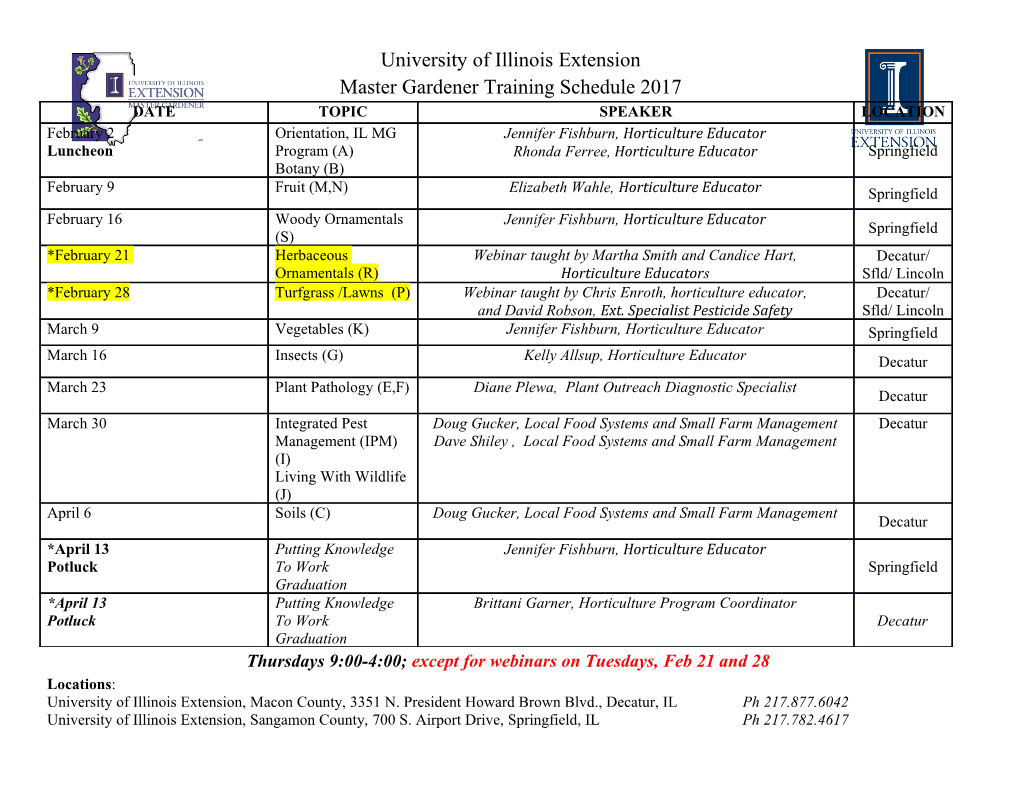
MODE I INTERLAMINAR FRACTURE PROPERTIES OF OXIDE AND NON- OXIDE CERAMIC MATRIX COMPOSITES A Dissertation Presented to The Graduate Faculty of The University of Akron In Partial Fulfillment of the Requirements for the Degree Doctor of Philosophy Rabih Mansour May, 2017 MODE I INTERLAMINAR FRACTURE PROPERTIES OF OXIDE AND NON- OXIDE CERAMIC MATRIX COMPOSITES Rabih Mansour Dissertation Approved: Accepted: Advisor Department Chair Dr. Gregory Morscher Dr. Sergio Felicelli Committee Member Interim Dean of the College Dr. Minel Braun Dr. Donald Visco Committee Member Dean of the Graduate School Dr. Kwek Tze Tan Dr. Chand Midha Committee Member Date Dr. Gary Doll Committee Member Dr. Alper Buldum ii ABSTRACT This work provides a novel method for determining interlaminar fracture properties at both room and elevated temperature, offering the first glimpse of the interlaminar fracture behavior of CMCs at elevated temperatures. Interlaminar fracture properties play an important role in predicting failure of structural components for CMC materials. Elevated temperatures induce more severe conditions for interlaminar properties resulting in a weaker interlaminar toughness. The main challenges associated with determining interlaminar fracture toughness are the ability to measure crack growth without visual observation and to develop an experimental setup that can be used at both room and high temperature. Hence, a non- visual crack monitoring technique has been successfully introduced to estimate crack length in CMCs using electrical resistance. In a parallel effort, a wedge-loaded double cantilever beam method has been developed to determine the interlaminar fracture properties of CMCs at room and elevated temperatures. It has been found that the wedge method does not depend on the wedge material, as long as the correct coefficient of friction is taken into consideration. Additionally, the wedge method was found to be comparable to the traditional double cantilever beam method. The interlaminar fracture properties depend immensely on the composite microstructure and the weave architecture; the interlaminar crack propagates along the longitudinal fiber tows, passing through the porosities, which serve as stress iii concentration points. Moreover, depending on the fiber tows orientation along the crack propagation path, a rising or flat R-curve behavior can be seen for the same composite system. High temperature testing revealed that the energy required to initiate a crack at room temperature is greater than that at 815 °C. However, more energy is required to propagate the interlaminar crack at high temperature for some CMC systems (such as PIP SiC/SiNC). This behavior was attributed to softening of the matrix, which was evident when comparing crack growth rate at elevated temperature to room temperature. The data presented provides the first glimpse of the interlaminar fracture properties of CMCs at elevated temperatures. The wedge method was also verified using finite element analysis and micromechanics approaches. However, in order for a model to accurately predict the interlaminar behavior of the material and assist in optimizing specimen’s geometry, the mechanical response of the studied composite should be well-known, especially shear properties. Finally, a method for determining the out-of-plane electrical resistivity for composite materials has been proposed, while introducing the concept of length constant as a composite property. This method was utilized and successfully verified for two ceramic matrix composite systems with significantly different electrical properties. The out-of-plane electrical resistivity was found to be 8-9 times greater than the in-plane electrical resistivity. iv ACKNOWLEDGEMENTS First and foremost, I would like to express my sincere gratitude to my advisor Dr. Gregory Morscher for his guidance, support and above all friendship. He is an inspiration to both my professional and personal life, and I am forever grateful to have had him as an advisor and a mentor. I would like to thank the Naval Air Systems Command (NAVAIR), specifically Dr. Sung Choi, for financially supporting this project under STTR N13A-T008. My appreciation is also extended to Dr. Frank Abdi for supporting this project and for the time I spent at AlphaSTAR Corporation. I also would like to thank my committee members for their valuable comments and suggestions. Dr. Minel Braun has been a mentor and a friend throughout graduate school, and for that I am extremely grateful. A most special acknowledgement is made to my family and friends for the support that they have always provided me with. I also would like to express my appreciation for the enjoyable collaboration with my colleagues in my research group and the help I received from them. v TABLE OF CONTENTS Page LIST OF