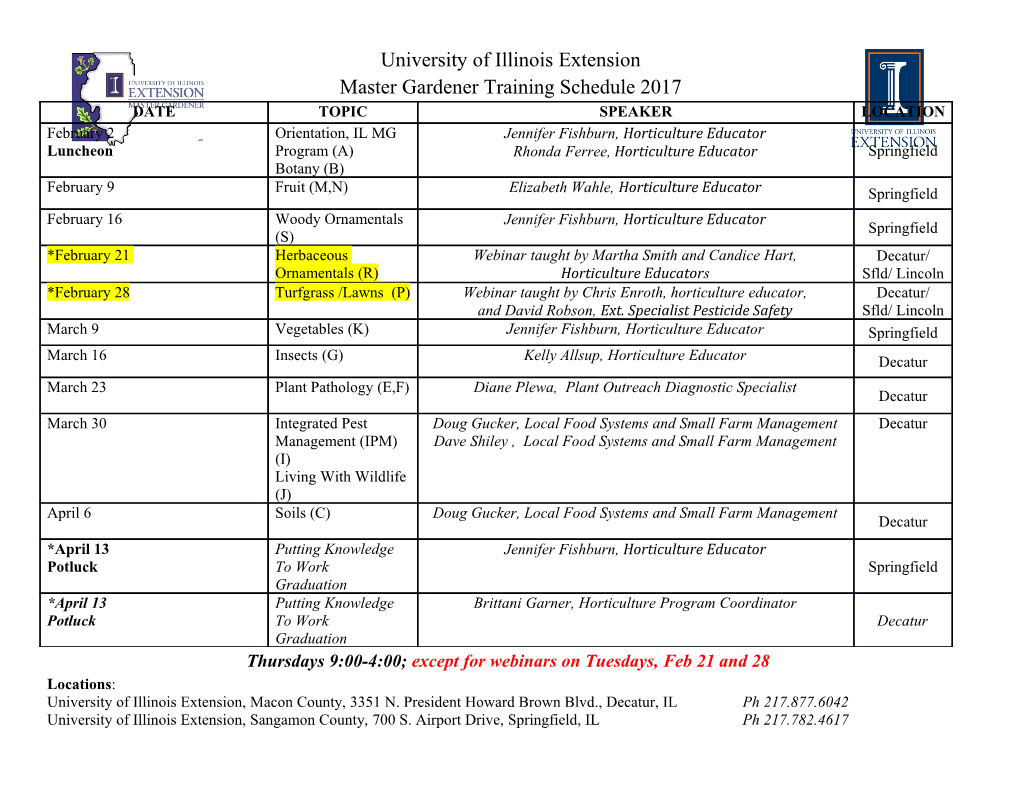
MATEC Web of Conferences 129, 02009 (2017) DOI: 10.1051/matecconf/201712902009 ICMTMTE 2017 Simulation of boron and carbon fiber composite characteristics of the elasticity Victor .P. Pavlov1, Vilina. M. Kudoyarova2,*, and Alexander. A. Philippov1 1Ufa State Aviation Technical University, Chair of Strength of Materials, st. K. Marcsa,12, Ufa, 450000, Russian Federation 2Ufa State Aviation Technical University, Chair of Aviation Thermal and Energy Engineering, st. K. Marcsa,12, Ufa, 450000, Russian Federation Abstract. The use of hybrid fiber-reinforced polymer composites (FRP) opens up wide possibilities for creating structures that are most suitable for different operating conditions. The modelling of a multilayer FRP structure is the most important stage in the creation and manufacture of FRP products since the FRP structure determines the entire complex of elastic, strength and other properties. This paper proposes a method for the theoretical prediction of anisotropic elastic characteristics of material equivalent to a given FRP. A technique for calculating the stiffness coefficients of a homogeneous anisotropic material equivalent to a hybrid composite material having a magnesium matrix reinforced with boron and carbon fibers has been developed and tested in ANSYS. This paper has found that the results of the finite element analysis essentially depend on the dimension of the mesh, and it is necessary to use a mesh with a number of nodes exceeding N = 1·105 to obtain sufficiently accurate calculated values of the elasticity coefficients. 1 Introduction element method (FEM) is implemented by using the ANSYS. The FRP of two or more kinds of reinforcing fibers are widely used in modern technology-based products, e.g. boron and carbon fibers. For the strength and stiffness 2 Problem definition calculation, an equivalent homogeneous anisotropic The paper considers a FRP composite with a given material usually replaces the heterogeneous FRP, for mechanical characteristics (matrix and reinforcement) which the mechanical properties will be determined [1- and orientation of the fibers. 12]. This paper builds the theoretical prediction task of The experimental simulation of properties FRP the anisotropic elastic material characteristics that are composites is very time-consuming [13-19], and a wide equivalent to the FRP composite. An equivalent material variety of structures FRP composites does not allow to is considered to be obeying to the linear Hooke's law study the characteristics for all possible variants. [20]. Therefore, computer simulation of the mechanical characteristics FRP materials for its various structures is very promising [8-12]. 3 Formation a FRP Composite Two problems arise: Representative Element • What do we take as an equivalence for considering heterogeneous FRP composite and for homogeneous In order to predict the mechanical characteristics of the anisotropic material? hybrid FRP, it is necessary to specify its structure and • How do we determine the effective elasticity the mechanical characteristics of its components. characteristics of an equivalent anisotropic material? The real FRP structure has a significant It should be noted that there is no unequivocal