirable to develop iron loss models that produce an acceptable prediction of the ovedi im losses in a relatively simple way and provide machine designers a more reliable method to estimate iron losses in the initial design of PM machines. In this thesis, simplined models for the estimation of tooth and yoke eddy current losses are devdoped based on the observations of FEM results and anaiyticai analyses of the magnetic fields taking into account detailed geometrical effects. The effectiveness and limitations of the models are investigated. Correction factors are derived for geomehical Muences. The nature of the flux density waveform has great impact on iron losses. Therefore, reduction of iron Iosses cmbe achieved by properly shaping the magnets, designing the dots and choosing appropriate number of poles. Some guidelines are provided to minimize iron losses of PM synchronous motors. In order to test the proposed simplifieci loss models, measurements were performed on two dace-mounted PM synchronous motors. Puticular attention was focused on the measmement of PWM wavefoms and decomposition of no-load losses. Eqcrimental dts of the two motors codbmed the validÏty of the proposed iron loss models. 1 am etemally grateful to my supervisors, Professor G. R Slemon and Professor R Bonert, for their invaluable guidance, encouragement and financiai support throughout the period of my course study and thesis research, TheY attitude, entbusiasm and dedication towards scientSc research deeply influenced me and will benefit for al1 rny Me. 1 sincerely th& Professor Lavers and Profesor Dawson for their precious suggestions and technical discussions. 1 am also thaWto Dr. KV.Namjoshi for spending much of his spare time reading the draft of my thesis and giving me a lot of advice. Specid thanks are due to the leaders and feiIows at Xi'an Petmleum Mtute for granting me the opportunity to study abmaci. The author also wishes to extend his gratitude to his Master's thesis supervisor Professor Jiang Zongrong, one of the pioneers in the field of rare-earth PM machines, for his excellent quality of teaching. Special appreciation goes to my wife Yuhong for her undetsfalldmg and support during my Ph.D studies- This thesis is aiso a gift to my lovely daughter Shishi for the many sacrifices she deredduring the years of my research work. This thesis is also dedicated to my parents and my parents-blaw for their understanding, encouragement and mental support. The hancial supports hm the Ontario Graduate Scholmhip for Science and Technology (OGSST), the University of Toronto S.G.S Intemational Student Award, the University of Toronto Doctorkd Feiiowships and Ontario Shrdent Assistant Program (OSAP), are gratefully acknowledged. CONTENTS CONTENTS ............................................................................................................................eV Chapter 1 Introduction .........m....,b...e~~..~.a..~~~~.~~~~~~~~..~.............a.a........a..~m.~mm..........e......ea..1 1.1 Thesis Objectives .................. .....*.*.*..................*.*.*.......*.................................1 1.2 Thesis Outline........................................................................................................... 3 Chapter 2 Iron Losses and TimeStepped FEM of PM Synchronous Motors ........ ., ...-5 2.1 PM Synchronous Motoa ..........................................................................................5 2.2 Iron Losses in PM Machuies .................................................................................... 8 2.3 Finite Elment Method of Electromagnetic Field hblems .................................. 10 2.3.1 Maxwell's Equations ...................................................................................... 10 2.3.2 The Magnetic Vector Potential ......................................................... 11 2.3.3 Two Dimensional FEM Formulation of Magnetostatic Roblems ................. 12 2.3.4 Magnetization ModeIs of Magrets............................................................... 14 2.4 Time-Stepped FE'of PM Synchronous Motors................................................... 15 2.401 C0mcti0~1of Meshe~......+~~~........................................................................ 15 2.4.2 Boundary Conditions ..................................................................................... 15 2.4.3 Examples Used in the Thesis .. ...................................................................+...17 2.5 EvaIuation of Iron Losses with FEM~.~~o.****-.*.--.----*---ti--------*---~~-.~-~~~~~~-~~~--~~---~-~-.+-*r23 2.5.1 Eddy CumtLoss .......................................................................................... 23 2.5.2 Hysteresis Los............................................................................................... 24 Chapter 3 Shpiified Lroa Loss Mode1 ........... ..................................................................... 25 3.1 Review of Analfical Iron Loss Mode1 .................................................................. 26 31Test of Linear Waveforms of Tooth Flux Density ................................................. 27 3.3 SimpIified Tooth Eddy Cment Loss Model .......................................................... 34 3.3.1 Eddy Current Loss Induced by the Nomial Component ................................ 34 3.3.2 Effect of SIot Closure .....................................................................................35 3.33 Effect of Magnet Width ................. .......... ...............................................38 3.3.4 Effect of Slots Per Pole Per Phase with Fked Slot Pitch............................... 42 3.3.5 Effect of Airgap Length and Magnet Thiclmess ................... .............. 46 3.3.6 Effect of SIots Pet Pole Per Phase with Fixed Pole Pitch ............................ -47 33.7 Effect of Tooth Width with Fixed Slot Pitch .............................................. 50 33.8 Eddy Current Loss Induced by Circderential Component ......................... 51 3.3.9 Simplified Expression of Tooth Eddy Current Loss ...................si.................C53 3.3.10 Case Studies on Tooth Eddy Currait Loss ................... ... ....................... 54 3.4 Wavefoms of Yoke Flux Density ............ .... .................................................. 59 3.4.1 Waveforms of the Longitudinal Component of Yoke FIux Density ..............59 3 .4.2 Waveforms of the Normal Component of Yoke Flux Dnisity .................... ..64 3.4.3 Anaiytical Solutions to Yoke Flux Density ...................................................65 3.5 Simplified Yoke Eddy CmtLos Mode1.......................................................... 69 3.5.1 Eddy Current Los Induced by the Longitudinal Component .......................69 3.5.2 Effect of Slot Closure ..................................................................................... 70 3.5.3 Efféct of Magnet Coverage ............................................................................ 71 3.5.4 Effect of SIots Per Pole Per Phase.................................................................. 72 3.55 Effect of Magnet Thickness ..........................................................................
Details
-
File Typepdf
-
Upload Time-
-
Content LanguagesEnglish
-
Upload UserAnonymous/Not logged-in
-
File Pages148 Page
-
File Size-