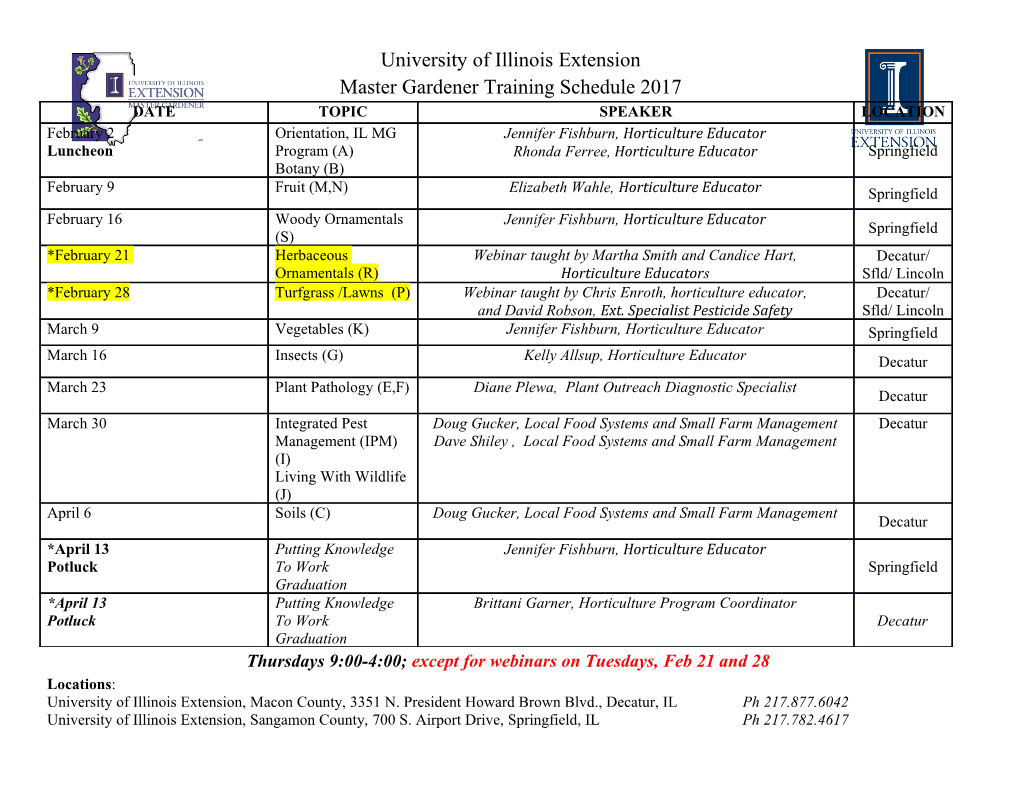
Global ice ridge ramming loads based on full scale data and specific energy ap- proach Job Kramers echnische Universiteit Delft T GLOBAL ICE RIDGE RAMMING LOADS BASED ON FULL SCALE DATA AND SPECIFIC ENERGY APPROACH by Job Kramers in partial fulfillment of the requirements for the degree of Master of Science in Offshore and Dredging Engineering at the Delft University of Technology, to be defended publicly on November 25th, 2016 at 14:30. Sponsor: Sustainable Arctic Marine and Coastal Technology (SAMCoT) Research Centre Student number: 4011120 Date: ?, 2016 Supervisor: Prof. S. Løset NTNU Prof. dr. ir. A. V. Metrikine TU Delft M. A. van den Berg TU Delft Thesis committee: Prof. dr. ir. A. Metrikine TU Delf Prof. S. Løset NTNU An electronic version of this thesis is available at http://repository.tudelft.nl/. ABSTRACT This thesis analyses the loads that occurred during an ice ridge ramming experiment with the icebreaker Oden. Sea ice ridges are formed due to breaking and deformation of the ice cover. Wind, current, thermal expansion and Coriolis forces induce compression and shear forces onto level ice which can break the ice into rubble. The blocks of ice rubble are pushed together, forming a wall of broken ice in hydrostatic equilib- rium. This wall of broken ice forced up by pressure is defined as an ice ridge. In general ice ridges are long, nonsymmetrical, curvilinear features with a wide variability of sizes and shapes. In Arctic regions, sea ice ridges are often used to calculate the design load in the absence of icebergs. Ice ridges also play a major role in icebreaker efficiency, since an icebreaker might need several ‘rams’ to break through an ice ridge. Ice ridge actions on icebreakers are not completely understood. Complex ice behavior under rapidly applied stress, and the complex geometries of the bodies in contact makes it a challenging re- search topic. The dynamic behavior of the vessel during the ramming can be used to make an estimate of the ice loads that occurred. This thesis analyses the ice load that occurred during a ridge ramming experiment that was performed with icebreaker Oden during the ODEN AT research cruise project in 2013. To advance our understanding in the global ice ridge ramming loads, two models were developed: 1) a simulation model using the Specific Energy Absorption (SEA) of mechanical crushing of ice to calculate the global ice loads, 2) a load identification model using full-scale data to determine the global ice loads. The simulation model was developed to enhance the understanding of relevant physical phenomena and parameters. During this process, specific energy principles of crushing of ice were identified as a promising although relatively unknown method for impact dynamics into ice. The Specific Energy Absorption (SEA) of mechanical crushing of ice is defined as the energy per unit mass of crushed ice, necessary to turn solid ice into crushed (pulverized) material. Besides the SEA value, the penetration velocity, density of ice, and volume of crushed ice, are required to calculate the ice load. A contact model was developed to determine the load location and direction on the hull. The icebreaker Oden is represented by a