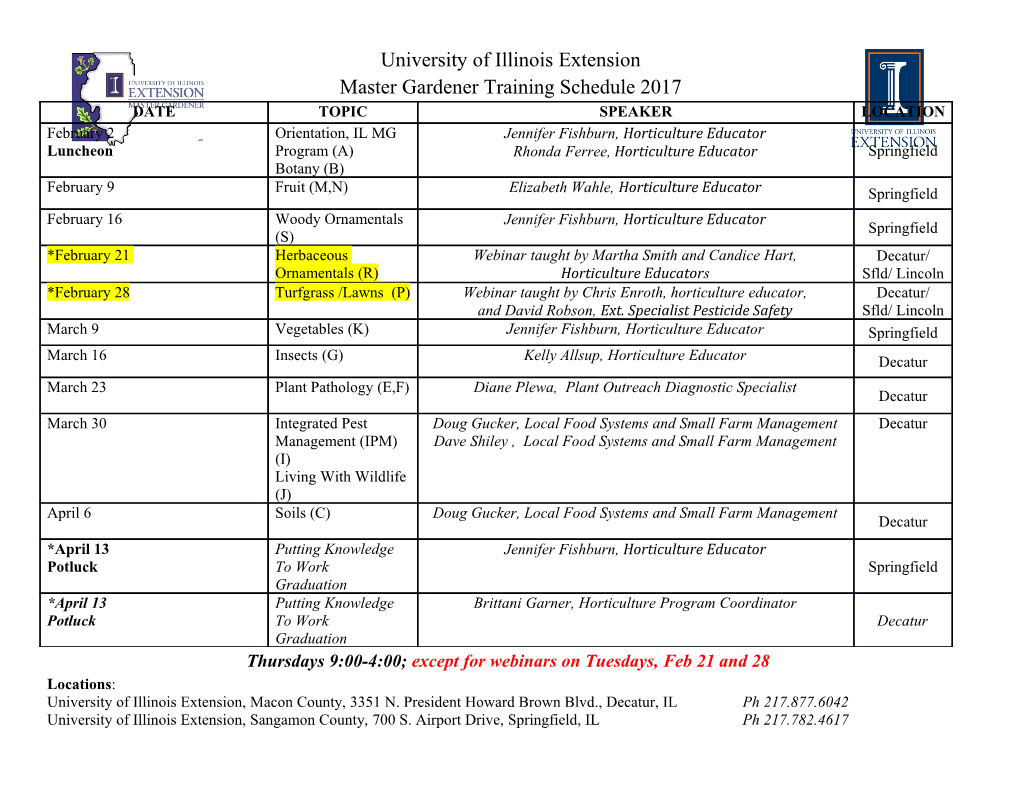
ULTIMET® alloy Principal Features STELLITE alloy-like wear resistance and HASTELLOY alloy-like corrosion resistance in a single, highly weldable material ULTIMET® alloy (UNS R31233) provides a unique blend of properties. From a wear stand- point, it behaves like the STELLITE® alloys with lower carbon contents. From a corrosion standpoint, it possesses many of the attributes of the C-type and G-type HASTELLOY® ma- terials, in particular outstanding resistance to chloride-induced pitting and crevice corrosion. Its mechanical and welding characteristics are much closer to those of the HASTELLOY® alloys than those of the STELLITE® alloys, whose low ductilities can be problematic. While ULTIMET® alloy has been used successfully in the form of wrought products, its larg- est applications have involved weld overlays, made with solid wire consumables and arc- welding processes such as GMAW (MIG) and GTAW (TIG). Nominal Composition Weight % Cobalt: 54 Balance Chromium: 26 Nickel: 9 Molybdenum: 5 Iron: 3 Tungsten: 2 Manganese: 0.8 Silicon: 0.3 Nitrogen: 0.08 Carbon: 0.06 H-2082E © 2020 Haynes International ISO-Corrosion Diagrams Each of these iso-corrosion diagrams was constructed using numerous corrosion rate values, generated at different acid concentrations and temperatures.The blue line repre- sents those combinations of acid concentration and temperature at which a corrosion rate of 0.1 mm/y (4 mils per year) is expected, based on laboratory tests in reagent grade ac- ids. Below the line, rates under 0.1 mm/y are expected. Similarly, the red line indicates the combinations of acid concentration and temperature at which a corrosion rate of 0.5 mm/y (20 mils per year) is expected. Above the line, rates over 0.5 mm/y are expected. Between the blue and red lines, corrosion rates are expected to fall between 0.1 and 0.5 mm/y. Haynes International - ULTIMET® alloy Comparative 0.1 mm/y Line Plots To compare the performance of ULTIMET® alloy with that of other materials, it is useful to plot the 0.1 mm/y lines. In the following graphs, the lines for ULTIMET® alloy are compared with those of two popular, austenitic stainless steels (316L and 254SMO), and two nickel alloys (625 and C-22), in hydrochloric and sulfuric acids. The tests in hydrochloric acid were limited to a concentration of 20% (the azeotrope). At hydrochloric acid concentrations up to 15%, the performance of ULTIMET® alloy exceeds that of alloy 625, and in sulfuric acid, the performance of ULTIMET® alloy matches that of alloy 625 at many concentrations. Haynes International - ULTIMET® alloy Selected Corrosion Data Hydrochloric Acid Conc. 50°F 75°F 100°F 125°F 150°F 175°F 200°F 225°F Wt.