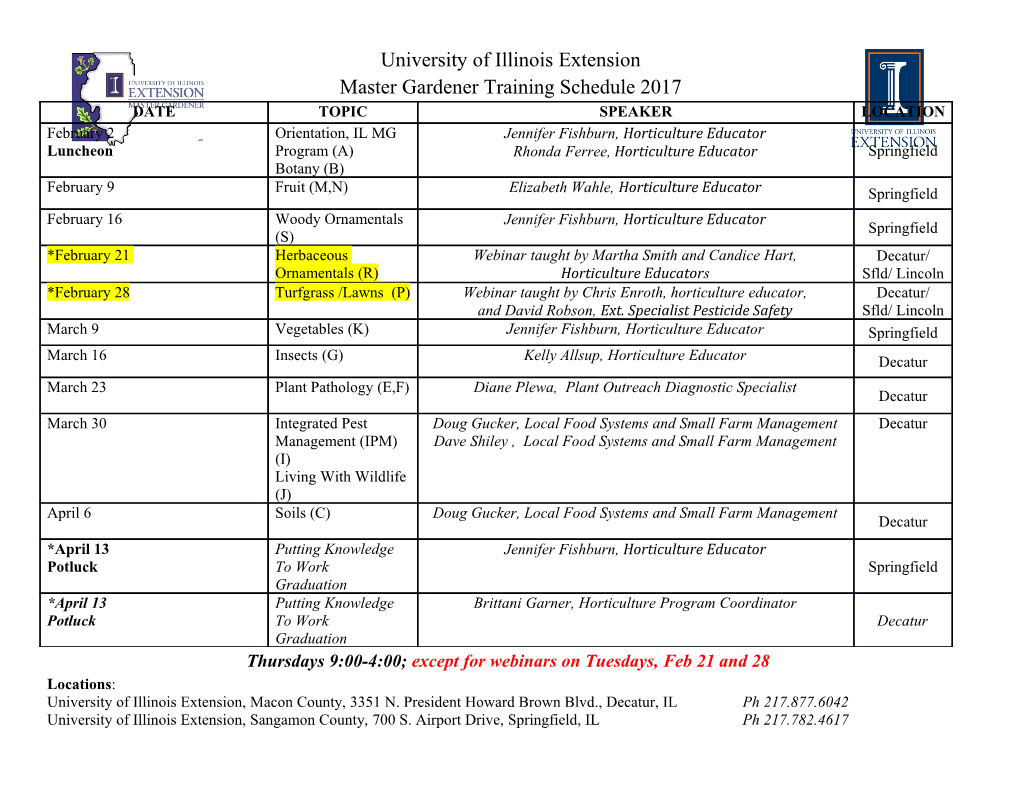
AERODYNAMIC AND MECHANICAL DESIGN OF AN 8:1 PRESSURE RATIO CENTRIFUGAL COMPRESSOR by Colin Osbosne, P. W. Runstadler, Jr., and W. Dodd Stacy (KASR-CF-134762) AHRODYNP.IIC AND MSCLilNICiL E:75-25188 DESIGN !)F 25 fj:l PFESSU'E FIT10 CPICT9IFUGRL CO?i?PESSO:? (Creare, Inc.) 145 p liC ,-55-75,-,CL ,. 21ii lirlclas G3/37 24219 **--- > CREARE INCORPORATED prepared for 'C NATIONAL AERONAUTICS AND SPACE NASA Lewis Research Center >- Contract NAS 3-17848 1. Rcport No. 2. Government Accession No. 3. Recipient's Catalog No. NASA CR-134782 4. Title and Subtitle 5. Rcprt Dare AERODYNAMIC AND MECHANICAL DESIGN OF AW 8:l April 1975 PRESSURE RATIO CENTRIFUGAL COMPRESSOR 6. Performing Organization Code 7. Authoris) 8. Performing Organization Report No. Colin Oshorne 'EN-204 Peter W. Runstadler, Jr., and W. Dodd Stacv 10. Work Unit No. 9. Performing Organinlion Name and Address Creare Incorporated P. 0. Box 71 11. Contract or Grant No. Hanover, N. H. 03755 NAS3-17848 13. Type of Report and Psriod Cavered 12. Spnsorlng Agency Name and Address Contractor Rsport National -4eronautics and Space Adninistration Washington, D. C. 14. Sponsorin: Igency Code 15. Supplemcnrary Notes Project Manager, Jerry R. Wood, Lewis Research Center and U. S. Army Air Mobility R & D Laboratory, Clevaland, Ohio 16. Abstract An 8:l pressure ratio, 0.907 kg/s (2.0 lbm/s) centrifugal compressor stage has been designed and fabricated. The design proceeded subject to the specifi- cations that [i) the stage be representative of "state-of-the-art" performance (efficiency and flow range) and (ii) the stage will be used as a "workhorse" compressor for experiments to be conducted using laser Doppler velocimeter (LDV) equipment. The final design is a 75,000 RPM, 19 blade (no splitters) impeller with an axial inducer and 30' of backward leaning at the impeller tip. An optimally matched, 17 channel, vane island diffuser was designed and built. The calculated total-to-static efficiency is 77% with a flow range of i2%, choke-to-surge, at design speed. All of the compressor hardware has been fabricated and inspected and the stage has been checked out for mechanical integrity at design speed under a companion program. 