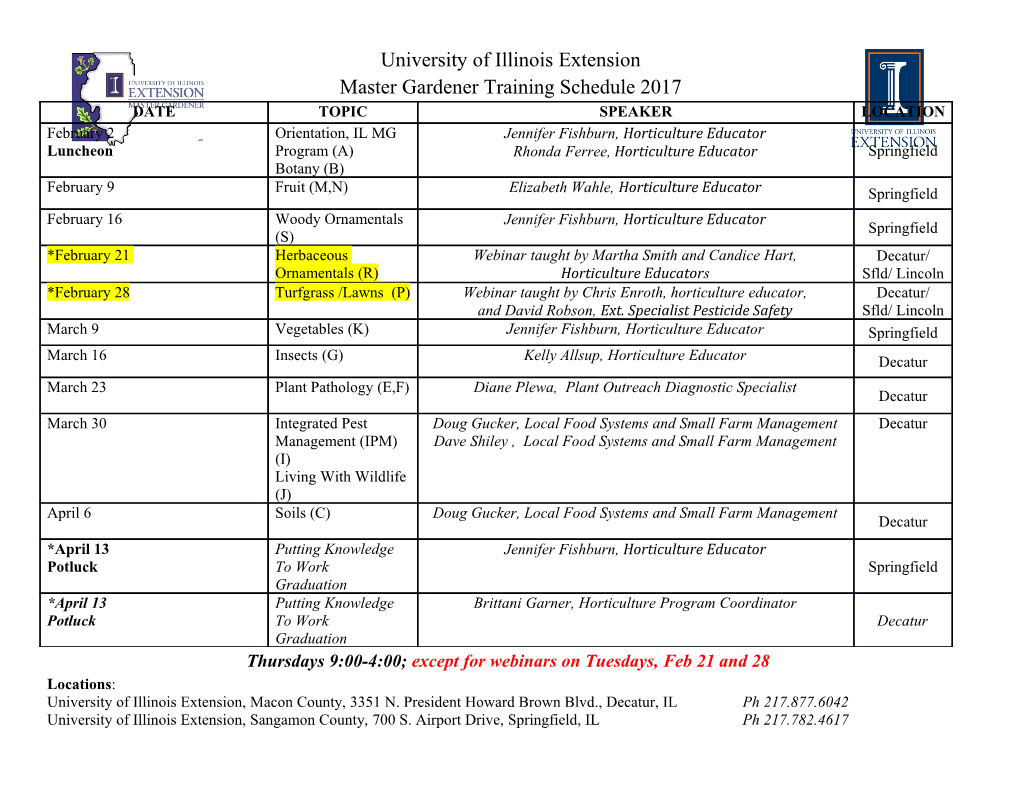
Space Policy 17 (2001) 291–298 Nuclear propulsionFa historical perspective Stanley Gunn*,1 P.O. Box 808, Moorpark, CA 93020-0808, USA Abstract Those who fear development of nuclear propulsion for space travel forget that considerable work on it has already been done, starting in the 1950s, and that the concept of a nuclear rocket was safely and successfully tested in the 1960s. This article describes the history of the US Nuclear Engine for Rocket Vehicle Application programme, with technical details of its development. Although funding for the programme ceased in the 1970s, there is no reason to suppose that the concept would not work today. r 2001 Published by Elsevier Science Ltd. Nuclear propulsion, at least in the lay community, has times was nothing short of watershed research, far- long been a misunderstood technology. More accu- ranging in concept and highly directed in terms of rately, it has been an unknown technology, existing in application. In viewof its potential for the future Ffor the shadowof over four decades of highly successful example in a piloted Mars missionFit is worth chemical propulsion techniques. Yet the truth of the examining this pioneering work in detail. matter is that nuclear propulsion is a viable option that could represent our best chance to put humans in motion towards distant planets in the first decades of the 21st century. Nuclear propulsion is inherently more 1. Nuclear vs. chemical propulsion efficient than chemical methods by a factor of at least two, is significantly simpler in overall concept and could All liquid rocket propulsion systems rely on the be applicable with contemporary vehicles. Moreover, creation of a continuous supply of high-pressure, high- the basics have been understood and studied for over 40 temperature gas, and the expansion of that gas through years. a suitable supersonic nozzle to the system’s low-pressure Meaningful research and development work was environment. In conventional, bi-propellant liquid rock- actually initiated in 1955 by the Atomic Energy et engines, the combustion process defines the tempera- Commission (AEC) and was directed towards the ture and the average molecular weight of this gas supply, utilization of a nuclear thermal rocket (NTR) concept thereby determining the performance (specific impulse) to propel single-stage, ballistic missiles over interconti- of the propulsion system. nental trajectories. At the same time, both the Los A nuclear thermal rocket (Fig. 1), in contrast, Alamos Scientific Laboratory (with the KIWI pro- depends on a temperature source of thermal energy, gramme) and the Lawrence Livermore Laboratories (the typically a high-temperature, solid-core reactor, to heat Tory programme) had begun exploratory propulsion a single propellant (working fluid) to as high a research programmes. Unfortunately, the work came to temperature as possible, and then to expand the a halt in the early 1970s as interestFand fundsFwaned resulting high-temperature gas to the exhaust pressure. and priorities moved in favour of chemical methods. In a practical NTR engine, the working fluid is pumped Nevertheless, what was accomplished in those earlier from its supply tank to the reactor–nozzle subsystem, where it is first used to cool both the nozzle and the *Tel.: +1-818-341-5995. reactor’s pressure shell, the neutron reflector and the E-mail address: [email protected] (S. Gunn). core support structure. Next, the working fluid passes 1 Dr. Stanley Gunn worked on advanced nuclear propulsion through the reactor core where most of the energy being programs and on other advanced technology energy and propulsion programs at Rocketdyne from 1953 until his retirement. This article is released by fissioning uranium atoms is absorbed by the an edited and updated version of one that appeared in the fall 1992 working fluid. Finally, the resultant super-heated gas is issue of Rocketdyne’s Threshold journal. expanded out of the supersonic nozzle. 0265-9646/01/$ - see front matter r 2001 Published by Elsevier Science Ltd. PII: S 0265-9646(01)00044-3 292 S. Gunn / Space Policy 17 (2001) 291–298 temperature to the gases’ average molecular weight, the design of the NTR system has some freedom in the system trade studies involved in the selection of a preferred working fluid. The gas temperature, however, is limited by the intrinsic melting temperature of the fuel element materials. Typically, solid-core reactor perfor- mance can be expected to offer twice the performance of a chemical rocket system, but the attendant engine weight will be significantly greater. 