nonlinear mass-damper-spring system. Maneuvering theory is ap- plied, which means that the hydrodynamic variables are estimated at one frequency of oscillation. In the simulation model, a known thrust force is applied on the vessel, making it move forward in open water, and then penetrate the ice ridge. The simulation model calculates the ice loads and vessel’s motions (i.e. accel- erations, velocity, and displacement). The load identification model combines the Kalman filter and a joint input-state estimate algorithm to estimate the state- and excitation vector from acceleration, velocity and displacement data in 3DOF (i.e. surge, heave, pitch). The joint input-state estimate algorithm combines measured data with an estimate of the state of the system in a way that minimizes the error. The full-scale data analyzed in this thesis includes a profile of a multi-year ice ridge, vessel characteristics, acceleration data from a motion reference unit (MRU), GPS data, and propulsion data. From the results of the load identification model, we conclude that the current combination of model and data does not provide sufficient information to estimate the global ridge ramming loads with high reliabil- ity. The main reasons for this are the absence of additional MRU(s), the low sample frequency of the MRU, the data uncertainty, and the simplified hydromechanics. However, the suggested approach to calculate the global ice loads is reliable as long as the data is valid. This is verified by recalculating the ice loads from the data (i.e. motions), generated by the simulation model. Results indicate that the specific energy approach can be used to simulate an impact of a vessel into an ice ridge, under assumption that the ice fails purely due to crushing. This assumption is only valid during the beginning of the impact, as other failure modes often start to dominate as the penetration of the vessel into the ridge increases. Cover picture: https://upload.wikimedia.org/wikipedia/commons/f/f8/Antarctica_--_Oden_the_ Icebreaker_-m.jpg iii ACKNOWLEDGMENT I would like to express my gratitude to professor A.V.Metrikine and my supervisors M.A. van den Berg at Delft University of Technology, and professor S. Løset of Norwegian University of Science and Technology. I would like to give a special thanks to Hongtao Li, Thorvald Grindstad, and Ekaterina Kim for their help and guidance during my research. Then I would like to take the opportunity to thank my friends and colleagues at NTNU and Fjordgata 7, who made my stay in Trondheim so much fun. Finally, I could not have done this without the encouragement and support of my family and friends. Job Kramers, Delft 20 October, 2016 iv ABBREVIATIONS BFS Bottom Founded Structures CEP Circular error probability CM Contact Model CP Contact Point CPP Controllable Pitch Propeller CFD Computational Fluid Dynamics COB Centre of Buoyancy COG Centre of Gravity COR Centre of Rotation COS Centre of Shape DOF Degree of Freedom DWT Deadweight tonnage FPP Fixed Pitch Propeller FS Floating Structures GNSS Global navigation satellite system GLONASS Global navigation satellite system GPS Global positioning system HMI Human Machine Interface IMU Inertial Measurement Unit LOA Length Over All LWL waterline length MRU