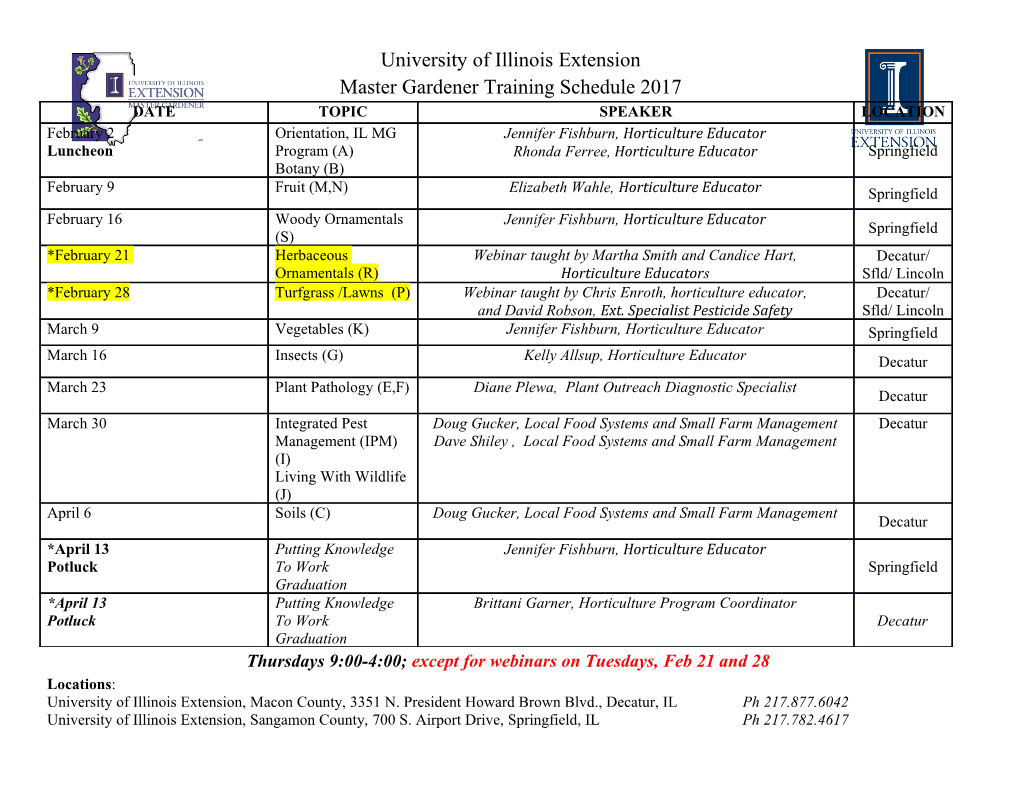
University of Colorado Department of Aerospace Engineering Sciences ASEN 4018 Conceptual Design Document (CDD) VORTEX: Vertically Optimized Research, Testing, & EXploration September 28th, 2020 1 Information 1.1 Project Customers Name: Steve Borenstein Email: [email protected] Phone: 303-735-7558 1.2 Group Members Name: Mohamed Aichiouene Name: Stephen Albert Email: [email protected] Email: [email protected] Phone: 720-883-8862 Phone: 303-358-0177 Name: Joe Buescher Name: Bill Chabot Email: [email protected] Email: [email protected] Phone: 720-331-0852 Phone: 720-454-4430 Name: Colton Cline Name: Brandon Cummings Email: [email protected] Email: [email protected] Phone: 720-255-8935 Phone: 303-882-4382 Name: Roland Ilyes Name: Delaney Jones Email: [email protected] Email: [email protected] Phone: 303-856-8124 Phone: 720-490-7728 Name: Cameron Kratt Name: Michael Patterson Email: [email protected] Email: [email protected] Phone: 719-351-1003 Phone: 303-513-0325 Name: Joseph Rooney Name: Justin Troche Email: [email protected] Email: [email protected] Phone: 309-214-0438 Phone: 718-915-8444 1 Nomenclature TWR Thrust to weight ratio COTS Commercial off-the-shelf products RAP-Cat Rapid Acceleration Pneumatic Catapult 2 Contents 1 Information 1 1.1 Project Customers.....................................1 1.2 Group Members......................................1 Nomenclature 2 2 Project Description5 2.1 Project Overview......................................5 2.2 Objectives..........................................5 2.3 Concept of Operations...................................8 2.4 Functional Block Diagram.................................9 2.5 Functional Requirements.................................. 10 3 Design Requirements 11 4 Key Design Options Considered 14 4.1 VTOL Configuration.................................... 14 4.1.1 Tilt Rotor...................................... 15 4.1.2 Tail sitter...................................... 18 4.1.3 Hybrid........................................ 21 4.1.4 Tilt Wing...................................... 23 4.2 Landing Sensors...................................... 25 4.2.1 LiDAR....................................... 26 4.2.2 Micro Radar.................................... 27 4.2.3 Sonar........................................ 28 4.3 Battery Chemistry..................................... 28 4.3.1 Lithium Polymer (Li-Po)............................. 29 4.3.2 Lithium-Ion (Li-ion)................................ 29 4.3.3 Nickel Metal Hydride (NiMH)........................... 30 4.3.4 Nickel Cadmium (NiCd).............................. 30 4.3.5 Lithium Iron Phosphate (LiFePO4)........................ 31 4.4 Flight Controller Firmware................................ 32 4.4.1 ArduPilot...................................... 32 4.4.2 PX4......................................... 32 4.4.3 iNav......................................... 33 4.4.4 PaparazziUAV................................... 33 5 Trade Study Process and Results 34 5.1 VTOL Configuration.................................... 34 5.1.1 Criteria and Weight Assignment......................... 35 5.1.2 Scale Assignment.................................. 35 5.1.3 VTOL Configuration Trade Matrix........................ 37 5.2 Landing Sensors...................................... 38 5.2.1 Criteria and Weight Assignment......................... 38 5.2.2 Scale Assignment.................................. 39 3 5.2.3 Trade Matrix.................................... 41 5.3 Battery Chemistry..................................... 41 5.3.1 Criteria and Weight Assignment......................... 42 5.3.2 Scale Assignmnent................................. 43 5.3.3 Trade Matrix.................................... 43 5.4 Flight Controller Firmware................................ 44 5.4.1 Flight Controller Firmware Criteria Standards................. 45 5.4.2 Scale Assignment.................................. 45 5.4.3 Flight Controller Firmware Trade Matrix.................... 47 6 Selection of Baseline Design 47 6.1 VTOL Configuration.................................... 47 6.2 Landing sensors....................................... 47 6.3 Battery Chemistry..................................... 48 6.4 Flight Control Firmware Design Option......................... 