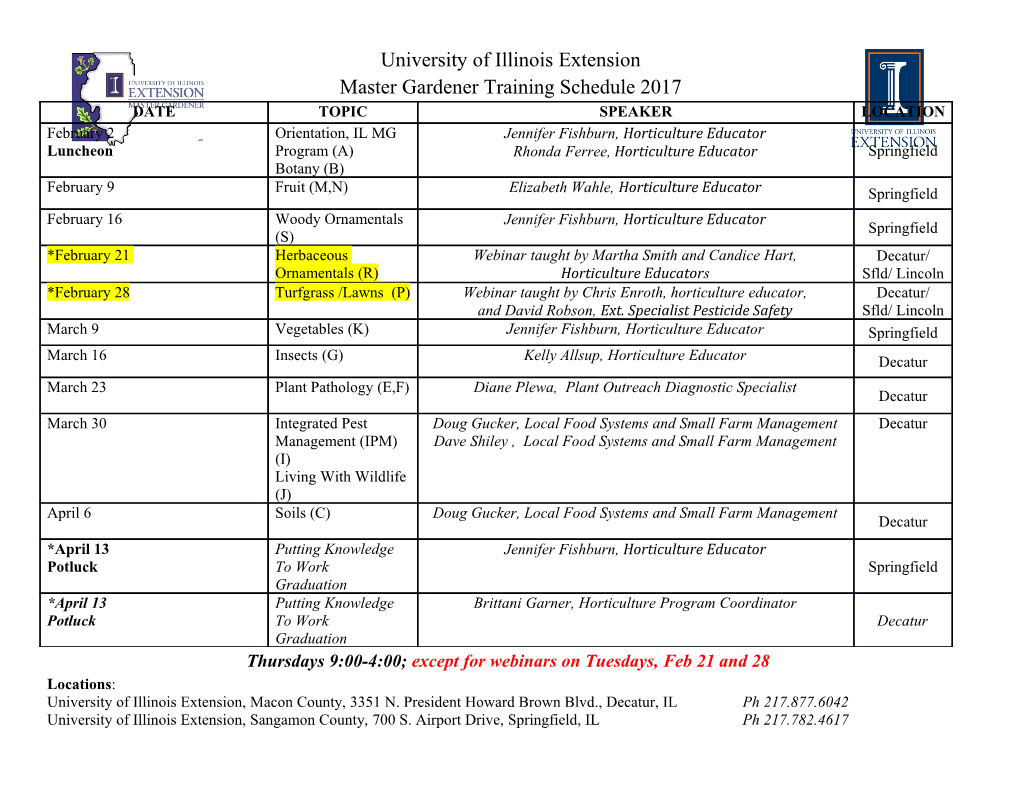
materials Article Mechanical Vibration Damping and Compression Properties of a Lattice Structure Katarina Monkova 1,2,* , Martin Vasina 2,3,* , Milan Zaludek 2, Peter Pavol Monka 1,2 and Jozef Tkac 1 1 Faculty of Manufacturing Technologies, Technical University in Kosice, 080 01 Presov, Slovakia; [email protected] (P.P.M.); [email protected] (J.T.) 2 Faculty of Technology, Tomas Bata University in Zlin, Nam. T.G. Masaryka 275, 760 01 Zlin, Czech Republic; [email protected] 3 Faculty of Mechanical Engineering, VSB-Technical University of Ostrava, 17. Listopadu 15/2172, 708 33 Ostrava-Poruba, Czech Republic * Correspondence: [email protected] (K.M.); [email protected] (M.V.); Tel.: +421-55-602-6370 (K.M.); +420-57-603-5112 (M.V.) Abstract: The development of additive technology has made it possible to produce metamaterials with a regularly recurring structure, the properties of which can be controlled, predicted, and purposefully implemented into the core of components used in various industries. Therefore, knowing the properties and behavior of these structures is a very important aspect in their application in real practice from the aspects of safety and operational reliability. This article deals with the effect of cell size and volume ratio of a body-centered cubic (BCC) lattice structure made from Acrylonitrile Butadiene Styrene (ABS) plastic on mechanical vibration damping and compression properties. The samples were produced in three sizes of a basic cell and three volume ratios by the fused deposition modeling (FDM) technique. Vibration damping properties of the tested 3D-printed ABS samples were investigated under harmonic excitation at three employed inertial masses. The metamaterial behavior and response under compressive loading were studied under a uniaxial full range (up Citation: Monkova, K.; Vasina, M.; to failure) quasi-static compression test. Based on the experimental data, a correlation between Zaludek, M.; Monka, P.P.; Tkac, J. the investigated ABS samples’ stiffness evaluated through both compressive stress and mechanical Mechanical Vibration Damping and vibration damping can be found. Compression Properties of a Lattice Structure. Materials 2021, 14, 1502. https://doi.org/10.3390/ma14061502 Keywords: mechanical vibration; displacement transmissibility; excitation frequency; compression behavior; Acrylonitrile Butadiene Styrene; 3D printing Academic Editor: Juergen Stampfl Received: 9 February 2021 Accepted: 12 March 2021 1. Introduction Published: 18 March 2021 Nowadays, ecological problems and efforts to save energy are of great importance in industry. Industrial processes’ design can be improved to overcome these problems, but Publisher’s Note: MDPI stays neutral these design improvements have inevitable limitations. Further process improvements with regard to jurisdictional claims in can be made by developing and improving the materials used in the processes. Design published maps and institutional affil- will inevitably change as new materials are used. Currently, an increasingly important iations. characteristic for materials used in various fields, such as automotive, aerospace, construc- tion, and biomedical industries, is being lightweight, usually caused by material porosity. Weight reduction can significantly reduce material and energy consumption, carbon dioxide emission, and waste generation, promoting the sustainability of materials used in various Copyright: © 2021 by the authors. industries. Porous materials with good mechanical properties can reduce production costs, Licensee MDPI, Basel, Switzerland. make production more efficient, and make a product more environmentally friendly. This article is an open access article The development of additive technologies now makes it possible to produce lightweight distributed under the terms and metallic and nonmetallic porous materials with properties that are highly controllable. conditions of the Creative Commons This means that their structure is designed in a controlled way. Such a structure is based Attribution (CC BY) license (https:// on a so-called basic cell, which is regularly distributed (or according to a certain rule) in creativecommons.org/licenses/by/ the core of the product and whose size is also explicitly controlled. A special category 4.0/). Materials 2021, 14, 1502. https://doi.org/10.3390/ma14061502 https://www.mdpi.com/journal/materials Materials 2021, 14, 1502 2 of 16 of cellular materials is materials with a lattice structure. In the language of structural engineering, a lattice truss or spatial truss is an arrangement of struts that are pin-jointed or rigidly connected at their joints [1]. The investigation of the behavior of cellular materials with lattice structures make it possible to use the most suitable structure (with specified properties) for a component