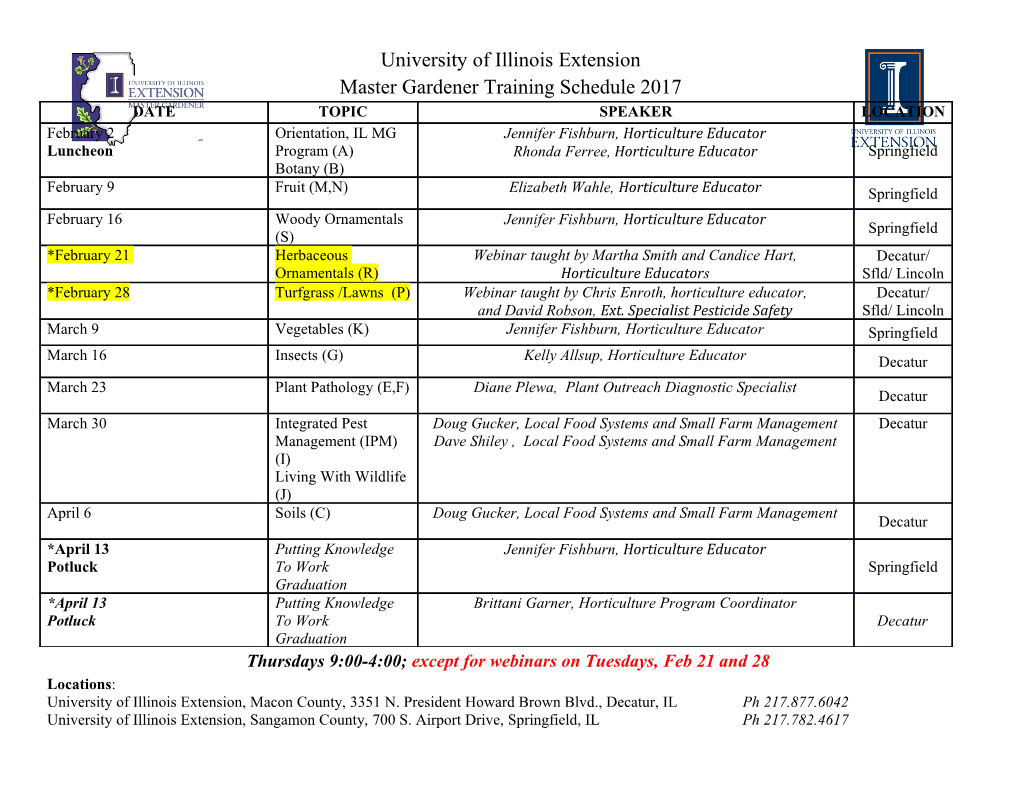
Materials Transactions, Vol. 60, No. 3 (2019) pp. 450 to 457 ©2019 The Japan Society for Technology of Plasticity Evaluation of Work Hardening and Tensile Strength for Press Worked Products Plastic Strained from Multiaxial Direction Tetsuro Ishimura1 and Souichiro Nishino2 1Power Generation Systems Div. Power Business Unit, Hitachi, Ltd., Hitachi 317-8511, Japan 2Institute of Quantum Beam Science, Graduate School of Science and Engineering, Ibaraki University, Hitachi 316-8511, Japan Tensile strength and work hardening characteristics in the case that strain was applied from multi-axial directions by press processing and in the case that uniaxial strain was applied by tensile test were compared. Furthermore, in a unified manner with the results of the tensile tests, fatigue tests on plate material subjected to multiaxial strain were conducted, and the strength reliability of the pressed product was evaluated. Tensile strength of mild-steel plate subjected to uniaxial or multiaxial plastic strain was increased. If a tensile test is carried out again after a certain period of time has elapsed by applying strain, not only yield stress but also tensile strength are increased. This trend is due to strain aging inside the material. Degree of work hardening is higher when multiaxial strain is applied compared to when uniaxial strain is applied. For materials work hardened by applying strain, their hardness and the tensile strength are proportional regardless of the load status of strain. Accordingly, tensile strength of a product subjected to different strains can be evaluated uniformly by measuring the product’s hardness. When strain is applied from multiple axes in press working, as well as tensile strength, fatigue strength is improved by work hardening. According to the results the microscopic analysis by X-ray diffraction combined with the full-width-at-half-maximum method, dislocation density is increased when multiaxial strain is applied compared to when single-axis strain is applied, and the degree of work hardening is greater. The full width at half maximum is correlated with tensile strength regardless of the state of strain applied to the material. TEM observation of dislocations revealed that the third-step-pressed product subjected to multiaxial strain has a coaxial, fine-grain dislocation-cell structure. On the other hand, in the case of pre-strained (plastic strain of 20%) material subjected to a uniaxial tensile load, the cell structure was unclear, and even the cells that were produced had coarse grains stretched in the tensile direction. [doi:10.2320/matertrans.P-M2018854] (Received May 21, 2018; Accepted December 12, 2018; Published February 25, 2019) Keywords: mild steel plate, uniaxial and multiaxial straining, work hardening, tensile strength, fatigue strength, X-ray diffraction, full width at half maximum intensity, TEM (Transmission Electron Microscope), dislocation cell 1. Introduction It can therefore be considered that when plastic strain is applied from multiple axial directions, as in the manner of In regard to the manufacture of automotive parts, press press forming, the change in mechanical properties of the (plastic) working is indispensable, and among the available strained material will be larger than that in the case of processing methods, press forming of steel sheets produces uniaxial