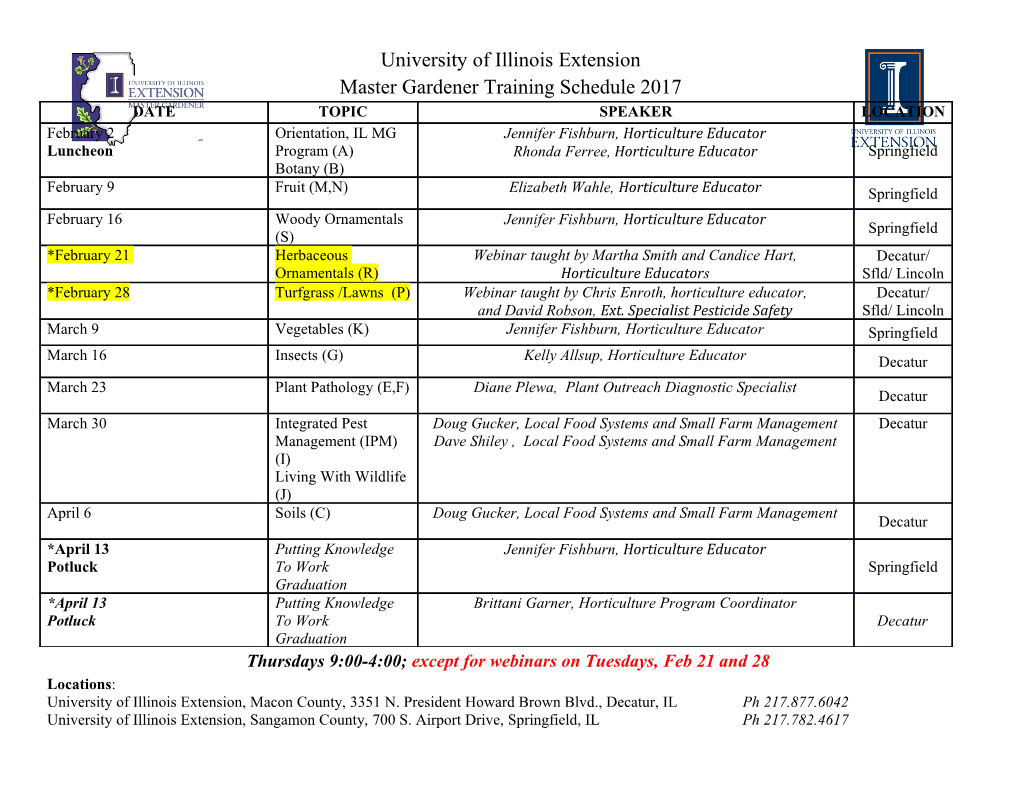
......................... Pollution Prevention in Machining and Metal Fabrication A Manual for Technical Assistance Providers Excerpts March 2001 ......................... CHAPTER 4 Pollution Prevention and Metalworking Fluids - Selection, Maintenance, and Application The selection of a fluid that is easily serviced and that does not interact adversely with other processes can eliminate many of the pollution problems resulting from fluid use. The use of in- process treatment technologies may greatly extend the useful life of metalworking fluids. Microbial degradation of fluids is one the most frequent causes of premature fluid disposal and therefore must be addressed. To further reduce the environmental burden created by spent fluids, the application method used to apply the fluid and the volume of fluid applied should be optimized to minimize contamination of the work area as well as the process baths. This Chapter covers the fluid selection process, fluid maintenance programs and technologies, and fluid application techniques. Table 4.1 Metalworking Fluid Selection, Maintenance, and Application Fluid Selection • evaluating if fluids are necessary • standardizing - using as few types of fluids as possible • recyclability/treatability • cleanability/cleaning bath life extension Fluid Maintenance • water quality • fluid testing • contaminant removal (see summary table, p. 58) • preventing and inhibiting microbial growth Fluid Application • optimize application methods • implement microdispersion, where appropriate Fluid Selection Firms have been using fluids in the fabrication of metal parts for over a hundred years to provide lubrication and chip removal, and more recently cooling. The industry’s use of fluids has evolved as the fluid industry has evolved. There may be a number of factors that drive a firm to select a new fluid: • the company is looking for a fluid to use in a new or expanded product line • the existing fluid has become incompatible with some new equipment • the existing fluid is incompatible with changes to subsequent processes • the company wants to increase process times and needs increased lubricity and/or cooling • the fluid life is too short and hence the fluid is too costly 49 The process firms use to select a fluid may vary greatly based on company size and level of in- house technical expertise. Some firms may select a fluid based solely on its lubricating qualities and its compatibility with the tools and workpieces while other firms may do a more detailed analysis. The time spent carefully selecting a fluid can greatly reduce wastes from metal fabrication processes and subsequent processes. Issues that should be considered in fluid selection are discussed in the sections below. These issues are: •cost • recyclability Circular Sawing at Bartley Machine with • cleanability Vegetable-based Metalworking Fluid • standardization Bartley Machine, a fabrication job shop in Amesbury, Massachusetts, cuts stock into two-inch lengths using a Cost circular saw. This saw previously used a lard-based fluid, applied to the saw blade manually using a brush at a rate It is more important to select a fluid of 1.5 quarts of fluid per day. The saw now uses a that is appropriate to the process than it is vegetable-based fluid, delivered directly to the cutting area by two fine misting nozzles with a consumption rate to select a fluid that is the least expensive. of two ounces per day. The old fluid was purchased at a The hidden costs that result from fluid use cost of $15 per gallon ($5.63/day), while the new fluid is are much greater than the fluid material purchased for $80 per gallon ($1.25/day). costs. Metalworking fluid management In the old process, the fluid would hit the saw blade and costs range from 7 to 17 percent of spray all over. To contain the spraying fluid, the operator manufacturing costs, with purchase costs needed to cut cardboard and build an enclosure around the machine and work area at the beginning of every shift being a small fraction of that (Heine 1997). and remove the enclosure at the end of every shift and Much of a firm’s labor and overhead costs dispose of it. This process had high waste handling are associated with machine downtime and charges and setup and breakdown labor costs; building other maintenance related to fluid use. and removing the cardboard enclosure was about a 20 minute process. No enclosure is required with the new fluid and application method. Chips are dry and clean- Recyclability/treatability up time is minimal. The volume of fluid applied and the Another benefit of the change to higher quality vegetable- based fluid and low-volume mist spray application is the method of fluid application varies increase in tool life. With the old fluid, a carbide blade depending on the cooling, lubricating, and would last for five production runs. With the new fluid, the chip removal requirements of a given operator gets sixty production runs out of a single carbide application. These factors, as well as the blade and the steel blade-life has been increased five-fold (Piekunka 