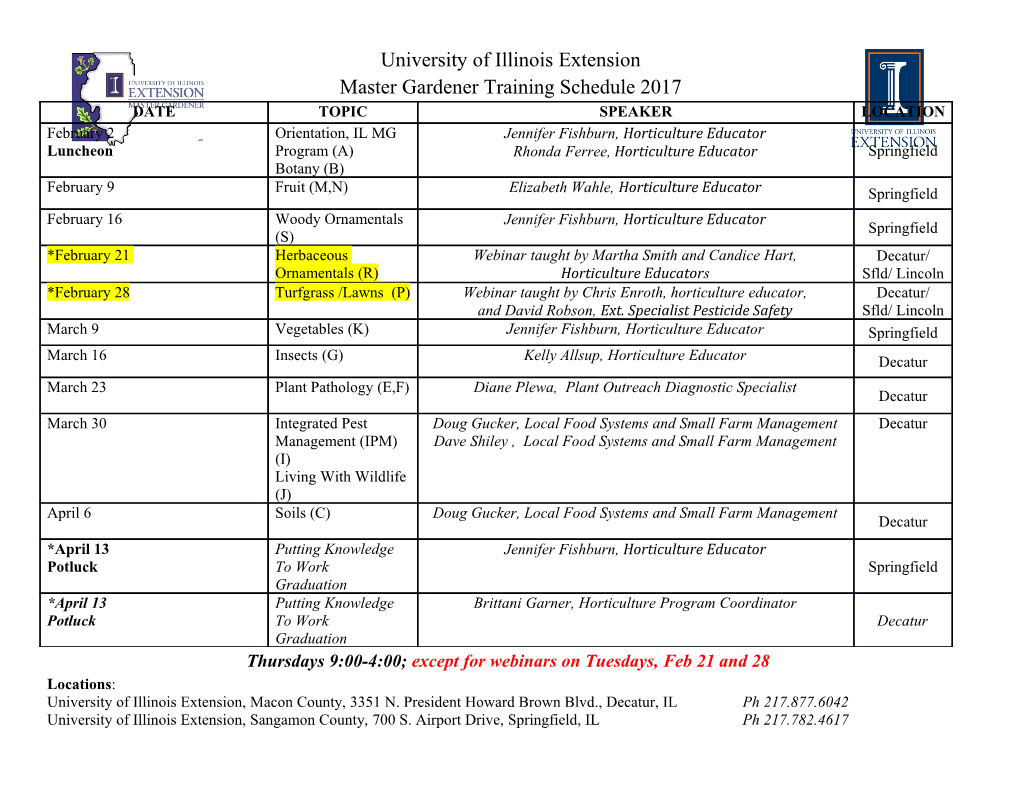
Design and Optimization of a Small Reusable Launch Vehicle Using Vertical Landing Techniques Stephane Contant Delft University of Technology Design and Optimization of a Small Reusable Launch Vehicle Using Vertical Landing Techniques by Stephane Contant to obtain the degree of Master of Science at the Delft University of Technology, to be defended publicly on Thursday, November 28, 2019 at 13:00. Student number: 4735676 Project duration: March 6, 2019 to November 28, 2019 Thesis committee: Ir. B.T.C. Zandbergen, TU Delft, Supervisor Prof.dr. E.K.A Gill, TU Delft Dr.ir. D. Dirkx, TU Delft This thesis is confidential and cannot be made public until November 28, 2019. An electronic version of this thesis is available at http://repository.tudelft.nl/. Cover image: Falcon 9 landing burn, credited to SpaceX. Abstract Recent years have seen a drastic increase in the number of small satellites launched per year, as these systems weighing less than 1000 kg have become a less expensive alternative to obtaining scientific data compared to satellites weighing multiple tons. However, one current drawback with these systems is their current price per kilogram to orbit, often reaching over $100k (2018) per kilogram for rideshare and cluster launches. Dedicated small satellite launch vehicles are a third solution to bringing small satellites to orbit that present potential reductions in price per kilogram. In parallel, reusability of the first stage of a launch vehicle using vertical landing techniques also presents the potential for further price per kilogram reductions. A baseline of $20.0k (2018) per kilogram to orbit is deemed as the benchmark for cost-effective solutions, as the current average reported price per kilogram of small launch vehicles totals $29.9k (2018). With small launch vehicle developers making bold claims about their advertised launch prices, a need for verifying these claims has been established to determine the true potential for price reductions. The combi- nation of reusing the first stage of a small launch vehicle presented the most promising solution to reducing these prices. The scope of this research is to develop a tool capable of costing a small, reusable launch ve- hicle using a Multidisciplinary Design Analysis approach, before implementing a Multidisciplinary Design Optimization method to optimize such systems for price per flight in the Tudat development environment. To determine the price per flight and price per kilogram of a small, reusable launch vehicle, the propulsion, geometry and mass of such systems are first modelled, before the trajectory is modelled using a direct as- cent for the simulation to the target orbit, and both return-to-launch-site and downrange landing options are considered for the reuse trajectory. Subsequently, a small launch vehicle cost model is integrated into the Multidisciplinary Design Analysis environment and is modified for the inclusion of reusability, before combining these models into the Multidisciplinary Design Optimization tool. A 100 kg and a 500 kg payload launched to 650 km altitude Sun-synchronous orbit from Plesetsk Cosmodrome are first investigated. Under the design choices made in this study, it is immediately concluded that small, reusable launch vehicles are not a cost-effective solution for the 100 kg payload class, reaching up to five times the benchmark per kilogram. It is also concluded that three-stage launch vehicles are more expensive to launch than two-stage systems. Six different propellant and engine configurations are investigated for both the return-to-launch-site and downrange landing options. While all optimal designs for the former are below the $20.0k (2018) per kilogram assuming 20 launches per annum, 100 total launches and 10 first stage reuses, none of the downrange landing designs meet this target price. Furthermore, only a single design from the previous twelve, namely an RP1-propelled, 9-engine configuration, meets all trajectory path constraints, establishing this design as the optimal case for a small, reusable launch vehicle with a price per kilogram of $18.2k (2018). Nine additional expendable launch vehicles are optimized to compare these to the reusable system, with the configurations ranging in price per kilogram from $20.5k (2018) to $30.4k (2018), further demonstrating the cost-reduction potential of the small, reusable launch vehicle. The effect of changing the target orbit is observed to have a 9.35% reduction in price per flight while a near- equatorial launch further reduces this value by 3.34%, indicating that it is more important to design the launch vehicle for the target orbit rather than the intended launch site. Over 5 reuses is the minimum number of first stage reuses needed to see an improvement in price per flight compared to an expendable counter- part. Designing for the highest