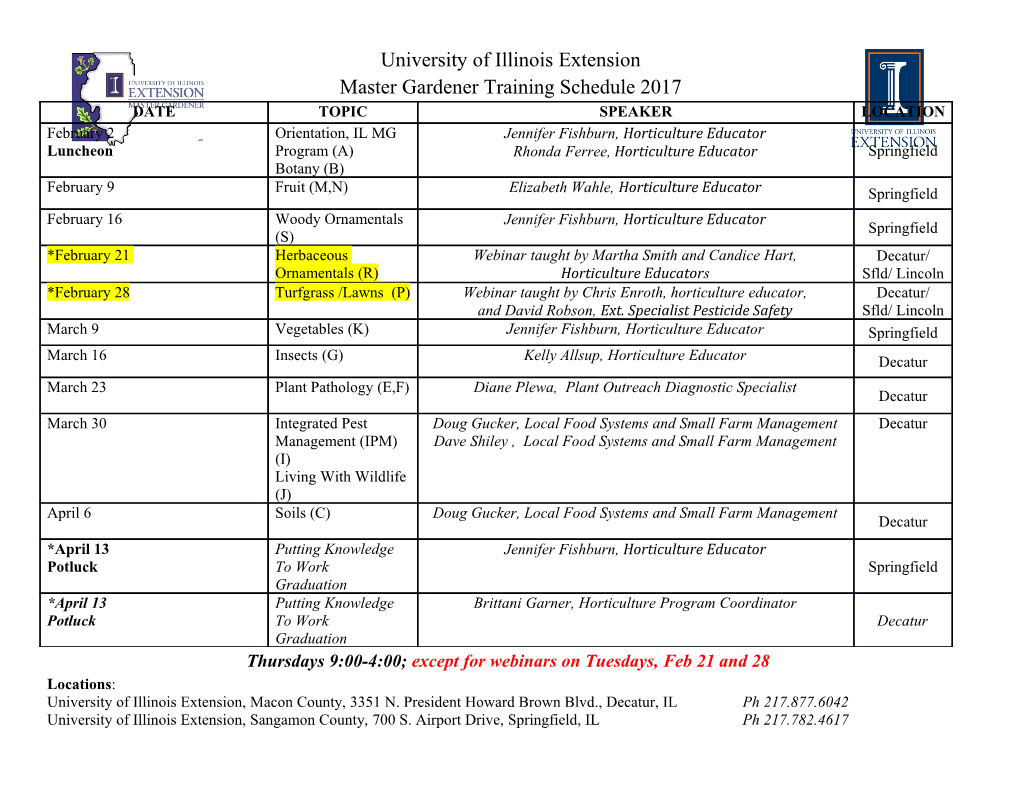
The Vanderbilt Concrete Canoe Design Project: The Little Engine that Canoed Stephen Schmitt School of Engineering of Vanderbilt University The Vanderbilt’s Concrete Canoe (VCC) Team has a competitive history at the Southeastern Regional ASCE Conference, placing in the top five schools throughout the past three years. The most recent concrete canoe project was named The Little Engine That Canoed in 2006 to honor Commodore Cornelius Vanderbilt’s origins in the railroad industry and as a reminder of the power of persistence. Developing The Little Engine was a small portion of the overall project objectives. The design team first compiled a significant body of literature that systematically outlined the steps for a successful concrete canoe project. The Little Engine boasts a fresh hull, three-dimensional finite element analysis, and an optimized concrete composite. The canoe construction efforts yielded a female mold, canoe carrier, and stands. Team members found the process of modeling the V-shaped bow and stern sections and a rounded stern stem to be the most challenging obstacles. Three-dimensional analysis was performed for the first time in school history and provided insight into graduate level coursework. Similarly, designing a concrete composite to withstand the rigors of competition required the use of a polymer to replace water in the concrete mix. To reach new heights, the team utilized a functional break- down structure. Teamwork and communication, in the face of limited manpower, resulted in performing over 800 man-hours of concrete canoe related activities during a two-year period. The 2006 Vanderbilt Concrete Canoe Hull Development (HD) Team envisioned The Little Engine that Canoed as the product of methodical research and design and creativity. Brainstorming sessions suggested remodeling Don’t Panic, the name of the previous year’s concrete canoe design project, to incorporate aesthetically pleasing Native American distinctions. The previous year’s team utilized an iterative design process, resulting in conservative geometric dimensions. Accordingly, optimization was desired. The HD Team assessed the advantages to be gained in all scoring divisions of the 19th Annual National Concrete Canoe Competition (NCCC), and proceeded to research and design an innovative hull for The Little Engine. Canoe design is considered more an art than a science. Design evolution has grown from experience unlike naval research, which guides ship development. This difference in design strategy does not neglect the fact that designs are governed by their use. Ship theory literature, past experience, and interviews with a commercial canoe designer led the research effort. Vanderbilt Undergraduate Research Journal, Volume 2, Number 1, Spring 2006 © Board of Trust of Vanderbilt University Vanderbilt Concrete Canoe 2 TABLE 1 Hull Dimensions FIGURE 1 Rendered View of Hull Design Dimensions Size WL Length 17 feet WL Width 31 inches Freeboard 7 feet Draft 6.5 inches Asymmetry 126 inches Unfortunately, the sprint and slalom racecourses have contradicting requirements. The performance criteria of stability, maneuverability, and top speed are ranked in descending order by design teams. Before exploring the means for meeting these criteria, the alterable geometric dimensions were limited to the waterline length, waterline width, longitudinal curvature, freeboard, and draft. Stability is the tendency of a hull form to return to its original position when inclined away from that position (Rawson and Tupper 1994). Lowering the center of gravity or providing excessive freeboard to counteract heeling, which is shown in rotation about the longitudinal axis, will reduce the risk of overturning. Excessive freeboard will hinder paddling technique. Therefore, lowering the center of gravity by increasing the waterline width is an effective method to increase stability. Maneuverability is the ability to effectively carve a turn and track straight without losing momentum. Accomplished primarily by reducing lateral resistance, lateral surface area is a function of draft, waterline length, and longitudinal curvature. Turning was considered more important than tracking due to the numerous buoys encountered in the slalom course. Fortunately, there are means to track straight and arc well: V-shaped cross sections have the ability to act as a keel. These were employed near the bow and stern to provide greater lateral stiffness. Top speed is the product of the hydrodynamic hull form, paddling technique, and quality of wetted surface. The HD Team focused on the hull form and research indicated that longer waterline lengths and narrower waterline widths were beneficial to higher speeds. Furthermore, asymmetric shapes and sharp bow and stern tips were found to provide top speed advantages. Before proceeding