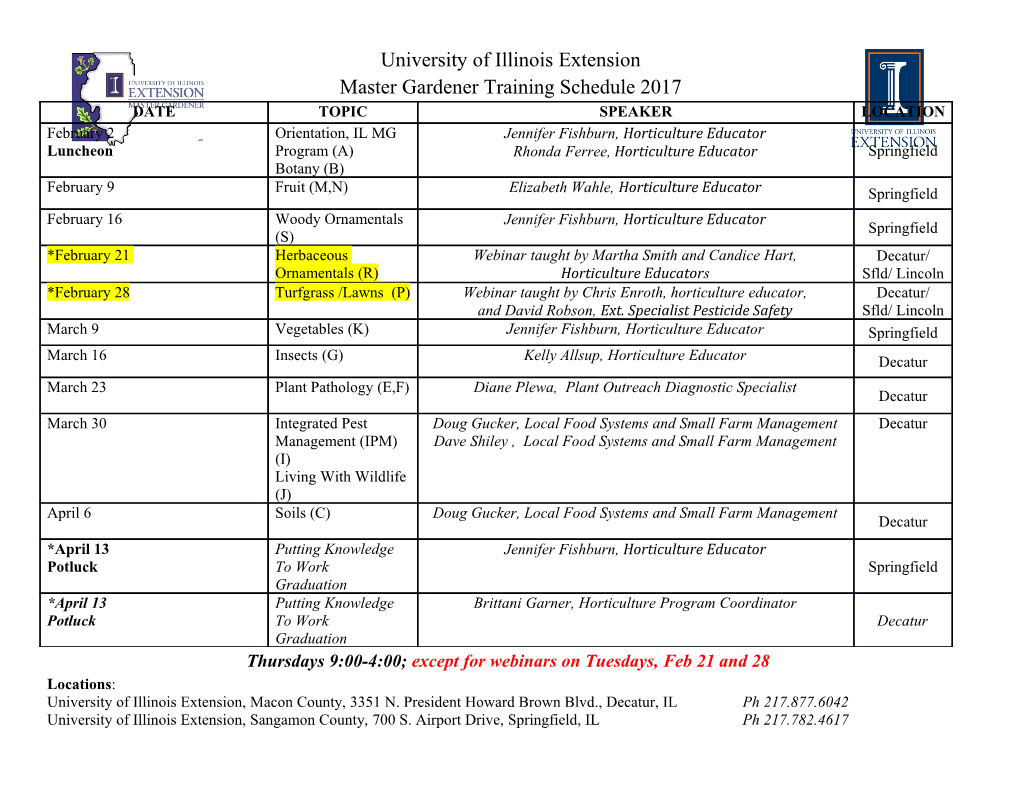
Sådhanå (2018) 43:168 Ó Indian Academy of Sciences https://doi.org/10.1007/s12046-018-0928-5Sadhana(0123456789().,-volV)FT3](0123456789().,-volV) Developments of mathematical models for prediction of tensile properties of dissimilar AA6061-T6 to Cu welds prepared by friction stir welding process using Zn interlayer SHAILESH N PANDYA* and JYOTI V MENGHANI Department of Mechanical Engineering, S. V. National Institute of Technology, Surat 395 007, India e-mail: [email protected] MS received 5 September 2017; revised 14 April 2018; accepted 19 April 2018; published online 31 August 2018 Abstract. Amount of intermetallics formed at the weld interface in dissimilar friction stir welding may be reduced by use of suitable interlayer materials such as Zn. In the present investigation, mathematical models have been developed for prediction of tensile properties of dissimilar AA6061-T6 to pure Cu welds prepared by friction stir welding process with Zn interlayer. Experiments were planned as per Box–Behnken design of response surface methodology. Three-factor, three-level Box–Behnken design with 15 runs was employed. Three process parameters: tool rotation speed (710, 1000 and 1400 rpm), tool travel speed (28, 56 and 80 mm/min) and tool pin offset (?0.5, ?1.0 and ?1.5 mm towards AA6061-T6 sheet) were considered. Lacks of fit for the developed models were assessed using analysis of variance (ANOVA). Validities of the developed models were checked by conducting confirmation runs. Predicted and experimental results of confirmation runs were found in reasonable agreements. Microstructural characterization revealed typical microstructure com- posed of intercalation of base metals. It was observed by X-ray diffraction analysis that use of Zn interlayer coupled with tool offset of ?1.0 and ?1.5 resulted in elimination of intermetallics of Al–Cu system at the weld interface, improving dissimilar weld quality. Keywords. Friction stir welding; dissimilar; response surface methodology; interlayer; tensile strength. 1. Introduction welding processes for joining dissimilar materials is nor- mally not desirable due to several melting- and solidifica- Friction stir welding process is a solid-state joining tech- tion-related issues [7] such as differences in melting points nique [1] invented at The Welding Institute (TWI), London, and thermal conductivities of base metals, differences in in 1991. The process has been successfully applied for coefficients of thermal expansion of base metals, higher joining similar metal joints of many ferrous and non-ferrous residual stresses, formation of brittle intermetallics, etc. metals [2, 3] as well as dissimilar metal joints [4]. In the Friction stir welding process is a better technique for friction stir welding process, the welded joint is formed welding dissimilar metals. Due to solid-state nature of the with typically wrought microstructure [1] by heating and friction stir welding process, welded joints prepared using stirring of softened base metal sheets beneath a rotating the process are free from melting- and solidification-related non-consumable tool. Heating takes place due to plastic defects. deformation and frictional contact between the rotating tool Microstructure and mechanical properties of Al–Cu dis- and base metal sheets. Subsequently, the weld is formed by similar welds prepared by friction stir welding have been a