2. The KIWI and Tory programmes At the inception of the KIWI and Tory programmes, the choice of a working fluid was influenced by concerns over the potential for chemical interactions between the fuel elements and the working fluid, as well as by the availability of suitable feed systems equipment to deliver the working fluid to the reactor at the flow rates and pressures planned. Ammonia was selected by the Los Alamos Scientific Laboratory (LASL) as the working fluid for the KIWI 1 reactors, and nitrogen was selected by Lawrence Livermore Laboratories (LLL) for the Tory reactors. Graphite was chosen for the requisite fuel elements because of its high-temperature capabilities and its ability to serve both as a container of uranium atoms and as an effective moderator of the high-energy, fission-produced neutrons. At the same time, the Rocketdyne Div. of North American Aviation initiated nuclear rocket studies for the US Air Force. These early studies showed that for high DV (vehicle velocity achieved at thrust termination) and heavy payload applications, the use of hydrogen as working fluid would result in a significant lessening of the launch weight of single-stage ballistic missiles. Unfortunately, the technology did not exist then to support the design of large-scale, liquid hydrogen pumping systems. As a consequence, Rocketdyne proposed a design for the development of a model liquid hydrogen pump that was capable of delivering 10 000 gallons per minute (gpm) at 1500 psi. The Air Force was impressed with the design and awarded Rocketdyne a follow-on contract to undertake this development effort. Fig. 1. A typical Rover/NERVA nuclear thermal rocket thruster. In 1957, the AEC reviewed the two nuclear rocket reactor programmes and finally chose to focus their resources on LASL’s KIWI reactor, part of the Rover In concept the system is remarkably simple: its programme. LASL, in turn, reviewed its development operating characteristics are well defined, while control plans and, in recognition of the Air Force–Rocketdyne is accomplished by matching the reactor’s heat genera- LH2 pump development programme, decided to switch tion to the working fluid flow rate. To stop the engine, from ammonia to hydrogen as the working fluid. the reactor’s control drums are positioned to place The combined results of the Air Force’s decision to neutron absorption plates close to the core, the implement Rocketdyne’s proposed LH2 pump develop- turbopump is programmed down to cool-off speed and ment programme and LASL’s subsequent decision to thrust is caused to decay. Since the performance of the adopt hydrogen as the working fluid for the KIWI system is based on the ratio of the reactor-exit gas reactor test programmes were to have far-reaching S. Gunn / Space Policy 17 (2001) 291–298 293 effects on NASA’s Apollo programme. The J-2 engine’s pumping systems (featuring an electric-motor-driven MK15 liquid hydrogen pump was derived directly from oxygen pump and a gas-generator, turbine-powered the nuclear rocket programme’s MK 9 liquid hydrogen MK9 LH2 pump) were engineered to provide the pump. necessary propellants for the nozzle heat load tests. The KIWI test programme initially concentrated on This system was, in effect, a breadboard hydrogen– relatively modest power-density reactors (KIWI A, A0 oxygen engine, and was tested in late 1960. and A3), which were rated at 100 MW. The objective A total of five KIWI B reactors were tested in the was to verify the fundamental performance potential of loosely coupled breadboard engine systems that were graphite-moderated fuel elements that could heat assembled in test cells A and C at the Nevada test site hydrogen to as much as 45001R. For these exploratory between 7 December 1961 and 10 September 1964. The tests gaseous hydrogen was to be used as the working final and complete verification of the capabilities of the fluid. Rocketdyne was awarded the contract to design, KIWI reactor occurred on 28 July 1964, when the KIWI fabricate and qualify (by LOX–alcohol chemical thrust B4E reactor was operated at full power and temperature chamber tests) the requisite KIWI A (RN1) nozzles. for 8 min. Then, on 10 September 1964, the same reactor Since the planned operating chamber pressure would was restarted and operated at full power and tempera- only be 100 psi, the predicted heat load was modest, and ture for another 2.5 min. Based on the post-test a double-walled (nickel) water-cooled configuration was appearance of the core, and on the analyses of the adopted. recorded test parameters, the breadboard engine system The three KIWI reactors were tested at the nuclear test was judged a complete success, clearing the way for rocket development site in Nevada in July 1959 and in a similar Westinghouse NRX-A2 reactor to begin its test July and October 1960. The results of these pioneering evaluation. tests met their objectives and clearly demonstrated that The formation of NASA in July 1958 produced a coated, graphite-fuel elements could be used to heat major change in the thrust and subsequent scope of the hydrogen to temperatures in excess of 40001R. USA’s nuclear rocket programme. Possible application interest shifted from the Air Force’s missile application 2.1.
Details
-
File Typepdf
-
Upload Time-
-
Content LanguagesEnglish
-
Upload UserAnonymous/Not logged-in
-
File Pages8 Page
-
File Size-