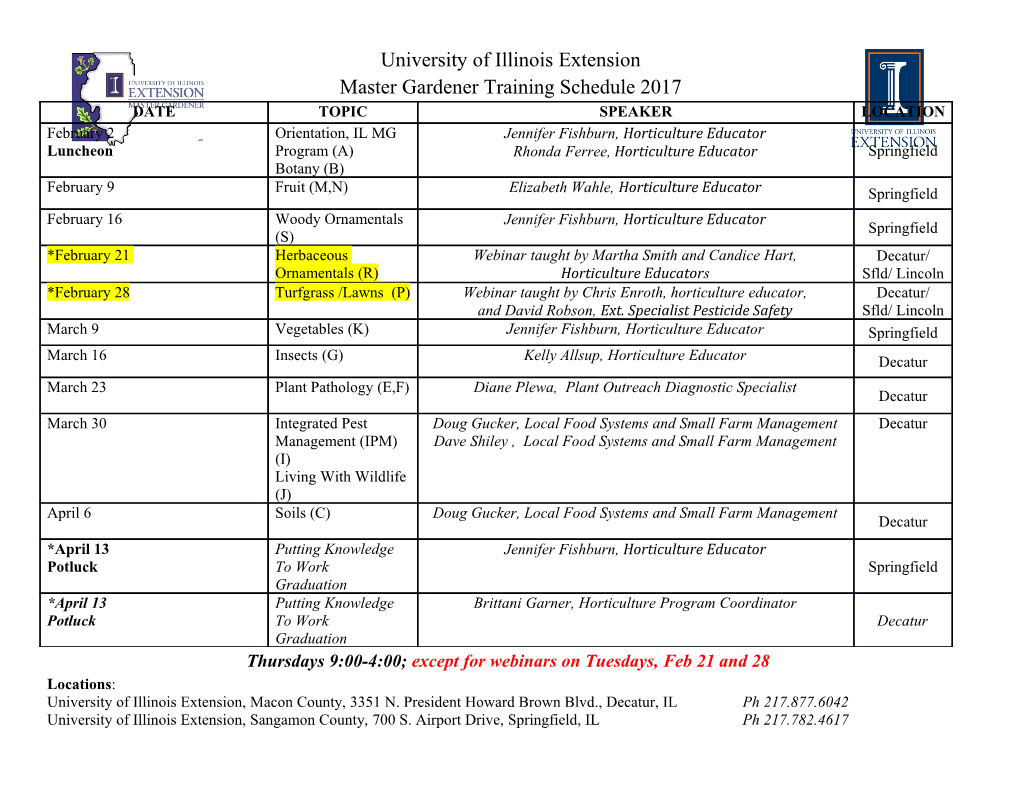
Federation for Advanced Manufacturing Education TAMAR JACOBY FEBRUARY 2019 1 2 Federation for Advanced Manufacturing Education INDUSTRY-DRIVEN APPRENTICESHIP CASE STUDY TAMAR JACOBY FEBRUARY 2019 3 4 ABOUT THE AUTHOR Tamar Jacoby is president of Opportunity America, a Washington-based nonprofit working to promote economic mobility—work, skills, careers, ownership and entrepreneurship for poor and working Americans. A former journalist and author, she was a senior writer and justice editor at Newsweek and, before that, the deputy editor of The New York Times op-ed page. Her articles have appeared in The New York Times, The Wall Street Journal, The Washington Post, The Weekly Standard and Foreign Affairs, among other publications. She is the author of “Someone Else’s House: America’s Unfinished Struggle for Integration” (Free Press, 1998). Her edited volumes include “Reinventing the Melting Pot: The New Immigrants and What It Means To Be American” (Basic Books, 2004) and “This Way Up: New Thinking About Poverty and Economic Mobility” (American Enterprise Institute, 2017). Since 2008, she has also been president of ImmigrationWorks USA. ABOUT THE ORGANIZATION Opportunity America is a Washington-based nonprofit promoting economic mobility—work, skills, careers, ownership and entrepreneurship for poor and working Americans. The organization’s principal activities are research, policy development, dissemination of policy ideas and working to build consensus around policy proposals. ACKNOWLEDGEMENTS Opportunity America thanks the managers, instructors and trainees we spoke with at the Federation for Advanced Manufacturing Education who helped us understand independent apprenticeship programs and the skills standards on which they are based. Special gratitude goes to the Annie E. Casey Foundation for its generous support of this project. 5 6 PREFACE Changing technology, growing skills mismatches Among the most important findings of that and weak wage growth are drawing attention to broader study: newly available data from the US the need for more sophisticated, more relevant Department of Education’s 2016 Adult Training career and technical skills, especially for workers and Education Survey (ATES) suggest that about who lack a four-year college degree. Among the same number of American workers have the most effective ways to raise skill levels and participated in unregistered earn-and-learn prepare workers for rewarding careers is with training as in registered apprenticeship programs. apprenticeships that combine classroom learning and paid on-the-job experience, teaching skills Like registered programs, independent offerings in demand across an industry. Yet it has proven appear to be common in the construction surprisingly difficult to scale apprenticeship in the trades, but also an array of other industries. United States. Some are fostered and supported by national industry associations; others arise spontaneously, In 2018, just three-tenths of one percent of US at the initiative of an enterprising employer. workers were enrolled in civilian apprenticeship Employers who participated in the study were all programs—about 450,000 apprentices, compared but unanimous in explaining why they chose to to nearly 20 million students in degree-granting offer unregistered earn-and-learn programs: the postsecondary institutions. flexibility it gave them to meet rapidly changing business needs. President Donald Trump aims to dramatically increase this number by encouraging industry This case study is one in a series of four groups to develop and oversee programs, standalone profiles of quality unregistered including in sectors that have not traditionally apprenticeship programs in industries where relied on apprenticeship training. An approach the approach may be particularly prevalent: of this kind would align with a long American construction, advanced manufacturing, health tradition of employer-sponsored, apprenticeship- care and automotive maintenance and repair. like training that is not registered with state or federal agencies. Yet little is known about these Independent earn-and-learn training is a great programs—how widespread they are, how and largely untapped opportunity: an effective effective or whether and how they maintain quality and, for employers, relatively accessible way to standards absent regulation by the government. upskill workers, improve the quality of jobs and This study begins to address that gap. increase productivity, while significantly expanding apprenticeship in the US. The case study that follows is part of a larger project—a paper by Tamar Jacoby and Urban The goal of the case studies and the paper is Institute fellow Robert I. Lerman that explores to explore this potential and propose how the the landscape of independent earn-and-learn nation can tap it for the benefit of workers and training, drawing on four case studies, a half- employers. day convening of employers and employer associations and lessons from other countries with robust apprenticeship systems to reflect on the Trump administration’s approach and offer recommendations for policy. 