stirring and mixing of base materials by the rotating tool matter of research interest in the last decade. Formation of pin. brittle intermetallics is one of the common observations in Joining of dissimilar metals is required in numerous microstructure of dissimilar Al–Cu friction stir welds. engineering applications. Pure Cu is widely utilized in Muthu and Jayabalan [8] investigated effects of tool travel engineering applications because of its higher electrical and speed on 6-mm-thick dissimilar AA1100-H14 to pure Cu thermal conductivity [5]. Aluminium alloys are utilized for butt joints prepared by friction stir welding process. They numerous applications because of their higher strength to reported formation of Al2Cu, AlCu and Al4Cu9 inter- weight ratio [6]. Therefore, there are many potential metallics. The higher tensile strength of the strongest weld applications of dissimilar Al–Cu welds. Use of fusion was attributed to thin and continuous nano-sized inter- metallic layer and strengthening due to dispersion of Cu particles within Al matrix in stir zone. Xue et al [9] also *For correspondence 1 168 Page 2 of 18 Sådhanå (2018) 43:168 reported strengthening due to formation of composite-type offset) eliminates formation of brittle intermetallics in structure along with formation of thin interlayer (*1 lm) friction stir welding of dissimilar Al–Cu welds. Sahu et al for dissimilar AA1060 to commercially pure Cu welds. [22] varied tool pin offset and observed that sound AA1050 Genevois et al [10] also attributed formation of defect-free to pure Cu welds are obtained when tool pin offset is set to dissimilar Al–Cu joints to formation of very thin interlayer ?1.5 mm. If the tool is set offset towards retreating side composed of intermetallics – Al2Cu and Al4Cu9. Bisadi (RS) sheet, then tool pin offset is denoted with a ?ve sign, et al [11] investigated effects of tool travel speed and tool while if the tool pin offset is set towards advancing side rotation speed on dissimilar AA5083 to pure Cu sheets in material then it is denoted with a -ve sign as per common lap configuration. They observed low strength with fracture convention. Improvement in tensile properties of dissimilar location for lap shear testing specimen on advancing side. Al–Cu welds due to use of tool pin offset in friction stir The lower strength of the weld was attributed to hooking welding is also reported by Yaduwanshi et al [23], Galvao defects and formation of brittle intermetallics – Al2Cu and et al [24] and Xue et al [25]. Al4Cu9. Mehta and Badheka [12] observed highly brittle There have been very few studies reported on friction stir welds of dissimilar AA6061-T651 to pure Cu sheets pre- butt welding of dissimilar Al–Cu welds using design of pared by friction stir welding process. They attributed experiments (DOE). Recently, Sahu et al [26] optimized brittleness of the weld to the presence of hard intermetallics friction stir welding process parameters for welding of of Al–Cu system. Geometry of friction stir welding tool pin dissimilar Al–Cu sheets using systematic experiments as also affects formation of Al–Cu intermetallics. Muthu and per the Taguchi method of DOE. DOE is a good technique Jayabalan [13] investigated effects of three different types to collect and analyse experimental data. DOE is also of tool pin profiles on microstructure and mechanical helpful for optimization of process parameters [27]. properties