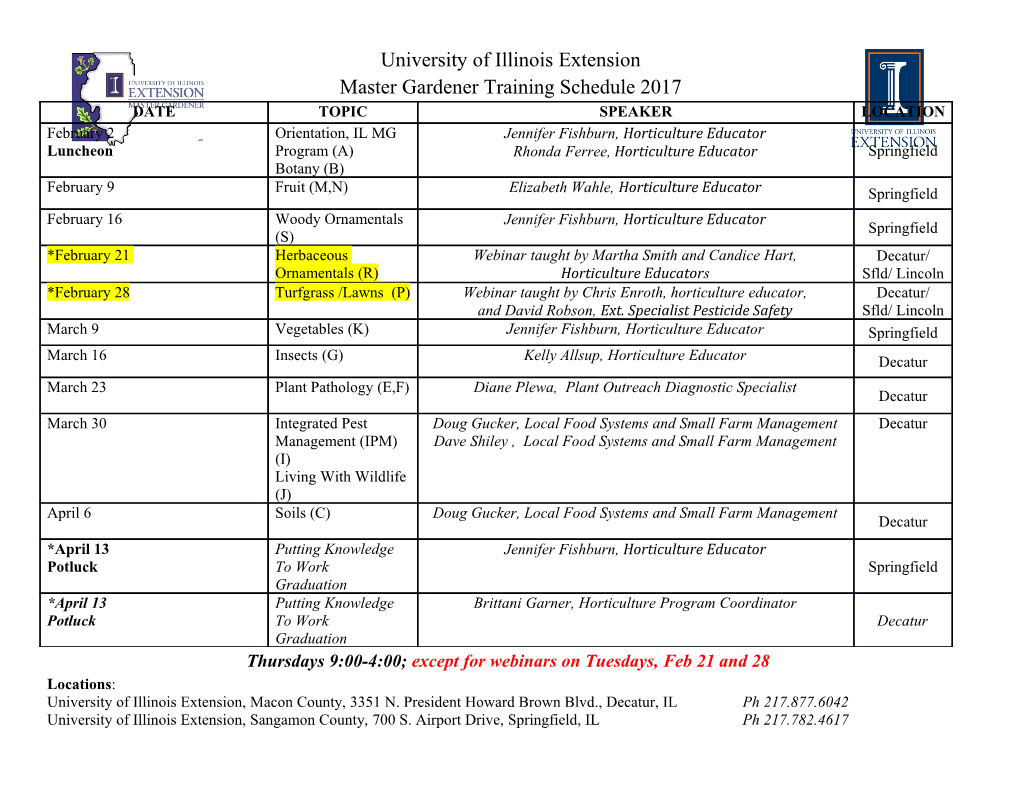
PREVENT LINT CONTAMINATION . clean cotton means satisfi ed customers! PROTECT YOUR COTTON FIBER . and you will preserve your markets! Even the tiniest particles can contaminate seed cotton and lint and result in blemished fi nished goods. U.S. cotton producers are competing with man-made fi bers and foreign cotton in today’s global market- place, one of cotton’s greatest attributes - its pure, natural quality – can be degraded by a variety of contaminants. This impairs producers’ relationships with textile manufacturers and also undermines the industry’s “value-added” promotional activities. HOW? PLASTIC Contaminants can Storing cotton in modules in the end up in fi nished fi eld allows pickers to operate yarn and fabric continuously during optimum harvesting products. These conditions. Over time, module covers may de- tainted yarns and teriorate and tear, leaving pieces of plastic on seed fabrics become cotton as contamination. More often, the practice of “seconds.” This using plastic twine to tie down module covers leads decreased value and to contamination problems. Even a short piece of condition shrinks plastic twine or rope can contaminate several bales U.S. textile manu- Enlargement reveals contaminant of cotton if the material enters the gin. The foreign facturers’ profi ts and which tangled with cotton fi bers material will be shredded and dispersed into the lint. undermines cotton’s during yarnmaking market appeal. Manufacturers constantly determine Plastic irrigation ditch liners left in the fi eld may which raw materials they can mix for spinning that be picked up by harvesting equipment and become will offer the best profi t potential. There’s no place mixed in with the seed cotton. If not removed, for contaminated cotton in that recipe. this plastic will travel through the gin with the seed cotton, become shredded and remain with IDENTIFYING MAJOR TYPES the ginned lint. These small pieces of plastic cause OF CONTAMINATES major problems at textile mills by increasing spin- If U.S. cotton producers and ginners want a market- ning costs and by their very presence in fabric. As able product, they must work to eliminate contami- a result, large quantities of fabric must be sold as nation of seed cotton and lint. The most cost-effec- defective materials or seconds. tive way is to prevent contamination, but if impurities Trash which may have blown into a fi eld from the are found, steps must be taken to eliminate the roadside is also a contaminant. Debris such as small contaminants before they are processed through the plastic bags can be picked up by harvesters and marketing chain. ginned with the seed cotton. The fi rst step is recognizing contaminants and their sources. Contaminants can best be catego- rized as plastic, rubber, grease and oil, apparel and other materials. RUBBER Black, rubber doffers and moistener pads were used Mills also have reported evidence of sticky cotton exclusively on spindle pickers at one time. In recent traced to oils on cotton. Excessive oil on lint causes years, though, cotton picker manufacturers are sup- processing problems in textile mills because cotton plying non-contaminating, non-rubber, materials as may stick and wrap on mill equipment rather than original equipment. passing through effi ciently. Non-contaminating doffer materials have been test- Excessive use of picker oils in picker moistening ed and found to perform just as well or better than systems is believed to be one cause of oil on cotton. conventional rubber doffers and moistener pads. Most specialists recommend that water or a solution The widespread use of non-contaminating materials of water with an approved wetting agent be used in has virtually eliminated black rubber specks from moistening systems to keep plant sap from accumu- tainting fi nished textile products. While black rubber lating on the spindles. Some picker manufacturers doffers and moistener pads still are available in the have warned that use of oil in the spindle moisten- aftermarket throughout the Cotton Belt, growers are ing system increases fi re hazards. encouraged to use only non-contaminating replace- APPAREL AND OTHER MATERIALS ment doffer and moistener pads. Cleaning rags, clothes hats and other materials left However for pickers which have not been updated near harvest, module or gin machinery, especially with the new non-contaminating doffers, extreme at gin suction pipes, can be pulled into the gin and care must be taken to maintain a precise spindle-to- chopped up. This puts small pieces of contaminant doffer clearance. Misalignment to the point that the in the ginned lint. Even textile items made from doffers and spindles touch causes tiny doffer par- cotton can cause contamination. When the contami- ticles to be ground off and left in seed cotton. An in- nated bale is mixed with 25 to 50 other bales at the terference of a few thousandths of an inch between textile mill, a huge loss results. just one spindle bar and a black, rubber doffer