number of total launches and launches per annum is best for cost-reduction of these systems, with 100 total launches and over 10 launches per annum established as minimum values. A sensitivity analysis shows that the errors associated with the cost estimation relationships can reduce the Theoretical First Unit cost of the launch vehicle by 23.9% or increase it by 32.8%, indicating that great caution should be taken when refining future cost estimates. Additionally, the price per flight is not significantly af- fected by uncertainties in launch vehicle and cost parameters, with greatest sensitivity seen from uncertainty in the inert mass and in the manufacturing cost parameters. Thus, it is concluded that a small, reusable launch vehicle can definitively offer a 30% reduction in price per flight compared to the reported $29.9k per kilogram. iii Acknowledgements The following project is the culmination of my Master’s thesis in Aerospace Engineering at the Delft University of Technology. During these last few months of hard work and pushing myself to my limits both physically and mentally, I can definitively stated that this was the most challenging yet rewarding task I have undertaken in my life. There are many people that were essential to my success, and I will forever be grateful for their endless support. First, I would like to thank my daily supervisor Barry Zandbergen for being a great mentor not only through- out this thesis, but throughout my entire time in Delft. Barry has been an incredible resource in helping me adapt from a non-aerospace background, ceaselessly providing critical feedback that allowed me to become the best engineer I could be. I was given the freedom to explore a topic that was incredibly fascinating to me during my research and for that, I will always be thankful. In addition, I would like to thank Dominic Dirkx, who always welcomed my questions about and problems concerning Tudat with open arms. Without Dominic’s help, the thesis would have been a much longer and more difficult process. Furthermore, I would like to thank my parents, Sandra and Daniel, and my sister Emilie, for their unending support of my life choices. Despite being more than an eight hour flight from home, my family was always there to talk, support me or give me advice whenever I needed it. They have been my rock since well before my post-secondary studies and I can confidently say that I would not be the person I am today without them. Thank you Anthony, Jaime Q, Jaime N, Tino and Pablo, as spending almost every day with you over the last two years has made this Master’s degree go by extremely quickly, and you have all helped me feel at home in your native continent through our countless adventures together. I will never forget and always cherish our good times, and I hope our paths will cross many more times in the future. Thank you Pat, Andrew, Pedro, Sean and Rob for being the best long distance friends anyone could ever need. You have supported me through countless conversations and Skype calls, forever giving me the best reason to come home. To the rest of my friends and colleagues in Delft, thank you all for the memories that we have created while working towards the common goal of becoming aerospace engineers. v Contents Abstract iii Acknowledgements v List of Figures ix List of Tables xi Nomenclature xiii 1 Introduction 1 2 Literature Study 3 2.1 Small Launch Vehicles......................................3 2.2 Reusable Launch Vehicles.....................................4 2.3 Multidisciplinary Design Analysis and Optimization.......................6 2.4 Optimization Algorithms.....................................7 2.5 Development Environment....................................8 2.5.1 Existing Models......................................9 2.6 Tool Requirements........................................9 3 Launch Vehicle Propulsion, Geometry and Mass 11 3.1 Propulsion............................................ 11 3.2 Geometry and Mass........................................ 13 3.2.1 Solid Rocket Stage..................................... 13 3.2.2 Liquid Rocket Stage.................................... 14 3.3 Launch Vehicle Model...................................... 15 3.4 Reusability Geometry and Mass Model.............................. 16 3.5 Verification and Validation.................................... 17 4 Trajectory Model 25 4.1 Nominal Ascent Trajectory.................................... 25 4.2 Reusable Descent Trajectory................................... 26 4.3 Trajectory Constraints...................................... 27 4.4 Trajectory Model Verification and Validation........................... 28 5 Cost Model 33 5.1 Launch Vehicle Cost Model...................................
Details
-
File Typepdf
-
Upload Time-
-
Content LanguagesEnglish
-
Upload UserAnonymous/Not logged-in
-
File Pages133 Page
-
File Size-