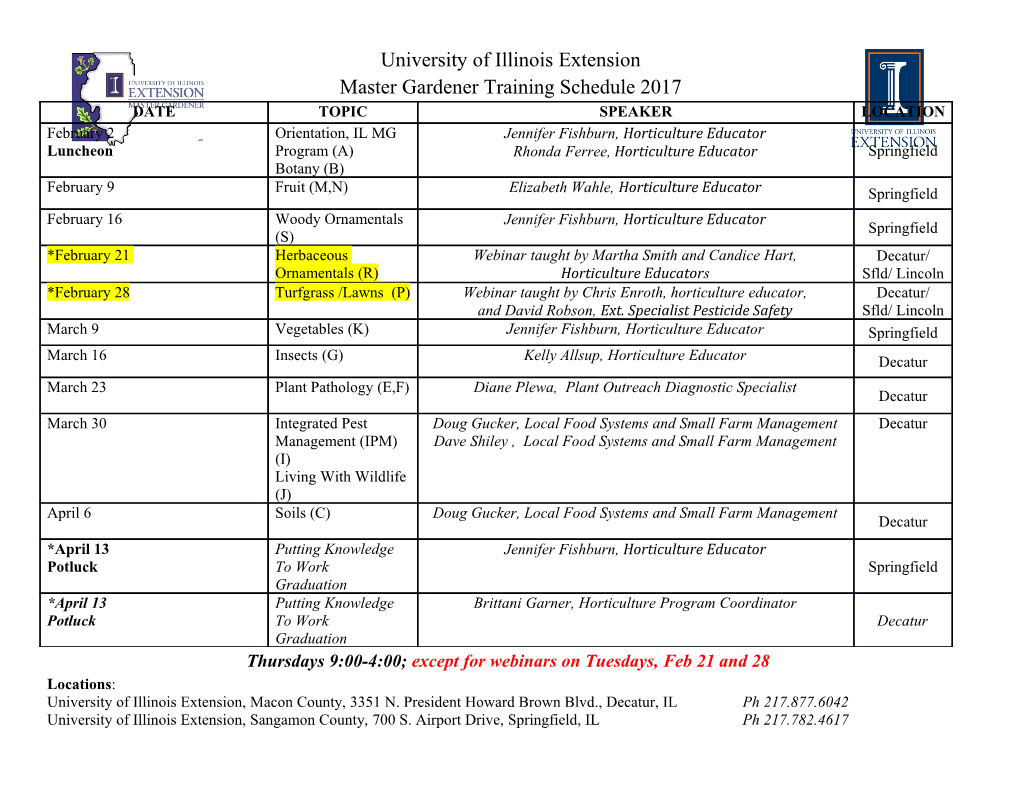
!!l ..................... ..... ..... ............... ............. ....... ......................... ... ..... ......... ...... ............. ........ ............. ...... ......... ........ .. ......... ....... ......... ..... .. ......... ..... .. ......... ..... .. ......... ....... ............. ....... ......... ....... ......... ..... .. ......... .. ......... ......... ......... ;7 .. ......... y ......... .... .. ......... ....I .... .....,. ......... .I.. ..... ...I. .... ...,....... ......... ...,... ......... ,... ......... ....I .... .....,.. .. ......... .....I.. .. .......... ........ .. ......... iuii - Published by The EPRl Center for MaterialsProduction CMP - 076 An Electric Energy Tool for High-Temperature Materials Processing Introduction Over the past 40 years, engineers I worldwide have developed many ! 1. Plasma torch materials processing applications using 2. Plasma plasma arc heaters. Early applications 3. Tundish injection chamber at low power levelsof 10 - 20 kW were 4. Tundish heating chamber for the cutting and welding of metals 5. Tundish casting chamber and for plasma spraying of metal and 6. Plasma power supply refractory powders to form protective 7. Bottom electrode coatings. These are now well-estab- 8. Controller lished commercial processes. Contin- 9. Molten steel temperature sensor ?ddevelopments are being made for 10. Ladle the surface treatment of metals (phase transformations for hardening, carburiz- ing, nitriding) and for metal overlays. Present research efforts at low powers include the synthesis of diamond films as well as the productionof supercon- ductive and engineering ceramic powders. Figure 1 Plasma Tundish Heater and ControlSystem During the 1960s plasma arc heaters were developed at power levels of500 What are Plasma Arc Heaters? hydrogen), oxidizing (oxygen) or inert kW up to35 MW for aerospace materi- (argon). als testing. Subsequent plasma heater All electric arcs are plasmas. Plasma developments have resultedin many simply refers to the presence of ionized Heaters can be designed for both low high-power applications for materials gases. Plasma arc heaters are electri- and high gas-flow rates. The gas can processing.Today, industrial-worthy cal resistance heaters where the be used to convey fine solids, liquids, plasma arc systems are available for resistive element is the electrically- or additional gases into the arc-heated extended reliable operation at high conductive partially ionized gas be- zone for physical transformations and power and current levels. Commercial tween two electrodes. Whereas chemical reactions. This controlled breakthroughs in technology include plasma arcs occurin nature as sudden flow of various gases enhances the simple physical tasks, such as heating lightning discharges, plasma arc versatility of plasma arc heaters when of molten steel in continuous casting heaters