plate can generate thousands of tiny, black particles that Although tests show that modern bale packaging are not visible in seed cotton. materials are not a major source of contamination, some textile mills believe that these materials are a Gin and mill cleaning equipment cannot remove possible contamination source. This should be con- the rubber particles. These rubber particles almost sidered when choosing a packaging material. always go undetected until the costly processes of spinning, weaving or knitting, scouring and bleach- Another problem is created when producers, ginners ing are completed. The result: rubber-blemished and warehousemen use common spray paint to mark fabrics or garments. seed cotton modules and packaged bales. When sprayed on cotton, paint stains the lint and cannot be GREASE AND OIL removed in any gin or mill process. This stained cot- Growers are urged ton then shows up as a defect in fi nished fabrics. The to take every problem can be avoided by using one of the textile- precaution to keep friendly “marking” products currently on the market. grease and oil sepa- Residues of plant parts such as bark, grass and seed rated from cotton. coat fragments have the potential to become con- Heavy accumula- taminants. They are diffi cult to remove at the mill. tions of grease and Problems caused by these impurities are one reason grime on picker why grade penalties are imposed on lint containing bars often break off these contaminants. in chunks and mix Prevent grease stains from contami- with the seed cot- nating bales at the gin and during Occasionally, machine parts, pieces of bale ties and handling as seen on this bale in the other objects are found pressed inside cotton bales. ton. Grease concen- opening room of a mill. trations stain cotton These materials may become trapped in the lint at the and ultimately end up as fl aws in otherwise high gin. Besides posing a fi re risk, such materials can seri- quality cotton fabrics. ously damage mill equipment. PRECATIONS YOU CAN TAKE TO PROTECT SEED COTTON AND LINT FROM CONTAMINATION PLASTIC: • Avoid using plastic • Grind new doffers before putting them on the twine for securing machine and clean excess particles from the doffer tarps on seed cotton assembly after grinding. modules and trailers. • Maintain proper operation of the moistening system. Cotton rope or cotton cord materials are • Keep the picker in good mechanical repair. Worn recommended. parts, such as spindles, moistener pads, doffers, bearings, bushings, springs and rails should be • Make sure all covers replaced and adjusted to factory specifi cations by and tie down materi- trained personnel. als on or near seed cotton are removed • Doffer and moistener pads made from non-con- Care taken during harvesting will taminating materials are available. Check with before seed cotton prevent debris, such as the plastic reaches the suction protruding from this module, from your dealer. lane or module feeder becoming a lint contaminant. GREASE AND OIL: at the gin. • Growers are urged to follow the picker manufac- • Remove all irrigation ditch liners and other foreign turer’s recommendations carefully. materials from fi elds prior to harvest. • Lubricate pickers daily but use only the necessary • Cover bales with only those packaging materials amounts of grease and lubricating oils. Wipe excess which meet the specifi cations of the Joint Cotton accumulations from fi ttings after each lubrication. Industry Bale Packaging Committee. • Clean picker heads and assemblies at least once a • Consider using cotton rather than plastic tarps for week to remove accumulations of lubricants. covering seed cotton. If plastic covers are used, • Use only a solution of water and approved wetting make sure they are not worn or frayed. agents in the moistening system for normal har- RUBBER: vesting conditions. If picker oils are absolutely nec- • Adjust the spindle- essary because of special picking conditions, only to-doffer clearance use oils approved by picker manufacturers. Never to the manufactur- use motor oil or diesel oil in moistening systems. er’s recommenda- OTHER MATERIALS: tions. • Keep cleaning rags and clothing, such as gloves, • Replace worn hats and handkerchiefs, away from seed cotton doffer columns and gin machinery. promptly with • Inform employees of hazards created at textile non-contaminat- mills by foreign objects in bales. ing parts that fully Improperly adjusted spindles will meet the picker grind doffer pads, creating small • Avoid production and harvesting practices which rubber particles that contaminate cause excessive bark. manufacturer’s cotton. standards. • Use non-contaminating markers to mark modules and bales. Use only marking products tested and proven to be removable from lint at the mill. Published by the National Cotton Council, in cooperation with Cotton Incorporated and USDA, Extension Service..
Details
-
File Typepdf
-
Upload Time-
-
Content LanguagesEnglish
-
Upload UserAnonymous/Not logged-in
-
File Pages3 Page
-
File Size-