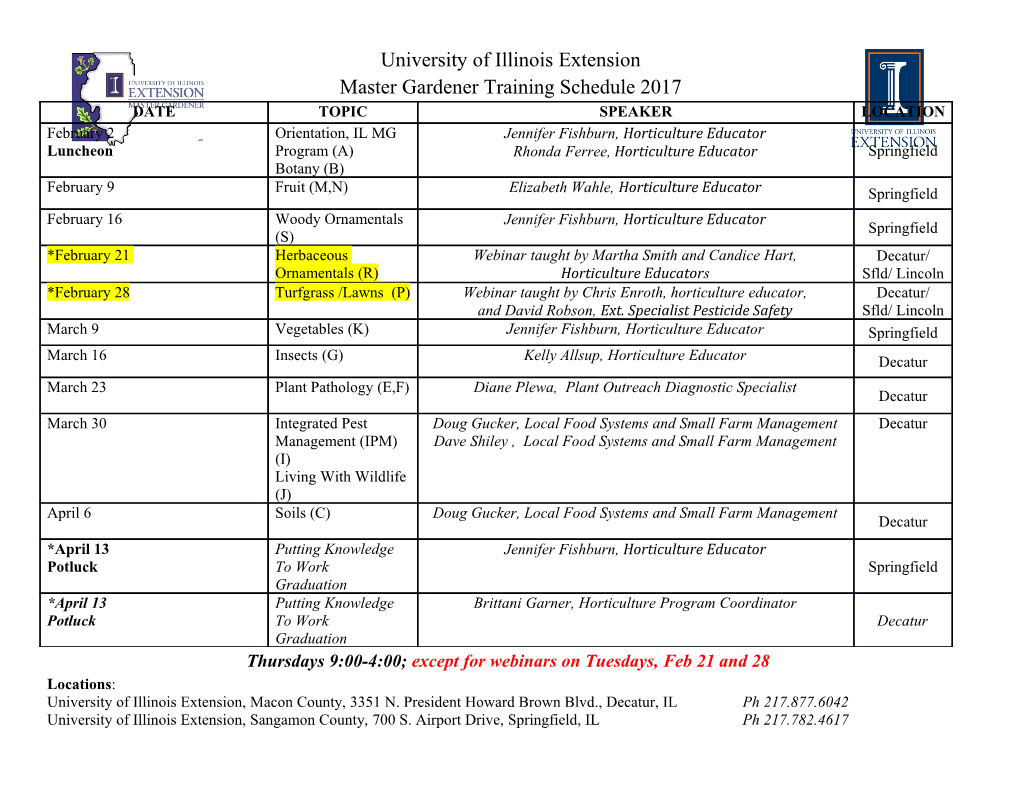
University of Colorado Department of Aerospace Engineering Sciences Senior Projects - ASEN 4018 Visual In-Situ Sensing for Inertial Orbits of NanoSats (VISION) Conceptual Design Document Monday 30th September, 2019 1. Information 1.1. Project Customers Name: Dr Penina Axelrad Email: [email protected] Phone: (303) 492-6872 1.2. Group Members Name: Max Audick Name: Cameron Baldwin Email: [email protected] Email: [email protected] Phone: 858-603-2275 Phone: 304-282-2037 Name: Adam Boylston Name: Zhuoying Chen Email: [email protected] Email: [email protected] Phone: 303-720-9755 Phone: 303-264-7129 Name: Tanner Glenn Name: Ben Hagenau Email: [email protected] Email: [email protected] Phone: 720-219-4960 Phone: 650-701-4092 Name: Adrian Perez Name: Andrew Pfefer Email: [email protected] Email: [email protected] Phone: 720-250-7538 Phone: 303-519-8777 Name: Ian Thomas Name: Bao Tran Email: [email protected] Email: [email protected] Phone: 843-670-1593 Phone: 720-288-5845 Name: Theodore Trozinski Name: Mathew van den Heever Email: [email protected] Email: [email protected] Phone: 973-349-8821 Phone: 970-402-0332 Contents 1 Information 1 1.1 Project Customers.............................................1 1.2 Group Members..............................................1 2 Project Description 4 2.1 Purpose..................................................4 2.2 Objectives / Levels of Success......................................4 2.3 Concept of Operations (CONOPS)....................................5 2.4 Functional Block Diagram (FBD)....................................6 2.5 Functional Requirements.........................................7 3 Design Requirements 7 4 Key Design Options Considered 11 4.1 Sensor Suite ............................................... 11 4.1.1 Wide Angle Visual and ToF Camera ............................... 11 4.1.2 Telephoto Visual and ToF Camera ................................ 12 4.1.3 Wide Angle Visual and ToF Camera ............................... 13 4.1.4 Stereoscopic Cameras ...................................... 13 4.1.5 Single Visual Camera ....................................... 14 4.1.6 Staggered Dual Visual ...................................... 15 4.2 Structural Interface Method ...................................... 15 4.2.1 Internal Mounting ........................................ 16 4.2.2 External Mounting ........................................ 16 4.2.3 Launch Tube Replacement .................................... 17 4.2.4 Modular Internal/External Mounting .............................. 18 4.3 Embedded Systems ........................................... 18 4.3.1 Nvidia Jetson Nano ........................................ 19 4.3.2 Intel NUC8i7HVK ........................................ 20 4.3.3 Intel NUC8i7HNK ........................................ 20 4.3.4 Intel NUC8i5BEH ........................................ 21 4.3.5 Xilinx Zynq-7000 SoC ZC702 .................................. 22 4.3.6 Xilinx Zynq Ultrascale+ MPSOC ................................ 22 4.4 Flight Software Programming Language ............................... 23 4.4.1 MATLAB ............................................. 23 4.4.2 Python .............................................. 25 4.4.3 C++ ............................................... 26 4.5 State Estimation Method ........................................ 26 4.5.1 Weighted Least Squares..................................... 27 4.5.2 Recursive Least Squares..................................... 27 4.5.3 Classical Kalman Filter...................................... 28 4.5.4 Extended Kalman Filter..................................... 28 4.5.5 H1 Filter............................................. 29 4.5.6 Dynamics Model Considerations................................. 29 5 Trade Study Process and Results 31 5.1 Sensor Suite Trade Study......................................... 32 5.1.1 Trade Study Results....................................... 33 5.2 Structural Interface Method Trade Study................................. 34 5.2.1 Metric Weight Determination.................................. 34 5.2.2 Trade Study Results....................................... 35 5.3 Embedded Systems Trade Study..................................... 35 5.3.1 Measure of Weighting...................................... 35 5.3.2 Trade Study Background..................................... 36 09/30/19 2 of 46 CDD University of Colorado Boulder 5.3.3 Trade Study Results....................................... 37 5.4 Flight Software Programming Language Trade Study.......................... 37 5.4.1 Metric and Weight Determination................................ 37 5.4.2 Trade Study Results....................................... 38 5.5 State Estimation Method......................................... 