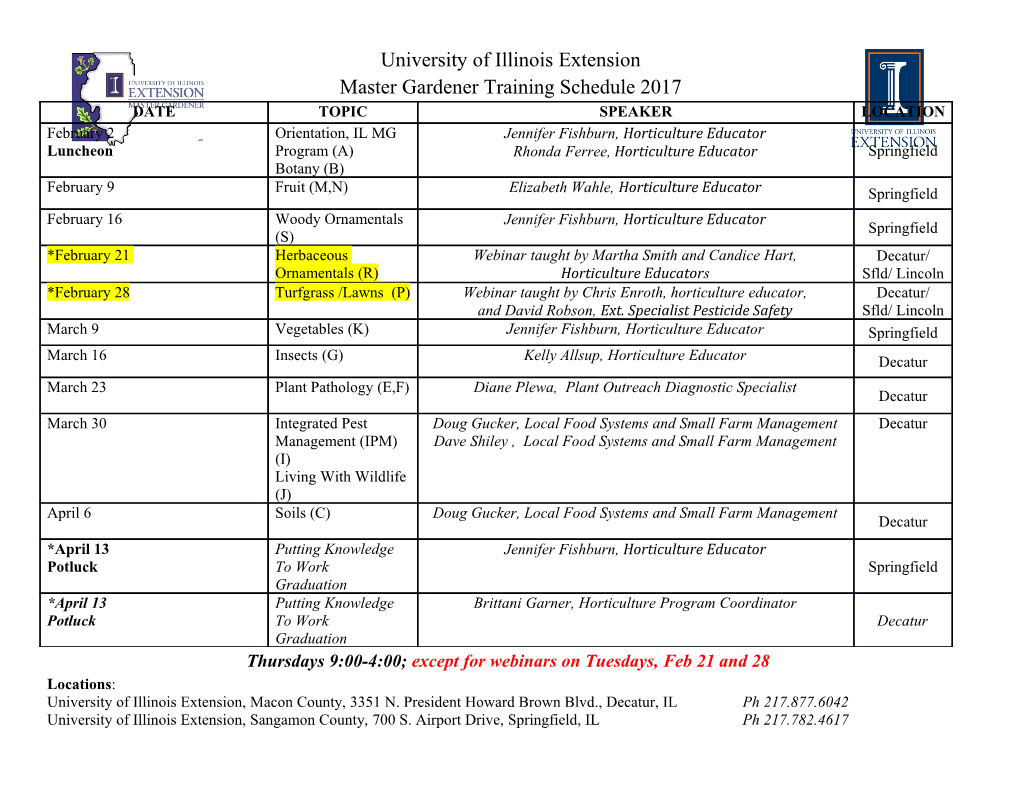
Durham E-Theses The development of an endoprosthesis for the metacarpophalangeal joint Joyce, Thomas J How to cite: Joyce, Thomas J (1997) The development of an endoprosthesis for the metacarpophalangeal joint, Durham theses, Durham University. Available at Durham E-Theses Online: http://etheses.dur.ac.uk/4731/ Use policy The full-text may be used and/or reproduced, and given to third parties in any format or medium, without prior permission or charge, for personal research or study, educational, or not-for-prot purposes provided that: • a full bibliographic reference is made to the original source • a link is made to the metadata record in Durham E-Theses • the full-text is not changed in any way The full-text must not be sold in any format or medium without the formal permission of the copyright holders. Please consult the full Durham E-Theses policy for further details. Academic Support Oce, Durham University, University Oce, Old Elvet, Durham DH1 3HP e-mail: [email protected] Tel: +44 0191 334 6107 http://etheses.dur.ac.uk THE DEVELOPMENT OF AN ENDOPROSTHESIS FOR THE METACARPOPHALANGEAL JOINT By Thomas J Joyce BEng MSc Thesis submitted for the degree of Doctor of Philosophy at the University of Durham The copyright of this thesis rests witli the author. No quotation from it should be published without the written consent of the audior and information derived from it should be acknowledged. School of Engineering University of Durham South Road Durham DHl 3LE August 1997 2 1 MAY m ABSTRACT The Development of an Endoprosthesis for the Metacarpophalangeal Joint Thomas Jonathan Joyce Doctor of Philosophy 1997 Rheumatoid arthritis is a painful and debilitating disease which often afflicts the key joint of the hand, the metacarpophalangeal joint. In the worst cases the diseased joint has to be replaced with an artificial joint or prosthesis. The development of the Durham metacarpophalangeal prosthesis as it was taken fi-om prototypes through to production samples, is described in this thesis. Testing of several Durham prostheses to over 70 million cycles has been carried out on a finger fijnction simulator and consistent wear factors of the order of 0.4 x 10" ^mm^/Nm have been measured. These wear factors for the prosthesis were also sigruficantly lower than any found previously. Production samples of the prosthesis have been manufactured together with appropriate surgical instrumentation. Tests of the prosthesis material, cross-linked polyethylene, rubbing against itself, have been undertaken on reciprocating pin on plate rigs and again show total wear factors of the order of 0.4 x lO'^mm^/Nm. Interestingly, it was found that pin wear was very much less than plate wear. The pin on plate tests were extended to include ultra-high molecular weight polyethylene (UHMWPE) rubbing against UHMWPE, as well as both polyethylenes against hard counterfaces and the results are reported. A new finger fijnction simulator has been designed, manufactured and a validation test undertaken. Having written the necessary protocol, in conjunction with clinicians and the prosthesis manufacturer, ethical approval was obtained from the local research ethics committee and the Medical Devices