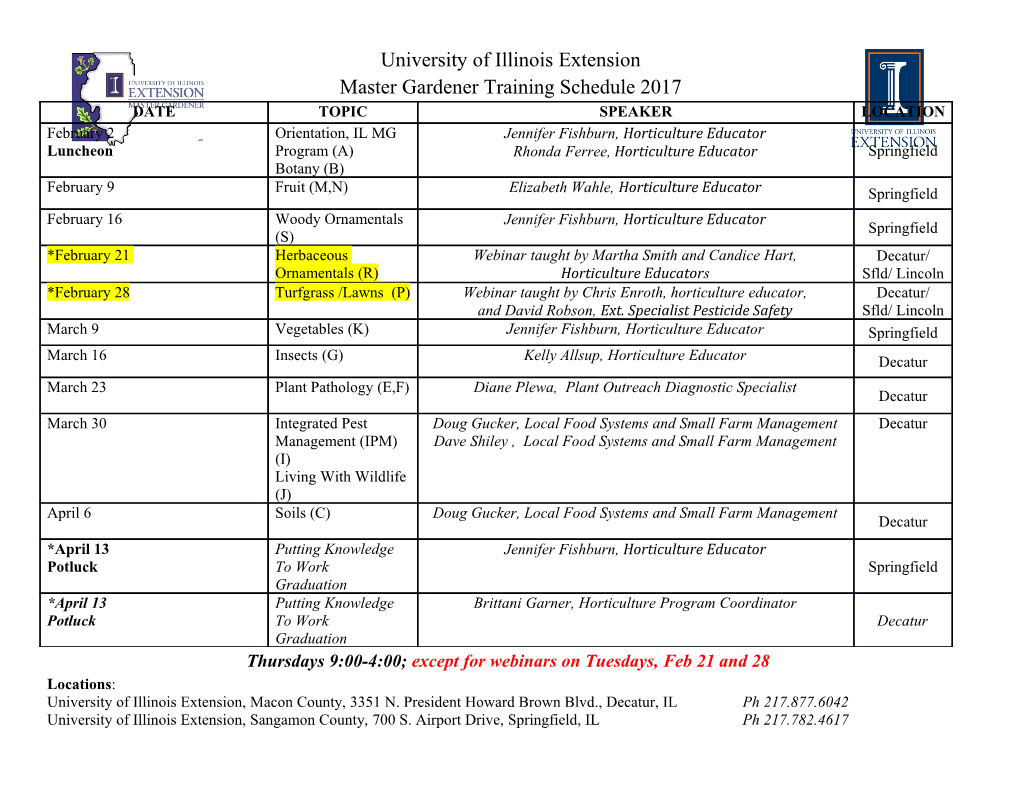
DESKTOP USE OF COMPUTATIONAL FLUID DYNAMICS TO DESIGN AND TROUBLESHOOT COMPRESSORS AND TURBOEXPANDERS by Grant Nordwall Senior Machinery Engineer Jigger Jumonville Senior Consulting Engineer Mafi-Trench Corporation Santa Maria, California and Terryl Matthews Principal Rotating Equipment Specialist Bechtel Corporation Houston, Texas Grant Nordwall is a Senior Machinery Engineer for Mafi-Trench Corporation, in Terryl Matthews is a Principal Rotating Santa Maria, California. He has been with Equipment Specialist with Bechtel Corpora- Mafi-Trench since 1990 working in the tion, in Houston, Texas. He retired in 2003 areas of machine design, performance from Dow Chemical, Design and Construc- testing, rotordynamic analysis, and aerody- tion, after 30 years. His responsibilities namics including computational fluid there included specifications, technical dynamics. support, mechanical and performance Mr. Nordwall received his B.S. degree testing, consulting, and field assistance in (Mechanical Engineering, 1990) from the area of rotating equipment. California Polytechnic State University. He Mr. Matthews holds a B.S. degree has continued his education with rotordynamic and aerodynamic (Mechanical Engineering, 1972) from the University of Houston. courses at Concepts NREC, Engineering Dynamics Inc., Rotordy- Author of six technical papers, he is a member of ASME, the Ethyl- namics Seal Research (RSR), AEA Technology, and Numeca. Mr. ene Producers Conference Rotating Machinery Subcommittee, and Nordwall is a registered Professional Engineer in the State of the ASME International Gas Turbine Institute’s Industrial and Cogen- California. eration Committee. He is a former member of the API Committee on Refinery Equipment and sponsor for SOME, served on API Task Forces 613 and 677, is a former member of ASME B73 Committee, Jigger Jumonville is a Senior Consulting and is a registered Professional Engineer in the State of Texas. Engineer for Mafi-Trench Corporation, in Santa Maria, California. He has been with them since 1990 and has held many titles ABSTRACT including Chief Engineer. Mr. Jumonville is For several decades, turboexpander designers have relied on currently involved in mechanical, aerody- experience and traditional design tools to create their products. namic, and magnetic bearing product Recent advances in CFD (computational fluid dynamics) software improvements, as well as troubleshooting and desktop computing power have made it possible for some unusual field problems. Previously, he manufacturers to investigate unique fluid flow fields in routine worked for 10 years at the Dow Chemical design applications. Company in Plaquemine, Louisiana. Five In this paper, four case studies of CFD in high performance of those years were spent as the Rotating Equipment Engineer in a expanders and compressors are discussed. The first case study world scale ethylene plant. shows CFD used as a screening tool for a radial inflow turbine Mr. Jumonville received his B.S. degree (Mechanical stage. The second demonstrates a challenging compressor design, Engineering, 1979) from Louisiana State University. While in where CFD was integrated into the design process. The third case school, he was a member of various honorary societies, including study details the uncommon application of CFD to a fluid film Pi Tau Sigma and Tau Beta Pi. He is a part-time professor at Cal thrust bearing, showing comparisons to traditional bulk flow cal- Poly in San Luis Obispo, where he teaches a senior level culations. The fourth case study highlights the use of CFD in Mechanical Engineering course in turbomachinery. Mr. troubleshooting a centrifugal compressor stage. The CFD solution Jumonville is a registered Professional Engineer in the State of was subsequently verified by factory testing, and the equipment is Louisiana. successfully operating in the field. 