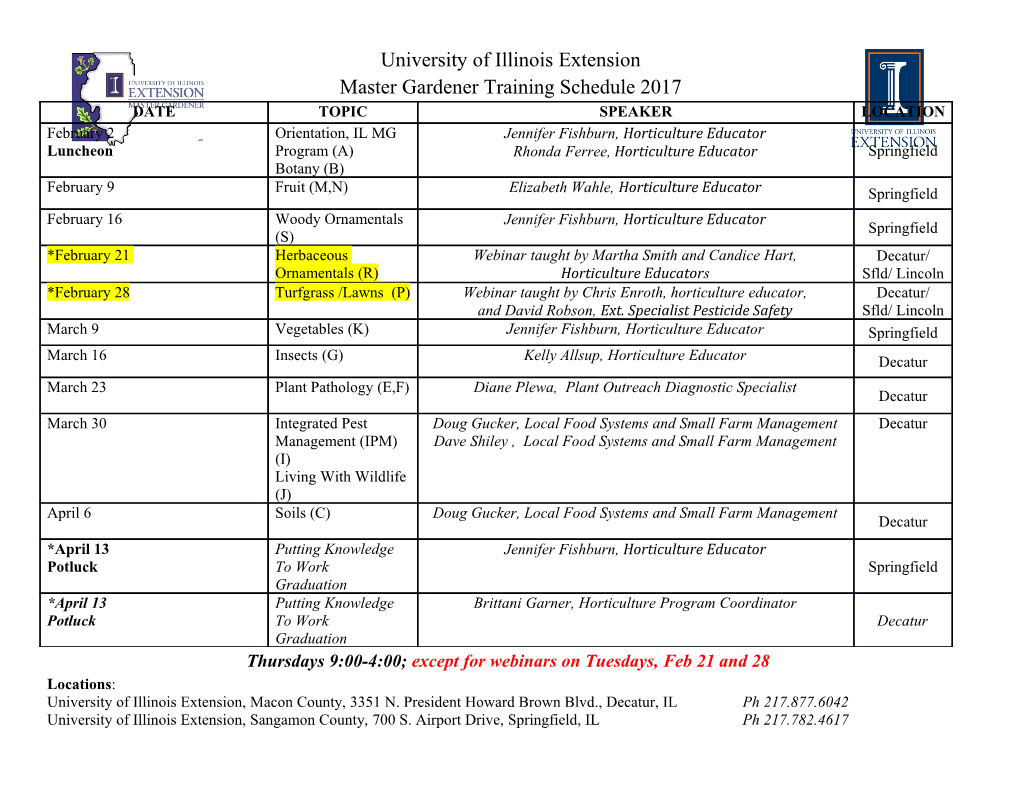
Int J Turbo Jet Eng 2020; aop Foroozan Zare and Árpád Veress* Novel Closed-Form Equation for Critical Pressure and Optimum Pressure Ratio for Turbojet Engines https://doi.org/10.1515/tjj-2019-0039 energy sector too. Significant amount of research has Received October 07, 2019; accepted October 23, 2019 been carried out in analyzing and developing gas turbine – Abstract: Advanced mathematical model has been devel- systems [3 5] and system components [6, 7]. oped for design and analysis of turbojet engines. It The gas turbines are currently the only available pro- includes closed form algebraic equation for critical pres- pulsion systems for high-powered commercial and military sure and optimum pressure ratio at maximum thrust. The airplanes. Although their thermodynamic cycles do not model and the algebraic equations consider efficiencies, have high core thermal efficiency (~ 28 to 38 %), the jet pressure recovery rates meanwhile the gas parameters are engines have substantial advantages in overall power, the function of the fuel to air ratio and the temperature. power density, compactness, streamlining, simplicity and РД-9Б and АЛ-21Ф3 engines are applied for demonstrat- low maintenance cost demands. These power units are ing the capabilities of the calculation process. The also less sensitive to overloads and produce less vibration unknown parameters as efficiencies, pressure recovery due to the well balanceable and rather axisymmetric rota- rates, power reduction rate of the auxiliary systems, tional components. The gas turbines have high availability – bleed air ratio, air income ratio due to blade cooling (80 99 %), reliability, which can exceed 99 % and low and total temperature in the afterburner were identified emissions (there is no lubricant in the combustion cham- ber and no soot during transient loads). They have fewer by constrained optimization. The effect of i. T04/T02 ratio for the thrust and TSFC in the function of compressor moving parts and lower sensitivities to fuel composition. pressure ratio, ii. the real (viscous) flow conditions and Additionally, gas turbines do not need a liquid-based cool- iii. the temperature and fuel to air ratio on gas parameters ing system, although the maximum allowable temperature were also investigated for verification and plausibility (~ 1500 °C) at the turbine inlet section is limited due to check. metallurgical reasons [8]. Beside the technical level of gas turbines today, there Keywords: jet engine, thermodynamics, cycle analysis of are many possible areas for potential improvements of real engine, critical pressure ratio, optimum compressor their efficiency, power and emissions. Although the expe- pressure ratio riences and the know-how of the gas turbine manufac- turers are increasing continuously, developing more ® PACS (2010). 07.20.Pe, 89.40.Dd, 05.70.-a, 88.05.Xj accurate mathematical models for determining the most suitable thermo-dynamical parameters and completing optimizations can significantly contribute to decrease Introduction cost, time and capacity in the early phases of design and developments. These are proven by the scientific In these days, there are many ongoing researches in the literature too; there are many research publications deal field of aeronautics [1, 2]. Regarding the power genera- with thermodynamic-based simulation approaches. tion, the application of heat engines