indeterminacy which is associated with the fact that FRP solution of these problems, and each researcher can consists of many fibers of small diameter, and it is realize his own path. almost impossible to dispose the fibers by a uniquely This paper considers a technique for mathematical defined law. We can only orient the fiber's threads in modeling of the elasticity characteristics of FRP having space as a whole and even then not with absolute carbon and boron fibers, based on the FEM using exactness. In addition, the fibers combined into the FRP ANSYS. thread will be located at different distances unknown for The proposed work solves the mathematical each individual thread. modeling problem of the elasticity characteristics FRP It is possible to determine the average direction for composite having carbon and boron fibers. The finite the fiber bundle in the space and also determine the * Corresponding author: [email protected] © The Authors, published by EDP Sciences. This is an open access article distributed under the terms of the Creative Commons Attribution License 4.0 (http://creativecommons.org/licenses/by/4.0/). MATEC Web of Conferences 129, 02009 (2017) DOI: 10.1051/matecconf/201712902009 ICMTMTE 2017 proportions of one or the other type fiber in the volume VC of hybrid FRP by studying the structure and composition ΨС = = 0,339; V (2) of hybrid FRP experimentally. Ψ B Thus, we have assumed that we knew the directions ΨB = = 0,264. Ψ of the reinforcing threads and the coefficients of their concentration in the considering volume of hybrid FRP. The FRP reinforcement ratio for carbon fibers equal Based on this, we are applying some idealization and to ΨC = 0,339 and for boron fibers equal to ΨB = 0,264. forming the representative element for FRP composite based on magnesium binder reinforced with carbon and boron fibers to calculate its effective elastic 4 Modeling the elasticity characteristics characteristics. It has a rectangular prism form with ax, of FRP composite by using FEM ay, az side dimensions and contains a single boron fiber dB = 100 mic diameter, fourteen carbon fibers dC = 10 This paper considers a homogeneous anisotropic mic diameter. Boron fiber is oriented along to Y-axis, material is accepted as the equivalent for the FRP with carbon fibers are directed along X-axis (Fig. 1). the relationship between stresses σx, σy, σz, τxy, τyz, τxz and deformations εx, εy, εz, γxy, γyz, γxz that is determined by six relations [20]: σx = E11ε x + E12ε y + E13ε z + E14γ xy + E15γ yz + E16γ xz , σ = ε + ε + ε + γ + γ + γ y E21 x E22 y E23 z E24 xy E25 yz E26 xz , σ = ε + ε + ε + γ + γ + γ z E31 x E32 y E33 z E34 xy E35 yz E36 xz , (3) τxy = E41ε x + E42ε y + E43ε z + E44γ xy + E45γ yz + E46γ xz , τ = E ε + E ε + E ε + E γ + E γ + E γ , yz 51 x 52 y 53 z 54 xy 55 yz 56 xz τxz = E61ε x + E62ε y + E63ε z + E64γ xy + E65γ yz + E66γ xz , The stiffness coefficients of the equivalent material Eij, i, j = 1,6 are determined on the basis of mathematical modeling of the deformation for a FRP representative element at six numerical experiments, in Fig. 1. Representative element for FRP composite each of which only one of the strain components differs from zero. The distance between adjacent carbon fibers along In the first experiment