Agency, to permit implantation of the prosthesis in human subjects. Lastly a hand strength measurement device for pre and post operation assessment of patients has been developed and manufactured. DECLARATION The work presented in this thesis was carried out in the School of Engineering at the University of Durham. This material has not been submitted previously for any degree in this or any other university. No claim of originality is made for chapter 1, but the remaining chapters are claimed as original, except where authors have been specifically acknowledged in the text. Material from Chapters 3 and 4 has been published in the Journal of Engineering in Medicine, part H of the Proceedings of the Institution of Mechanical Engineers. The copyright of this thesis rests with the author. No quotation from it should be published without his prior written consent and information derived from it should be acknowledged. 11 ACKNOWLEDGEMENTS I would like to thank the technical staff of the School of Engineering, specifically the staff of the mechanical, electronic and electrical workshops. Brian Blackburn, Harry Kelly, Roger Little, Michael Wilson and Ian Garrett have all, at times, provided much assistance. In particular, the craftsmanship of Mr George Tumbull is appreciated. George was responsible for the manufacture of the mechanical components used in the simulator described in Chapter 5. Also thanks are due to Ms Julie Morgan who supplied many of the photographs included in this thesis. De Puy International Limited supplied the test prostheses and the bulk of the test material. None of my work would have been possible without the support of Action Research (Grant Ref A/F/0475) and I thank the charity for this fellowship, and its belief in me. Finally, thanks are due to my family; my supervisor, Professor Tony Unsworth; and especially my partner Ms Pauline McCormack. Their contribution, advice and comments have helped my work greatly. This thesis is dedicated to my dearest friend, Ben Brown, killed by a drunk driver 30th July 1997. Ben's two sons are too young to remember him, but I'll never forget him. Ill CONTENTS Pages Abstract i Declaration " Acknowledgements Contents iv-ix List of Figures x-xiv List of Tables xv-xviii Notation xix Chapter 1 Introduction and Literature Review 1-43 1.1 Introduction 1-2 1.2 Anatomy and Physiology of the Hand 3-8 1.2.1 Osteology 3-4 1.2.2 Synovial joints 4-5 1.2.3 Skeletal muscle tissue 5-7 1.2.4 Metacarpophalangeal (MCP) joint anatomy 7-8 1.3 Rheumatism and Arthritis 8-11 1.3.1 Significance 8 1.3.2 Rheumatoid arthritis 8-11 1.3.3 Osteoarthritis 11 1.4 Biomechanics 12-23 1.4.1 Introduction 12 1.4.2 Forces across the MCP joint 12-20 1.4.3 Models of MCP joint forces 20-22 1.4.4 MCP joint range of motion 23 1.5 Biomaterials 23-27 1.5.1 Introduction 23-24 1.5.2 Metals 24-25 1.5.3 Polymers 25-26 1.5.4 Ceramics 26 1.5.5 Other materials 26 1.5.6 Cross-linked polyethylene 26-27 1.6 Metacarpophalangeal Prostheses 27-36 IV 4.5.2 Comparison of XLPE against XLPE wear results 100-1 with those of other workers 4.5.3 XLPE mean plate roughness values 101-4 4.5.4 Conclusions regarding XLPE against XLPE pin 104-5 on plate wear results 4.5.5 Comparison of XLPE against XLPE pin on plate