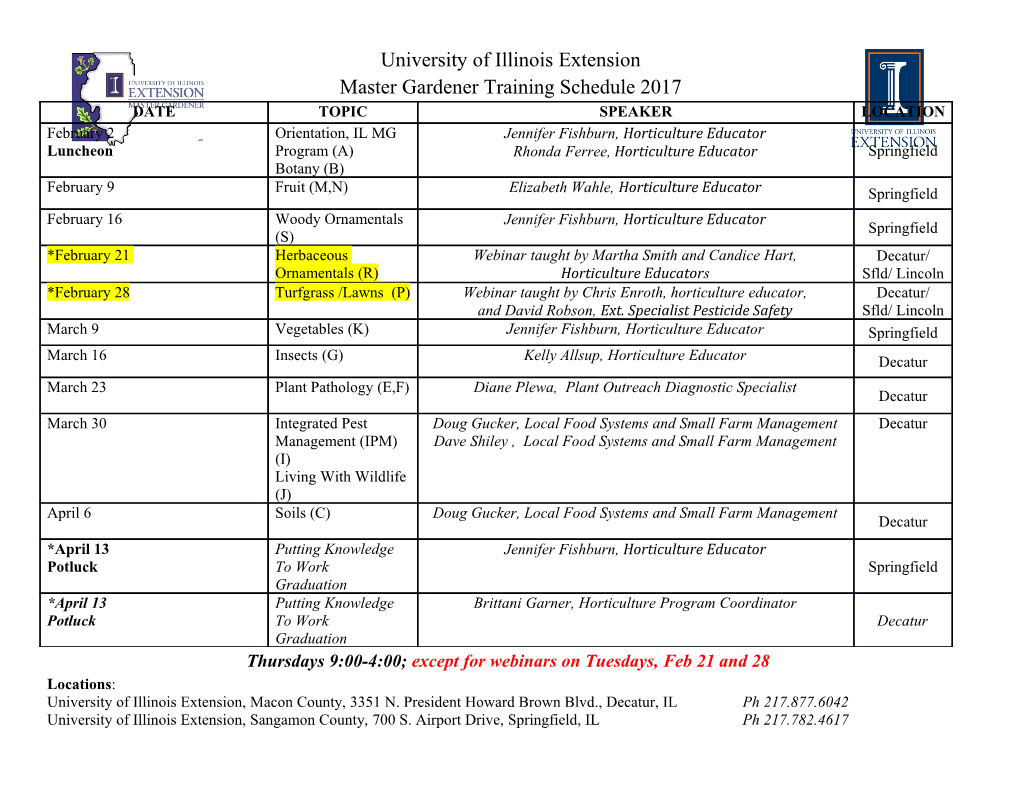
JOURNAL OF PROPULSION AND POWER Vol. 27, No. 5, September–October 2011 Reliability as an Independent Variable Applied to Liquid Rocket Engine Test Plans Richard Strunz∗ EADS Astrium, GmbH, 81663 Munich, Germany and Jeffrey W. Herrmann† University of Maryland, College Park, Maryland 20742 DOI: 10.2514/1.B34279 Manufacturers lack an adequate method to balance performance, reliability, and affordability. The reliability-as- an-independent-variable methodology is the solution proposed by expressing quantitatively the reliability trade space as ranges of a number of hardware sets and a number of hot-fire tests necessary to develop and qualify/certify a liquid rocket engine against a stated reliability requirement. Therefore, reliability-as-an-independent-variable becomes one of the key decision parameters in early tradeoff studies for liquid rocket engines because the reliability trade space directly influences the performance requirements and, as a result, the affordability. The overall solution strategy of reliability-as-an-independent-variable is based on the Bayesian statistical framework using either the planned or actual number of hot-fire tests. The planned hot-fire test results may include test failures to simulate the typical design-fail-fix-test cycles present in liquid rocket engine development programs in order to provide the schedule and cost risk impacts for early tradeoff studies. The reliability-as-an-independent-variable methodology is exemplarily applied to the actual hot-fire test history of the F-1, the space shuttle main engine, and the RS-68 liquid rocket engine, showing adequate agreement between computed results and actual flight engine reliability. Nomenclature = parameter of Poisson probability mass function Beta = Beta probability density function = probability of success of a functional node Bi = Binomial probability density function = posterior probability C = level of confidence (credibility bound) 0 = prior probability c = number of cycles = standard deviation CTD = cumulated test duration, s Subscripts FX = cumulative density function HW = number of hardware D = integration domain L = likelihood function i = functional node n = number of trials, i.e., hot-fire tests j = hot-fire test group p = probability of success med = median q = failure fraction MD = mission duration q = candidate probability density function ind MIQ = mission ignition quantity R = reliability pr = prior used in empirical Bayes estimation r = number of failures rem = remaining t = hardware life, s tot = total tp = hot-fire test proportion u = upper percentile T = median lifetime, s 50 0 = used in empirical Bayes estimation w = weighting factor x = number of successes, i.e., hot-fire tests = shape parameter I. Introduction 1, 2 = weighting factors IQUID rocket engines have always been one of the major = shape parameter affordability drivers of launch vehicles, but in the past, national fi L = median regression coef cients prestige or military requirements were dominating the decisions = integration domain for the development of a new launch vehicle. This paradigm has = parameters to be estimated changed. Performance, reliability, and affordability have equal = acceptance rate importance in the decision-making process. Europe is currently = Gamma function facing this paradigm change by defining the requirements for an expendable next generation launcher in the frame of the ESA’s Future Received 7 March 2011; revision received 25 May 2011; accepted for Launchers Preparatory Program.