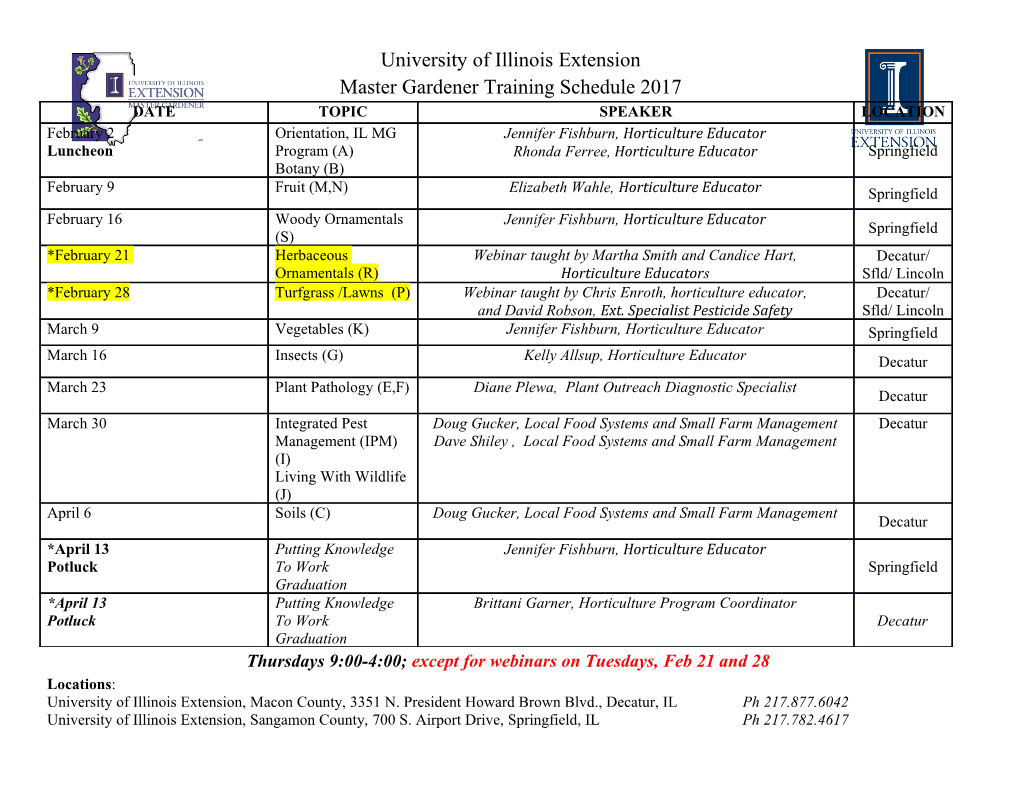
The statistics that summarize a population are referred to as categorical statistics descriptive statistics probabilistic statistics control statistics 1 The following chart was developed by a six sigma team to measure reactions on two different products. In this chart, temperature represents the repetition factor response level 2 Which of the following measures is increased when process performance is improved? Variability range Capability index Repeatability index Specification limits 3 Which of the following tools can be used to identify and quantify the source of a problem? Affinity diagram Control chart Pareto chart Quality function deployment 4 A correlation analysis is used to provide a numeric value for which of the following type s of relationships between two variables? Random Linear Curvilinear Causation 5 Which of the following tools is used to translate broad requirements into specific requirements? A quality control plan The theory of constraints (TOC) A critical to quality (CTQ) tree A process flowchart 6 Which of the following tools is used extensively in quality function deployment (QFD)? Affinity diagram Matrix diagram Cause and effect diagram Activity network diagram 7 Which of the following control charts is used to monitor discrete data? p I & mR X̄ X̄ – R 8 Which of the following shapes is used to present a termination point in a flowchart? Rectangle Diamond Arrow Oval 9 For a normal distribution, two standard deviations on each side of the mean would include what percentage of the total population? 95% 68% 47% 34% 10 Which of the following is a commonly accepted level for alpha risk? 0.05 0.50 0.70 0.95 11 When the sampling method used creates a difference between the result obtained from the sample and the actual population value, the difference is known as correlation precision accuracy bias 12 Which of the following is an example of mistake-proofing? Using an X̄ - R chart to prevent errors Using 100% inspection to detect and contain defects Using color coding as an error signal Having the team that created the errors repair them 13 Which of the following is the key objective of a six sigma project? Developing detailed control charts for critical processes Developing a matrix to understand the how’s and what’s of a problem process Reducing variation in critical processes Reducing investment costs while improving output quality 14 Which of the following tools is used to identify potential events and contingencies for an implementation plan? PERT chart Process decision program chart Fishbone diagram House of quality 15 Which of the following measures is used to show the ratio of defects to units? DPU DPO DPMO PPM 16 Which of the following terms is used to describe the risk of a type I error in a hypothesis test? Power Confidence level Level of significance Beta risk 17 Positional, cyclical, and temporal variations are most commonly analyzed in SPC charts multi-vari charts cause and effect diagrams run charts 18 In order for value flow analysis to be effective, a team must take which of the following steps first? Define the value stream Eliminate backlogs in the value stream Identify overlapping functions in the value stream Identify specific work practices within the value stream 19 When an inspection process rejects conforming product, what type of error is being made? α β σ H0 20 The critical path for a project is best described as the sequence of steps with the highest costs tasks in the project that have the highest risk of failure sum of the tasks with the shortest time requirements longest path from the start to the completion of the project 21 Which of the following graphs represents a factorial experiment with the strongest interaction? 22 Statistical process control (SPC) is best defined as the use of Pareto charts to understand and control a process inputs to control critical and complex processes statistical methods to identify and remove manufacturing errors statistical methods to understand and control a process 23 A measurement system analysis is designed to assess the statistical properties of gage variation process performance process stability engineering tolerances 24 When calculating the Cp index, what does the standard deviation represent in the formula ? The tolerance interval The confidence interval for the result The range of the process The variance of the index 25 Why do organizations use Six Sigma (6σ)? Bottom Line Benefits Customer Satisfaction Continuous Improvement All of the above Six Sigma is a methodology for pursuing continuous improvement in customer satisfaction and profit that goes beyond defect reduction and emphasizes business process improvement in general. Six Sigma enables quality and continuous improvement to achieve the highest level of customer satisfaction. 26 Corporate scorecards are organized around financial, customer, internal process, learning and growth metrics. As these areas are broken down into components, projects are NOT limited to: Sigma quality level, defect rate Ease and quickness of completion Profit and loss None of the above Organizations should not just measure against sigma quality levels and/or process output defect rates. 