wear 105 test results with those involving standard biomaterials 4.6 UHMWPE Against UHMWPE Pin on Plate Tests 106-15 4.6.1 Wear of UHMWPE pins and UHMWPE plates 106 4.6.2 Discussion ofUHMWPE against UHMWPE wear results 106-8 4.6.3 Comparison ofUHMWPE against UHMWPE wear test 109-10 results with those of other workers 4.6.4 UHMWPE test samples: changes in visual appearance 110-11 of wear faces 4.6.5 Comparison of XLPE against XLPE with UHMWPE 112-5 against UHMWPE results 4.7 XLPE and UHMWPE Pin on Plate Tests Against Hard 116-7 Counterfaces 4.8 XLPE and UHMWPE Against Stainless Steel Plates 117-28 Pin on Plate Tests 4.8.1 Pin wear factors and test conditions 117-9 4.8.2 Changes in test pin topography 119-21 4.8.3 Changes in plate topography 121-4 4.8.4 Discussion of stainless steel results 124-7 4.8.5 Comparison of stainless steel results with those 127-8 of other workers 4.9 Zirconia Results 128-46 4.9.1 Development of tests 128-9 4.9.2 Pin wear factors and test conditions 129-31 4.9.3 Changes in test pin topography 131-2 4.9.4 Changes in plate topography 133-5 4.9.5 Zirconia plate weight changes 135-6 4.9.6 Discussion of zirconia results 136-40 4.9.7 Comparison of zirconia results with those of 140-1 other workers 4.9.8 Comparison of zirconia and stainless steel results 142-5 4.9.9 Future tests 145-6 4.10 Test of Polyethylene Plates Rubbing Against 146-50 Vll Stainless Steel Pins 4.10.1 Aim 146 4.10.2 Pin wear factors and test conditions 146-7 4.10.3 Visual changes 147-8 4.10.4 Pin weight changes 148 4.10.5 Discussion of results 148-9 4.10.6 Comparison with other researchers 150 4.11 Comparison of Finger Function (XLPE prostheses) Simulator 150-3 and Pin on Plate (XLPE against XLPE) Results Chapter 5 New Finger Function Simulator Design 154-71 5.1 Introduction 154 5.2 Assessment of Stokoe Finger Function Simulator 154-5 5.2.1 Positive aspects 154 5.2.2 Faults 154-5 5.3 Summary of Improvements in New Finger Function Simulator 155-7 5.3.1 Load actuation 155-6 5.3.2 Location of components 156 5.3.3 Electronic components 156 5.3.4 Design of individual mechanical components 15 7 5.4 Description of New Finger Function Simulator 157-64 5.4.1 Introduction 157 5.4.2 Bath 157-60 5.4.3 Drive and pinch mechanisms 160-2 5.4.4 Control and measurement 162-3 5.4.5 Control sequence and description of a load cycle 163-4 5.5 Calibration 164-5 5.6 Operation 165 5.7 New Finger Function Simulator Validation Test 166-9 5.7.1 Aim 166 5.7.2 Test procedure 167 5.7.3 Discussion of results 167-9 5.8 Modifications Made and Future Work 170-1 5.8.1 Mechanical modifications 170 5.8.2 Modifications to the pneumatic system 170 5.8.3 Possible fiiture improvements 170-1 Vlll 5.8.4 Future tests 171 Chapter 6 Towards Implantation 172-81 6.1 Summary 172 6.2 Protocol for Ethical Approval 172- 3 6.3 Surgical Instruments 173- 4 6.4 Assessment of Hand Strength 175-81 6.4.1 Overview 175- 6 6.4.2 Grip strength measurement device 176- 81 Chapter 7 Summary and Further Work 182-4 7.1 Summary 182- 3 7.2 Further Work 183- 4 References 185-94 Appendices 1 The Durham Metacarpophalangeal Prosthesis: 195-96 Production
Details
-
File Typepdf
-
Upload Time-
-
Content LanguagesEnglish
-
Upload UserAnonymous/Not logged-in
-
File Pages355 Page
-
File Size-