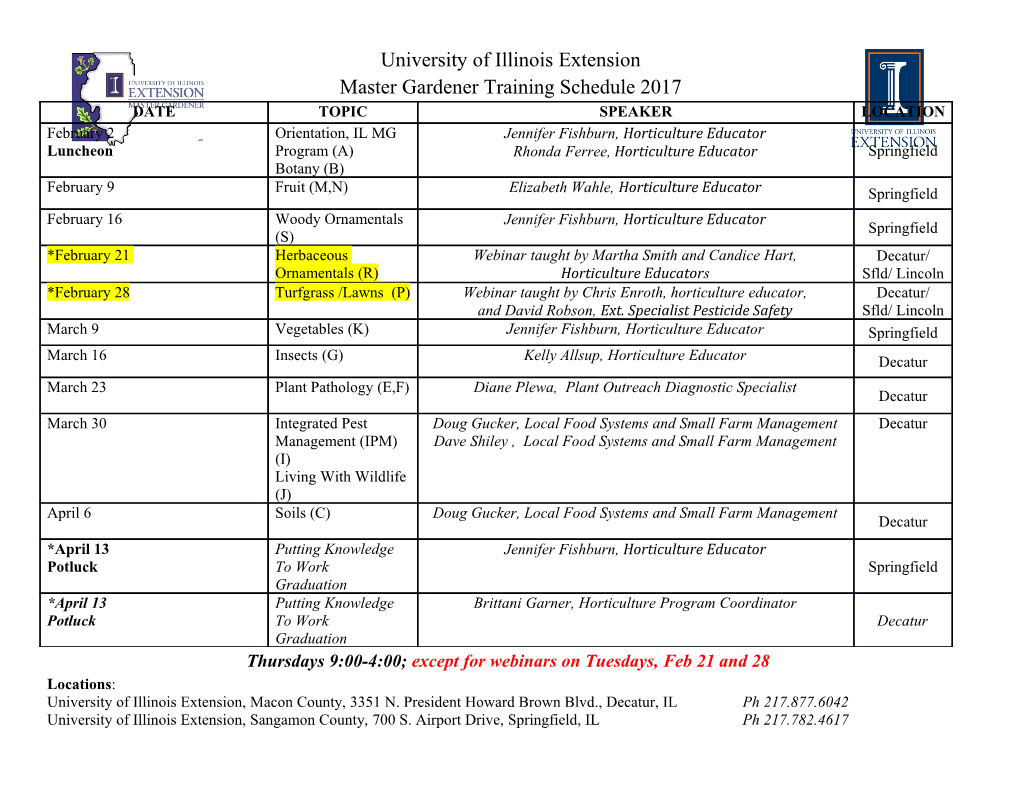
iRliS942 Bureau of Mines Report of Investigations/1985 Application of Cast-On Ferrochrome-Based Hard Surfacings to Polystyrene Pattern Castings By J. S. Hansen. R. R. Jordan. S. J. Gerdemann. and G. F. Soltau UNITED STATES DEPARTMENT OF THE INTERIOR Report of Investigations 8942 Application of Cast-On errochrome-Based Hard Surfacing to Polystyrene Pattern Castings By J. S. Hansen, R. R. Jordan, S. J. Gerdemann, and G. F. Soltau UNITED STATES DEPARTMENT OF THE INTERIOR Donald Paul Hodel, Secretary BUREAU Of MINES Robert C. Horton. Director of Congre::;s Cataloging in Publication Data: Application of cast-on ferrochrome-based hard surfacings ro polystyrene pancrn cascings,. (Burcau of 'Iincs report of in \'cstig,Hion s Bibliography: p. Supt, of Docs. nO.: I 28.23:8942. I. Hard.facing. 2. Hard-facing alloys. I. Hansen, J. (J cffrcy 5.). II. Series: Report of investigations (United States. l3ureau of \1ines) ; 8942. TN23. U43 622s CONTENTS Ab s t r ac t .•••..•....•••.........••..•....................•..•.............•...•. 1 In t roduc t ion .............................................•..........•.......... 2 Background •..••...............•.• " .......•...............••.................... 2 Process of cast-on surfacing with polystyrene patterns ••••••••••••••••••••••••• 3 Experimental procedure .•..•.....•....•...••..•..........•.............•........ 7 Definition of variables affecting ferrochrome cast-on surfacings ••••••••••••••• 7 Results ....................................................................... 10 Binder type .....•..•...••.......•.•...•••..•••.•...........................•• 10 Bi nder level ..............•.................................................. 11 Surfacing material particle size .......•..........•••........................ 12 Pour ing temp er a t u re ....•••.......... ~ . ...........•.....•....•••••....•........ 12 VacullID. level ......•....•.........................•................•..•....... 14 ~pplication procedure .•••.......................••........................... 14 Cas ting thickness ...........................••••......................•••.... 15 Surfacing thickness •......••.................•........••.............•...•... 15 Compositional variations on ferrochrome surfacings ••••••••••••••••••••••••••••• 21 Steel and white iron substitutes for ferrochrome ••••••••••••••••••••••••••••••• 23 Field trials •......•........•..•.•..............•....................•......... 24 Bucket-wheel excavator teeth .••••.•.......•....................•....•........ 26 Plowshares •• .. .. .. .. .. 30 Conclusions ••• .. .. .. .. .. 32 References .•...•••................................••••••.••.•.................. 33 Appendix.--Ranking guide for defects ••••••••••••••••••••••••••••••••••••••••••• 36 ILLUSTRATIONS 1. Process steps for applying cast-on surfacings to polystyrene pattern cas tings •• It. • • • • • • • • • • • • • • • • • • • • • • • • • • • • • • • • • • • • • • • • • • • • • • • • • • • • • • • • • • • • • 4 2. Hard-surfacing material applied to a polystyrOene pattern corresponding to the casting wear-prone area •••••••••••••••••••••••••••••••••••••••••••••• 5 3. Pattern placed in unbonded sand in double-walled vacuum flask ••••••••••••• 6 4. Stopper rod procedure for preventing slag and air from entering gating s ys tem and cas ting ............