48 Bibliography 49 4 2 Project Description 2.1 Project Overview The Integrated Remote and In-Situ Sensing (IRISS) group at the University of Colorado Boulder currently utilize a fleet of unmanned aircraft to collect atmospheric data in order to improve the conceptual model of supercell thunderstorms. These unmanned aerial vehicles (UAVs) are launched into flight from a catapult system mounted to the top of an automobile or from a bungee rail system. The IRISS group has expressed desire for an alternative to this fleet of UAVs: a vertical takeoff and landing (VTOL) drone. The launch sites of the UAVs currently utilized are restricted to wide open spaces to allow for belly landings in open fields. A VTOL capability would allow IRISS to launch in a wide variety of locations, including heavily wooded areas and coastal regions. IRISS desires the vertical takeoffs and landings to be completely autonomous– not requiring any input from the pilot. Further, the IRISS team desires a UAV capable of one hour of cruise time, including an additional takeoff and landing during the mission. The replication cost for one VTOL UAV must be under $1000, excluding the avionics package. The successful completion of this project will further the IRISS group’s effort in reducing false alarm tornado warnings and improving detection of potentially lethal storms. 2.2 Objectives 1. Flight - The aircraft shall be capable of vertical takeoffs and landings. In between takeoff and landing the aircraft shall be able to maintain a steady hover, transition from vertical flight mode to horizontal flight mode, and transition back to vertical flight mode from horizontal flight. As a customer requirement, stability in 5-7 m/s is expected but does not need to be validated as part of this project. Verification: Before the aircraft is assembled, the motors and propellers shall be tested on a static test stand to prove that a thrust to weight ratio (TWR) greater than 1 can be generated. Then the transition mechanisms and software will be tested while the aircraft is fixed to the ground to demonstrate functionality. Next a tethered flight will be conducted to show that steady hover can be achieved. The aircraft will then be tested with the RAP- Cat launch system to demonstrate compatibility. Finally, full flight regime will be tested demonstrating full transition of flight modes starting from both vertical takeoff and launch from the RAP-Cat. 2. Budget - The final aircraft design shall have a production cost below $1000 per unit, per customer request. This is to increase the ease of manufacturing and production of multiple aircraft. This budget does not include the standard avionics kit provided by the customer but does include the Drak wing kit. Verification: During the design process, material costs will be tracked and monitored to ensure that a production model does not exceed the desired amount. After design and testing is complete, a materials cost sheet will be created for the final production aircraft, and the resulting cost shall be below $1000. 3. Endurance - The aircraft shall have an endurance total of 1 hour at cruise conditions along with two vertical takeoffs and landings. This will be broken up into two flights involving a takeoff, a 30 minute cruise, and a landing. 5 Verification: The propulsion system shall be tested at the required thrust output equivalent for 1 hour cruise and 2 takeoffs and landings. The test will be conducted for approximately 1 hour and 15 minutes on a stand in simulated flight conditions. Once the test is concluded the battery will be measured demonstrating it has a remaining capacity equal or greater than 15% 4. Airframe - The aircraft shall be constructed using the RiteWing Drak wing set. The final product shall require fewer than 20 hours of work time to be assembled. The airframe shall also be able to withstand RAP-Cat takeoff forces of up to 5G of acceleration as well as potential incidental forces up to 10G. Verification: A Drak kit shall be used as the basis of any design. By modeling potential materials to withstand the expected forces, materials with insufficient properties will be ruled out. After a material is selected, prototypes will be created of the physical components and tested under the expected loads, demonstrating the ability for airframe to withstand necessary forces. An assembly guide will be created to document the process of making a unit 5. Avionics & Sensors - The aircraft shall have all motors and actuators integrated with the flight controller and shall have all non-native sensors integrated with the avionics system. Verification: The successful integration of the sensors will be confirmed by showing that flight controller receives data from sensors, as well as demonstrating the ability to actuate all control surfaces and control individual motor thrusts. 6. Autonomy - The customer has requested the vehicle be capable of performing a fully au- tonomous takeoff and landing procedure, being able to navigate to waypoints using an au- topilot system, as well as have the capability for a pilot to manually resume control at any time. Verification: Through a series of individual tests, the system shall display the capability to control all relevant systems while mounted
Details
-
File Typepdf
-
Upload Time-
-
Content LanguagesEnglish
-
Upload UserAnonymous/Not logged-in
-
File Pages51 Page
-
File Size-