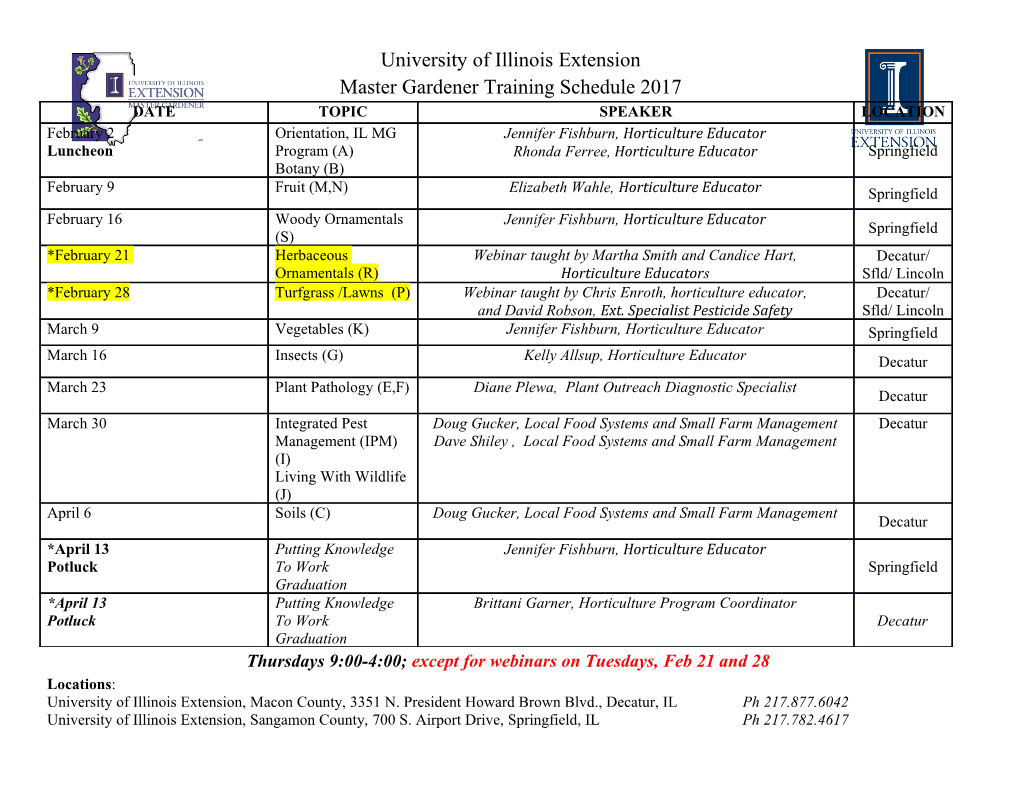
Vol. 56 Issue 1 Vol. THE SHIPBUILDER THE SHIP BUILDER Vol. 56 Issue 1 THE SHIPBUILDER ▶ Contents CONNECT WITH NASSCO 04 08 10 12 16 Messages NASSCO PDP PROFILES PERFORM CONTINUOUSLY From NEWS EVERY DAY IMPROVE The Helm BRIEFS The Shipbuilder Manager of Public and Government Relations: Dennis DuBard Senior Communications Specialist: Staci Ignell Communications Specialist: Xenon Alidag Content Layout: Jacqueline Ruiz 18 28 30 32 COVER Published by General Dynamics NASSCO Communications Department, P.O. Box 85278, San Diego, CA 92186-5278. Spring 2016. Direct comments to Dennis DuBard at [email protected] or Staci Ignell at [email protected] EMPLOYEE NASSCO In The SHIPYARD NASSCO- NASSCO SHIPBUILDERS Contributors: Nydia Ortiz-Avendano, Greyson Bailey, Hugo Bermudez, Lila Casora, Keith Cobb, Allyson Darroch, Lary Duby, Sandi Dunkel, Sherry CORNER community VISITORS NORFOLK INSTALL NON-SKID ABOARD Eberling, Larry Ehmer, Valerie Fusco, Dave Hastings, Samantha Huerta, Anthony Jemison, Beth Korkuch, Mark Lendy, Bob Liddell, Keith Londot, Megan THE USS AMERICA McLaughlin, Zach McWaters, Tony Muniz, Steve Murray, Petia Pavlova, Allison Pierson, James Pope, Lisa Root, Bryan Ruiz, John Russell, Steve Severs, Zach NEWS Sharpe, Clint Spivey, Katie Urbas, Duke Vuong, Mike Wagoner. 2 3 THE SHIPBUILDER ▶ MESSAGES FROM THE HELM Message From The PresidentFrederick J. Harris Message From The GeneralKevin manager M. Graney Our workload has largely stabilized Quality In February, the Navy’s Chief of Naval Operations, Admiral John Richardson, stopped by our following the historic delivery of In 2015, while we were working hard to deliver three lead shipyard in San Diego to learn more about our current work in both new construction and repair. three lead ships, and for 2016, ships, our quality suffered. While the finished product we We also enjoyed a visit from Admiral Scott Swift, commander of the U.S. Pacific Fleet. Visits like we are focused on getting back delivered to our customer was consistent with our reputation these are so critical; they serve as an opportunity for us as shipbuilders and designers to showcase the to basics when it comes to safety, as a high-quality yard, it simply took too much time, effort and extraordinary concepts and capabilities of the ships we proudly build for the Navy. quality, schedule, and cost. money to make it that way. This year, we are making quality a key part of our performance measures and have established In 2015 our new construction side of the business made headlines and history. We successfully 2015 was a busy year for us. a goal of cutting rework, our measure of quality – in half delivered the world’s first containership to be powered by liquefied natural gas – and we delivered two Demand for ships was sparked on the ECO program. This goal requires each of us to think other lead ships: the Lone Star State (ECO 1) and the USNS Lewis B. Puller (T-ESB-3). from the significant increase in about the product we deliver to our customers. If you work in the transportation of crude, the Steel, then your customer is the Outfitting and Steel Erection Equally important to the new construction we perform for commercial and government customers is our repair side of the blossoming of the shale oil industry, and the deadline for teams. If you work in Engineering, then your customer is the business. meeting Tier 2 EPA emissions requirements. As a result, Planning and Production teams. our backlog of ships to build has grown and we are now With four locations on both coasts of the United States, our repair operation is currently working 26 ships in 12 locations in challenged to fulfill our nation’s maritime transportation needs I am pleased to see that quality is improving. At least weekly, four ports, including the USS Pearl Harbor, USS America, USS New York, and USS Gunston Hall. Other key availabilities include – a task we are well-equipped to meet. But, we cannot be I review the metrics in Steel and Outfit. We are experiencing work on the USS Lake Champlain, USS Cape Saint George, USS Milius, USS Nimitz, USS Freedom, USS Fort Worth, USS Mitscher, satisfied with good enough. better inspection performance, with fewer defects per USS Coronado, USS Whidbey Island, USS Boxer, and the USS Essex. inspection. Our weld quality is steadily improving and we are As we “spring” into 2016, allow me to provide you with some seeing improved levels of completion on each of the blocks For 2016, it’s the ‘Drive to Five’ – meaning let’s get our safety incident rate down to 5.0. The goals we have established for insight into what our “must have’s” are for the year: and ships we are building. We are also making hard decisions 2016 are aggressive yet achievable and this year our Safety Department will be focusing on our Safety Roadmap that leads about when to send a product, like a block, from one stage of to a Total Safety Culture, including our commitment to get ‘Back to Basics.’ Each employee maintains the responsibility of Safety construction to the next. If it is not complete, we are going to themselves—and their coworkers—so let’s all make it our number one priority to work safely every single day. I will never stop talking about the importance of working take the time to get it right. In our every day work, we must safely. We can never be satisfied in this area because people’s ask ourselves “Am I proud of the product I just made? Is it Our communications team is working hard to keep everyone informed of shipyard happenings, upcoming events and lives and their livelihood are at risk. complete?” If the answer is “no,” then we must do better. initiatives. In addition to the quarterly editions of The Shipbuilder, information is readily available via our social media portals (Facebook, Twitter, Instagram, LinkedIn, and Vimeo) and our website, www.nassco.com. Just recently, we launched the All of us come to work to support our families and We must work together to improve the quality of our work, NASSCO Message Center, a text notification system for very important messages. For more information, see page 31. ourselves. This year alone, we have already seen people and to do so as efficiently as possible. In my view, quality is taking unnecessary risks to perform their job. In one case, all about pride. When we deliver our ships to our customers Work safely, a NASSCO employee was moving a 900 pound piece of we want to let them know that when we say this ship is equipment by himself and without the aid of a lifting device. proudly NASSCO made, that this reflects the high level The result: an injury to his foot and a damaged piece of of workmanship and skill that only you and NASSCO can Fred Harris equipment. In this case, the person was working alone with no provide. one around him. Imagine if he had taken that same risk with others in the area. We could have had multiple people seriously Schedule injured. We must always think about our actions, and the This year we will remain focused on the performance of our actions of those around us. If you see people taking risks with ECO program. We have learned a great deal from our lead their own safety, then guess what? They are taking risks with ships, and sometimes the best lessons learned come from YOUR safety. Don’t let it happen! challenges that are the hardest to overcome. Today, as I write this, the yard is on schedule. We are starting to see a dramatic This year we are reinvesting in our Total Safety Culture (TSC). shift in performance as a result. While Hulls 552 and 553 will The leadership team and our ASIG groups are being proactive continue to challenge us, the real opportunity we have is on in making sure everyone relearns the behaviors that have made Hulls 554 through 558 – the back half of the ECO program. us one of the safest shipyards in the country. We are taking This opportunity will come easily if we stick to the plan and the time to re-train ourselves on Levels 1 and 2 of the TSC execute to the schedule. Roadmap and we are already seeing improved performance over last year. Remember, we still have many people who I am particularly energized about recent developments in the are new to our business that need to be taught about our steel organization where we have implemented a new commitment to safety and to each other. Our safety mantra approach to planning and executing our work. SOC 1, 2 and 3 for this year is “Drive to 5.” This represents a safety incident rate that is 15 percent better than what we saw in 2015. (Continued on page 7) 4 5 THE SHIPBUILDER ▶ (Continued from page 5) relate to cost. The less March 2016: Shipbuilders from SOC 3 outfitting and SOCs 4 & importance we give to each 5 celebrated the completion of the last block for the Garden are performing more of them, the more cost we State (Hull 554) on a rare foggy day in san diego. efficiently than they have incur. ever performed on the ECO program, and this Safety, quality, schedule, new approach represents a and cost all fall within our fundamental shift in the way strategic goals – especially we control our work. We continuous improvement. have implemented a process The goals for 2016 are out, where the production and hopefully now you have supervisors apply their a better understanding of expertise to plan how each our focus for continuous block will be attacked, the improvement.
Details
-
File Typepdf
-
Upload Time-
-
Content LanguagesEnglish
-
Upload UserAnonymous/Not logged-in
-
File Pages19 Page
-
File Size-