tension. Car parts are molded from steel sheets by press-worked products with a large specific gravity. More- various press-working processes, and clarifying the influence over, various steel plates with different microstructures and of the plastic strain received in those processes on the static mechanical properties®ranging from mild steel plate to strength (yield stress, tensile strength, etc.) of the parts is a 1180-MPa-class high-strength tensile steel plate®are used key task in regard to correctly evaluating the strength of the for press-forming steel sheets. Many of these press-formed press-worked parts. Although many researches on tensile parts are given plastic strain by the press working, and the strength7­13) and fatigue strength14­20) of steel plates loaded hardness and microstructure of the processed material are with plastic strain have been reported, the majority of those changed by this plastic strain. However, in the case of the reports deal with strain loads in the form of simple tensile current automobile design process, the strength of a designed deformation.5­20) Regarding strain load from multiaxial part is set on the basis of the tensile strength of the steel sheet directions, although some examples of investigations on before pressing. the strength characteristics of steel plate after rolling have If a steel plate is subjected to a certain amount of plastic been reported,5,6) few examples of directly investigating deformation in an unloading and reloading manner, its yield the strength characteristics of pressed products have been stress is increased by work hardening (which is caused by reported. increased dislocation density in the steel sheet). In addition, it In consideration of the above background, in this study, is known that the hardness of a material is improved by strain focusing on the difference in strain-loading methods for press applied by plastic working, and an example in which the forming, we compared the influences on strength reliability hardness of a mild-steel plate is nearly doubled by plastic of (i) strain in one direction (“uniaxial” strain hereafter) under working the plate has been reported.1) As reported, hardness simple tension (plastic strain of 5 to 20%) and (ii) strain from corresponds to tensile strength,2­4) so tensile strength can also multiple axial directions (“multiaxial” strain hereafter). In be improved by plastic deformation. When a steel sheet is particular, car parts made of mild-steel plate and manufac- subjected to uniaxial tensile plastic strain, its yield stress is tured by 10-step press working were targeted. Tensile increased, but its tensile strength is assumed to stay constant. specimens were cut out from blank material, molded into On the contrary, it is known that rolled steel sheet has not pressed products by one of three different pressing processes, only increased yield stress and hardness but also increased and subjected to a tensile test. The effect of the plastic strain tensile strength and fatigue strength compared to those in the multiaxial direction received by the material in each properties of the sheet before rolling.5,6) process on the mechanical properties of the specimens was Evaluation of Work Hardening and Tensile Strength for Press Worked Products Plastic Strained from Multiaxial Direction 451 Table 1 Mechanical properties. piston,1) which was processed from blank