Motion Reference Unit RMS Root mean square IACS International Association of Classification Societies SEA Specific Energy Absorption v SYMBOLS a acceleration [m/s2] aii added mass i=1,2,3,4,5,6 see below a11 added mass surge [kg] a22 added mass sway [kg] a33 added mass heave [kg] a added mass roll [kg m2] 44 ¢ a added mass pitch [kg m2] 55 ¢ a added mass yaw [kg m2] 66 ¢ Ac system matrix 2 A j,i wake area normal to flow at location i [m ] 2 AN nominal contact area [m ] 2 Aw wetted surface [m ] 2 Awp contact area below water plane [m ] b hydrodynamic damping i=1,2,3 [N s/m] ii ¢ b nonlinear surge damping [N s2/m2] 11,NL ¢ b nonlinear heave damping [N s2/m2] 33,NL ¢ B beam [m] Ba,f aft,front beam [m] Bc system matrix 2 B j,i hull area at location i [m ] C damping matrix C f friction coefficient [-] C f p flat plate friction coefficient [-] C f r residual friction coefficient [-] Cow open water friction coefficient [-] Ct thrust coefficient [-] Cw wake fraction [-] d displacement [m] 2 d Abow,btm change of indentation (bow, bottom) [m/s ] d(t) measurement data vector D diameter [m] Dr draft [m] f (t) excitation vector [N] F force [N] Fx1,ice horizontal global ice load [N] Fx3,ice vertical global ice load [N] Fb buoyancy force [N] FH horizontal load [N] FN normal load [N] FV vertical load [N] g gravitational acceleration [m/s2] Gc influence matrix GM metacentric height [m] GZ righting stability arm [m] h height [m] hk keel height [m] hs sail height [m] HR ridge height [m] vi SYMBOLS vii I second moment of inertia of water plane area [m4] I moment of inertia around y axis [kg m2] y ¢ Jc direct transmission matrix k hydrostatic spring stiffness i 1,2,3,4,5,6 [N/m2],[N m/r ad] ii Æ ¢ k nonlinear hydrostatic spring stiffness i 1,2,3,4,5,6 [N/m],[N m2/r ad 2] ii,NL Æ ¢ k35 heave-pitch coupling hydrostatic spring stiffness k53 heave-pitch coupling hydrostatic spring stiffness K stiffness matrix KQ Torque coefficient [-] L length [m] LB j,i hull length i [m] Lpp characteristic traveled length of the fluid [m] Lm middle body length [m] m mass [kg] M mass matrix M pitching moment due to ice loads [N m] x5,ice ¢ M pitching moment due to thrust force [N m] x5,T ¢ M stability moment [N m] s ¢ n numbers of revolutions [1/s] P pressure [Pa] p(t) force time histories pav pressure averaged over area [Pa] P error covariance matrix PD,E,in,out Power. delivered, effective, in, out [W] P/D pitch ratio [-] Pi tch® pitch angle [deg] P Px1,x3,x5(t) total excitation force in direction x1,x3,x5 Q torque [N m] ¢ Q process noise covariance matrix 3 Q j flow rate [m /2] r radius [m] R measurement noise covariance matrix R resistance [N] RB ice breaking resistance [N] RF friction resistance [N] Ri ice resistance [N] Row open water resistance [N] RR ridge resistance [N] RS ice submerging resistance [N] Rn Reynolds number [-] S sensitivity [%] Sa,v,d,p selection matrix SEA specific energy absorption [J/kg] T thrust force [N] Tx1 horizontal component thrust force [N] Tx3 vertical component thrust force [N] v velocity [m/s] ve entrance velocity [m/s] v j mean wake velocity [m/s] vk measurement noise V volume [m3]
Details
-
File Typepdf
-
Upload Time-
-
Content LanguagesEnglish
-
Upload UserAnonymous/Not logged-in
-
File Pages244 Page
-
File Size-