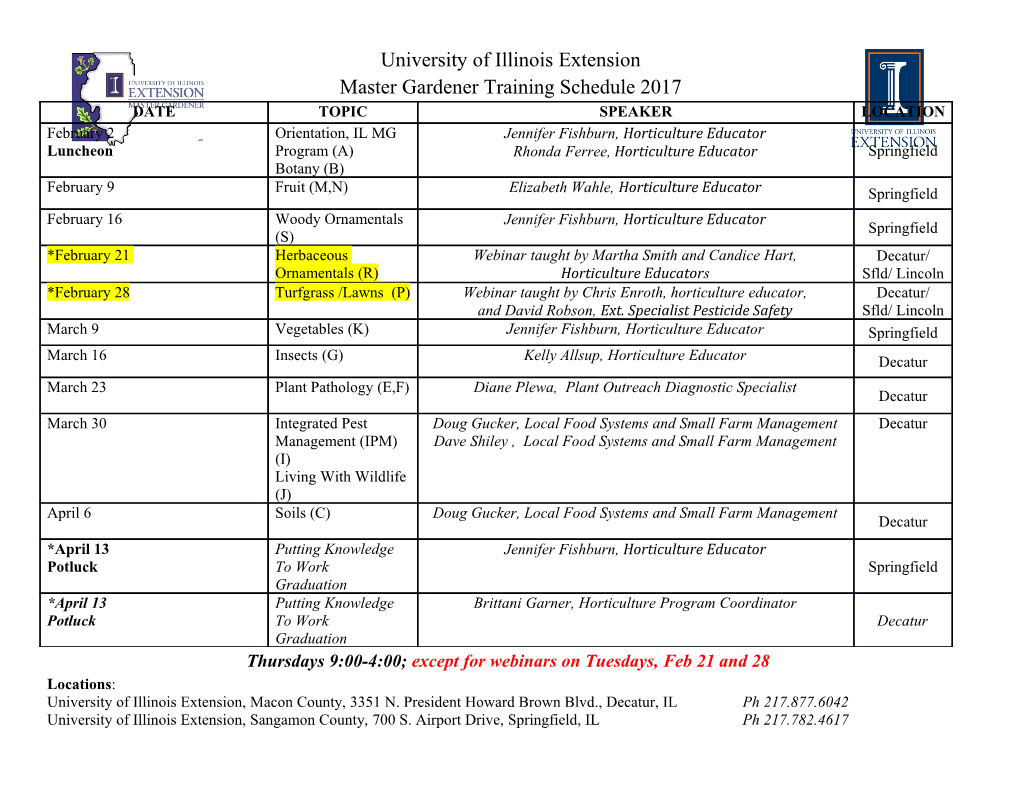
This material is intended solely for internal use by Mauna Loa Helicopters and is not for distribu=on. Mauna Loa Helicopters is not responsible for, and expressly disclaims all liability for, damages of any kind arising out of use, reference to, or reliance on any informa=on contained in this document. While the informa=on contained within the document is periodically updated, no guarantee VFR Book is given that the informa=on provided is correct, complete, and up-to-date. Ownership of all materials is held by original copyright holders. Bibliography Helicopter Flying Handbook. Oklahoma City: United States Department of Transporta=on, Federal Avia=on Administra=on, 2012. Pilot’s Handbook of Aeronau:cal Knowledge. Oklahoma City: United States Department of Transporta=on, Federal Avia=on Administra=on, 2008. Federal Avia:on Regula:ons and Aeronau:cal Informa:on Manual. Newcastle, Washington: Avia=on Supplies and Academics Inc., 2015. AircraB Weight & Balance Handbook. Oklahoma City: United States Department of Transporta=on, Federal Avia=on Administra=on, 2007. Robinson R-22 Pilot Opera:ng Handbook. Torrance, California: Robinson Helicopter Company, 1979. Wagtendonk, W.J. Principles of Helicopter Flight. Newcastle, Washington: Avia=on Supplies and Academics Inc., 2006-2011. GFD Instrument/Commercial Textbook. Englewood, CO: Jeppesen Sanderson Inc., 1998-2006. Avia:on Weather. Published jointly by the FAA Flight Standards Service and the Na=onal Weather Service (NWS). Newcastle, Washington: Avia=on Supplies and Academics Inc., 1975. Avia:on Weather Services, Advisory Circular 00-45G, Change 1. Published jointly by the Na=onal Weather Service (NWS) and the Federal Avia=on Administra=on (FAA). Newcastle, Washington: Avia=on Supplies and Academics Inc., 2010. Swan, John. Robinson R22: A Pilot’s Guide. Newcastle, Washington: Avia=on Supplies and Academics Inc., 2001. Lesson #1: Helicopter Components Objective This lesson will introduce the student to the components, systems and instruments of the Robinson R22. The student will also gain an understanding of the SFAR 73 to Part 61. Lesson #1: Helicopter Components Structural Airframe • The primary fuselage structure is made of welded steel tubing and riveted aluminum panels. Fiberglass Thermo Plastic • The materials used for some of the non-structural components of the R22 such as doors, ducts, fairings and secondary cabin structures Firewall • Is a stainless steel plating situated forward and above the engine compartment to provide added structural protection as well as separation to the pilot and cabin in case of engine fire. Lesson #1: Helicopter Components Structural Tail Cone Stabilizer • Is an aluminum monocoque structure in which the skin carries • Both vertical and horizontal, improve aircraft stability in cruise the primary load. flight. • Dents or damage in the skin of the tail cone create weakness - The vertical stabilizer helps improve left/right yaw stability. in the conical structure preventing it to withstand its maximum - The horizontal stabilizer helps fore/aft rotation during leverage. forward flight. • During pre-flight it is important to inspect the tail cone for any damages and report any findings to your instructor or maintenance. Lesson #1: Helicopter Components Structural Skids • The R22 has skid type landing gear built to spring and yield. • Hard landings are absorbed by elastic flexing of the cross