17. Key Words (Suggesled by Authorlsl t 18. Distribution Statomcnt Centrifugal Compressor High pressure ratio compressor Unclassified - unlimiked 19. Sccuritv Ctassif. (of this report) 20. Z=urity Clawif. (of this page) 21. No:of Pages 22. Price* Unclassified Unclassified 146 $3.00 ' For sale by Lhe National Technical Informalion Service, Springfield, Virginia 22151 NASA-C.lbR (Rcv. 6-71) TABLE OF CONTENTS Page LIST OF TABLES .................... v LIST OF FIGURES .................... vi SUMMARY ........................ 1 INTRODUCTION ..................... 3 DESIGN OBJECTIVES AND SPECIFICATIONS ......... 4 Aerodynamic Specifications. ........... 4 Other Design Constraints. ............ 4 PRELIiJTINARY AERODYNAMIC DESIGN ............ 6 Design Procedures ................ 6 Preliminary Design Analyses ........... 22 Results ..................... 30 Conclusions/Recoinmendalions ........... 41 AERODYNAMIC DESIGN OF INDUCER ............. 43 General Philosophy ................ 43 Inducer Design Method .............. 44 Design Procedures ................ 45 AERODYNAMIC DESIGN OF IMPELLER ............ 55 Approach ..................... 55 VANCO Potential Flow Program ........... 56 Modifications to Reflect Creare Flow Model .... 57 Aerodynamic Criteria ............... 57 Results ..................... 61 Final Blade and Passage Definition ........ 75 InletDesign .................. 78 iii PRzcgDING PAGE BLANK NOT FLm TABLE OF CONTENTS .Continued Page DIFFUSER FINAL DESIGN .................. 80 Objectives ..................... 80 Input from Preliminary Design Analysis ....... 80 Approach ...................... 81 COMPRESSOR INSTRUMENTATION ............... 87 Type and Location of Aerodynamic Instrumentation . 87 Mechanical Instrumentation ............. 101 Readout Instrumentation .............. 102 MECHANICAL DESIGN .................... 104 Basic LSM Rig Description ............. 104 High Speed Rotating Components ........... 106 Inlet Hardware ................... 116 Impeller Cover ................... 116 Diffuser Components ................ 116 EARDWARE FABRICATION AND INSPECTION ........... 118 Impeller ...................... 118 Impeller Cover ................... 118 Diffuser ...................... 118 Dynamic Balance of Impeller Assembly ........ 118 CONCLUSIONS ....................... 125 APPENDIX A - NOMENCLATURE . + . 9 . = . rn . 126 REFERENCES ....................... 138 LIST OF TABLES Page I EFFICIENCY VARIATION WITH SPEED .......... 22 I1 SENSITIVITY FACTORS ................ 25 111 TITAFJIUM STRESS LIMITS .............. 29 IV STRESS FUNCTION VS . TAPER RATIO CONSTANT ..... 