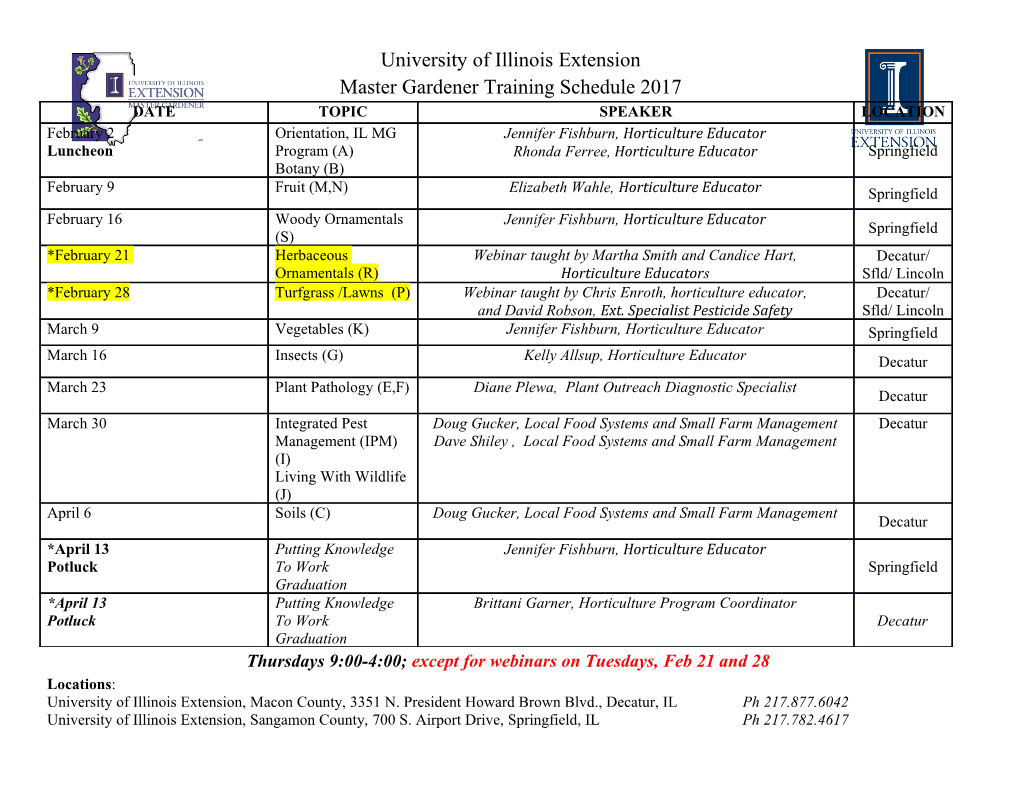
FUNCTION BLOCK ALGORITHMS FOR ADAPTIVE ROBOTIC CONTROL Bachelor Degree Project in Automation Engineering Bachelor Level 30 ECTS Spring term 2014 Lander Egaña Iztueta Javier Roda Martínez Supervisors: Göran Adamson Examiner: Jan Oscarsson Certificate of Originality I. Certificate of Originality This document is submitted by Lander Egaña Iztueta and Javier Roda Martínez to the University of Skövde as a dissertation towards the Bachelor degree (BSc) in Automation Engineering, by examination in the School of Technology and Society. We here by certify that all material in this dissertation which is not ours own work has been identified and that no work is included for which a degree has already been conferred on us. Skövde, Sweden, 12th April, 2014 Signature: Lander Egaña Iztueta & Javier Roda Martínez III Quote II. Quote “It is paradoxical, yet true, to say, that the more we know, the more ignorant we become in the absolute sense, for it is only through enlightenment that we become conscious of our limitations. Precisely one of the most gratifying results of intellectual evolution is the continuous opening up of new and greater prospects.” Nikola Tesla IV Abstract III. Abstract The purpose of this project is the creation of an adaptive Function Block control system, and the implementation of Artificial Intelligence integrated within the Function Block control system, using IEC 61499 standard to control an ABB 6-axis virtual robot, simulated in the software RobotStudio. To develop these objectives, we studied a lot of necessary concepts and how to use three different softwares. To learn how to use the softwares, some tests were carried out. RobotStudio is a program developed by ABB Robotics Company where an ABB robot and a station are simulated. There, we designed and created a virtual assembly cell with the virtual IRB140 robot and the necessary pieces to simulate the system. To control the robot and the direct access to the different tools of RobotStudio, it is necessary to use an application programming interface (API) developed by ABB Robotics Company. C sharp (C#) language is used to program using the API, but this language is not supported by the Function Block programming software nxtStudio. Because of this, we used VisualStudio software. In this software, we use the API libraries to start and stop the robot and load a RAPID file in the controller. In a RAPID file the instructions that the robot must follow are written. So, we had to learn about how to program in C# language and how to use VisualStudio software. Also, to learn about IEC 61499 standard it was necessary to read some books. This standard determines how an application should be programmed through function blocks. A function block is a unit of program with a certain functionality which contains data and variables that can be manipulated in the same function block by several algorithms. To program in this standard we learnt how to use nxtStudio software, consuming a lot of time because the program is quite complex and it is not much used in the industrial world yet. Some tests were performed to learn different programing skills in this standard, such as how to use UDP communication protocol and how to program interfaces. Learning UDP communication was really useful because it is necessary for communication between nxtStudio and other programs, and also learning how to use interfaces to let the user access the program. Once we had learnt about how to use and program the different softwares and languages, we began to program the project. Then, we had some troubles with nxtStudio because strings longer than fourteen characters cannot be used here. So, a motion alarm was developed in VisualStudio program. And another important limitation of nxtStudio is that C++ language cannot be used. Therefore, the creation of an Artificial Intelligence system was not possible. So, we created a Function Block control system. This system is a logistical system realised through loops, conditions and counters. All this makes the robot more adaptive. As the AI could not be carried out because of the different limitations, we theoretically designed the AI system. It will be possible to implement the AI when the limitations and the problems are solved. V Acknowledgments IV. Acknowledgments Thanks to the help of some people, we were able to perform this project. Through the help, we did not waste too much time looking for solutions for some errors, learning a lot of concepts and programs and getting useful information to explain in the report and structuring it well. First, thanks to our supervisor Göran Adamson, who guided us during the project. He helped us with the report and the different concepts of the project. The first contact with the nxtStudio program was not too hard thanks to Aimar Cordero Garcia who spent more than three weeks teaching us