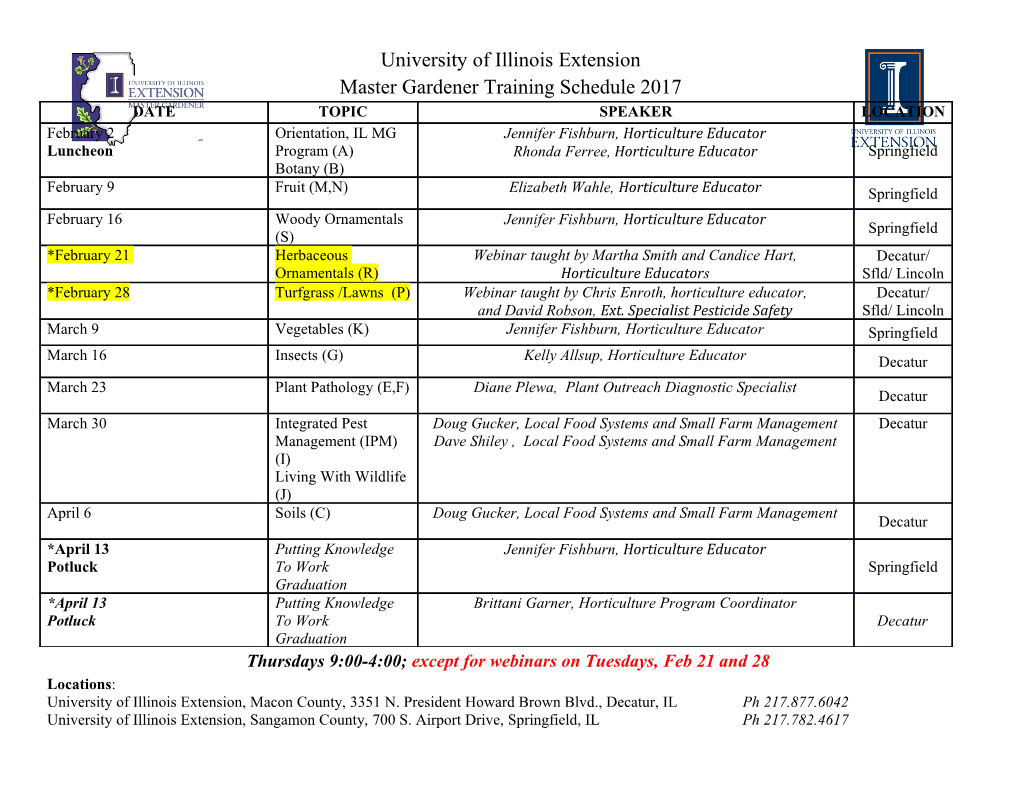
Motion of Complex Kinematic Robotic Structures Example: Complex Kinematic Chain • Tree structure • Closed kinematic loops So far in this course: only serial robotic structures 2 Sensor Based Robotic Manipulation and Locomotion Tree Structures Desired values can be assigned for all joints independently. qA1 qA1 q qF1 ^ qF 4 M (q)q C(q,q)q g(q) Kinematics and dynamics can be computed in principle identically as for serial manipulators (for example using Euler-Lagrange or Newton-Euler formalism for the dynamics). 3 Sensor Based Robotic Manipulation and Locomotion Closed Kinematic Loops The loop introduces mathematical constraints O between the joints. Passive joints are necessary in order to minimize the constraint forces which would appear if all joints were active due ^ to positioning inaccuracies. qa active joints q q p passive joints Assumptions: • Point contact • The contact point between finger and object does not change. Under the given assumptions, the contact can be modelled as a virtual passive joint. 4 Sensor Based Robotic Manipulation and Locomotion Forward Kinematics for Closed Loops TCP1 A3 TCP TCP´2 A (attached to ) A A2 3 A2 3 A2 A3 TCP1 TCP2 active A active A4 A1 4 A1 O passive qa O passive q q usually, only the position of active p joints is measured by encoders General procedure: • Breaking the link at a certain joint (typically the output) => a tree structure results • Computation of the geometric model for the tree structure OT (q ,q ), OT (q ,q ) O O TCP1 a p TCP2 a p T (q ,q ) T (q ,q ) TCP1 a p TCP2 a p • From the loop condition (constraint) the passive joints q p are expressed. or • The TCP is expressed by substituting q p TCP1(qa ,qp (qa )) TCP2(qa ,q p (qa )) Remark: inverse kinematics (given TCP, find q) is computed in the known manner for both serial manipulators resulted by breaking the loop. It is generally much easier than direct kinematics, since 5the two manipulators have simple structures. Sensor Based Robotic Manipulation and Locomotion Example: Four Bar Linkage qa TCP1 q q q2 3 l A3 TCP q p 2 ´2 A TCP A2 3 l1 active active q q4 A4 1 A1 passive passive 3 4 1 2 Generally: T4 T1 T2 T3' I Three constraint equations result: 3 corresponding to two translations (q) 0, R and one rotation in the plane In the simple case of the parallelogram, the solution can be written directly : q4 q1 q q 4 joints =>The robot has 1 DoF at the TCP 2 1 3 constraints q3 q1 => it follows that only one joint can be actively positioned. 