29 V RESULTS FOR RAP?AL AND BACKSWEPT BLADE DESIGNS (DESIC?; POINT CONDITIONS) ............. 31 VI NO!.LINAL IMPELLER GEOMETRIC COORDINATES ...... 76 VII IMPELLER COVER STATIC TAP LOCATIONS ........ 91 VIII IMPELLER TIP STATIC TAP LOCATIONS......... 93 IX VANELESS/SEMI-VANELESS STATIC TAP LOCATIONS .... 94 X CHANNEL DIFFUSER STATIC TAP LOCATIONS ....... 95 XI IMPELLER AND INLET TRANSDUCER LOCATIONS ...... 97 XI1 DIFFUSER INLET TRANSDUCER LOCATIONS ........ 98 XIII IMPELLER BLADE ROOT STRESSES (90. 000 RPM) .....109 XIV PHYSTCAL CHARACTERISTICS OF IMPELLER .......110 XV MAXIMUM DISC STRESS AND =DIAL AND AXIAL TIP DEFLECTIONS ....................114 LIST OF FIGURES LOCUS OF INDUCER HUB-TO-TIP RATIO WITH SPEED =1.2 Mrel1t ................ ... 8 INDUCER TIP RELATIVE MACH NUMBER VARIATION WITH AXIAL VELOCITY .Zo = 0.5. ............ 9 INDUCER TIP RELATIVE MACH NUNBER VARIATION WITH AXIAL VELOCITY .Zo= 0.3. ........... 10 INDUCER TIP RELATIVE AIR ANGLE VARIATION WITH AXIAL VELOCITY- Zo= 0.5. ............... 11 INDUCER TIP RELATIVE AIR ANGLE VARIATION WITH AXIAL VELOCITY .Zo = 0.3. ........12 CHANGE IN INDUCER TIP INCIDENCE BETWEEN DESIGN POINTANDSURGE- Zo= 0.5 ............ 13 CHANGE IN INDUCER TIP INCIDENCE BETWEEN DESIGN POINT AND SURGE .Zo = 0.3 ............ 14 INDUCER PERFORMANCE MAP (IM.70) .......... 16 AXIAL FAN ROTOR PEFSOlW?iNCE HAP .P & W 305 METERS/SEC (1000 fps) FAN ............. 17 VARIATION OF COMPRESSOR EFFICXENCY WITH DESIGN PARAMETERS .................... 24 IMPELLER EXIT DEPTH VARIATION WITH DESIGN PARAMETERS (mw/rn = 0.2) .............. 26 VANELESS SPACE RADIX EIMENSION VARIATION WITH DESIGN PARAMETERS................. 27 DESIGN POINT STAGE EFFICIENCY AS A FUNCTION OF IMPELLER BLADE BACKSWEEP ANGLE .......... 35 COMPRESSOR PERFORMANCE MAP . = O0 ...37 COMPRESSOR PERFORMANCE MAP .BZ1, = .30° ...... 38 VELOCITY VECTOR DIAGRAMS AT INDUCER INLET ..... 39 LIST OF FIGURES - Continue6 Page VELOCITY VECTOR DIAGRAMS AT IMPELLER EXIT 82b = 0' and -30'. 40 DEFINITION OF INDUCER GEOMETRIC PARAMETERS . 46 BLADE MEAN LINE ANGLE DISTRIBUTION AT ROTOR LEADING EDGE . 49 INCIDENCE DISTRIBUTION AT ROTOR LEADING EDGE . 50 CREARE'S IDEAL IMPELLER LOADING DISTRIBUTION . 60 BLADE NORMAL THICKNESS DISTRIBUTION - HUB AND COVER. 63 BLADE ANGLE DISTRIBUTION - HUB AND COVER . 64 RELATIVE MACH NUMBER DISTRIBUTION - COVER STREmLTNE....................66 RELATIVE fT4CH NUMBER DISTRIBUTION - MEAN SF.W STREAMLINh . 67 RELATIVE MACH NUMBER DISTRIBUTION - HUB STREAMLINE . 