is widespread not Homaifar et al. [9] presented an application of genetic only in the aerospace industry, but in the oil, gas and algorithms to the system optimization of turbofan engines. The goal was to optimize the thrust per unit mass flow rate *Corresponding author: Árpád Veress, Department of Aeronautics, Naval Architecture and Railway Vehicles, Faculty of Transportation and overall efficiency in the function of Mach number, Engineering and Vehicle Engineering, Budapest University of compressor pressure ratio, fan pressure ratio and bypass Technology and Economics, Műegyetem rkp. 3, Budapest H-1111, ratio. Genetic algorithms were used in this article because Hungary, E-mail: [email protected] they were able to quickly optimize the objective functions Foroozan Zare, Department of Aeronautics, Naval Architecture and involving sub functions of multivariate. Although the Railway Vehicles, Faculty of Transportation Engineering and Vehicle model used here to represent a turbofan engine is a rela- Engineering, Budapest University of Technology and Economics, Műegyetem rkp. 3, Budapest H-1111, Hungary, tively simple one, the procedure would be exactly the same E-mail: [email protected] with a more elaborate model. Results of assorted runs fixed Open Access. © 2020 Zare and Veress, published by De Gruyter. This work is licensed under the Creative Commons Attribution- NonCommercial-NoDerivatives 4.0 License. 2 F. Zare and Á. Veress: Novel Closed-Form Equation for Critical Pressure with experimental and single parameter optimization flows through can annular combustion chambers mounted results. Chocked condition was not considered, and the air in a single cover. The axial flow turbine has two stages with and gas properties were constant or averaged at the given a hydraulically-regulated nozzle situated behind the after- sections of the engine based on the used reference. burner chamber. The РД-9Б was designed as a light, power- Guha [10] determined the optimum fan pressure ratio ful engine for fighter aircraft, and it was used in the MiG-19S, for separate-stream as well as mixed-stream bypass MiG-19P, MiG-19PM and Yak-25 aircraft. The АЛ-21Ф3 turbo- engines by both numerical and analytical ways. The opti- jet aircraft engine is used in the Sukhoi Su-17, Sukhoi Su-24 mum fan pressure ratio was shown to be predominantly a and Sukhoi T-10. It can equal the GE J-79 engine as one of function of the specific thrust and a weak function of the the most powerful supersonic engines in service today. bypass ratio. The gas properties were constant in the Although the hereinafter introduced new equations expression of optimum fan pressure ratio for separate- and the thermodynamic calculation methodology are stream bypass engines at real flow condition. valid for single spool turbojet engines, they can also be Silva and his co-workers [11] presented an evolution- applied for other types of jet engines and goal functions ary approach called the StudGA which is an optimization in case of consistently adapted theoretical derivations. design method. The purpose of their work was to opti- mize the performance of the gas turbine in terms of minimizing fuel consumption at nominal thrust output, maximize the thrust at the same fuel consumption and Optimum compressor total pressure minimizing turbine blade temperature. ratio at maximum specific thrust Mattingly [12] published a detailed theoretical review about the rocket