6 Sensor Based Robotic Manipulation and Locomotion Number of DOF in a Loop For a serial robot: q R n N links, n 1dof joints (q) 0, R r constraints for n joints, r constraints => n-r degrees of freedom at TCP For an arbitrary closed structure with N links, n joints, k DOF/joint: • Planar case: 3 DOF/Link, 3-k constraints/joint n DoF 3(N n) ki i1 • Spatial case: 6 DOF/Link, 6-k constraints/joint n (known as Grübler formula) DoF 6(N n) ki i1 Example at the whiteboard is valid only for independent constraints 7 Sensor Based Robotic Manipulation and Locomotion Differential Kinematic Model How do I compute the Jacobian? qa q q p v3 A3 By equating the Cartesian velocities at the l2 v3 A separated joint one obtains the differential A2 3 v3 v3 constraints: l1 q1 q3 "velocity v3 v3 J3(q1,q2) J3(q3,q4) active A4 constraints" q2 q4 A1 passive q1 q2 Together: J3(q1,q2), J3(q3,q4) 0 q3 J c0 (q1 ,q2 ,q3 ,q4 ) q4 By introducing the constraints: Jc (q1)q 0 differential constraints 8 Sensor Based Robotic Manipulation and Locomotion Differential Kinematic Model One can obtain the equations also by differentiating the constraints: (q ,q ) 0 a p Jc (qa )q 0 (qa,qp ) (qa,qp ) qa , 0 differential constraints q qa q p p J c0 q Or: a Jca (qa ), Jcp (qa ) 0 q p since J cp ( q a ) is quadratic (number of constraints = number of passive joints) 1 q p Jcp (qa )Jca (qa )qa (if J cp ( q a ) is not singular) The Cartesian velocity of the open kinematic structure can now be computed in al classical way. q1 e.g., for the four bar linkage: v J , J J J q 3 31 32 31 32 1 q1 9 Sensor Based Robotic Manipulation and Locomotion Dynamics of Closed Kinematic Structures First, the dynamics of the opened chain (tree structure) 3 is computed with following additional assumptions: • All joints are actuated. A3 3 A2 A3 • The torques are chosen such that the robot performs the same motions q , q , q as for the closed loop. A4 A1 Ba B M (q)q C(q,q)q g(q) B Bp a In reality, we have and the closed chain is held together by 0 at the virtual separation point the constraint force . The forces are dual to the constraint T velocities v at the separation point: (q) (q) v q q q Since the real and the virtually separated robot must move identically, it follows: B (q,q,q) B (q,q,q) 10 Sensor Based Robotic Manipulation and Locomotion Dynamics of Closed Kinematic Structures Remark: In der classical mechanics one obtains this relation through the constrained Euler-Lagrange equation: T d dL(q,q) dL(q,q) (q) mit L(q,q) T (q,q) U (q) dt dq dq q B (q,q,q) T a Ba Jca 0 T Bp Jcp from the second equation: T Jcp Bp T T a Ba JcaJcp Bp T T T T or simply a J B B with JB I, JcaJcp The dynamics of the closed loop can be computed from the dynamics of the tree structure and from the constraint conditions. 11 Sensor Based Robotic Manipulation and Locomotion Dexterous Hands Grasp Types Precision grasp Pinch grasp Power grasp 13 Sensor Based Robotic Manipulation and Locomotion Opposing Thumb 14 Sensor Based Robotic Manipulation and Locomotion The Complete Finger System 15 Sensor Based Robotic Manipulation and Locomotion Stiffness Control 16 Sensor Based Robotic Manipulation and Locomotion Kinematics of Dexterous Hands Grasp planning: selection of a