71 72 PROCEEDINGS OF THE THIRTY-SECOND TURBOMACHINERY SYMPOSIUM • 2003 INTRODUCTION High speed turboexpanders are widely used in many industrial processes, including hydrocarbon processing, chemical, and air separation plants. The Seventh Edition of API 617 (2002) now includes a chapter on turboexpanders, which confirms their wide use and importance in our industry. The typical turboexpander includes a high speed, high efficiency turbine, direct coupled to either a centrifugal compressor or an electrical generator, with a rotor supported by either oil bearings or magnetic bearings. The design tools discussed in this paper include FINE/Turbo by Numeca (CFD software), CCAD® by Concepts NREC (three-dimen- sional blade design and analysis software), NSFixed by Rotordynamics Seal Research (Navier-Stokes thrust bearing analysis), and various inhouse programs by Mafi-Trench Corporation. While all four case studies relate to turboexpander components, the information and results can be applied to other machines that use centrifugal compressors or oil lubricated thrust bearings. CASE 1—RADIAL INFLOW EXPANDER DESIGN Figure 1. Radial Inflow Expander Computational Mesh. (h− h) A turboexpander is used in hydrocarbon processing to refriger- Nozzle Efficiency = 0T1a − ate a gas stream, by removing work directly from the gas. By (h0Th1ideal) (1) expanding the gas in a nearly isentropic fashion, energy in the high pressure gas entering the expander is removed and the gas exits at a lower pressure and temperature. where: A radial inflow expander is able to accomplish near-isentropic h0T = Total inlet enthalpy expansion by a series of efficient energy conversions. The gas flows h1a = Actual IGV static exit enthalpy radially inward and is accelerated through inlet guide vanes and h1ideal = Ideal static outlet enthalpy turned. The swirling, high velocity gas enters the expander impeller It should be noted that expansion through nozzles is an isen- with relatively low incidence, because the blade tip velocity at the thalpic process, where the total enthalpy at the nozzle exit will be impeller outside diameter approximately matches the gas velocity. the same as the total enthalpy at the nozzle inlet (h0T). The static Work is extracted from the gas by removing this momentum: as the enthalpies can be used when modeling the process as isentropic. gas moves inward, it is forced to slow down because the blade tan- However, there will be some loss of total pressure, as a portion of gential velocity decreases with the decreasing radius. The blades the inlet pressure is not converted to velocity, but increases the also turn the gas to reduce the gas velocity even further. As a result, static temperature (heating caused by friction). This increase in the gas exits the impeller with low tangential velocity relative to the static outlet temperature makes h1a larger than h1ideal, and thus outside world. In this way, the angular momentum of the gas is effi- results in an efficiency less