tubes. • Extremely heavy landings will cause the cross tubes to yield, causing the four struts to hinge, up and out. • Skids Shoes are are placed at three different positions on the underneath side of each skid to prevent wear due to ground run and general use. • Preflight Note - Yielding in the cross tubes can be measured by the height of the tail strike guard (stinger). - If it’s less than 34” off the ground when sitting empty, the cross tubes must be replaced on Beta and Beta II’s. - Wearing of the skid shoes should also be checked. When the thinnest point is less than 1/16” they should be replaced. (thickness of the pre-flight checklist) Exterior Dimensions • Width including skids = 76” • Height (ground to the top of the Lesson #1: Helicopter Components Rotor System Main Rotor • The main rotor consists of two blades attached to the hub by coning hinges. • The hub is attached to the rotor shaft by a teeter hinge. Rotor Hub • The main rotor blades are mounted to the main rotor hub by the Blade Grips. • Inside the hermetically sealed blade grip housing, at the blade root, is where you will be able to find the spindle bearings which allow for a pitch change (feathering). Teeter Hinge • The center most hinge, allows rotor hub and thus the rotor disc to teeter as one unit. • Flap in unison so when one flaps up the other flaps down (see-saw). Rotor Hub • Unique to Robinson, allow the blades to cone. • Other helicopters eliminate this hinge through the use of the flapping hinge or by having blades that can bend and flex. Lesson #1: Helicopter Components Rotor System Pitch Horn • The structure that protrudes from the blade grips and allows control inputs (collective and cyclic) to change the pitch angle of the blades (feather). Pitch Link • The connector arms between the swashplate and pitch horns. Lesson #1: Helicopter Components Rotor System Swashplate • The mechanical link between the stationary controls and the rotor blades. • This allows the control inputs from the cyclic and/or collective, to change the pitch of the blades. • Lower ‘stationary’ swash plate: is connected to the control rods which are mechanically linked to the controls (cyclic and collective). • Upper ‘rotating’ swash plate: connected to the pitch links which transfer the control inputs to the blades. • The upper and lower swashplates interface through the use of a uniball-bearing allowing for the upper swashplate to rotate freely on the lower swashplate. • Inputs from the cyclic, change the pitch at different positions of the blades path. (at one point during the Cycle of rotation). • Inputs from the collective change the pitch of the blades evenly (Collectively) throughout its rotation. Lesson #1: Helicopter Components Rotor System Main Rotor Blades • 25’2” in diameter • Chord (width) of 7” • Twist of -8° from root to tip • All Metal Composition: - “D” shaped stainless steal leading edge called the D- spar - Aluminum honeycomb filler - Aluminum skin. • Symmetrical blades - Upper and lower camber are symmetrical. • Normal Operating Blade speed: - 104% tach = 530 Actual RPM - Tip Speed @ 100% = 672 FPS - Delamination is a rare occurrence when the skins begin to de-bond (separate) at the skin-to-spar bond lines. Lesson #1: Helicopter Components Rotor System Tail Rotor Blades • All metal construction; forged aluminum root fittings with wrap around aluminum skins • Asymmetrical in structure • The Tail Rotor diameter is 3’6” wide and has