••.....••••...............•................ 8 5. Pattern incorporating sample ridges for three separate surfacings ••••••••• 10 6. Effect of surfacing binder level •••••••••••••••••••••••••••••••••••••••••• 13 7. Effect of particle size ••••••••••••••••••••••••••••••••••••••••••••••••••• 13 8. Effect of temperature on external casting porosity at two vacuum levels ••• 14 9. Microstructure showing dendrites and interdendritic carbides typical of thin (1/16-in), chromium-rich, white iron surfacings derived from f errochrome ................................................................ 16 10. Effect of increasing surfacing thickness •••••••••••••••••••••••••••••••••• 17 11. Microstructures of surfacings at three thicknesses •••••••••••••••••••••••• 18 12. Ef fec t of surf acing thickness •....•....................................... 20 13. X-ray radiographs showing inclusions at the surfacing-casting interface of samples surfaced with commercial ferrochrome and number 2 low-impurity CllS tom-mel ted ferrochrome ..............•....•.•.....•.................... 21 14. Microstructure of number 3 custo~melted ferrochrome and commercial ferro­ chrome with 0.1 g added carbon per gram of ferrochrome ••••••••••••••••••• 22 15. Cast iron microstructure of cast-on surfacing with the composition Fe-5C- 21Cr-8. 5Cb-9Mo-O. 3Mrl-O. 6Si. • . 24 16. Cross sections of a 4-in ball valve, 6-in crusher plate, and 3-in cylinder showing ferrochrome cast-on surfacings ••••••••••••••••••••••••••••••••••• 25 ILLUSTRATIONS--Continued 17. One of eight buckets of a bucket-wheel excavator at a Centralia, WA, coal mine. • . • . • . • . • . .• . • . • . 26 18. Bucket-wheel excavator tooth pattern with surfacing powder applied to outside. .•• .... .•. ... .. .. .. .. ....... ....• .. .. •. • ...... .. .. .•. .. ... 27 19. Radiograph of bucket-wheel excavator tooth showing small voids at casting- surfacing interface...................................................... 28 20. Microstructure of number 2 custom ferrochrome and white iron alloy sur·' faces from bucket-wheel excavator teeth used in field trials............. 28 21. Cross section of bucket-wheel excavator tooth tip showing ferrochrome sur- facing along outside edge................................................ 29 22. Bucket-wheel excavator teeth after field trials at Centralia, WA, coal mine ........•..••......•......•..•..•..............•...•......•..•....... 29 23. Plowshare affixed to lower portion of one of five blade assemblies........ 30 24. Weld-rod hard-faced control plowshare and ferrochrome cast-on-surfaced plowshare after field trials............................................. 31 TABLES 1. Binders investigated for use with ferrochrome powders..................... 11 2. Experiments to determine effect of five variables on surfacing integrity with centerpoint checks.................................................. 12 3. Experiments without centerpoint checks to determine effect of five vari- ables on surfacing integrity............................................. 15 4. Effect of surfacing thickness on surfacing composition and hardness....... 