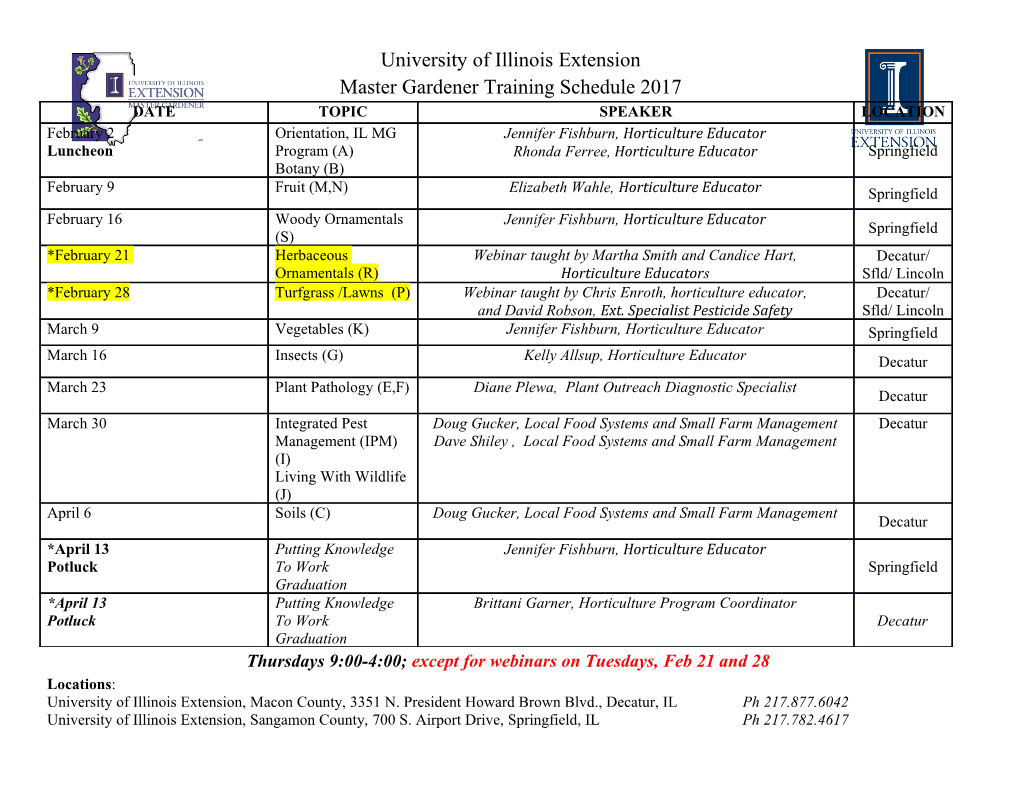
The Kraft Recovery Process Honghi Tran Pulp & Paper Centre University of Toronto Toronto, Canada Tappi Kraft Recovery Short Course St. Petersburg, Florida, January 7-10, 2008 Kraft Pulping Process Most important chemical pulping process Global kraft pulp production: 130 million metric tons/year (67% of total) Advantages High pulp strength Versatility - ability to handle a wide range of wood species Favorable economics - High chemical recovery efficiency (96 - 98%) 1 Kraft Pulping Process Fibre Lignin Fibre + White Liquor (NaOH + Na2S) Wood 155oC 900 kPa Black Liquor A 1000 t/d Kraft Pulp Mill produces 1500 t/d BL d.s. 8000 ~ 10,000 t/d weak black liquor 3000 2500 Chemicals Chemicals 2000 Black t/d Dissolved 1500 Liquor Organics 1000 Wood 500 Fibre Pulp 0 2 Kraft Recovery Process A Closed Cycle Process with 3 Main Functions: Eliminate the waste material (black liquor) Pulping Recover pulping chemicals (NaOH and NaOH, Na, S, Organics Na2S Na2S) Recovery Generate steam and power Steam & Power Kraft Recovery Process Wood PulpingDigester Pulp WashingWashing Weak Black Liquor 15 – 18% ds 3 Kraft Recovery Process Wood PulpingDigester Pulp WashingWashing Weak Black Liquor Evaporators Ash Heavy Black Liquor Recovery 65 – 85% d.s. Boiler Makeup Na2SO4 As-Fired Black Liquor Composition (750 liquor samples; All Wood Species) Typical Range Solids content, % 72 65 – 85 HHV, MJ/kg 13.9 12.5 – 15.5 C, wt% d.s. 33.9 30 – 40 H 3.4 3.2 – 4.0 O 35.8 34 – 38 Na 19.6 17 – 22 S 4.6 3.6 – 5.6 Composition K 2.0 1 – 3 Cl 0.5 0.1 – 4 4 Smelt Formation 0.4 kg smelt /kg BL d.s. C H Na2CO3 O 2/3 Na 1/3 Na2S (Reducing Conditions) S K Others: Cl Na2SO4, NaCl K2CO3, K2S, K2SO4, KCl Smelt Spout Smelt Na2CO3 + Na2S 5 Kraft Recovery Process Wood PulpingDigester Pulp NaOH WashingWashing Weak Black Liquor Evaporators Na2CO3 Green Water Liquor Heavy Black Liquor Na2S Recovery Smelt Boiler Kraft Recovery Process Wood Lime Kiln PulpingDigester White Pulp Liquor WashingWashing Lime Lime Mud Weak Black Liquor CausticizingCausticizing Plant Plant Evaporators Green Water Liquor Heavy Black Liquor Recovery Smelt Boiler 6 Na and Ca Cycles Makeup Wood Lime Kiln PulpingDigester NaOH Pulp CaO WashingWashing Na2S CaCO3 Calcium Na, S CausticizingCausticizing Sodium Plant Evaporators Na2CO3 Water Na, S Na2S Recovery Makeup Boiler Sulfur Cycles SO2 Fuel Wood Lime Kiln PulpingDigester S Pulp NCG/ CaSO Na S 4 2 SOG WashingWashing Na2SO4 S Loss/ Scrubbing/ S Incineration CausticizingCausticizing Recovery Plant NCG/SOG Evaporators Na S SO 2 Water 2 Na SO 2 4 S Recovery S Makeup Boiler 7 Makeup Chemicals (Na, S and Ca) Sodium 8 to 16 kg/ADt as Na2O NaOH, Na2CO3, Na2SO4 (salt cake) Organic Na compounds (acetate, etc.) Sulfur 1.4 to 4 kg/ADt as S Na2SO4, NaSH, H2SO4, Na3H(SO4)2, Elemental S S in lime kiln fuels Calcium 4 to 8 kg/ADt as CaO Purchased lime Lime rock Main Sources of NPEs (Non Process Elements) Wood: Si, Al, Cl, K, Mg, Mn, P, Fe, Ni, Cr, etc. Makeup caustic: Cl Additive: Si, Mg Makeup lime: Si, Al, Mg, P, Fe Refractory bricks: Si, Al Corrosion products: Fe, Ni, Cr 8 Types of NPEs Form soluble compounds: Cl, K Be with the liquor Accumulate Form partially soluble compounds: Si, Al Precipitate under appropriate conditions Form insoluble compounds: Most other elements