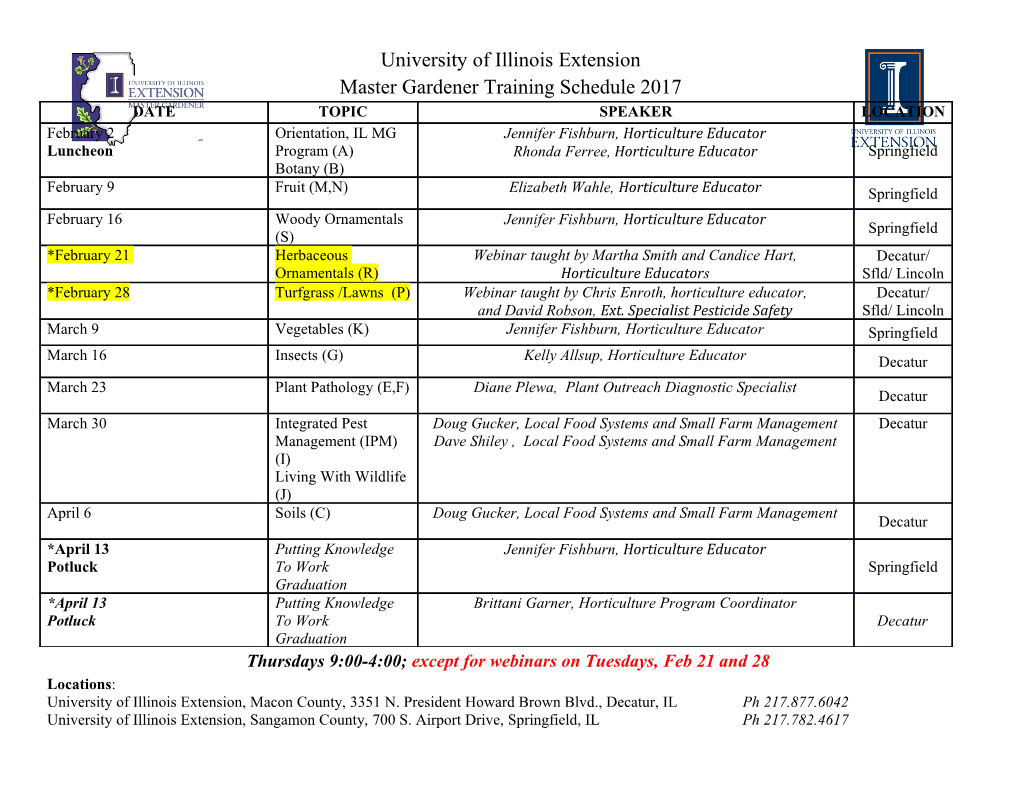
Opportunities and Challenges at the Interface between Petrochemistry and Refinery DGMK/SCI-Conference October 10-12, 2007, Hamburg, Germany Light Olefins – Challenges from new Production Routes ? H. Zimmermann Linde Engineering, Pullach, Germany Abstract Light Olefins are the building blocks for many modern plastic products and are produced in large quantities. Driven by high crude oil prices, production is shifted to regions with low cost raw materials. Alternatives to the traditional production from Naphta, AGO and other crude products are becoming attractive. This paper evaluates several methods Ethylene and Pro- pylene production economically and also the regional advantageous routes. The analysis includes Steamcracking, dehydrogenation, dehydration of Ethanol, Methanol based routes and olefin conversion by Metathesis. Introduction Almost 200 million t/a of light olefins are produced and processed to a variety of products. The production of the bulk products Ethylene and Propylene is traditionally based on Steam- cracking and separation of off-gases from refinery processes. However, today, with the dramatic change of raw material costs due to crude oil price development, a number of new processes are being utilized for the production of light olefins. 1. Light Olefin Production Routes The petrochemical production routes for light olefins are Steamcracking of hydrocarbons from Ethane to Naphta, AGO and even Hydrocracker bottoms, dehydrogenation of hydro- carbons, dehydration of alcohol, Methanol based routes and Metathesis. Economic comparison of the different routes is complex, since some routes (Naphtacracking) produce many valuable by-products. A first comparison can be made on the basis of selec- tivity of the routes as shown in Fig. 1. Due to the low conversion per pass, the Dehydrogenation of Ethane can be excluded for commercial production, as this route is not competitive to cracking of Ethane. The other processes have to be evaluated in detail in order to see the commercial competitiveness. 2. Steamcracking of Hydrocarbons Steamcracking of hydrocarbons is the most important method of producing Ethylene and Propylene today. Ethylene production is almost exclusively utilizing this route, whereas 70 % of the Propylene is produced via Steamcracking today. Steamcracking technology has been used for more than 50 years and can be summarized as shown below in Fig. 2. DGMK-Tagungsbericht 2007-2, ISBN 978-3-936418-70-5 75 Opportunities and Challenges at the Interface between Petrochemistry and Refinery Linde Engineering Light Olefins – Production Routes Selectivity % Conversion % Cracking of Ethane 82-84 64-75 Dehydro of Ethane 80 15-20 Dehydration of EtOH 97 -99 70-100 MTO 70 (E+P) 100 MTP 70 (P) 100 Metathesis 90 Dehydro of Propane 85-90 35-50 Linde AG Geschäftsbereich Linde Engineering 6 Zimmermann / DGMK 2007t Fig. 1: Light Olefin Production Routes Linde Engineering Steamcracking Steam Feed C2 H 4 , C 3 H 6 , C 6 H 12 , C H 4 + PyGas (C5-C10) +PFO(C10+ ) 820 -860 °C 0,2-0,5 sec Feed Steam / Feed (Typical) Ethane 0, 3 ( wt/wt) Propane 0,4 Naphta 0,5 AGO 0,6 HVGO 0,8 Linde AG Geschäftsbereich Linde Engineering 7 Zimmermann / DGMK 2007t Fig. 2: Steamcracking of Hydrocarbons The cracking reaction is carried out in cracking furnaces as shown in Fig. 