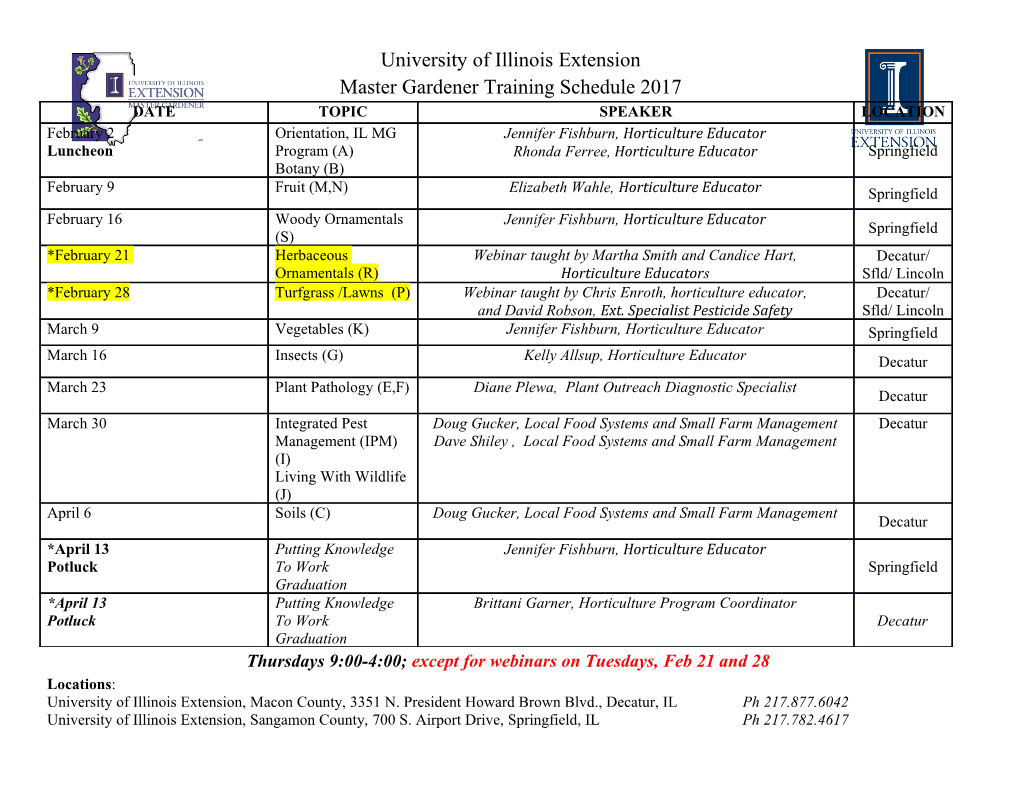
EDFAAO (2014) 3:14-19 1537-0755/$19.00 ©ASM International® How to Recognize Electromigration Electromigration History and Failure Analysis David Burgess, Accelerated Analysis [email protected] lectromigration is a wearout mechanism recog- Figure 2 shows additional details. Specifically, nized as an important cause of failure in semi- Fig. 1 shows dark spots in the wide collector contact. Econductor integrated circuits (ICs). Modern In Fig. 2, the dark spots are clearly voids or missing design rules necessarily push the limits for current aluminum. Electron current flow in the collector is density. Nevertheless, analysis of field failures rarely from the silicon into the metal. Voids in this loca- identifies electromigration as a cause of failure. This tion are consistent with electromigration; that is, the may be evidence that designers and reliability engi- electron wind tends to push metal away from the neers have achieved near perfection. Alternatively, it contact. Voids must occur because no aluminum is may be that electromigration in field failures is hard to available to replenish the vacated metal. Voids have recognize and even harder to prove. The mechanism also developed in the narrow collector metal at the remains, but its failure modes and visible evidence left in the photo. have changed. A contrasting situation exists in the emitter contacts Field Failure Example of where electrons flow from the metal into the silicon. Metal molecules pushed toward the emitter reach a Electromigration dead end. Aluminum piled up and caused mechani- Figure 1 is an optical microscope photo of electro- cal pressure on the transistor. Pressure on the emitter migration damage in a 1980s field failure. Irrefutable base junction caused a decrease in gain. The emitter evidence of electromigration is clearly visible. dark spots in Fig. 1 are bright spots in the second- ary electron microscopy (SEM) image in Fig. 2. The emitter defects are extrusions of aluminum pushed through the ruptured interlayer oxide. Another characteristic of electromigration is illu - strated in the lower right corner of Fig. 2. Electromi- Fig. 1 A large NPN output transistor is in the center of the photo. The failure mode was low gain of the transistor. The large “W” shape is the collector metal (aluminum) of the NPN. The two two-prong structures entering from the top are the emit- ter metal of the NPN. The narrow metal line snaking in from the right is the base of the NPN. Evidence of electromigration Fig. 2 Secondary electron image taken after top passivation was can be seen as dark spots in the collector and emitter metal. removed 14 Electronic Device Failure Analysis gration is driven by both current density and exposed to high current. Copious data showed the temperature. Note the large block of second-layer electromigration phenomenon to be a predictable and metal, which is connected to the collector through well-behaved mechanism. Measurements were made a large rectangular via. The bright spots in the via of time to failure of metal lines under controlled cur- are aluminum hillocks caused by electromigration. rent density and temperature conditions. Plots show Electromigration moved metal from the contact to- that lifetime is inversely proportional to the square ward the via. Metal entering the via was stuck there. of current density. Further, data show that lifetime Current density was lower in the thicker, wider metal as a function of temperature can be characterized by 2. Additionally, the massive block of metal acted as a a parameter called activation energy. Both variables heat sink and decreased the temperature, or, simply are included in one equation, now known as Black’s put, differences in current density and temperature equation: caused metal to enter the via at a faster rate than t = (A/J2) exp(E /kT) metal moved out. Electromigration caused metal to 50 a accumulate. where t50 is the median time to failure, A is a constant, E is the activation energy, and T is the temperature in This example provides a vivid picture of the ele- a Kelvin. Black’s equation has survived the years with ments of electromigration. These characteristics are as only minor adjustments. valid today as they were 30 years ago, and these basic elements arguably are sufficient for failure analysis. A very limited sampling of electromigration papers The elements are: is discussed here. The selected papers contain insight of value to failure analysts. Electromigration was a • Above a minimum current density, electron flow major obstacle to semiconductor design. Many papers can cause aluminum or copper to move in the direc- focused on material changes to improve electromigra- tion of electron flow. Momentum transferred from tion performance. Improvements of a factor of 2 re- many electrons creates a force