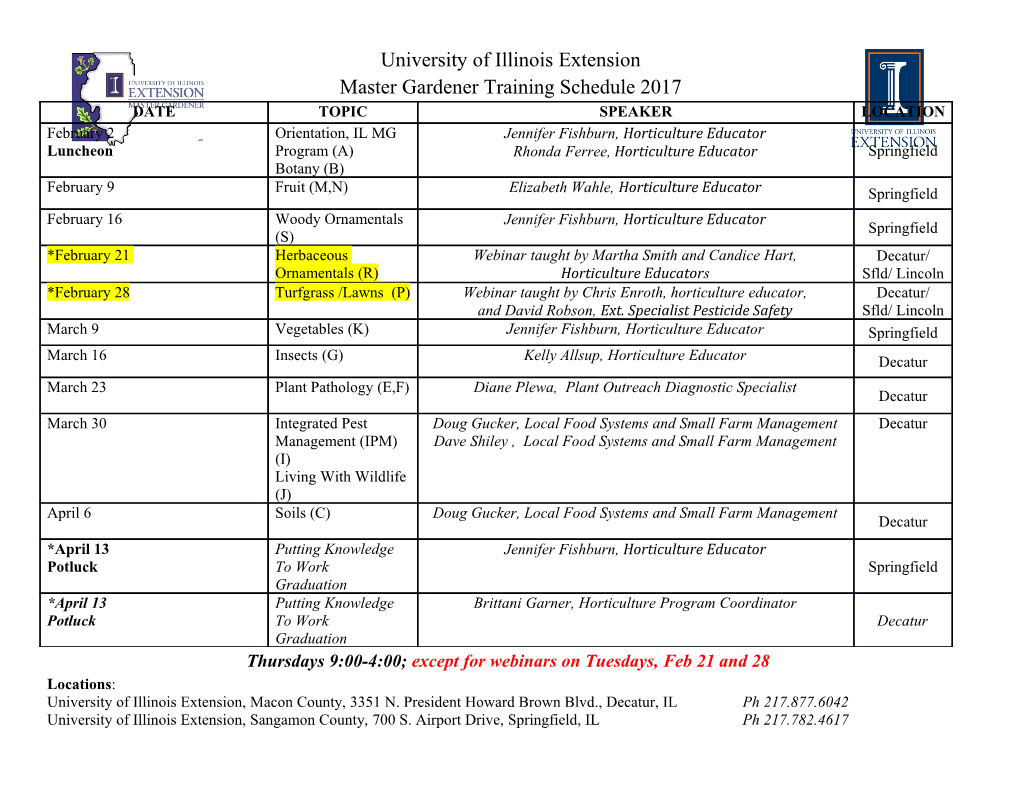
Amity Aviation Mission One Report Amity Regional High School Submission Date: December 2, 2016 Amity Aviation 25 Newton Road Woodbridge, CT 06525 Table of Contents Section Page Executive Summary 2 Research Report 3 Introduction 3 Bypass Ratio and Weight Reduction 3 Emissions 4 Reliability and Integrity 5 Weight and Strength 5 Calculations 1 (Old and New) 6 Efficiency Justification 6 Cost Justification 7 Conclusion 7 Calculations 2 (Choice Justification) 8 Engine Requirements 8 References 10 1 Executive Summary Throughout the two month process, Amity Aviation worked diligently to design and implement a research based approach that looked at utilizing the new CFM International LEAP engines. The team approached this task in a way that ensured efficiency and depth of understanding by all persons on the team. After looking through the background information, the team began exploring the increased efficacy the LEAP engines provide over the aging generation of CFM fans for our re-engining purposes. The team agreed to utilize a four-factor matrix while assessing all components that justify switching each original CFM engine to the new CFM LEAP engines. The individual factors that contributed to our conclusion were fuel consumption, noise, emissions, and cost. Within the matrix, each of these elements were weighted based upon a research drive approach, and then tabulated to arrive at an overall score. For instance, fuel consumption was given a 40% weight, the highest out of all the factors, as its effect on the overall efficiency was determined to be significantly higher than the other factors. Since fuel consumption is a recurring cost to a company that purchases the engine, maximizing fuel consumption is one way a purchaser can limit extraneous spending. The transition to LEAP engines not only allows the airline to minimize its fuel costs but also allows them to pass these savings onto customers. After finalizing the matrix (which can be viewed on the [Calculations 1] page) it was concluded that CFM LEAP engines were approximately 12% more efficient (for the team’s purposes) than their CFM56 counterparts. After this preliminary phase was completed, the team needed to decide which of the CFM LEAP engines would be used to re-engine both the Boeing 737-700, which originally had two CFM International CFM56-7B engines, and the Airbus A319, which originally had two CFM International CFM56-5B engines. After performing additional calculations comparing the specifications of the three engines, and analyzing requirements of the aircraft (Calculations 2), the team decided that the LEAP 1-A engine would best fit the Airbus A319, and that the LEAP 1-B would best fit the Boeing 737-700. Calculations showed that while in terms of thrust, each LEAP engine was certified for the Airbus 319 and the Boeing 737-700, that only the LEAP 1-B could be used for the 737 due to the size constraints of the engine and the height of the wing. For the Airbus A319, the team utilized the information that the LEAP 1-B had significantly worse thrust and bypass than the 1-A and 1-C. This was in order to rule out the potential use of the 1-B, as the other two engines were significantly better choices for the Airbus. In deciding between the 1-A and the 1-C, the team ultimately decided to re-engine the Airbus with the LEAP 1-A engine, which had a significantly higher range of thrust than the 1-C, allowing for more versatility and higher maximum takeoff weight. 2 By utilizing and pairing each of the LEAP engines to the Airbus A319 and the Boeing 737-700, Amity Aviation was able to achieve the most cost efficient and high performance solution, creating high performance for the two aircraft while saving money for the companies utilizing the newly engined aircraft. Research Plan Introduction The CFM LEAP Engine family is a group of high-bypass turbofans, which utilize high bypass ratios in order to create significant increases in propulsion force in the engine. The LEAP engines are an advancement from the previous group of CFM engines, known as the CFM56 engines. The LEAP engines are capable of operating under much higher pressure than the CFM56 engines, resulting in much higher efficiency for the engine. Similarly, the material use to construct the engine was changed to a carbon fiber, allowing for a much larger fan and engine, while keeping the weight of the engine reasonable. This creates a much higher bypass ratio, allowing for more propulsion in the engine. The CFM LEAP family of engines is a group of three engines: LEAP 1-A, LEAP 1-B, and LEAP 1-C (Figure 1.1). Each engine is specifically designed to be new engine options for three different aircraft families. The LEAP 1-A is utilized in the Airbus A320neo, under which the Airbus A319 is included. The LEAP 1-B is utilized in the Boeing 737 