3. DGMK-Tagungsbericht 2007-2, ISBN 978-3-936418-70-5 76 Opportunities and Challenges at the Interface between Petrochemistry and Refinery Linde Engineering Steamcracking Furnace Linde AG Geschäftsbereich Linde Engineering 9 Zimmermann / DGMK 2007t Fig. 3: Cracking Furnace Modern Steamcracking Plants have capacities of up to 1.5 million t/a Ethylene and a total olefin production (Ethylene + Propylene) up to 1.8 million t/a. Investment costs for such plants are in the range of 1 billion Euros. A typical view of a cracker is shown in Fig. 4. Linde Engineering 3D Model View of a Steamcracker 260 m 230 m Linde AG Geschäftsbereich Linde Engineering 10 Zimmermann / DGMK 2007t Fig. 4: 3D View of a Steamcracker Typical cracking yields for the different feedstocks are shown in Fig. 5. DGMK-Tagungsbericht 2007-2, ISBN 978-3-936418-70-5 77 Opportunities and Challenges at the Interface between Petrochemistry and Refinery Linde Engineering Steam Cracking Yields ( wt % ex Furnace) Feedstock Ethane Propane FR Naphtha AGO HCR H2 + CO 4.06 1.70 1.03 0.71 0.68 CH4 3.67 23.37 15.35 10.69 9.38 C2H2 0.50 0.67 0.69 0.34 0.43 C2H4 52,45 39.65 31.02 24.85 29.64 C2H6 34.76 4.57 3.42 2.75 2.77 C3H6 + C3H4 1.15 13.28 16.21 14.28 16.83 C3H8 0.12 7.42 0.38 0.31 0.37 C4 2.24 4.03 9.54 9.61 11.17 Pyrolyis Gasoline 0.87 4.27 19.33 20.6 17.73 Pyrolysis Fuel Oil 0.16 1.11 3.01 15.78 10.98 Dilution Steam / HC 0.30 0.35 0.50 0.80 0.80 Total HC Load 100% 132% 169% 211% 177% Linde AG Geschäftsbereich Linde Engineering 15 Zimmermann / DGMK 2007t Fig. 5: Cracking Yields As can be seen from the Fig. 5 Ethane can be cracked very selectively compared to Ethyl- ene, whereas all other feedstocks produce significant quantities of by-products such as Methane, Propylene, C4- cut, Benzene, Pygas (Pyrolysis Gasoline) and Pyrolysis Fuel Oil (PFO). The attractiveness of Ethane cracking can be explained by the selectivity but also the regionally advantaged Ethane price contributes to the outstanding economics of Ethane cracking. Costs of 0,75 to 1,6 USD per MM BTU equivalent to 40 to 85 USD /t are typical for Middle East locations and countries like Venezuela, where several cracker projects are in the planning phase. Low cost Ethane cracking has an advantage of 300 to 400 USD per t of Ethylene in produc- tion costs compared to Naphta cracking at market price. The huge difference is the driver for all new investments in areas with advantaged feedstock costs as shown in Fig. 6. Linde Engineering Market - Feedstocks Key Areas of Oil & Gas Exploration Norway Caspian China Egypt Gulf Algeria of Mexico South East Asia Peru, West Colombia, Africa Middle East Ecuador and countries Iran, Venezuela Iraq, Qatar, UAE Linde AG Geschäftsbereich Linde Engineering 21 Zimmermann / DGMK 2007t Fig. 6: Key Areas with advantaged feedstock costs DGMK-Tagungsbericht 2007-2, ISBN 978-3-936418-70-5 78 Opportunities and Challenges at the Interface between Petrochemistry and Refinery The detailed comparison of Ethylene production costs by cracking of Ethane and Naphta is shown in Fig. 7 on the basis of a 1 million t/a cracker including raw materials, capital costs, operation costs as well as overhead and maintenance costs. Linde Engineering Comparison Ethane / Naphtacracker (Basis 1MM MTA) Production Costs 2007 USD /t Ethylene Overhead 900,00 Operation 800,00 Raw Material 