to build The Little Engine, the HD Team contacted a commercial hull designer to confirm our research. Nearly all previous nationally-recognized concrete canoes have featured waterline lengths over twenty feet that help in long courses. The short sprint and slalom courses limit length advantage dramati- cally (Scarsborough 2005). Thus, the designers reduced waterline length to improve weight, con- struction, maneuverability, and material cost. The team utilized Vacanti Prolines V7 R3.5 Pro® to 3 Vanderbilt Undergraduate Research Journal TABLE 2 Paddlers and Positions FIGURE 2 Two-Man Diagram Race Paddlers and Position Aft Bow (Inches) Coed One Male (36) Male (104) Female (138) Female (174) Coed Two Male (36) Female (76) Female (138) Male (174) 3 Males/Females 36 107 174 2 Males/Females 38 174 model and iteratively optimize The Little Engine for a four-person loading condition. Table 1 shows the concrete canoe dimensions and Figure 1 shows a rendered view of the hull design. Analysis The next phase of analysis on The Little Engine began immediately after finalizing the hull design with all team members. Collaboration with the Mix Design Team was vital to gauge the material properties of the cementitious composite in tension, compression, and flexure. In previous years, two-dimensional detailed analysis was employed as the only means of analyzing composite capacity. Distributed loads were made constant or linear to model shear and bending moment diagram calculations, and cross-sections were considered polygonal to calculate moments of inertia for bending stress equations. Compression and tension stress limit states were determined to be 282 pounds per square inch and 196 pounds per square inch, respectively. Building upon these efforts, the analysis team decided to perform a two-dimensional precise analysis using the loading scenarios shown in Table 2. Men and women were assumed to be 180 pounds and 135 pounds, respectively. Extensive calculations were used to determine The Little Engine should weigh 175 pounds with concrete mixes designed at sixty-five pounds per cubic feet. The distribution of the buoyancy and gravity forces were determined by modeling submerged areas at every six inches along the length of the design model. Vacanti Prolines Pro® provided the means to export dxf files for AutoCAD 2006® use. Submerged ar- eas were assumed typical for 6 inch widths. The volume of water displaced for each section was de- termined and used to calculate a concentrated force. Spaced every 6 inches along the hull length, these concentrated forces formed the distributed buoyancy and gravity forces along the length of The Little Engine. MATLAB Version 6.0.0.88 Release 12© was programmed to produce the shear and bending moment diagram shown in Figure 2. The two-man loading scenario was most critical for loading, producing Vanderbilt Concrete Canoe 4 FIGURE 3 FIGURE 4 SAP Section FEA Stresses maximum service shear and bending moment magnitudes of 160 pounds and 520 feet-pounds. The moments are not exactly zero at the ends due to computer rounding errors. By examining the widest cross-section of The Little Engine, the moment arm between the tension and couple was estimated to be eight inches. Figure 3 shows a six-inch shell element modeled in SAP 2000® to aid this estimation. Using a safety factor of 2.0 and an ACI Building Code recommended dynamic load factor of 2.0, the required compression and tension capacities were computed to be 950 pounds per square inch and 145 pounds per square inch, respectively. Since a three-dimensional analysis had never been performed on a concrete canoe at Vanderbilt University, performing further analysis required researching basic finite element systems defined as masses connected by springs. Similarly, an introduction to the commercial software available for analysis was necessary to gauge the difficulty in using their interfaces. An IGES NURB, a high-level industry standard file defining the hull shape completely, was imported into ANSYS Release 7® and SAP 2000®. SAP 2000® was utilized for its ease in entering load data and applying end constraints. Restricting rotation and translation in all Cartesian directions, The Little Engine was treated as a beam, fixed at thirty-six inches from either end. Since tension and compression limit states were found from two-dimensional analysis, the goal of three-dimensional analysis was to determine a composite flexural capacity. Assuming a linear isotropic concrete composite, the flexural strength capacity, as computed by the effective stress, von Mises equation, was 425 pounds per square inch. Development and Testing The aim of the mixture design was to minimize concrete density while exceeding the minimum design
Details
-
File Typepdf
-
Upload Time-
-
Content LanguagesEnglish
-
Upload UserAnonymous/Not logged-in
-
File Pages11 Page
-
File Size-