% 10°C 24°C 38°C 52°C 66°C 79°C 93°C 107°C Boiling 1 - - - - - - - - <0.05 1.5 - - - - - - - - - 2 - - - - - - - - - 2.5 - - - - <0.01 <0.01 <0.01 - 43.85 3 - - - - - - - - - 3.5 - - - - - - - - - 4 - - - - - - - - - 4.5 - - - - - - - - - 5 - - - - 0.01 5.75 - - - 7.5 - - - - - - - - - 10 - <0.01 0.16 0.8 1.74 - - - - 15 - 0.15 0.73 1.83 4.75 - - - - 20 - 0.17 0.56 1.04 2.58 - - - - All corrosion rates are in millimeters per year (mm/y); to convert to mils (thousandths of an inch) per year, divide by 0.0254. Data are from Corrosion Laboratory Job 181-90. All tests were performed in reagent grade acids under laboratory conditions; field tests are encouraged prior to industrial use. Haynes International - ULTIMET® alloy Selected Corrosion Data Continued Nitric Acid Conc. 50°F 75°F 100°F 125°F 150°F 175°F 200°F 225°F Wt.% 10°C 24°C 38°C 52°C 66°C 79°C 93°C 107°C Boiling 10 - - - - - - - - <0.01 20 - - - - - - - - <0.01 30 - - - - - - - - 0.01 40 - - - - - - - - 0.03 50 - - - - - - - - 0.07 60 - - - - - - 0.03 - 0.12 65 - - - - - - 0.04 - 0.15 70 - - - - - - 0.06 - 0.18 All corrosion rates are in millimeters per year (mm/y); to convert to mils (thousandths of an inch) per year, divide by 0.0254. Data are from Corrosion Laboratory Job 182-90. All tests were performed in reagent grade acids under laboratory conditions; field tests are encouraged prior to industrial use. Haynes International - ULTIMET® alloy Selected Corrosion Data Continued Phosphoric Acid Conc. 125°F 150°F 175°F 200°F 225°F 250°F Wt.% 52°C 66°C 79°C 93°C 107°C 121°C Boiling 10 - - - - - <0.01 20 - - - - - 0.01 30 - - - - - 0.01 40 - - - - - 0.03 50 - - - <0.01 - - 0.14 60 - - - 0.01 - 0.01 0.25 70 - - - 0.01 0.01 0.02 0.46 80 - - - 0.01 0.07 0.55 10.95 85 - - - 0.01 0.07 0.57 30.58 All corrosion rates are in millimeters per year (mm/y); to convert to mils (thousandths of an inch) per year, divide by 0.0254. Data are from Corrosion Laboratory Job 183-90. All tests were performed in reagent grade acids under laboratory conditions; field tests are encouraged prior to industrial use. Haynes International - ULTIMET® alloy Selected Corrosion Data Continued Sulfuric Acid Conc. 75°F 100°F 125°F 150°F 175°F 200°F 225°F 250°F 275°F 300°F 350°F Wt.% 24°C 38°C 52°C 66°C 79°C 93°C 107°C 121°C 135°C 149°C 177°C Boiling 1 - - - - - - - - - - - 0.13 2 - - - - - <0.01 - - - - - 0.27 3 - - - - - - - - - - - - 4 - - - - - - - - - - - - 5 - - - <0.01 - 0.01 - - - - - 1.26 10 - - - - - 0.43 - - - - - 1.92 20 - - - <0.01 0.01 1.83 - - - - - 4.48 30 - - - <0.01 1.36 3.58 - - - - - 10.54 40 - <0.01 <0.01 0.29 2.25 - - - - - - 20.94 50 - <0.01 - 0.96 - - - - - - - - 60 - <0.01 <0.01 1.48 - - - - - - - - 65 - - 0.63 - - - - - - - - - 70 - <0.01 0.55 - - - - - - - - - 80 - <0.01 1.02 1.64 - - - - - - - - 85 - 0.03 - - - - - - - - - - 90 <0.01 0.26 1.68 - - - - - - - - - 96 <0.01 0.21 1.76 2.24 - - - - - - - - All corrosion rates are in millimeters per year (mm/y); to convert to mils (thousandths of an inch) per year, divide by 0.0254. Data are from Corrosion Laboratory Jobs 159-90 and 8-91. All tests were performed in reagent grade acids under laboratory conditions; field tests are encouraged prior to industrial use. Haynes International - ULTIMET® alloy Selected Corrosion Data (Reagent Grade Solutions, mm/y) Concentration 100°F 125°F 150°F 175°F 200°F Chemical wt. % 38°C 52°C 60°C 79°C 93°C Boiling Acetic Acid 99 - - - - - <0.01 1 - - - - - 0.05 2.5 - - <0.01 <0.01 <0.01 43.85 Hydrochloric 5 - - 0.01 - - - Acid 10 0.16 