MAX, which is the Boeing 737-700 equipped with the new engine option. Finally the LEAP 1-C is used in the Comac C919, a competitor to both the Boeing 737 MAX and the Airbus A320neo. Figure 1.1 Bypass Ratio and Weight Reduction A large component of the CFM engines is the the fact that they are high bypass turbofans (Figure 1.2), meaning they have a high bypass ratio, which is the ratio of low pressure air to high pressure air within the engine. In order to create a higher bypass, higher airflow or a large fan is needed. However, a 3 larger fan creates a larger engine, which in turn weighs down the aircraft significantly. The CFM LEAP engines have a high bypass ratio without dramatically increasing the weight of the engine itself. Instead, CFM combats the increased fan size by changing the material of the fan blades, from a heavy metal to carbon fiber, a material that is both light and durable enough to support the weight of the Airbus A319 and the Boeing 737-700. This allows the bypass ratio to significantly improve, becoming approximately 11:1 for the 1-A and the 1-C, and 9:1 for the 1-B. The high bypass ratio of the engines allows for greater difference in pressure between the high pressure compressed air inside the engine and the low pressure air surrounding the engine, creating more propulsion in the engine. This extra propulsion generates more thrust which, in turn, allows for increased lift while providing better overall efficiency for the aircraft. Figure 1.2 Emissions One of the greatest strengths of the LEAP engine family is the extreme reduction in nitrogen oxide (NOx) emissions. Standard regulations under the CAEP/6 regulations require certain standards regarding NOx emissions to be met in order to reduce environmental pollution. The LEAP engine family is capable of reducing emissions by at least 10% compared to the CFM56 engines, and reducing emissions by 50% compared to the CAEP/6 standards, significantly reducing air pollution. This reduction in air pollution is achieved through the use of the second generation Twin-Annular, Pre-Mixing Swirling Combustor (TAPS II). TAPS II preemptively mixes a solution of air and fuel before both elements reach the combustion chamber, allowing for a much more efficient burn, and significantly less NOx emissions. 4 Reliability and Integrity According to the Bureau of Transportation Statistics (BTS), approximately 77.34% of flights are delayed, meaning they do not arrive within 15 minutes of schedule. Mechanical problems within the engine can severely delay flights, causing high costs for both airline companies, and loss of time for passengers. However, the LEAP engine family boasts a 99.98% dispatch reliability, meaning that 99.98% of planes with the LEAP engine are predicted to leave within this 15 minute departure window. While most aircraft operators follow a standard of 98% dispatch reliability, the LEAP engine significantly increases the reliability. While other standard aircraft are projected to leave late in 200 out of 10,000 prospective flights, the LEAP engines are only projected to miss two flights. This high reliability reduces the cost of maintenance, and increases the flight time spent in the air. Weight and Strength The CFM LEAP engines were constructed with methods new and revolutionary to the industry. Resin Transfer Molding (RTM) is a liquid closed mold process, featuring a vacuum, that is used to create 3D woven composites. The RTM method allows for the creation of more complexly shaped composites that have superior strength-to-weight ratios. The new LEAP engine family implements these 3D woven carbon composites, as produced by the RTM method, in the fan blade and case. The standard manufacturing method in the aerospace industry is the 2-D composite production. However, the LEAP engines recognize and implement the numerous benefits of 3D woven composites. These materials, having been produced in a fairly new way, are more lightweight and durable than the parts used in a standard aircraft engine. These materials reduce risks of malfunction, meaning there are fewer cracks, and they cost much less for producers, both in manufacturing and through the benefits reaped. In fact, it is estimated by Bally Ribbon Mills, a leader in manufacturing, that for every pound of weight reduced in the components of an aircraft, operator's save roughly $1 million in expenses. The LEAP engines are also, for the first time ever, using 3D printed parts. The fuel nozzles on the LEAP 1-B engines are being 3D printed using lightweight ceramic matrix composites (CMCs). These nozzles can now operate in extremely high temperatures since they hold high density, more hardness and superior thermal and chemical resistance.
Details
-
File Typepdf
-
Upload Time-
-
Content LanguagesEnglish
-
Upload UserAnonymous/Not logged-in
-
File Pages12 Page
-
File Size-