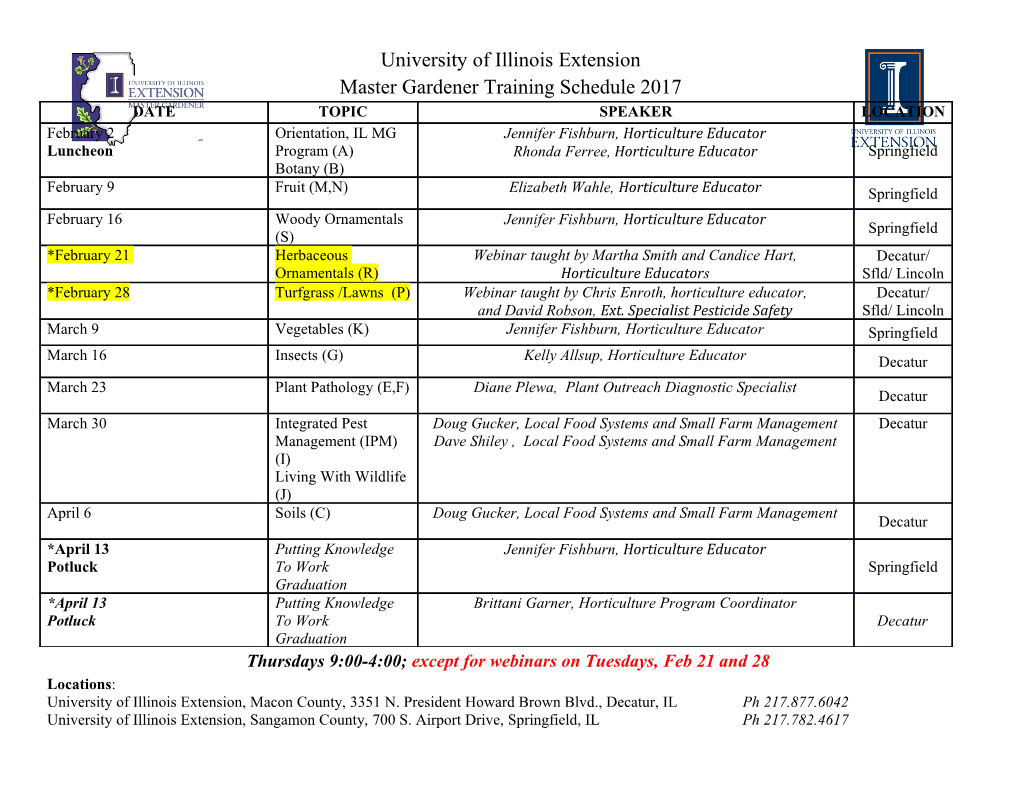
SELECTING SUITABLE METHODS FOR TREATING MINING EFFLUENTS* Nural Kuyucak Golder Associates Ltd. 32 Steacie Drive Kanata, Ontario, K2K 2A9 Canada (613) 592-9600 (613) 592-9601 [email protected] *Prepared for the “PerCan Mine Closure” Course, Lima, Peru (July 13-23, 2006) CONTENTS ABSTRACT........................................................................................................................ 1 MINE EFFLUENT SOURCES: FROM EXPLORATION TO AFTER CLOSURE......... 2 Acid Mine (or Rock) Drainage (AMD or ARD) ............................................................. 2 Mine Dewatering - Ammonium and Nitrate.................................................................... 2 Process Waters – Cyanide and Acids .............................................................................. 3 Mineral Processing and Tailings Reclaim Water - Thiosalts .......................................... 3 TREATMENT OBJECTIVES AND APPROPRIATE PROCESS SELECTION ............. 3 Regulatory Standards....................................................................................................... 3 Sustainability Considerations .......................................................................................... 4 TREATMENT OPTIONS .................................................................................................. 5 Active methods – Neutralization and Precipitation Processes ........................................ 5 Lime Neutralization Processes, High Density Sludge (HDS) Method and Critical Process Parameters........................................................................................................................ 7 In-Line Lime Treatment.................................................................................................. 10 Alternative Neutralizers.................................................................................................. 11 Limestone (CaCO3) Neutralization ........................................................................... 11 Magnesium Hydroxide (Mg(OH)2)............................................................................. 11 Sulphides .................................................................................................................... 11 Sodium Hydroxide (NaOH)........................................................................................ 12 Ammonia (NH3).......................................................................................................... 12 Others (Waste/By-Products of Industries) ................................................................. 12 Coagulation/Flocculation For Better TSS Removal (Solid/Liquid Separation)................ 13 pH Adjustment For Meeting Final Effluent Quality Requirements.................................. 13 Sludge Dewatering Options............................................................................................ 13 Sludge Stability and Fixation.......................................................................................... 14 Biological and Passive Processes..................................................................................................... 14 Sulphate Reducing Bacteria “SRB” Based Processes................................................................. 14 Wetlands..................................................................................................................... 17 Anoxic Limestone Drains (ALD)............................................................................... 17 Open Limestone Trenches.......................................................................................... 17 Biosorbents................................................................................................................. 18 CONSIDERATION FOR DESIGN AND IMPLEMENTATION OF APPROPRIATE TREATMENT PROCESSES ........................................................................................... 18 Process Selection (i.e. Lime Precipitation, Active, Passive, etc.) ............................... 18 Conducting Tests and Evaluating Treatability................................................................. 19 Thiosalts in Mill “Tailings Reclaim” Water..................................................................... 20 Removal of Sulphate (SO4)............................................................................................. 22 Removal of Total Dissolved Salts (TDS) ........................................................................ 22 Removal of Cyanide, Ammonia, and Nitrate (NH4-N/NO3)............................................ 22 Removal of Cyanide....................................................................................................... 23 CONCLUSIONS............................................................................................................... 