1999). amount of fluid carried out on parts, will dictate the need for and applicability of fluid recycling. Many processes continually re-circulate and reuse metalworking fluids. These processes employ some form of treatment ranging from gross chip removal using a simple screen to final particle removal in a flatbed wedge-wire pressure filter. Any time fluid can be recovered in a process its life may be extended to some extent by treating it. For more information on the treatment of metalworking fluids, see the Contaminant Removal Systems section later in this Chapter. Research is underway through both the Massachusetts Toxics Use Reduction Institute and UCLA to evaluate the recovery of metalworking fluids from cleaning baths for reuse in the 50 process. Trials to date have had mixed results. However, further developments in this area can have a significant impact on closing the loop of metal fabrication processes. Cleanability/cleaning Bath Life Extension When selecting a metalworking fluid it is crucial to consider the entire process that the fluid will affect. The machine shop will most likely need to remove the fluid it has applied, or if the workpiece is going off-site for further processing, someone else will have to remove the fluid before the workpiece can be further processed. By working with metalworking fluid vendors, firms should select a fluid that may be easily removed, collected, and disposed of or recycled. Metal fabricators should also talk with their metal stock suppliers to determine what fluids they apply to metal stock during primary metals manufacturing or as a protective coating during storing and shipping. It may be possible for fabricators to ask them to use a fluid that is more compatible with the fluid the fabricator is using or to use a fluid that is easier to clean off. With the phase out of chlorinated solvents and their use in cleaning systems, Milling Machines at Bartley Machine firms have switched to a number of different In the milling operations at Bartley Machine, a soluble alternatives. Alternative cleaning chemistries metalworking fluid is applied to the work area by an air and systems require a more tailored approach nozzle. A vacuum draws off chips and lube mist to cleaning than did their chlorinated solvent overspray. Oil-coated chips and lube overspray are carried to a barrel where chips are retained and fluid is counterparts. Certain cleaning systems may recirculated to the feed. A water-soluble metalworking be more effective at removing a given fluid was selected for this process because it is easier to contaminant than others. For example, clean off the parts and it was already being used by a aqueous cleaning systems are effective at belt sander that has a filtration system. When the fluid starts to foul, it is added to the belt sander sump where removing soluble oils but may be less it is filtered through a settling tank and cyclone filters to effective at removing dry-film lubricants. For remove fines. By standardizing fluids, Bartley has been more information on various cleaning able to greatly extend the useful life of its fluid by using a sophisticated centralized filtering system. For more processes and P2 alternatives, see Pollution information on metalworking fluid treatment systems, Prevention in the Metal Finishing Industry: A see the Fluid Maintenance Section in this Chapter Manual for Technical Assistance Providers, (Piekunka 1999). http://www.newmoa.org/publications. Aqueous cleaning systems are effective at removing metalworking fluids, but some systems do not have the proper filtration equipment to remove emulsified fluids from the cleaning fluid bath, which causes the bath to be changed frequently at potentially significant disposal and purchase costs. In this situation another metalworking fluid could be selected that provides the necessary lubricity, cooling, and chip removal while simplifying separation of the metalworking fluid from the cleaner bath and hence extending the life of the cleaner bath (MA TURI 1996). For other applications, where the volume of fluid used in metal fabrication processes has been minimized and the cleaning bath has a small loading rate, it may be possible to install an inexpensive media filter, such as a polypropylene bag, to capture the emulsified machining fluid. Firms that out source metal parts and products for further processing should be encouraged to identify the fluids they are using so that the electroplater, coater, or other parts/product processor may make educated decisions about which cleaning processes to use for cleaning a 51 given work order. Electroplating job shops usually employ multiple cleaning systems to preclean the various work orders they fill. By knowing more about the contaminants on a given part, job shops can make much better decisions about how to clean it, therefore eliminating the time- consuming and costly trial and error cleaning trials, the costs of which are passed on to the metal fabricator.
Details
-
File Typepdf
-
Upload Time-
-
Content LanguagesEnglish
-
Upload UserAnonymous/Not logged-in
-
File Pages17 Page
-
File Size-