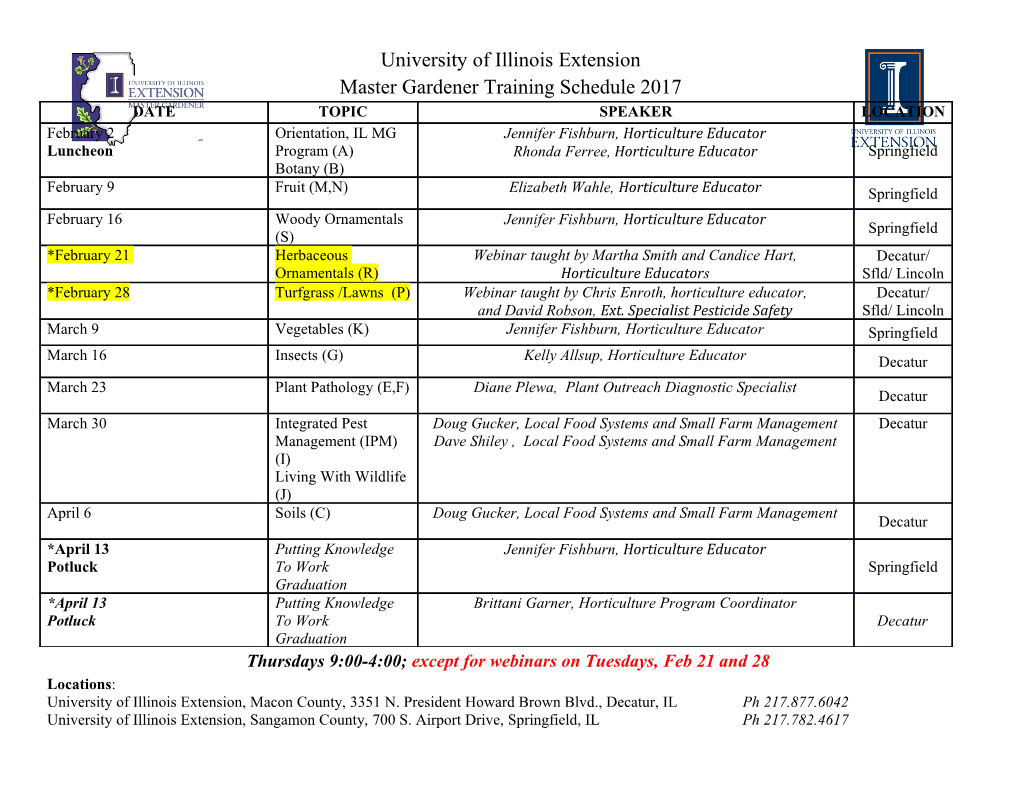
BRAZILIAN JOURNAL OF INSTRUMENTATION AND CONTROL, VOL. 01, No 01, NOVEMBER, 2013 1 Industrial Ethernet for Distributed Control in Factory Automation Alexandre Baratella Lugli, Lúcia R. H. Rodrigues Franco .____________________________________________________________________________ layers. It was created by Robert M. Metcalfe, also in the mid Abstract—The manuscript aims to propose a new way to seventies, to assist the physical connection of computer accomplish the fieldbus modules control, using a flexible systems. [2, 15] distributed architecture applied to the industrial Ethernet Nowadays, there are fourteen industrial Ethernet networks, networks. The work proposal is to develop an algorithm for as follows: PROFINET, Ethernet/IP, HSE (High Speed messages scheduling, applied to a distributed architecture, with Ethernet), Modbus/TCP, EPA, EPL, EtherCAT, IEC 61850, the removal of the master controller, where only the fieldbus JetSync, P-Net, Sercos III, SynqNet, TCnet and Vnet/IP. [3, 4, modules and switches operate on the network, and then having a 18] These networks operate typically with master-slave type communication messages distributed control. The proposed communication. [3, 4, 5, 17] algorithm uses an off-line or pre-run-time type technique of messages scheduling. Therefore, the manuscript develops a new This manuscript discusses the communication technologies, communication concept, applied industrial Ethernet networks, known as "industrial Ethernet". The proposal presented seeks with communication network control and each field element to develop a communication methodology adequate for distributed throughout the manufacturing process. For this, it is flexible distributed control applications. The manuscript necessary to model the new communication concept, perform the proposal is to develop an algorithm for messages scheduling, messages scheduling (which is essential for defining the message applied to a distributed architecture with the removal of the communication order in the network trafficked, due to not using master controller, where only the fieldbus modules and a centralized master controller) and perform verification testing switches operate on the network, and then having a distributed and idea proposal validation. control of the manufacturing process. The proposed algorithm uses an off-line or pre-run-time type technique of messages Index Terms— Ethernet; Industrial Networks; Optimization, Scheduling. scheduling. II. THE REQUERIMENT FOR A DISTRIBUTED CONTROL CONCEPT I. INTRODUCTION Most difficulties faced by distributed control system HE PROTOCOLS network suite, known as Internet standard, is one of the most widespread communication designers are related to the network elements definition and T their settings, as well as checking the imposed requirements networks architectures to interconnect computer systems. by the physical network (power cables sizing and network It was created by Vinton G. Cerf and Robert E. Khan [1] in the devices). mid seventies, and has been growing since then. Currently, the main difficulty for the use of industrial The Ethernet suite protocol is the one which is now part of networks is related to the interoperability among equipment the Internet suite and is used in the data link and physical from different manufacturers. There is a great variety of equipment, cables, connectors and other elements applied to the same industrial network. [14] More than often, designers become dependent on a certain Alexandre Baratella Lugli,, is Coordinator at Industrial Automation technology due to the lack of standardization in industrial Courses at INATEL (Telecommunication Institute) COLLEGE, MG, Brazil. Ethernet networks. [14] (e-mail: [email protected]). Lúcia R. H. Rodrigues Franco, is 2President at UniRede and Distance During a project implementation, several problems may Learning Coordinator of the UFABC – Federal University of ABC/SP Brazil occur, but some of them are not perceived during the design (e-mail: [email protected]). DOI: 10.3895/S2318-45312013000100001 ISSN: 2318-4531 BRAZILIAN JOURNAL OF INSTRUMENTATION AND CONTROL, VOL. 01, No 01, NOVEMBER, 2013 2 phase due to the lack of adequate network simulation III. THE PROPOSED APPROACH resources. Here are some facts which illustrate the problem: The fulfillment to time constraints of the scheduling system, A long time for starting the plant due to some type of applied to industrial Ethernet networks ensures that, when a physical network error (inadequate cable lengths or invalid message is transferred, it must be completed before its electrical characteristics). respective expiration time (deadline time). [10] This paradigm The network logical project is incorrect (for instance, the must be respected by the transferred messages that are related scan time is