ε x ≠ 0, εy = εz = γxy = γyz = γxz the Y- axis and the minimum distance between boron and =0. For this case the deformation of the representative carbon fibers equals to ΔC = 2 mic (fig. 1). The element is shown in Fig. 2. minimum distances from the carbon fibers to the side faces of the representative element that is perpendicular to the Y-axis and Z-axis are equal to ΔCY = 1 mic and ΔCZ = 1 mic, respectively, (fig. 1). The distance from the boron fiber to the side faces of the representative element that is perpendicular to the X-axis equals to ΔBX = 5 mic (fig. 1). In accordance with fig. 1 the representative element -4 -5 has the following sizes: ax = 1,1·10 m, ay = 1,2·10 m, -4 az = 2,7·10 m. We define for a representative element of the hybrid FRP for the indicated dimensions: total volume V, volume of the carbon component VC, volume of the Fig. 2. Linear deformation of a representative element along boron component VB: the X-axis −13 V = axayaz = 3,56 ⋅10 m, For all three faces of the FRP representative element 2 −13 (εx) (εx) (εx) (εx) (εx) (εx) VC = 14πdC ax / 4 = 1,21⋅10 m, (1) the averaged stresses σx , σy , σz , τxy , τyz , τxz = π 2 = ⋅ −14 VB dBay / 4 9,42 10 m. at given deformation are determined in ANSYS. The (εx) expressions of stiffness coefficients: E11 = σx /ε x , On the basis of these expressions, we determine the = σ(εx) ε , = σ(εx) ε , = τ(εx) ε , volume coefficients of FRP reinforcement by carbon E21 y / x E31 z / x E41 xy / x ε ε (ΨC) and boron (ΨB) fibers: ( x) ( x) E51 = τyz / ε x , E61 = τxz / ε x were obtained under substituting of averaged stresses in the first three equations of the system (1). Similarly, the elasticity coefficients Ei2 , i =1,6 and 2 MATEC Web of Conferences 129, 02009 (2017) DOI: 10.1051/matecconf/201712902009 ICMTMTE 2017 The remaining stiffness coefficients are equal to zero Ei3, i =1,6 of an equivalent anisotropic homogeneous in view of the presence of FPR composite’s plane material are determined by specifying the deformation symmetry. components different from zero ε y ≠ 0, and then ε z ≠ 0. To determine the stiffness characteristics under shear the deformation of the representative element under 6 Conclusion shear strain γxy ≠ 0, ε x = εy = εz = γyz = γxz =0 is considered (fig. 3), in which the averaged stresses 1. The representative element structure of a hybrid FRP σ(εx) , σ(εx) , σ(εx) , τ(εx) , τ(εx) , τ(εx) are calculated, and composite based on a magnesium matrix reinforced with x y z xy yz xz boron and carbon fibers is proposed. then the corresponding elasticity coefficients Ei4 , i =1,6 2. A technique for calculating the stiffness coefficients are also calculated. of a homogeneous anisotropic material equivalent to a hybrid composite material having a magnesium matrix reinforced with boron and carbon fibers has been developed and tested by using FEM in ANSYS. 3. It is found that the results of the finite element analysis essentially depend on the dimension of the mesh, and it is necessary to use a mesh with a number of nodes exceeding N = 1·105 to obtain sufficiently accurate calculated values of the elasticity coefficients.
Details
-
File Typepdf
-
Upload Time-
-
Content LanguagesEnglish
-
Upload UserAnonymous/Not logged-in
-
File Pages4 Page
-
File Size-