on metal atoms. sulted from using large-grain rather than small-grain • Thermal energy causes metallic molecules to diffuse aluminum. Similar improvement was measured for or move within their crystal lattice. Electromigration metal with a glass or nitride overcoat. By suppressing occurs when momentum from a very heavy flow of the growth of hillocks, the transport of aluminum was electrons is transferred to thermally energized metal hindered. More significant improvement was gained atoms. The combination of heat and momentum by adding a few percent of copper in the alumi- [3] results in a tendency for the metal to move, or drift, num. Copper made grains smaller and clogged up in the direction of electron flow. the grain boundaries where aluminum electromigra- tion occurred. • “Failure is not caused by the movement of metal. From the above information, it may be expected Failure is caused by the unequal transfer of metal that missing passivation over a portion of a metal line into an area compared with metal transferred out would have an effect on electromigration of that line. of that same area.” This is loosely quoted from a The question is: Would a missing passivation defect video presented in 1985.[1] cause premature failure due to localized increased In the example cited here, metal moved away from rate of electromigration? An electromigration study the collector, creating voids and increasing resistance. of samples with intentional passivation “defects” Accumulation of aluminum in emitter contacts caused confirms that expectation. The study also shows that mechanical pressure on underlying silicon, causing the location of the defect is important. A passivation junction leakage and diminished transistor gain. defect located at the negative end of a metal strip re- After pressure in the metal caused rupture of the en- duces lifetime significantly more than a defect located [4] capsulating oxide, metal protrusions resulted. In this farther downstream. case, shorting did not occur. However, with different A life test of microwave power transistors[5] attaches geometry, electrical shorting is clearly a possibility. the electromigration mechanism to shorted junction failure, not just open metal. Nevertheless, test data fit Early History: Aluminum Black’s equation, with a calculated activation energy of 1.01 eV. Current density in affected metal was near Electromigration 1 × 105 A/cm2. The subject device has wide metal Electromigration has a fascinating, well-document- lines to limit current density. Obviously, a metal with ed history stemming from the problem of “cracked superior electromigration performance is required. strips” in 1967.[2] James Black demonstrated that However, even with a 10× improvement in lifetime, the cracks and electrical opens were the result of electromigration will impose a limiting factor for aluminum material moving within a metal strip aluminum in semiconductor design. Volume 16 No. 3 15 Electromigration History and Failure Analysis Reference 6 is invaluable for its visual documenta- width. Further, data show that time to failure reaches tion of how electromigration progresses and ends a minimum as line widths narrow to 1.5 to 2.0 mm. with an open failure. Time-lapsed SEM images show The reason for improved lifetime is that very narrow growth and movement of voids and hillocks. The metal lines are less likely to include any triple points paper also documents behavior of a thin oxide layer at all. When aluminum grain size exceeds line width, on the metal. For failure analysts, it provides a picture grain boundaries span all the way from one side to of the angular break associated with electromigration. the other. This geometry is known as a “bamboo” (This is in contrast to straighter breaks associated structure. Reference 8 addresses the effect of line with stress cracks.) Failure analysts should be aware width and line length for several aluminum alloys. that this break characteristic may be destroyed if a constant current caused electromigration. With con- Current History: Copper stant current, the current density will increase as the Electromigration conductor area decreases. The final open will come from melted metal. Copper metallization replaced aluminum as the metal of choice for multilayer metallization in By the late 1980s, aluminum electromigration was 130 nm and smaller technologies. Copper lines can be reasonably well understood. Perhaps more accurately, thinner and better suited for multiple layers. Lower the limitations of aluminum were defined and many resistivity and better electromigration performance aspects, such as line width and thickness, substrate are major advantages. The threshold current density roughness,
Details
-
File Typepdf
-
Upload Time-
-
Content LanguagesEnglish
-
Upload UserAnonymous/Not logged-in
-
File Pages6 Page
-
File Size-