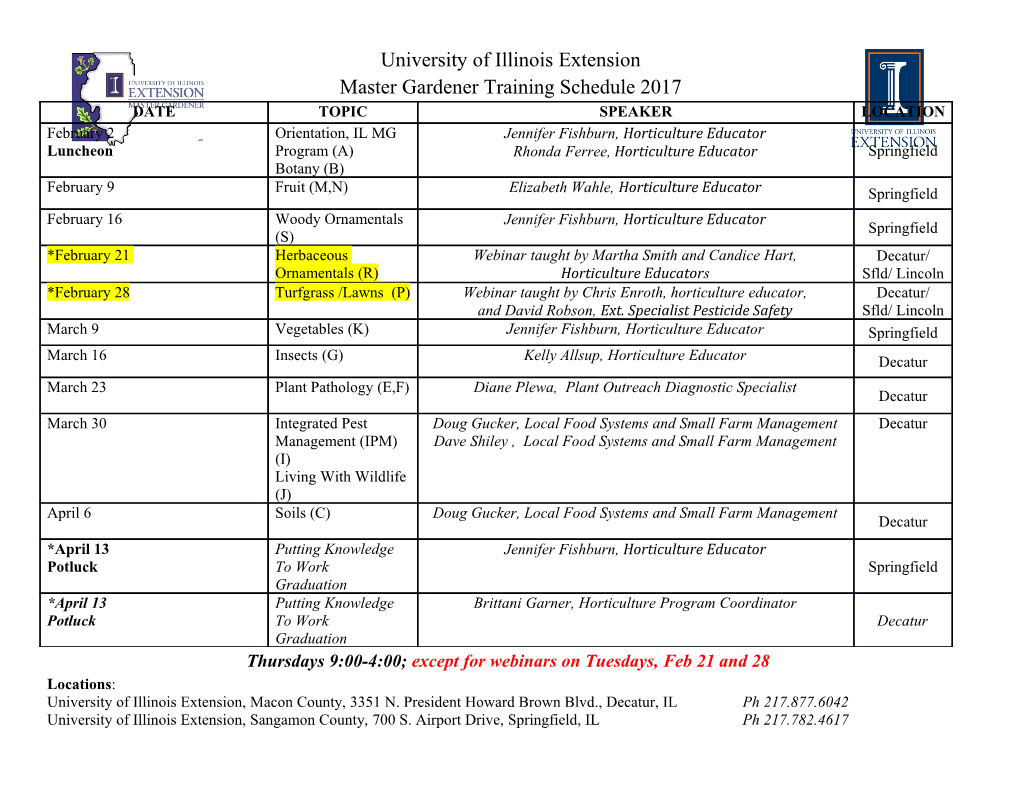
Draft Document Description of the Printing Processes Technical Annex1 10 November 2003 Technical Annex 1, Printing processes 1 10 November 2003 DRAFT 1 Overview 3 2 Offset (lithography) 4 2.1 Printing materials and products 6 2.2 Process description 6 2.3 Chemicals 15 2.4 Waste 19 2.5 Environmental burden 22 2.6 Potential for improvements 26 2.7 Expectations for the future 30 3 Flexography 33 3.1 Printing materials and products 34 3.2 Process description 34 3.3 Chemicals 37 3.4 Waste 39 3.5 Environmental burden 40 3.6 Potential for improvements 42 3.7 Expectations for the future 44 4 Gravure 45 4.1 Printing materials and products 46 4.2 Process description 46 4.3 Chemicals 48 4.4 Waste 51 4.5 Environmental burden 52 4.6 Potential for improvements 54 4.7 Expectations for the future 55 5 Screen 56 5.1 Printing materials and products 57 5.2 Process description 57 5.3 Chemicals 59 5.4 Waste 61 5.5 Environmental burden 63 5.6 Potential for improvements 64 5.7 Expectations for the future 65 6 Letterpress 66 6.1 Printing materials and products 66 6.2 Process description 66 6.3 Chemicals 68 6.4 Environmental burden 71 6.5 Potential for improvements 73 6.6 Expectations for the future 74 7 Digital printing 75 7.1 Printing materials and products 75 7.2 Process description 75 7.3 Chemicals 77 7.4 Waste 78 7.5 Environmental burden 78 7.6 Potential for improvements 79 7.7 Expectations for the future 79 Technical Annex 1, Printing processes 2 10 November 2003 DRAFT 8 Post-press or finishing 80 8.1 Finishing products 80 8.2 Process description 80 8.3 Chemicals 83 8.4 Waste 84 8.5 Environmental burden 85 8.6 Potential for improvements 86 8.7 Expectations for the future 87 9 Bibliography 88 Technical Annex 1, Printing processes 3 10 November 2003 DRAFT Description of printing processes 1 Overview The printing industry is a very diversified industry, owing to the multiplicity of printing processes utilized, the size of the plants, and the products it produces. Lithography (offset), flexography, gravure, and screen are the major conventional machine printing processes. Letterpress was the earliest form of printing but has been superseded by offset. Today letterpress finds only limited applications in simple text, such as business cards. Electronic/digital printing processes have developed during the last fifteen years. Electronic/digital printing include xerography and laser printing; ink jet printing; magnetography; thermal printing; ion deposition printing; and direct charge deposition printing. Lithography, gravure, and flexography are the dominant processes; lithography is the most widely used printing process today. The various electronic/digital printing processes are gradually becoming a major force in the industry and have to a great extent created new market opportunities and niches rather than being a replacement for conventional printing processes. Conventional printing processes can be divided into three major steps: prepress, press, and postpress, figure 1. All prepress operations follow the same initial stages of converting the original matter, which can be of either conventional or digital origin, into an image carrier such as a plate, cylinder or stencil. The image carrier are used in the printing processes to transfer the printing ink onto the substrate (paper, board, plastic, etc.). Press refers to actual printing operations. Postpress primarily involves the assembly of printing materials, and consists of binding and finishing operations. Computer Prepress Image carrier Printing Finishing “digital files” Photography preparation Finished product Figure 1 Individual graphic companies may incorporate a whole series of processes, from original pattern to finished product, but many specialise in, for example, printing, reproduction, or bookbinding. A single printing plant can also utilise several different printing processes, such as offset and screen, or different types of offset, such as sheet-fed offset and heat-set web offset. Many printing plants have now also complemented their equipment with different kinds of digital presses. The choice of printing process is usually based upon technical and commercial considerations, such as length of run, required print quality, choice of substrate, speed of printing and drying, and the end use of the product. A wide variety of products are produced and printed on many different types of materials. Examples of products that can be produced are newspapers, magazines, books, greeting cards, calendars, brochures, Technical Annex 1, Printing processes 4 10 November 2003 DRAFT leaflets, stamps, labels, business forms, passports, cheques, tickets, envelopes, paper or plastic bags, food packaging, gift-wrap paper, cans, decals, T-shirts, and wall coverings. Depending on the printing process, the substrates for printing can be different types of papers, coated and uncoated boards, corrugated boards, plastics, metal, ceramic, glass, cork, wood, and fabrics. A printed matter is made up of differently-sized