a chord of 4” with zero twist. • The Tail Rotor has a fixed coning angle of 1 degree 11 minutes rather than having a coning hinge. Semi-rigid System • Blades are able to feather and teeter. • Utilizes an Offset Teetering Hub (Delta Hinge) which is constructed at about a 45 degree angle in order to allow pitch change when the tail rotor flaps. - The 45˚ is the angle of the blades flapping axis, that allows for pitch angle change. - As a result, the Delta Hinge allows the tail rotor to be closer to the tail boom because the combination of teeter and pitch change corrects for aerodynamic forces more efficiently. Tail Rotor tip speed @ 100% = 599 FPS Lesson #1: Helicopter Components Power / Drive System Power Plant • Models: Lycoming 0-320 (Beta) or, Lycoming 0-360 (Beta II) • Type: Four Cylinder, horizontally opposed, direct drive air cooled, carbureted, normally aspirated. • 0-320 B2C - 160 BHP @2700 RPM (Alpha & Beta) • 0-360 J2A - 145 BHP (derated by lycoming from 180 BHP) @2700 RPM (Beta II) • Maximum Continuous Power (MCP) rating: 124 BHP @ 2652 RPM (104% tachometer) • 5 Minute TakeOff Power (TOP) rating for Beta & Beta II only: 131 BHP @ 2652 RPM Lesson #1: Helicopter Components Power / Drive System Power Plant • Engine Deration, Why? - Increase capability when operating at higher altitude. - Increase the life of the engine and life limited parts. - Less stress on the rest of the helicopter components along with a lighter construction. - Allows you to use smaller/less robust parts which helps cut down on weight. - As a result, Lycoming was able to make certain engine components out of lighter weight materials and thinned out the cylinder walls. • How is it limited to the 124/131 BHP ratings by Robinson? - The limitations are complied with by following the MAP chart, which tells you how much pressure (Hg) you can pull and is read off the MAP gauge. - By not pulling too much power (collective). Lesson #1: Helicopter Components Power / Drive System Power Plant • Normally Aspirated - The combustion air entering the engine is not forced, rather it depends on a partial vacuum to draw air into the intake. Induction air passes through a flexible duct to the carburetor air box. • Cooling System - A squirrel-cage fan mounted to the engine output shaft that supplies cooling air to the cylinders and oil cooler via a fiberglass and aluminum shroud. Ducts from the shroud supply cooling air to the alternator and main rotor gear box. • Reciprocating Engine - A series of pistons connected to a rotating crankshaft. As the pistons move up and down the crankshaft rotates. - The reciprocating engine gets its name from the back and forth movement of the internal parts. - Four different cycles that the four stroke engine undergoes to produce power; Intake, Compression, Power and Exhaust. Lesson #1: Helicopter Components Power / Drive System Power Plant • Detonation (knocking) - An uncontrolled explosive burn of the air fuel mixture within the combustion chamber, instead of the normal, smooth even burn. > Causes - high power setting, lean mixture and a lower grade of fuel (low octane) > Effects - engine overheating, roughness and loss of power > Corrections - reduce power, never use lower than specified fuel grades • Pre-ignition - The ignition of the mixture prior to the spark plug firing.
Details
-
File Typepdf
-
Upload Time-
-
Content LanguagesEnglish
-
Upload UserAnonymous/Not logged-in
-
File Pages346 Page
-
File Size-