grasp, which should be able to: • Withstand forces acting on the object in arbitrary directions - Force closure grasp • Move the object in arbitrary directions: - Manipulable grasp In the following, precision grasps are treated Assumptions: • Contact point on the object is known (or can be measured). • Contact point does not change during motion. • Object and fingers are rigid bodies • Exact geometric model of the object and the hand are available 17 Sensor Based Robotic Manipulation and Locomotion Contact Models • Point contact without friction: 0 0 zi z Fci O i1 1 Ci Ci1 F f f R ci 0 ci, ci normal 0 only force in normal direction 0 • Point contact with Coulomb friction: 1 0 0 0 1 0 0 0 1 Fci fci, fci FCci friction cone 0 0 0 0 0 0 0 0 0 3 2 2 FCci f R : f3 R , f1 f2 f3 friction coefficient 18 Sensor Based Robotic Manipulation and Locomotion Contact Models Soft finger model: 1 0 0 0 0 1 0 0 zi zi1 0 0 1 0 C F O Fci fci, fci FCci i ci Ci1 0 0 0 0 0 0 0 0 normal 0 0 0 1 4 2 2 FCci f R : f3 R , f1 f2 f3 , f4 f3 friction coefficient friction coefficient translation rotation The contact can transfer also rotations around the z-axis generally: Fci Bci fci, fci FCci selection matrix friction cone (wrench basis) 19 Sensor Based Robotic Manipulation and Locomotion Grasp Matrix Contribution of contact force Fci at the coordinate system O: o f R 0 pˆoci o ci z F B f i zi1 oi o o ci ci C Fci O C mo pˆoci Rci Rci i f m i1 o o Gi Normal Ad T B f G f ocici ci i ci Gci The total wrench in object coordinates is Ad is called the f oci k 1 adjoint matrix Fo Gi fci G1,,Gk Gfc i1 G fk f c or simply: Fo Gfc, fc FC grasp matrix 20 Sensor Based Robotic Manipulation and Locomotion Example: Point Contact without Friction 0 0 R o 0 1 F ci f , f o oi o o ci ci R Rci xi , yi , zi pˆ oci Rci Rci 0 0 0 By performing the multiplication one obtains: normal z F i f oi pˆ z ci oci i lever arm poci zi The grasp matrix results as: f1 z1 zk Fo Gfc pˆoc1z1 pˆock zk fk G 21 Sensor Based Robotic Manipulation and Locomotion Force Closure Grasp A grasp is force closure if it can resist any externally applied wrenchFe Gfc Fe, fc FC Definition: A grasp force f N f c is called internal force if it generates no net object force GfN 0, fN FC z 1 f z2 C c1 O fc2 Example: 1 C2 Theorem (without proof – Murray & al.): A grasp is force closure if and only if G is surjective and if the grasp admits internal forces 22 Sensor Based Robotic Manipulation and Locomotion Evaluation of Force Closure Grasps Generally a difficult problem, depending on the friction cone. (Schlegel, Buss & al.) For point contact without friction, simple solution: f1 z1 zk F Gf , f R o c ci pˆ oc1z1 pˆ ock zk fk G Theorem ( Murray & al.): Assume point contacts without friction.
Details
-
File Typepdf
-
Upload Time-
-
Content LanguagesEnglish
-
Upload UserAnonymous/Not logged-in
-
File Pages39 Page
-
File Size-