700,00 Depreciation 600,00 500,00 400,00 300,00 200,00 100,00 0,00 Naphta / Europe fully depreciated Ethan Naphta Plant Linde AG Geschäftsbereich Linde Engineering 24 Zimmermann / DGMK 2007t Fig. 7: Comparison of Ethane and Naphta cracking Fig. 7 also indicates that a fully depreciated cracker in Europe has excellent economics but cannot reach the production cost of an Ethane cracker. However, Ethane availability is limited in the Middle East and other raw materials have to be utilized. Fig. 8 shows a comparison between new Saudi Cracker economics and an existing European cracker and one can see that due to a discount of 30% for some feedstocks, cracking in this area is advantaged. Without the discount, the situation would be different and the European cracker would be quite competitive. Linde Engineering Saudi Crackers (new) compared with European (existing) Discount of 30% on Propane and Butane USD / ton of Ethylene 900 800 700 600 500 400 300 200 100 0 Ethan E/P 50/50 Butan E/B 50/50 Naphta / Europe Linde AG Geschäftsbereich Linde Engineering 25 Zimmermann / DGMK 2007t Fig. 8: Comparison of Crackers based on different feedstocks DGMK-Tagungsbericht 2007-2, ISBN 978-3-936418-70-5 79 Opportunities and Challenges at the Interface between Petrochemistry and Refinery 3. Alternative Processes for Ethylene Production An alternative route for production of Ethylene is the dehydration of Ethanol, which has a very high selectivity. A summary of the production costs by Ethanol dehydration are shown in Fig. 9. Linde Engineering Dehydration of Ethanol C2H5OH -------ÆC2H4 + H2O ( Cat , 300°C) Production: 500 000 MTA Ethylene Per ton C2H4 S: ,097 Weight Yield : 60,86 % Raw Material: 846 966 MTA @ 300 USD (400) 508 USD (677) Investment 500 MM USD @20% 200 USD Operation 20 USD Overhead & Maintenance @ 5% of Invest 50 USD Sum production Cost 778 USD (947) Linde AG Geschäftsbereich Linde Engineering 26 Zimmermann / DGMK 2007t Fig. 9: Summary of Ethylene production costs via Ethanol dehydration Methanol-based Ethylene production via MTO is one of the routes which creates a lot of interest. A process is offered by UOP / Hydro based on a special zeolithe catalyst. The process flow diagram is shown in Fig. 10. Linde Engineering UOP /Hydro MTO process Quench Caustic C2 C3 Reactor Regenerator Tower Wash De-C2 De-C1 Splitter De-C3 Splitter De-C4 Tail Gas Regen Gas Ethylene Propylene Dryer Mixed C4 DME Recovery C2H2 Reactor C5+ Air Water Propane Ethane Methanol Source : UOP Linde AG Geschäftsbereich Linde Engineering 11 Zimmermann / DGMK 2007t Fig. 10: UOP / Hydro MTO process DGMK-Tagungsbericht 2007-2, ISBN 978-3-936418-70-5 80 Opportunities and Challenges at the Interface between Petrochemistry and Refinery The economics for Ethylene production via MTO are shown in detail in Fig. 11. Linde Engineering MTO Economics for Ethylene 750 000 MTA Ethylene 750 000 Propylene Per ton Ethylene Raw Material 3 428 571 MeOH @ 200 USD (250) 1306 (1632) Byproduct Credit - 1040 Net Raw Material 266 (592) Investment 2 500 MM USD @20 % 666 Operation 13 Maintenance & Overhead @ 5 % of Invest 166 Production Cost 1112(1439) Linde AG Geschäftsbereich Linde Engineering 27 Zimmermann / DGMK 2007t Fig.
Details
-
File Typepdf
-
Upload Time-
-
Content LanguagesEnglish
-
Upload UserAnonymous/Not logged-in
-
File Pages12 Page
-
File Size-