that is particularly stressed in real operation. The basic building unit of cellular materials is a so-called cell that regularly repeats in the structure and can be distributed in one or more independent directions. The basic cell type can be different from a cubic, from a honeycomb up to a spherical type. Another important property is the specific volume of the material or so-called volume ratio Vr, which is expressed by Equation (1): Vso V = (1) r Vto where Vso is the volume of a solid material used for the cell structure building and Vto is the total volume of the sample. Many researchers have dealt with the mechanical properties of lattice materials. The influence of the length and orientation of the strut on the elastic mechanical response of the modified cubic lattice structures has been studied by Hasanain [2], Tahseen [3], and Alwattar [4]. The reference models’ samples were made by fusion deposition (FDM) tech- nique using acrylonitrile-butadiene-styrene (ABS) material and tested under compression load. It has been observed that the fixed length of a strut of the body-centered cubic (BCC) lattice structure with an angle of 100◦ offers the highest modulus of elasticity. However, the highest specific deformation energy absorption and specific stiffness, as well as the smallest weight value, were given by the variant strut length with a strut angle of 40◦. The results obtained from the finite element analysis (FEA) were compared with experimentally measured data, and a good agreement within the linear elastic limit has been achieved. The experimental tests performed by Iyibilgin [5] to evaluate the compressive properties (yield strength and compressive modulus) of different ABS 3D-printed cellular lattice structures showed that the differences between the different lattice structures were in the range of 7%. Fadeel [6] also discussed the behavior of ABS 3D-printed lattice structures during compression deformation through both physical tests and computer modeling. The results have shown that the strength of the lattice structures is greater when vertical elements are present, and it depends on the lattice geometry rather than its mass. Gautam [7] has been interested in the compressive properties of additively fabricated functionally graded Kagome structures made of Ti–6Al–4V and ABS materials. It was found that a function- ally graded Kagome structure provides 35% more energy absorption than the uniform density structure. Many researchers have also studied the failure of compression-loaded lattice structures. Cantrell [8] and Al Rifaie [9] focused on the failure behavior of 3D-printed lattice structures. They concluded that ABS material exhibited a hybrid behavior between strain and bend dominated properties. The results also showed that the failure of a compressed lattice structure is initiated in the regions of the connection nodes and that the selective placement of vertical support struts in the unit cell affects both the absolute and specific mechanical properties of the lattice structures. Calise and Saigal [10] studied the anisotropy and failure in octahedral lattice structures of two different relative densities, which were made from ABS material using FDM technology. It was found not only that the stiffness and strength of the as-fabricated parts are anisotropic, but also that they are a function of the relative density/strut diameter of the structure. Several authors have already discussed the stiffness and strength of the various lattice structures [11–15]. Mahshid et al. [16] fabricated structure samples, including solid, hollow, and lattice structure, and compared the strength of structures by the compression test. The result indicated that, though the strength of the lattice structure was lower than that of the solid structure, it can still meet the application requirements, and reduced the use of materials, achieving a lightweight design. Utomo [17] was concerned with Materials 2021, 14, 1502 3 of 16 the determination of the compressive strength of a 3D polymeric lattice structure as a template in powder metallurgy. Lattice structured samples were made of ABS (Acrylonitrile Butadiene Styrene), PLA (Polylactic Acid), and PVA (Polyvinyl Alcohol) filaments. They were designed in a cubic shape with uniform total dimensions, but with variations in pore size. Both computational and experimental tests were performed to determine the compressive strength of these structures, while observing the resulting stresses, strains, and deformations of the 3D polymer lattice. The results confirmed that the variations in materials and pore size significantly affect the stress, strain, and deformation of the 3D polymer lattice materials. Ozdemir et al. [18] carried
Details
-
File Typepdf
-
Upload Time-
-
Content LanguagesEnglish
-
Upload UserAnonymous/Not logged-in
-
File Pages16 Page
-
File Size-