Do not accumulate Be removed from the recovery system with grits, dregs and lime mud/dust Energy Recovery 1.9 GJ/ADt Wood Loss Lime Kiln PulpingDigester Pulp White WashingWashing Liquor Lime Lime Mud Power LP Steam Weak CausticizingCausticizing Black Liquor Plant PulpingTurbine Plant Evaporators Green HP Steam Liquor Heavy Black Liquor Recovery 22 GJ/ADt Smelt Boiler Loss 1 GJ/t = 0.860 MM Btu/ton 9 Recovery Boiler Energy Production Steam Typically 3.5 kg/kg BLds May vary from 2.5 to 3.8 kg/kg BLds Power A 1000 t/d kraft pulp mill may generate 25 to 35 MW of electricity from black liquor combustion Technological Advancements Evaporators/concentrators Falling film, plate-type High solids (75 to 85%) Recovery boilers High solids firing High steam temperature/pressure High efficiency Recaust and lime kilns Pressurized filters Lime mud dryer 10 Recovery Boiler Firing Capacity 6000 11 million lbs/d 5000 Maximum 4000 3000 2000 Capacity (t ds/d) (t Capacity 1000 0 1930 1940 1950 1960 1970 1980 1990 2000 2010 Year Vakkilainen (2006) Maximum Recovery Boiler Steam Temperature and Pressure 600 180 Temperature 960 F 500 150 1813 psi Pressure 400 120 300 90 200 60 100 30 Steam Pressure (bar) Steam temperature (C) 0 0 1930 1940 1950 1960 1970 1980 1990 2000 2010 Year Vakkilainen (2006) 11 Benefits of High Solids Firing Significantly increases steam generation Improves combustion stability Lower TRS and SO2 emissions Less boiler fouling and plugging Increase capacity in existing units. Operating Problems Many problems can occur They can be: Equipment related Process related Liquor chemistry related 12 Common Operating Problems Evaporators Lime kiln and Recausticizing Scaling High kiln fuel consumption Corrosion Ring formation High steam consumption Refractory damage Low solids in product liquor Chain damage Recovery Boilers NCG/SOG burning Fouling and plugging Gaseous/particulate emissions Tube corrosion and cracking Poor lime quality/availability Spout corrosion and cracking Overliming/underliming Low steam production Poor causticizing efficiency Poor sootblowing efficiency Poor mud settling and low solids Poor water circulation Clarifier corrosion Smelt-water emergencies Process control Gaseous/particulate emissions Liquor Cycle Tube damage by falling deposits NPE Accumulation (Cl and K) Unstable combustion/blackouts High deadload “Jelly roll” smelt/smelt run-off Chemical makeup Low reduction efficiency Na and S imbalance High dregs in smelt High sulphidity operation Problems Can Be Costly Recovery Boiler Plugging 0.8 - 1.5 million USD Recovery Boiler Tube Corrosion/Cracking 5 - 20 million USD Lime kiln ringing 10,000 - 500,000 USD Environmental impacts ??? USD 13 This Course is Designed to Help You To: Understand process principles Understand possible causes of problems and find solutions to them Recognize potential problems that may occur and devise means to prevent them from occurring Challenges Increased economy Increase production capacity Lower operating costs Increased environmental protection Increase recovery efficiency Reduce emissions and discharge New technologies, sensors and control strategies Process simplification 14.
Details
-
File Typepdf
-
Upload Time-
-
Content LanguagesEnglish
-
Upload UserAnonymous/Not logged-in
-
File Pages14 Page
-
File Size-