of dissimilar Al–Cu friction stir welds. It was Response surface methodology is a type of DOE technique. observed that pin profiles with threads and whorls on If the objective of the experimental study is to investigate peripheral surface result into pulsating material flow, individual, interaction and quadratic effects of process increasing transfer of higher Cu content in stir zone. Higher parameters on the response variable, response surface Cu content increases chances of formation of brittle inter- methodology is a good method. Response surface metallics. Higher strength was observed for the weld pre- methodology is useful to develop and verify the mathe- pared using plain taper profile as compared with strengths matical model correlating one or more than one response of welds prepared using tool pin with whorls and threads on variables and experimental process parameters [28]. For peripheral surface. It is observed that when there is for- development of mathematical model, initially the experi- mation of thick intermetallic intermediate layer at the Al– mental data are collected by conducting experiments as per Cu interface, the joint strength of dissimilar Al–Cu welds is response surface methodology. Thereafter, a first- or sec- low. However, stronger welds are produced when there is a ond-order regression equation is developed [29]. thin intermetallic intermediate layer. Thus, nature, form and Box and Behnken [30] developed Box–Behnken DOE, amount of intermetallics formed at the Al–Cu interface which is a sub-type of response surface methodology. Box– affect the tensile strength of the Al–Cu dissimilar friction Behnken designs are rotatable through design space. The stir welds. Box–Behnken design for three factors is divided into three It is necessary to control the amount of these inter- blocks. In each block, one factor is held fixed at interme- metallics to enhance the tensile properties of the dissimilar diate level (coded value: 0) while other two factors are Al–Cu welds. Ouyang et al [14] suggested insertion of any varied in all possible combinations of their high (coded type of interlayer material between base metal sheets to value: ?1) and low (coded value: -1) levels. Thus, they minimize amount of brittle intermetallics. Use of interlayer make 394 = 12 runs. Including three repeat runs for the to control growth of intermetallics in dissimilar metal central points (for which all factors are kept at their inter- welding has been reported in the literature for many fusion mediate levels; coded value: 0) makes a total of 15 runs [15–17] and non-fusion welding [18, 19] processes. For [31]. Applications of response surface methodology for dissimilar friction stir welding of Al–Cu welds, Kuang et al investigating effects of friction stir welding process [20] used 0.2-mm-thick Zn foil as interlayer material for parameters on tensile properties or other responses have joining of 2-mm-thick sheets in lap configuration. Sahu been reported in the literature [32–35]. Ghetiya and Patel et al [21] investigated effects of Ni, Ti and Zn foil as [32] developed a mathematical model for prediction of interlayer on dissimilar AA1050 to pure Cu sheets welded tensile strength of AA2014-T4 immersed friction stir welds by friction stir welding in butt configuration.
Details
-
File Typepdf
-
Upload Time-
-
Content LanguagesEnglish
-
Upload UserAnonymous/Not logged-in
-
File Pages18 Page
-
File Size-