dots (screened), which are created with a special camera or with the help of a computer (scanner). Colour pictures are separated and a picture is made for each colour: yellow, blue, red, and black. These colours are always used when printing a colour picture, and are printed separately on top of each other. The four primary colours are often called process colours, and a colour scale called the European Scale is principally used. To create spot colours, e.g., a special colour for a logotype, a different colour scale, named PMS (Pantone Matching System), is used. The PMS-scale consists of thirteen primary colours, but by mixing these before printing, a large number of colours can be created. In the following description of the different printing processes, only the most typical inks are mentioned. For every printing process there are many varieties of printing inks. There are many factors that affect the ink formulation, such as the type of printing press, printing speed, type of substrate, or the intended use of the printed product (food wrappers, wallpaper, etc.). 2 Offset (lithography) Lithography, a planographic process, is today usually referred to as “offset.” Offset printing dominates the printing industry both in Europe and the U.S., accounting for as much as 50 percent of all conventionally printed materials. However, the market for offset printing is decreasing. Offset printing is suited for printing both text and illustrations in short to medium length runs of up to 1 million impressions. Offset is a planographic printing method, meaning that the printing and the non- printing areas are on the same plane, and the substrate is pressed into contact with the whole surface. Offset works on the principle that ink and water do not mix. Images on the plates are first dampened with water and then with ink. The ink adheres to the image area, the water to the non-image area. Then the image is transferred to a rubber blanket and from the rubber blanket to paper. That’s why the process is called “offset” – the image does not go directly to the paper from the plates, figure 2. Figure 2 There are three basic offset press designs: unit-design, common impression cylinder design, and blanket to blanket design. Technical Annex 1, Printing processes 5 10 November 2003 DRAFT The unit-design press consists of a plate cylinder, a rubber blanket cylinder, and an impression cylinder together with the inking and damping rollers. The simplest offset press consists of only one unit, a single- colour unit press. A common impression cylinder press or satellite machine consists of two ore more sets of plate and rubber blanket cylinders sharing a common impression cylinder. Two or more colours can be printed at a single station. Most sheet-fed presses are built on the blanket-to-impression principle, and web-fed machines most often are built on the blanket-to-blanket principle. Sheet-fed printing presses are available from single-colour to multicolour configurations, and web-fed presses are usually available as four-colours or more. Most of the presses consist of four printing units, one printing unit for each primary colour for printing colour pictures. In a multicolour sheet-fed press the sheet travels on transfer cylinders or chain grippers between the units. Depending on the type of substrate or the products printed there are three types of offset printing sub processes: sheet-fed, heat-set web, and cold-set web offset, figure 3. Computer ”digital files" Film processing Proofing Digital proofing Film assembly Platemaking Sheetfed Heatset Coldset offset weboffset weboffset printing printing printing cleaning cleaning cleaning Drying Figure 3 Finishing On sheet-fed presses the substrate is fed into the press one sheet at a time while web presses feed paper continuously from a large roll, which is later cut to size. Finished product Technical Annex 1, Printing processes 6 10 November 2003 DRAFT Most sheet-fed presses can print only one side of the sheet at a time but there are presses that can print on both sides simultaneously. Web-offset presses print on both sides of the paper at the same time. Web-fed presses are faster than sheet-fed presses and are better suited for long-run works. A variation of the offset process is waterless offset printing, where printing is done without water. The plate for waterless offset has an ink repellent silicone rubber layer on top of a ink receptive photopolymer coating surface. Printing presses for waterless offset normally must be equipped with cooling systems. Waterless offset today appears mostly in the sheet-fed offset process. The digital presses which do not have variable printing are based on waterless offset technology, figure 4. Figure 4 2.1 Printing materials and products The most common products are newspapers, magazines, brochures, books, catalogues, posters, leaflets, cartons, envelopes, and forms.
Details
-
File Typepdf
-
Upload Time-
-
Content LanguagesEnglish
-
Upload UserAnonymous/Not logged-in
-
File Pages91 Page
-
File Size-