‡ Various launch vehicle architec- publication 9 June 2011. Copyright © 2011 by Astrium, GmbH. Published by tures were identified, ranging from a two-stage pure liquid rocket- the American Institute of Aeronautics and Astronautics, Inc., with engine-based architecture to a three-stage launch vehicle with two permission. Copies of this paper may be made for personal or internal use, on solid propellant stages and a cryogenic upper-stage engine. Although condition that the copier pay the $10.00 per-copy fee to the Copyright innovative technologies are identified in all relevant areas, the focus Clearance Center, Inc., 222 Rosewood Drive, Danvers, MA 01923; include § the code 0748-4658/11 and $10.00 in correspondence with the CCC. will be on affordability in order to develop a competitive launcher ∗Program Manager, Advanced Programs and Systems Technology; Ph.D. Student, Department of Mechanical Engineering, University of Maryland, ‡Data available at http://www.esa.int/esaMI/Launchers_Home/ College Park, Maryland 20742 (Corresponding Author). SEMNCI1PGQD_0.html [retrieved 30 October 2010]. †Associate Professor, Department of Mechanical Engineering and Institute §Data available at http://www.satnews.com/cgi-bin/story.cgi?number= for Systems Research, Martin Hall, Room 2181. 2083189758 [retrieved 30 October 2010]. 1032 STRUNZ AND HERRMANN 1033 Table 1 Qualification/certification hot-fire test attributes Test attributes F-1 J-2 RL10 LR87 LR91 SSME RS-68a Number of tests required 20 30 20 12 12 10 12 Total test duration required, s 2250 3750 4500 1992 2532 5000 1800 Number of samples 1 2 3 1 1 2 2 Hardware changes allowed Yes Yes No Yes Yes Yes Yes Fleet leader concept used No No No No No Yes No Overstress testing No No Yes No No Yes Yes aValues are based on data given in [6] Table 2 Detailed analysis of qualification/certification hot-fire test attributes Test attributes F-1 J-2 RL10 LR87 LR91 SSME RS-68 Test per hardware 20 15 6.7 12 12 5 6 Test duration per hardware, s 2250 1875 1500 1992 2532 2500 900 Duration per test per hardware, s 112.5 125.0 225.0 166.0 211.0 500.0 150.0 Mission nominal time (max), s 165 500 700 165 225 520 250 Multiple of mission nominal time, s 13.6 3.8 2.1 12.1 11.3 4.8 3.6 but at no expense of the mission success reliability and other qualification or certification tests. In short, the confidence-building launch service competitive factors compared with the current process is dominated by an expensive and schedule-impacting hot- European launch vehicle Ariane 5, as well as other operational fire test program [5]. launch vehicles. Historically, the hot-fire test program definitions experienced an The affordability of expendable launch vehicles is largely deter- evolution from a formal reliability demonstration to an aggressive mined by the development and production costs of liquid rocket cost minimization approach. Initially, liquid rocket engine devel- engines [1,2]. The major part of the development cost is spent on opment programs included a formal reliability demonstration development test hardware subjected to hot-fire tests in order to requirement (e.g., F-1 or J-2) but they were discarded in favor of sufficiently demonstrate design maturity/robustness and to qualify/ design verification specifications (DVSs) [e.g., space shuttle main certify the liquid rocket engines for a successful