27 What is the best way to select six sigma projects when addressing customer satisfaction issues? Problem Focus Product Focus Project Cost Savings Focus Process Focus The correct answer is: D –Process Focus –Overall, this is the best way to the root causes of defects and customer satisfaction issues. The key is identifying the processes that are critical to satisfaction and are operating at low sigma level. A, B, C –are all ways to select the projects, however when it comes to addressing customer satisfaction issues, the process approach is the best. 28 What is the Goal of Lean Manufacturing? Reduction of defects Elimination of waste Increased profits All of the above Lean Manufacturing intents to reduce waste in all its forms 29 Which of the following is a value-added activity? Inspection Just-In-Time Inventory Defect Correction Waiting Just in time, yields exactly the right product inexactly the right place and exactly the right time 30 The “Theory of Constraints” Focuses its continual improvement on: Empowering the employee Removing system bottlenecks Reducing defect Improving the bottom line By Definition, the theory removes bottlenecks, the other choices relate to other quality methods 31 Quality Function Deployment (QFD) is commonly referred to as: The House of Quality Listening to the voice of the customer Quality Fundamentals A and B QPD Often referred to as listening to the voice of the customer and QFD (Quality Function Deployment or the house of quality, a term coined QFD because of the shape of its matrix 32 The primary purpose of a Failure Modes and Effects Analysis is to: Solve Problems Manage the Product or Service to Be Delivered Manage Failure Risks Satisfy the Customer “FMEA is a specific methodology to evaluate a system design, process, or service for possible ways in which failures (problems, errors, risks, concerns) can occur.” 33 A DMADV approach is used for a product At the end of its product life Product is not in existence That has been recalled The customer sees no added value in it DMADV is design, product is being created 34 The roles and responsibilities of a Champion include all of the following EXCEPT: A Champion selects the Team Leader. A Champion reviews team progress. A Champion coordinates team logistics. A Champion assures the use of Six Sigma methods and tools. The Process Owner is responsible for coordinating team logistics. 35 The benefits of a process map include all of the following EXCEPT: Serves as a training and orientation tool Helps identify when and where to collect data Helps determine sigma values Identifies non value added activities The process flow map does not allow the user to determine sigma values 36 The roles and responsibilities of a Green Belt include all of the following EXCEPT: A Green Belt mentors Black Belts and Green Belts. A Green Belt is a part-time (25%) project leader or member and provides most of the functions of a Black Belt (Team Leader) for lower level project teams. A Green Belt analyzes data. Green Belts are the “work horses”of Six Sigma management. The Master Black Belt is responsible for coordinating team logistics. 37 An early step in any project must be seeking the voice of the internal and external customers of a project. This statement is: False, because projects should only be concerned with external customers. True, because both internal and external customers can be impacted by the project. True, because a project team wants to maintain good will with all customers. False, because internal projects only impact internal customers. Projects need to consider all stakeholders, including internal and external customers. 38 Which of the following methods is an effective tool to use when collecting customer data: Written surveys. Focus groups. Interviews by phone or in person. All of the above. Written surveys can be sent to a randomly selected group of customers or potential customers. Focus groups are an attempt to improve the depth and accuracy of the responses. Interviews by phone or in person permit a higher response rate than written surveys; a skillful interviewer can record customer feelings that written surveys wouldn’t detect. 39 Which quality management tool displays connections between customer needs and various product features? Parameter (P) Diagram Quality Function Deployment Cause and effect Diagram Relationship Matrix By definition 40 Which of the following quality terms is most closely associated with Quality Function Deployment (QFD)? House of Quality. SIPOC. Process flow diagram. Focus groups. One of the methods used in Quality Function Deployment is the “house of quality.” The house of quality is a graphical display, which includes prioritized customer needs, design requirements, relationship of design to needs, customer rating of competitors, technical benchmarks, correlation of design requirements, technical evaluation, and performance targets.
Details
-
File Typepdf
-
Upload Time-
-
Content LanguagesEnglish
-
Upload UserAnonymous/Not logged-in
-
File Pages19 Page
-
File Size-