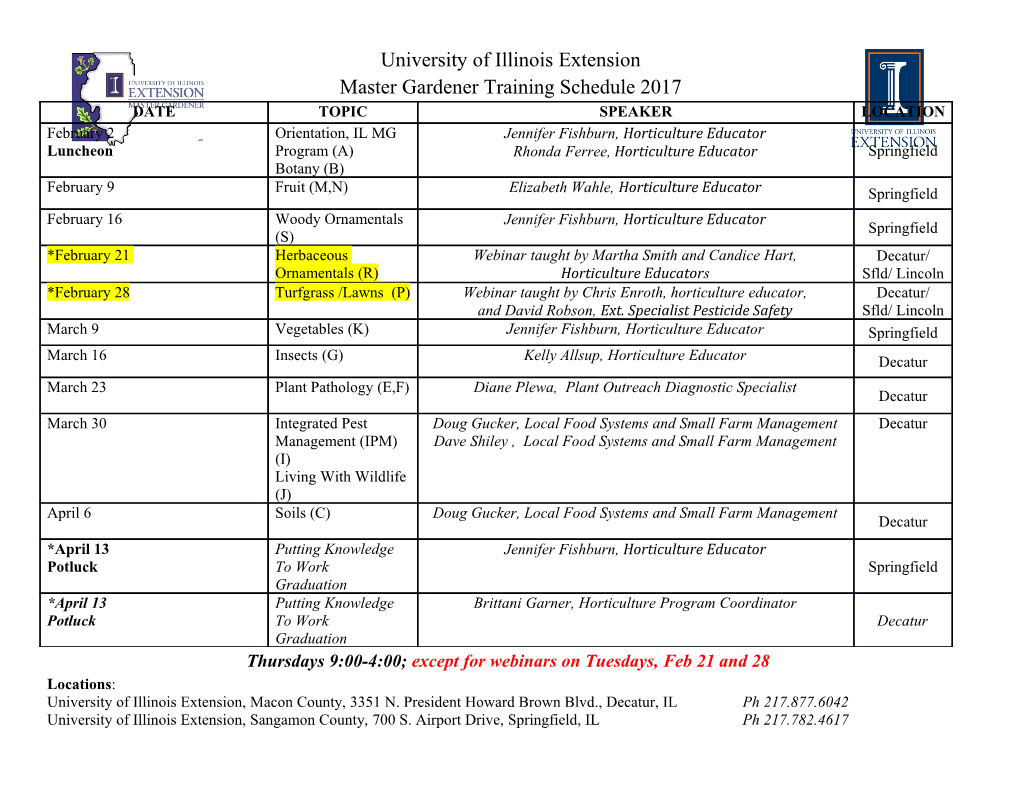
LEAN PRODUCTION IN A WORLD OF UNCERTAINTY: IMPLICATIONS OF VARIABLE DEMAND Prepared for Jerry Gabriel Instructor, Engineering Communications Program Jack Muckstadt Professor, School of Operations Research & Industrial Engineering Prepared by Diana Coggin Student, School of Operations Research & Industrial Engineering December 15, 2003 College of Engineering, Cornell University Ithaca, NY 14850 © 2003 Diana Coggin Table of Contents List of Figures................................................................................................................................iii 1. Introduction................................................................................................................................. 1 2. Methodology............................................................................................................................... 2 3. Discussion................................................................................................................................... 2 3.1. Background to Lean Production Systems............................................................................ 3 3.1.1 Principles........................................................................................................................ 3 3.1.2 Takt ................................................................................................................................ 4 3.1.3 Pull ................................................................................................................................. 5 3.2. Implications of Variable Demand........................................................................................ 7 3.2.1 Common Challenges...................................................................................................... 7 3.2.2 In-Depth Example: Velocity Manufacturing ................................................................. 8 3.3 Proposed Solutions.............................................................................................................. 10 3.3.1 Recommendations to Velocity and Implemented Transformations............................. 10 3.3.2 Volume and Variability Demand Analysis.................................................................. 13 3.3.3 Continuous Improvement - Beyond Factory Walls ..................................................... 17 4. Conclusion ................................................................................................................................ 19 List of References ......................................................................................................................... 20 Glossary ...................................................................................................................................... G-1 Appendices.................................................................................................................................. A-1 Appendix A. Volume-Variability Analysis of Velocity’s Parts ............................................. A-1 Appendix B. Customer Demand Analysis for Velocity Part Number 1................................. A-4 ii List of Figures Figure 1: Takt Time at Boeing 4 Figure 2: Push versus Pull System and Resulting Reduction in Inventory 6 Figure 3: New SKU Classification Based on Demand Volume and Variability 14 Figure A1: Velocity Part 1 - High Volume, Low Variability A-1 Figure A2: Velocity Part 7 – High Volume, High Variability A-2 Figure A3: Velocity Part 12 - Medium Volume, Medium Variability A-3 Figure A4: Velocity Part 59 – Low Volume A-3 Figure B1: Velocity Part 1 Demand, Customers 1 A-5 Figure B2: Velocity Part 1 Demand, Customers 1, 2, 4 A-6 Figure B3: Velocity Part 1 Demand, Customers 3 and 5 – 22 A-6 iii 1. Introduction American engineer and acclaimed inventor, Charles F. Kettering, once said, “The world hates change, yet it is the only thing that has brought progress.” Countless changes have taken place in the business environment during recent decades, including globalization, the technology boom, and the paramount importance of customer satisfaction in increasingly competitive markets. Whereas yesterday’s manufacturers could expect to sell massive amounts of standardized products manufactured at their convenience, customer demands today are much more stringent. Companies now must meet higher standards on quality, customization, and timely delivery to customers who are now accustomed to conducting business at Internet speed. Companies must meet these and other requirements while maintaining the lowest possible cost in order to avoid losing customers to the competition. Throughout these times of change, however, the goal of any company has remained the same: to make a profit and to stay in business. Numerous companies throughout the