19 5. Dry-sand, rubber-wheel abrasion test results on cast-on surfacings derived from ferrochrome powders................................................. 20 6. Compositions of white iron and steel cast-on surfacings and selected dry- sand, rubber-wheel abrasion test results................................. 23 7. Plowshare field trial parameters and test results......................... 31 UNIT OF MEASURE ABBREVIATIONS USED IN THIS REPORT °c degree Celsius lb pound DPH diamond pyramid hardness lb/ft 3 pound per cubic foot ft foot min minute g gram mm millimeter g/in2 gram per square inch mm3 cubic millimeter h hour pct percent in inch s second in2 square inch vol pct volume percent in Hg inch of mercury (atmospheric pressure) LI ION CAST-ON FERROCHROME-BASED H S ACINGS POLYSTYRENE PATTERN CAST INGS 4 By J. S. Hansen, 1 R. R. Jordan,2 S. J. 3 and G. F. Soltau ABSTRACT To advance technology that can conserve critical materials, the Bureau of Mines investigated a cast-on hard-surfacing that wear resistance and confines alloy additions to wear-prone surfaces. Wear-resistant material in form is on a polystyrene , the is embedded in a mold of unbonded s and the wear-resistant material is transferred to a cas sur­ face at the time of For low-stress abrasion, derived from high-carbon ferro- chrome had higher wear resistance than did commercially available weld- hard The microstructure of the was typi- white iron carbides. Free carbon added to the ferrochrome powder produced more M7C3 carbides than did material contained in surfacings made from ferrochrome alone, and improved the wear resistance. Several white iron powders with greatly reduced chromium contents also white iron contain- M7C3 carbides. One derived from white iron powder had wear resistance to that of weld-deposited hard facings. Among the parameters investigated, surfacing thickness was found to have a or influence on diffusion of elements out of the , microstructure, and wear resistance. The results of field tests on bucket-wheel excavator teeth and plowshares with cast-on hard surfacing are given. 3 Chemical technician. Albany Research Center, Bureau of Mines. , OR. 2 INTRODUCTION The Bureau of Mines is concerned with part may cause the overlay to crack, and the conservation of critical materials the heat generated during application may and improved performance of equipment result in harmful residual stresses or used in the mining and minerals process­ loss of heat treatment benefits to the ing industries. One of the major causes part. Excessive dilution of the overlay of failure of this equipment is wear. by iron from the part or absorption of Depending upon the severity of wear, atmospheric gases during application may equipment components may last as long as reduce wear resistance or cause failure several years or as briefly as a few upon impact. hours. The high costs involved, in terms Coatings also are applied by flame and of both labor and raw materials, have plasma spraying of powdered materials. provided the driving force for many ef­ Such coatings are uniform, and the pro­ forts to
Details
-
File Typepdf
-
Upload Time-
-
Content LanguagesEnglish
-
Upload UserAnonymous/Not logged-in
-
File Pages42 Page
-
File Size-