flight operation [3]. engine (SSME)] due to prohibitively high hot-fire test costs [2]. The The reliability-as-an-independent-variable (RAIV) methodology most recent approach is the objective-based variable test/time philos- provides the framework for specifying qualification/certification hot- ophy executed for qualifying the RS-68 liquid rocket engine that fire test attributes in terms of the number of tests, number of hardware required the least amount of hot-fire tests and accumulated hot-fire sets, and total test duration that are allocated at the component, the test duration (HFTD) [6]. subsystem, and the engine system level. The production cost is Although these different test program philosophies were applied mainly driven by performance and reliability requirements that can for various liquid rocket engines with large performance differences, be transferred into a manufacturing complexity expressed as a one may wonder why no significant trend can be seen on the number of parts, precision of the parts, and selected materials. One of qualification/certification hot-fire test attributes as listed in Table 1 the main leverages on the development cost is the chosen verification [7]. The numbers of tests required per hardware set are higher for the strategy with the objective to minimize the number of hardware sets F-1 and J-2 compared with the SSME, which were all man rated, and by testing the mission requirements on a single hardware set multiple the SSME is even reusable but subjected to different hot-fire test times but at the expense of a higher production cost because of definitions, i.e., the formal reliability demonstration versus the DVS. increased performance requirements, the selection of special mate- The J-2 and RL10 are both cryogenic upper-stage liquid rocket rials, and the need for elevated manufacturing precisions in order to engines, but hardware changes were allowed only for the J-2 and not guarantee the longer life capability. Affordability of the launch for the RL10. Table 2 may reveal the only difference among the test vehicle would be incomplete without the consideration of vehicle attributes that is linked to the propellant combination used and the operation and support, mission assurance, and range cost, as well as resulting internal loads present during engine operation; that is, more insurance fees [4]. tests and, as a consequence, a higher accumulated test duration, Therefore, the selection of the optimal choice for the settings of the which is expressed as a number of multiple mission durations, is conflicting trade spaces for performance, reliability, and affordability placed on hardware sets for the propellant combination liquid oxygen becomes a multiple-criterion decision-making (MCDM) problem. (LOX)/liquid hydrogen (two- to fivefold) compared with the The trade spaces for affordability and performance are generated propellant combination LOX/kerosene or hypergolic storable pro- with parametric cost models and thermodynamic cycle codes. pellants (more than tenfold). This identified difference may be biased However, the main shortcoming of the current MCDM solutions is by the lack of visibility on the extent of the prior component level or the lack of an adequate modeling technique for the reliability trade the development engine test history.
Details
-
File Typepdf
-
Upload Time-
-
Content LanguagesEnglish
-
Upload UserAnonymous/Not logged-in
-
File Pages13 Page
-
File Size-