0.8 1.74 - - - 15 0.73 1.83 - - - - 20 0.56 1.04 - - - - 10 - - - - - <0.01 20 - - - - - <0.01 30 - - - - - 0.01 Nitric 40 - - - - - 0.03 Acid 50 - - - - - 0.07 60 - - - - 0.03 0.12 65 - - - - 0.04 0.15 70 - - - - 0.06 0.18 10 - - - - - <0.01 20 - - - - - 0.01 30 - - - - - 0.01 40 - - - - - 0.03 Phosphoric 50 - - - - <0.01 0.14 Acid 60 - - - - 0.01 0.24 70 - - - - 0.01 0.45 80 - - - - 0.01 10.92 85 - - - - 0.01 30.58 1 - - - - - 0.13 2 - - - - <0.01 0.27 5 - - <0.01 - 0.01 1.26 10 - - - - 0.43 1.92 20 - - <0.01 0.01 1.83 - 30 - - <0.01 1.36 - - Sulfuric 40 <0.01 <0.01 0.29 2.25 - - Acid 50 <0.01 - 0.96 - - - 60 <0.01 <0.01 1.48 - - - 70 <0.01 0.55 - - - - 80 <0.01 1.02 - - - - 90 0.26 1.68 - - - - 96 0.21 1.76 - - - - Haynes International - ULTIMET® alloy Galling Resistance Haynes International - ULTIMET® alloy Erosion Resistance Haynes International - ULTIMET® alloy Abrasion Wear AWM = All weld metal WO = Weld overlay WRT = Wrought Haynes International - ULTIMET® alloy Resistance to Pitting & Crevice Corrosion ULTIMET® alloy exhibits very high resistance to chloride-induced pitting and crevice attack, forms of corrosion to which the austenitic stainless steels are particularly prone. To assess the pitting resistance of ULTIMET® alloy relative to other corrosion-resistant materials, it has been subjected to tests in Green Death (11.5% H2SO4 + 1.2% HCl + 1% FeCl3 + 1% CuCl2). Experiments wereperformed at various temperatures (in increments of 5°C) to determine the lowest temperature at which pitting occurs in a 24 h test period (the so-called Critical Pitting Temperature for Green Death). The results were as follows: Alloy Critical Pitting Temperature - °F °C ULTIMET® 248 120 C-22® 248 120 C-276 230 110 625 167 75 6B 113 45 316L 77 25 Resistance to Stress Corrosion Cracking Sulfide Stress Cracking Wrought ULTIMET® alloy has been tested according to NACE TM0177, which defines sulfide stress cracking as a room temperature phenomenon, resulting from hydrogen em- brittlement. The TM0177 tests involved 5% NaCl + 0.5% glacial acetic acid, saturated with H2S, proof- ring apparatus, and samples coupled to carbon steel and stressed to the point of yield. ULTIMET® alloy was able to withstand these conditions, both annealed and cold-reduced (15%), indicating good resistance to hydrogen embrittlement. H2S – Induced Stress Corrosion Cracking Cracking at elevated temperatures in environments containing H2S is defined as a form of stress corrosion cracking. ® Wrought ULTIMET alloy has been tested in 20% NaCl + 0.517 MPa (75 psi) H2S + 4.83 MPa (700 psi) CO2, with and without 0.5 g/l sulfur, at 121°C and 177°C; the tests were conducted according to the recommendations of ASTM Standard G 39, the fixtures being made of ULTIMET alloy, to prevent galvanic effects. Like other materials, ULTIMET® alloy was prone to cracking in the cold-reduced condition, but resistant to H2S-induced stress corrosion cracking in the annealed condition, at these temperatures.
Details
-
File Typepdf
-
Upload Time-
-
Content LanguagesEnglish
-
Upload UserAnonymous/Not logged-in
-
File Pages20 Page
-
File Size-