material with a diameter of 195 mm in 10 steps, were used. Photographs of the processed (press-worked) items after the first to third steps and their cross-sectional shapes are shown in Fig. 1. The first step is optimal cylindrical drawing with minimum thickness reduction. Specifically, minimum reduction in plate thickness is achieved by setting optimum punch radius Rp, die radius Rd (as shown in Fig. 2) and minimum blank- holding pressure. The second step is reverse-press forming 1st process 2nd process 3rd process in which the first-step-processed item is “reverse pressed” in order to greatly improve re-draw ability. Specifically, as shown in the schematic diagram of the forming process shown in of Fig. 2, the front and back surfaces of the steel sheet are inverted and processed by utilizing the rigidity of 5cm 5cm 5cm the pressed product itself. By this reversed forming of the front and back surfaces, stress in the direction opposite to that acted in the first step can be applied to the work-piece. 5cm 5cm 5cm As a result of this reverse press forming, which utilizes the so-called Bauschinger effect, formability is remarkably improved compared with that in the case of redrawing that is usually used. The third step involves intrusion forming to increase the Fig. 1 Press worked products and cross section. wall thickness of the second-step-molded item to more than the material wall thickness. Specifically, as shown in the investigated. In addition to the mechanical properties schematic diagram of the forming process in Fig. 2, the determined by the tensile tests, strength reliability of the diameter of the vertical wall portion is reduced by pushing pressed products was comprehensively evaluated by cutting the second-step-molded product into the mold, and the wall out test specimens from the pressed products and investigat- thickness is increased according to the constant-volume law. ing their fatigue characteristics. The difference between the Measured wall thicknesses of the first- to third-step- multiaxial strain load and the uniaxial strain load was pressed products are shown in Fig. 3. Tensile test specimens investigated by observing the respective microscopic were prepared by cutting them out from vertical wall portions dislocation structures by TEM. of these products by wire cutter. And these specimens were flattened in a vice and treated by machine before tensile test. 2. Specimens and Test Methods To confirm the influence of the anisotropy of the steel sheet, as shown in Fig. 4, the test specimens was cut in three 2.1 Test materials and test-specimen preparation meth- directions, namely, 0° (rolling direction), 45°, and 90° (right- od angle), to the rolling direction of the steel sheet. The cutout The mechanical properties of the test material (JSH 270 D) positions and dimensions of the tensile-test specimens are are listed in Table 1. For the pressed parts to be investigated, shown in Fig. 5 and Fig. 6, respectively. These cutting the first- to third-step pressed products of CVT pulley positions were determined vertical wall portion due to small 㻰㼞㼍㼣㼕㼚㼓 㻾㼑㼢㼑㼞㼟㼑 㻰㼞㼍㼣㼕㼚㼓 㻾㼑㻙㼐㼞㼍㼣㼕㼚㼓 㻿㼠㼑㼑㼘 㼟㼔㼑㼑㼠 㻼㼡㼚㼏㼔 㼙㼛㼠㼕㼛㼚 㻝㼟㼠 㼟㼠㼑㼜 㻞㼚㼐 㼟㼠㼑㼜 㻟㼞㼐 㼟㼠㼑㼜 㻰㼕㼑 㻼㼡㼚㼏㼔 㻰㼕㼑 㼓㼑㼛㼙㼑㼠㼞㼥 Fig. 2 Schematic illustration of 2nd and 3rd press working process.
Details
-
File Typepdf
-
Upload Time-
-
Content LanguagesEnglish
-
Upload UserAnonymous/Not logged-in
-
File Pages8 Page
-
File Size-