39 5.5.1 Robustness............................................ 39 5.5.2 Optimizability.......................................... 40 5.5.3 Learnability............................................ 40 5.5.4 Computational Expense..................................... 41 5.5.5 Weight Assignments....................................... 41 5.5.6 Trade Study Results....................................... 41 6 Selection of Baseline Design 42 6.1 Sensor Suite Baseline Design....................................... 42 6.2 Structural Interfacing Method Design.................................. 42 6.3 Embedded System Baseline Design................................... 42 6.4 Flight Software Programming Language................................. 42 6.5 State Estimation Baseline Design..................................... 43 6.6 Summary................................................. 43 7 Appendix 44 8 Appendix A Trade Study Theory 46 8.1 General Relative Orbit Equations of Motion............................... 46 8.2 Linearized General Relative Orbit Equations of Motion......................... 46 8.3 Hill-Clohessey-Wiltshire Equations................................... 46 8.4 Tschauner-Hempel Equations Equations................................. 46 09/30/19 3 of 46 CDD University of Colorado Boulder 2. Project Description 2.1. Purpose The motivation behind the VISION (Visual In-Situ Sensor for Inertial Orbits of NanoSats) project is to improve Space Situational Awareness (SSA) by developing a modular in-situ CubeSat tracking system. Using optical sensors, VISION observes CubeSats deployed from a variety of launch providers to estimate and deliver preliminary, inertial two-line-elements (TLE’s). With the ever-increasing number of NanoSats being launched in batches, keeping track of the numerous satellites is difficult, expensive, inefficient, and has lead to lost vehicles. [3] The current method of tracking orbiting satellites is to create a series of tracks for each satellite as they pass over ground-based surveillance systems. This can only be done when a satellite passes through the field of view (FOV) of a surveillance site. Despite the large number of these sites around the globe, this method has proved impractical for predicting and identifying orbits of small satellites deployed in groups. The available resolution of ground based systems hinders their ability to track closely-clustered objects. Multi-satellite deployments, especially of NanoSats in low earth orbit (LEO), can take 5-10 days or more to identify and track using ground based tracking stations. The vast majority of these mass-deployed satellites have no on-board propulsion or maneuvering systems, [4] and may remain in these clusters for days. A successful VISION project will supply launch providers with a preliminary tracking system to estimate the states of individual CubeSats immediately following deployment. These initial estimates will be used to augment the ground based efforts later, increasing the probability of successful identification and tracking. VISION will be the middle platform between the CubeSat customer and the verification of the success of the mission. More importantly, a successful project will reduce the number of unidentified objects in Earth’s orbit. This will ultimately improve and support the cause of space situational awareness and enable flexible tasking and rapid decision making for the avoidance of potential collisions between space objects. This year’s purpose is to advance last academic year’s VANTAGE project by incorporating the proof-of-concept into a working prototype. The system will be designed to integrate with, at a minimum, one CubeSat deployment platform where it will visually monitor up to 6 individual CubeSats after deployment. The system will undergo a ground simulation and testing to ensure project success as defined by the levels in the following sub-section. VISION’s goal is to achieve a NASA Technical Readiness Level (TRL) of 4. 2.2. Objectives / Levels of Success The following table represents the three levels of success of the VISION project. Each category has increasing levels of success by which the team intends to measure the end results of the project. Structures/Mechanical Level 1 • Mission-ready chassis that meets material requirements, verified by tests. • Chassis can interface with one deployer. • All components fit within volumetric and mass constraints of chassis/mechanical structure. Level 2 • Chassis interfaces with multiple launch deployers. • Component Testing in Relevant Environment (Launch and mission environment component testing, TRL-5). Level 3 • System Testing in Relevant Environment (Launch and mission environment system
Details
-
File Typepdf
-
Upload Time-
-
Content LanguagesEnglish
-
Upload UserAnonymous/Not logged-in
-
File Pages46 Page
-
File Size-