25 REFERENCES ................................................................................................................. 30 SELECTING SUITABLE METHODS FOR TREATING MINING EFFLUENTS Nural Kuyucak Golder Associates Ltd., 32 Steacie Drive, Kanata, Ontario, Canada K2K 2A9 [email protected] ABSTRACT Mining and metallurgical processes, during operations and after decommissioning, may generate effluents such as reclaimed tailings water, acid mine drainage (AMD) and seepage, and process acid streams. Depending on the type of ore and the metallurgical process, these effluents may contain one or more toxic compounds (e.g., acidity or alkalinity, cyanide, ammonia and/or nitrate, heavy metals, total suspended solids (TSS), sulphate) in elevated concentrations requiring treatment before their discharge to the environment or recycle/reuse in the process. Natural oxidation of sulphide minerals present in mining wastes (e.g., tailings and waste rock) at mining sites may generate AMD, which is characterized as a low pH, high acidity effluent containing heavy metals and sulphate. If generation of AMD cannot be controlled and/or prevented, AMD is collected and treated for neutralization of acidity and reduction of metals and TSS to meet regulated water quality standards. Treatment of mining and metallurgical process effluents can be accomplished by means of physical, chemical and/or biological methods. The mode of process application may vary from the use of either specifically designed, controlled and automated facilities or passive systems. Lime neutralization and precipitation is the most common method used in the mining industry to treat AMD. To reduce the problems associated with disposal and long-term storage of the resulting sludge, the use of a high density sludge process (HDS) has become a preferred option. The use of other chemical reagents, waste or by-products from other industries, and biological sulphate reduction methods can also be considered as viable options for site-specific situations. Recently, several passive treatment systems have been designed and successfully operated, even in the cold North American climate. This paper will discuss available options and provide insights for selecting a suitable method for a given situation using case studies from projects conducted by Golder Associates around the world over the last decade. - 1 - MINE EFFLUENT SOURCES: FROM EXPLORATION TO AFTER CLOSURE Disturbances to the ground start with drilling activities during exploration and continue until the site closure. Generation of poor water quality may start from the beginning of mining activities and may continue many years after the site is decommissioned. Sources of mining effluents that may require treatment include: Acid Mine (or Rock) Drainage (AMD or ARD) The management of waste materials such as tailings and waste rocks from mining of sulphidic metal and uranium ores and coal mines poses an environmental challenge to mining companies. Acid generation occurs when sulphide minerals (predominantly pyrite, FeS2 and pyrrhotite, FeS) contained in the waste material are exposed to oxygen and water (Kuyucak, 2001a, b; Kuyucak, 2002). Following the generation of acid, leaching of oxidized products occurs as rainwater and snowmelt enters the waste pile or dump. If sufficient alkaline or buffering minerals (for example, calcite) are not present to neutralize the acid, the resulting leach water becomes acidic with high concentrations of metal ions such as iron (Fe), manganese (Mn), aluminium (Al), zinc (Zn), copper (Cu), nickel (Ni), lead (Pb), cadmium (Cd), arsenic (As), etc. This water is generally known as acid rock drainage (ARD) or acid mine drainage (AMD). According to its acidity and metal content, AMD can be classified as low, medium, or high strength (Kuyucak et al., 1990). Acid generation can also be observed on roads, bridges, tunnels. Mine Dewatering - Ammonium and Nitrate Explosives made of ammonia and nitrate compounds are used for extraction of the ore. Solutions produced from mine dewatering may contain ammonia (NH4-N), nitrate (NO3) and, possibly, total suspended solids (TSS) and metal ions in elevated concentrations (Kuyucak, 1998). Careful management and proper disposal is necessary to prevent impacts to surface water and/or ground water resources. - 2 - Process Waters – Cyanide and Acids Different types of chemicals such as cyanide, sulphuric acid, and hydrochloric acid are used for processing of ores and recovery of metals. Cyanide (CN) is used for extraction of precious metals (i.e. gold, silver, and platinum) as well as conditioning of mineral processes such as flotation processes to improve recovery of base
Details
-
File Typepdf
-
Upload Time-
-
Content LanguagesEnglish
-
Upload UserAnonymous/Not logged-in
-
File Pages37 Page
-
File Size-