TABLES ...............................................................................................................x LIST OF FIGURES ........................................................................................................... xi CHAPTER I. INTRODUCTION ............................................................................................................1 II. MOTIVATION, HYPOTHESIS AND SCOPE OF WORK ..........................................4 III. LITERATURE REVIEW ..............................................................................................7 3.1 Processing of CMCs ................................................................................................7 3.1.1 Processing of Non-Oxide CMCs ..................................................................7 3.1.2 Processing of Oxide CMCs ........................................................................10 3.2 Damage Classification in CMCs ............................................................................11 3.2.1 Interlaminar Fracture Toughness in Composites ........................................12 3.3 Damage Monitoring and Non-Destructive Evaluation of CMCs ..........................21 3.3.1 Acoustic Emission ......................................................................................21 3.3.2 Electrical Resistance ...................................................................................29 3.3.3 Digital Image Correlation ...........................................................................32 3.3.4 Micro-Computed Tomography ...................................................................33 3.4 Micromechanical Modeling of Composites ...........................................................35 IV. DESIGN OF THE EXPERIMENT .............................................................................41 4.1 Introduction ............................................................................................................41 4.2 Materials ................................................................................................................44 vi 4.3 Mechanical Testing ............................................................................................... 47 4.4 Electrical Resistance ............................................................................................. 48 4.5 Acoustic Emission ................................................................................................ 49 4.6 Optical Microscopy, Digital Image Correlation (DIC), and Micro-CT ................ 50 4.7 Results and Discussion ......................................................................................... 51 4.7.1 Selection of the wedge material ................................................................ 51 4.7.2 Implementation of electrical resistance to monitor crack growth ............. 52 4.7.3 Implementation of acoustic emission to monitor damage accumulation .. 71 4.7.4 Mechanical Behavior ................................................................................. 79 4.8 Conclusions ........................................................................................................... 93 V. THE EFFECT OF FRICTION AND WEDGE ANGLE ON THE WEDGE-LOADED DOUBLE CANTILEVER BEAM METHOD ........................................................................ 95 5.1 Introduction ................................................................................................................ 95 5.2 Experimental Procedure ............................................................................................. 95 5.2.1 Material and Mechanical Testing ................................................................... 95 5.2.2 Friction Measurement ..................................................................................... 97 5.3 Analytical Analysis .................................................................................................... 97 5.4 Results and Discussion ............................................................................................. 101 5.4.1 Friction Study ............................................................................................... 101 5.4.2 Mechanical Data ........................................................................................... 104 5.5 Conclusions .............................................................................................................. 106 VI. COMPARISON BETWEEN THE WEDGE-LOADED DOUBLE CANTILEVER BEAM AND THE TRADITIONAL DOUBLE CANTILEVER BEAM ............................ 107 6.1 Introduction .............................................................................................................
Details
-
File Typepdf
-
Upload Time-
-
Content LanguagesEnglish
-
Upload UserAnonymous/Not logged-in
-
File Pages216 Page
-
File Size-