not suitable for the production process), affecting to the distributed control applications, since a non-compliance all the process dynamics. may lead to a communication failure, causing the messages The side effects of using the selected technology are loss. It is of fundamental importance to establish a precedence generally not fully discussed during the network design phase relation or execution order to the messages that must be and installation. transferred on the network. [10, 11] In addition, the proposed For centralized systems, the distributed system design solution to distributed control, using the RM (Rate Monotonic) usually does not consider master controller physical scheduling technique, operates with non-preemptive messages, redundancy or the field modules redundancy, due to the where the messages can not be interrupted by another message difficulty of performing such type of analysis and the high being transferred. The cyclic messages (e.g. sensors reading cost to achieve this redundancy. and actuators states updating) and acyclic (e.g. a field module Another problem encountered by industrial network parameter or possible network fault) should be initiated and designers is the system control logic centralization at a single completed in the same execution time for deterministic point: the network master controller. Most fieldbuses have this guarantee and for a feasible performance on the industrial centralized architecture. This may cause problems to designers Ethernet network communication. [9, 11] in the case of master controller failures, for instance, the cable The proposed solution in this paper uses an off-line rupture or power supply defaults. scheduling (pre-run-time technique, type RM), with previous Figure 1 illustrates, in practice, some of the problems priority in each transferred message on the bus, which is non- mentioned above regarding a set up industrial network. The preemptive. With the scheduling table generated after the studied cases are highlighted through the use of technical running scheduler a time schedule of actions is obtained to be reports prepared by a company in the industrial networks field, [6] performed on the bus through a specified prediction time during a technical visit to a client. defined according to the transferred messages characteristics and priorities. Therefore, it can be inserted into one or more network field modules to perform the bus communication control, to guarantee the distributed control realization applied to industrial Ethernet networks. Then, the inclusion of this scheduling table in more than one field module ensures the proposed architecture operation, even in case of failure at any field module. The cyclical messages timing (information exchanges [6] Figure 1. Manufacturer factory example. between sensors and actuators on the network) uses UDP, due to the imposed timing requirements by the distributed control As a result from these technical reports, it would be useful application. [7, 8] The TCP protocol is used for acyclic to the network designer to have a graphical environment messages, because the timing requirements of the transferred allowing him to verify the configured parameters and to make information are not critical in this case. [7, 8] the required network simulations, and verifications, before The network design approach proposed in this paper uses starting the installation and the network devices configuration. RM technique [9, 10], where the scheduling task is divided into Furthermore, it is essential to guarantee to schedule that three different impl ementation levels, according to the the control messages are adequately distributed along the field prioritization of the messages transferred on the bus. modules and not concentrated on a single network location Therefore, the developed scheduler analyzes the set of (master controller). messages that need to be transferred from each field module in Some works carried out, [9], [11] and [21], have proposed, three levels, to sort the information flow on the network. At in some way, the solution to these problems. However, the the first level, the scheduler groups all messages from each solutions are not completely resolved from the designer field module in "sub-groups by priority", which are defined viewpoint and the applicability to industrial Ethernet [20] [21] according to the message priorities (three different priority networks. The papers [20] and [21] discuss a modeling levels have been proposed: from zero up to two). and control system for industrial Ethernet networks, with At the second level, the scheduler analyzes the total centralized control in the master controller network, not execution time of each module,
Details
-
File Typepdf
-
Upload Time-
-
Content LanguagesEnglish
-
Upload UserAnonymous/Not logged-in
-
File Pages6 Page
-
File Size-