68 RELATIVE VELOCITY DISTRIBUTION - COVER STREAMLINE . 69 RELATIVE VELOCITY DISTZIBUTION - MEAN SPAN STREAMLINE . 70 RELATIVE VELOCITY DISTRIBUTION - HUB STREAMLINE. 71 BOUNDARY LAYER CHARACTERISTICS FOR BLADE SUCTION SURFACE - COVER STREAMLINE . 73 BOUNDARY LAYER CHARACTERISTICS FOR BLADE SUCTION SUXACE - HUB STREAMLINE . 74 MERIDIONAL VIEW OF IMPELLER. 77 COMPRESSOR INLET GEOMETRY. 79 VANED DZFFTJSER GEOMETRY - PRIMARY DESIGN . 84 LIST OF FIGURES - Concluded Page VANED DIFFUSER GEOMETRY .ALTERNATE DESIGN. ...86 INLET STATIC TAP LOCATIONS. ............89 IMPELLER COVER STATIC TAP LOCATIONS ..... PRESSURE STATIC TAPS AND SEFII-CONDUCTOR TRANS- DUCER LOCATIONS IN DIFFUSER INLET ......... 92 INLET AND IMPELLER SEMI-CONDUCTOR TRANSDUCER LOCATIONS.....................96 TYPICAL DESIGN OF STATIC PRESSURE TAP AND CONNECTOR ..................... 99 Po4 TOTAL Pmssum PROBES AND INSTALLAT~ON. ....LOO PROXIMITY PROBE CLOSED LOOP, VARIABLE FRESSURE COMPRESSOR TEST FACILITY. .................... .lo5 COMPREXSOR STAGE - MERIDIONAL VIEW. .......-107 DEFINITION OF IMPELLER STRESS CALCULATION STATIONS.111 IMPELLER CAMPBELL DIAGRAM ............ .112 HIGH SPEED IMPELLER ASSEMBLY. ...........I15 COMPRESSOR IMPELLER IMPELLER COVER. DIFFUSER ASSEMBLY .................I21 DIFFUSER VANELESS/SEMI-VANELESS REGION PRESSURE TAPS. .......................I22 ASSEMBLED COMPMSSOR HARDWARE! ...........I24 SUMMARY The aerodynamic and mechanical. design of a high pressure ratio (pr = 81, Low mass flow (m = 0,907 kg/s), centrifugal compressor, typical of desigcs that might be used for small aircraft and gas turbine engines, has been undertaken. The design was subject to the requirements that (i) the compressor be of "state-of-the-art" perfor- mance with respect to efficiency and range, (ii) the inducer tip operate at a relative Mach number of 1.2, and (iii) the compressor unit be used as a "workhorse" com- pressor together with laser Dopper velocirneter (LDV) equipment. A Preliminary Design (one-dimensional analysis) study examined the trade-offs, for both radial and back- ward leaning impellsrs, with regard to aerodynamic per- formance, rotative speed and geometrical dimensions that are best suited for use with the LDV equipment and sub- ject to the above constraints. State-of-the-art
Details
-
File Typepdf
-
Upload Time-
-
Content LanguagesEnglish
-
Upload UserAnonymous/Not logged-in
-
File Pages147 Page
-
File Size-