than one. ciently removed. Up to 10 percent of the stage energy still remains The nozzle efficiency should be above 95 percent for well as through-flow velocity at the impeller exit. Much of this designed vanes. remaining energy can be recovered with a conical diffuser. By con- Figure 2 and Figure 3 show the reduction in static pressure in the verting the velocity into pressure, the static pressure at the turbine IGVs and the corresponding increase in velocity. The velocity and discharge is reduced, which results in additional refrigeration. direction of the gas is relatively uniform at the exit of the IGV A radial inflow turbine is commonly designed for 50 percent channel. The total pressure plot of Figure 4 indicates that the flow reaction, with 50 percent of the enthalpy change occurring in the has accelerated with a minimal loss of total pressure. The plot also rotating section (the impeller). As an approximation, the “degree of shows the wake regions, which are acceptably small. The resulting reaction” is sometimes defined as the pressure drop across the rotor nozzle efficiency is 96 percent. divided by the pressure drop across the stage. As with most turbomachinery, the flow of gas through an expander stage encounters several rapid transitions. Although the guide vane and impeller geometry can be designed based on bulk flow assumptions, a CFD analysis provides insight into important localized fluid flow patterns, to refine the bulk-flow design. The expander stage in this discussion incorporates an 8.5 inch (216 mm) diameter impeller, rotating at 26,000 rpm. It is designed to provide 50°F (30°C) of refrigeration from a 90 psi (6 bar) pressure drop, and will provide 860 hp (660 kW) of power to a cen- trifugal compressor mounted on the same shaft. The CFD model for this stage included the inlet guide vanes, unshrouded rotor with tip clearance, and a conical diffuser. The computational mesh is shown in Figure 1. The CFD software’s implementations of the k-epsilon turbulence model were used. Inlet Guide Vanes Figure 2. Absolute Mach Number Contour in Expander Inlet Guide The pressure drop through the inlet guide vanes (IGVs) is used Vanes. to accelerate the gas, as it turns toward a circumferential direction. The goal is to do this with a minimal loss in total pressure, with Impeller uniform velocity and flow angle at the IGV exit, and to create a minimal wake region downstream. A “nozzle efficiency” for the When an expander stage operates at 50 percent reaction, the tan- vanes can be defined as in Equation (1): gential velocity at the IGV exit approximately matches the blade DESKTOP USE OF COMPUTATIONAL FLUID DYNAMICS 73 TO DESIGN AND TROUBLESHOOT COMPRESSORS AND TURBOEXPANDERS reaction was only 20 percent. This leads to high incidence on the blades at the inlet and very little pressure drop available to accel- erate the gas through the impeller. The CFD analysis of the initial rotor design showed recircula- tion in the rotor passage, near the shroud (Figure 5). This is due to the high incidence. Separation also occurred at the trailing edge of the splitter blade, and this resulted in a substantial swirling of the gas entering the diffuser. Figure 3. Static Pressure Contour in Expander Inlet Guide Vanes. Figure 5. Relative Velocity Vectors near Shroud of Original Figure 4.
Details
-
File Typepdf
-
Upload Time-
-
Content LanguagesEnglish
-
Upload UserAnonymous/Not logged-in
-
File Pages14 Page
-
File Size-