world have adopted an innovative production philosophy called Lean Production or World-Class Manufacturing in order to survive in today’s competitive markets. The goals of Lean Production, or simply Lean, are multifaceted, but its main goal is, “to get one process to make only what the next process needs when it needs it [and] to link all processes – from raw material to final consumer” [1]. The principles of Lean are based on continuous improvement and the minimization of defects, inventory, and non-value added time. If implemented correctly, the Lean approach provides for increased throughput, return on assets and, most importantly, profit. The success of Lean implementation, however, requires specific attributes of the manufacturing environment and the enterprise in which it exists. Primarily, because Lean attempts to match production rates with marketplace demand and requires processes engineered accordingly, lean systems are biased towards demand that is consistently level. However, many industries have demand rates that vary from season to season or even daily, and such variable demand can have numerous negative consequences on lean systems. According to Panizzolo, “The lean production system is fundamentally a fragile system, in which slight perturbations or deviations from the working conditions planned for can seriously affect system performance” [2]. Many companies that have invested significant amounts of time and money in Lean have experienced the detrimental effects of such deviations. The purpose of this 1 research paper is to present examples of how variable customer demand often undermines the mission of Lean Production Systems, and to explore potential solutions that may assist companies with variable demand in sustaining their competitive advantage. 2. Methodology My first goal in researching this problem was to get a firm understanding of Lean Production Systems. In order to do so, I have utilized widely cited resources written by experts in Lean and its implementation, which I obtained through Cornell University Libraries and Yale University Library. Online journals like the International Journal of Production Economics and Supply Chain Management Review have been instrumental in my search for recent challenges and developments in manufacturing and supply chain. I have also utilized Google.com as well as other public search engines to find information on specific companies and their initiatives. Furthermore, I have gained a substantial amount of knowledge from my course in design of manufacturing systems and the discussions I have had with my professors, Jack Muckstadt and Peter Jackson, both experts in the world of Lean. In this course, we have examined the Velocity Manufacturing Company, a real company protected by a fictional name, and we have experienced first-hand the challenges and consequences it has faced through a simulation of its shop-floor environment. Furthermore, I have worked with a team of peers to serve as a consulting firm with the goal of redesigning Velocity’s entire business strategy for the next five years. This class has provided me with an in-depth perspective on one company that has implemented Lean principles and undergone various challenges due to unpredictable customer demand. 3. Discussion I will begin by discussing Lean in further detail and examine the reliance on level-loaded demand. Next, I will examine common consequences of variable demand and give specific examples of lean companies that have faced such challenges. Finally, I will present potential 2 solutions to these challenges, including implemented practices and recently proposed strategies that may enable companies to meet unpredictable customer demand more successfully. 3.1. Background to Lean Production Systems As mentioned above, Lean is essentially characterized by doing more with less. However, Lean is a philosophy that goes beyond merely a method of inventory management and production control. Lean is based on a set of key principles, and Lean systems utilize a measurement tool called takt time, and a manufacturing strategy based on the pull system. 3.1.1 Principles Beginning with the acclaimed Toyota Production System and related operational modes of Just- In-Time (JIT) delivery and production scheduling, Kaizen (continuous improvement), and Kanban (visual signals utilized in a pull system), Lean has evolved and essentially embodies the spirit and approaches of all of these movements [3]. Womack et al. contend that “Lean thinking can be summarized in five principles: precisely specify value by specific product, identify the value stream for each product, make value flow without interruptions, let the customer pull value from the producer, and pursue
Details
-
File Typepdf
-
Upload Time-
-
Content LanguagesEnglish
-
Upload UserAnonymous/Not logged-in
-
File Pages32 Page
-
File Size-