the software. This program is new and it is really difficult to understand in the beginning. Also, thanks to Tom Ekblom for helping us in how to program C#, in the VisualStudio software. Last but not least, thanks to our universities and to University of Skövde for giving us the opportunity of spending one year in Sweden. Also, thanks to our families and our friends. VI Table of Contents V. Table of Contents I. Certificate of Originality ................................................................................................................ III II. Quote ............................................................................................................................................. IV III. Abstract ........................................................................................................................................... V IV. Acknowledgments .......................................................................................................................... VI V. Table of Contents .......................................................................................................................... VII VI. List of figures .................................................................................................................................. IX VII. List of equations ............................................................................................................................. XI VIII. List of abbreviations ...................................................................................................................... XII 1. Introduction .................................................................................................................................... 1 1.1. Motivation ............................................................................................................................... 2 1.2. Aims and objectives ................................................................................................................ 3 1.3. Project planning ...................................................................................................................... 4 1.4. Methodology ........................................................................................................................... 5 2. Sustainability ................................................................................................................................... 6 3. Literature review ............................................................................................................................. 7 3.1. Simulation ............................................................................................................................... 7 3.1.1. Simulation as an appropriate tool .................................................................................. 7 3.2. Industrial Robots ..................................................................................................................... 8 3.2.1. History ............................................................................................................................. 8 3.2.2. Definition of robot .......................................................................................................... 9 3.2.3. Advantages of using Industrial Robots............................................................................ 9 3.2.4. Classification of Industrial Robots ................................................................................... 9 3.2.5. Types of joint ................................................................................................................. 10 3.2.6. Articulated Industrial Robot .......................................................................................... 10 3.3. RobotStudio .......................................................................................................................... 12 3.3.1. What is RobotStudio ..................................................................................................... 12 3.3.2. Hardware concepts ....................................................................................................... 13 3.3.3. RAPID concepts ............................................................................................................. 13 3.3.4. Programming concepts ................................................................................................. 14 3.3.5. Simulating programs ..................................................................................................... 14 3.3.6. Handle I/O, working online ..........................................................................................
Details
-
File Typepdf
-
Upload Time-
-
Content LanguagesEnglish
-
Upload UserAnonymous/Not logged-in
-
File Pages146 Page
-
File Size-