and gas turbine propulsion. There is a New equations have been introduced in the present chap- description also in that literature how the thermo-dynam- ter for determining the optimum pressure ratio pertaining ical cycles determine the mean characteristic of the jet at maximum specific thrust. The expressions apply the real engines. The author presented a closed-form equation for (viscous) flow assumptions and the temperature and mass the optimum compressor pressure ratio at maximum spe- fraction dependencies of the relevant gas properties. cific thrust at ideal (inviscid) flow condition. The effects of temperature and fuel to air ratio were not considered in parameters describe the gas properties. As the revised references used simplifications as New closed-form equation to determine the excluding the effect of chocked flow condition at con- optimum compressor total pressure ratio verging nozzle flow and gas properties with considering the local temperature and fuel to air ratio for example, it The derivation of the optimum pressure ratio at specific also confirms the need for developing physically thermodynamic condition including losses and variable advanced, more accurate mathematical models, calcula- gas properties was based on finding the extreme value of tions and optimizations. the specific thrust in the function of the compressor total Single spool turbojet engines are frequently used in pressure ratio. Hence, as the first step, the expression of commercial and military applications due to their low nor- the thrust was introduced in eq. (1) [13]. malized range factor1 and low emissions at relatively high РД Б flight speed. Two turbojets of this type, the -9 and the T = ½m_ 9V9 − m_ airV0 + A9ðÞp9 − p0 (1) АЛ-21Ф3 were thus used for testing and verifying the results of the presently developed mathematical model. The РД-9Б The mass flow rate at the exhaust nozzle was determined was the first engine, which includes a supersonic stage by eq. (2) [14]. compressor. It is a single-spool axial flow turbojet engine with a nine-stage compressor and an afterburner. The m_ 9 = m_ air½ðÞ1 − δtech ðÞ1+fcc + fA ðÞ1+δbc (2) engine has a bleed air dump control system depending on the compression ratio. Following the compressor, the air Concerning the well fitted converging-diverging nozzle, if the pressure ratio of the nozzle is over the critical one the flow at the exit has ambient pressure, the flow is 1 The range factor in this context is the fuel and engine masses are unchoked and the velocity is supersonic. Converging- divided by the thrust, which force is reduced by the drag force of the diverging nozzle was considered (see Figure 1) with cor- nacelle at given speed and range. rectly expanded flow conditions (p9 = p0) because of the F. Zare and Á. Veress: Novel Closed-Form Equation for Critical Pressure 3 Figure 1: Layout of single spool turbojet engine with afterburner [15]. used engines. Furthermore, for extending the application Here, as usual, the fuel to air ratio, f was calculated range of the equation, the optimum compressor pressure by the available fuel mass flow rate divided by the avail- ratio at maximum specific thrust was also derived for able air mass flow rate at the investigated section. only converging nozzle at choked nozzle flow condition.
Details
-
File Typepdf
-
Upload Time-
-
Content LanguagesEnglish
-
Upload UserAnonymous/Not logged-in
-
File Pages13 Page
-
File Size-