7 8 Federation for Advanced Manufacturing Education AT A GLANCE creating new jobs, often more demanding than The Federation for Advanced Manufacturing the positions they’re replacing: jobs for highly Education’s advanced manufacturing technician skilled and adaptable technicians, adept at (FAME AMT) program is a two-year earn-and-learn problem solving. Perhaps most challenging, says experience that prepares college-age and older FAME founder Dennis Dio Parker, most American students for careers as industrial maintenance entry-level technical workers are “underskilled workers. As in a classical apprenticeship, trainees and not work-ready,” lacking in soft skills and divide their weeks into time spent in class and analytic ability and not competitive with 5 time on the job, learning by doing and earning entry-level workers in Europe and Asia. competitive wages. The hallmark of the FAME model: employer collectives, each made up of Generally more skilled and better paid than 10 to 25 companies in a single regional labor ordinary production workers, industrial mainte- market, determine every aspect of the program nance technicians are responsible for keeping a and its delivery. manufacturing facility operational and efficient, avoiding disruptive breakdowns and expensive An offshoot of a training regimen developed over downtime. Duties include equipment installation, several decades by Toyota Motor North America testing, routine maintenance, preventive at its flagship Georgetown, Kentucky, plant, AMT procedures, troubleshooting and repair work. has been adopted by more than 300 companies across 11 states.1 Firms come together in Entry-level technicians can earn $40,000 to employer collectives and partner with community $50,000 a year. After three years, according to colleges to adapt a highly standardized curriculum FAME employers, many earn as much as $65,000 6 that combines technical training with employability or more. skills, problem solving and lean manufacturing practices. It’s a relatively small, elite program— BACKGROUND now some 400 graduates a year total—but growing, and leadership is exploring organizational The FAME AMT program evolved over nearly changes that would allow it to scale nationwide.2 three decades of trial and error by Toyota and other manufacturing employers.7 The Toyota Georgetown plant established its first prehire LABOR NEED training in the late 1980s, building on a company According to the US Bureau of Labor Statistics, culture that values personal behavior and lean 522,000 manufacturing jobs stand empty today.3 manufacturing practices as if not more highly than Over the decade ending in 2028, Deloitte and technical expertise. From the start, the curriculum the Manufacturing Institute predict the industry included employability skills and manufacturing will need to fill 4.6 million positions, and as many efficiency. Already in the early 1990s, the pro- as 2.4 million of them may go unfilled because gram was geared to produce what the firm called employers cannot find skilled workers.4 “multiskilled” technicians, proficient across four essential trades: electrical, fluid power, mechanics Yet according to Toyota and other FAME employers, and fabrication—a combination Toyota says can 8 these numbers tell only part of the story. A gener- reduce its workforce needs by up to one-third. ation of manufacturing workers is retiring. At many Also in the ‘90s, the company added an on-the-job firms, robotics and other new technology are component, supplementing classroom learning with work experience in the factory. 9 CASE STUDY FAME AMT In the early years, all training took place in-house: The idea spread quickly across Toyota North instruction paid for by Toyota, at Toyota, delivered America. Over the next few years, Toyota manu- by Toyota employees. facturing facilities in seven other states adopted the FAME model, recruiting nearby companies Three critical breakthroughs transformed the to form collectives. Soon, other employer groups program in the early 2000s. not anchored by Toyota plants were following suit, coming together with guidance from Parker and First, Toyota experimented with outsourcing its the Kentucky department of economic development prehire training, partnering with several Kentucky to establish independent FAME chapters. community and technical colleges to provide the academic portion of the multiskilled curriculum for a
Details
-
File Typepdf
-
Upload Time-
-
Content LanguagesEnglish
-
Upload UserAnonymous/Not logged-in
-
File Pages20 Page
-
File Size-