provide a continuouslycon- compared to conventional electric arc tundishes for temperature control using trolled electrical arc discharge. furnaces with "free burning arcs" and 1 - 4 MW plasma heaters. Complex no gas control features. multiphase chemical reaction systems Although the arc discharge can be th high specific energy requirements, controlled by magnetic and mechanical The core temperatureof the plasma such as ferrochromium production by means, the key design featureof arc can range from4,000 to 20,OOO"C carbon reduction of chromite ore fines, plasma arc heaters is the controlled (7,200"-36,000"F). Theworking are being processed at power levels upfeed of gas to thearc environment. temperature of the bulk gas, depending to 30 MW. The gas can be either reducing (e.g., on the gas flow ratesand theheater design, is about 2,000 - 3,O0O0C (3,600”-5,400”F). Thehigh ternpera- amperes (as high as 100,000 A with ture of the arc and the working gas graphite electrodes) and a few hundred THE PLASMA ADVANTAGE plus heat transfer at the arc root volts. The workptece is one electrode; attachment area result in heat fluxes shown as the anode (+) in Figure 2b. The unique advantages for the about 10-50 times higher than oxygen - The gas phase electrode, or cathode application of plasma arc fuel flames. (-), can be a water-cooled copper technology include: cylinder or a refractory metal button Gas environment control Most plasma heaters operate on direct (e.g., thoriated-doped tungsten),or it Gas-flow rate control current, with ”nontransferred” and/or can be a hollow graphite electrode Fine particle feed capability “transferred” arcs. For nontransferred without water cooling. The hollow 1 Hightemperature operation the gas phase is the only passage canbe used for the direct \ Highenergy fluxes working resistive element, Figure 2a. introduction of gas and fine solids into : Rapidquenching The arc can be “transferred” attaching the arc environment as shown in Figure i’ No productsof combustion directly to a workpiece (e.g., an object 5 for the reduction of chrome ore fines I to be cut, welded, heated, melted, for ferrochromium production. reacted, etc.), as shown in Figure 2b, with resistive heating of both the gas phase and the workpiecein ,series. Nontransferred arc heaters areused when it is desirable to heat the gas phase, such as for gas phase reactions (e.g., production of acetylene from natural 3as) and for countercurrent solids - gas contact in shaft heaters, melters (cupolas), and reactors (blast furnaces). These heaters typically consist c: water-cooled cylindrical copper electrodes and operateup to 2,000 amperes and 6,000 volts with high flow rates of a reactive gas. Transferred arc heaters are useful for the bulk heating of solids and melts and where the gasphase is not a 1 principal reactant but can be important ..:.:.:.:.:.: ;.?.$.:~:<*:$::::::::j:.:::::::~ ......in\...,. ,..... .. .. ., . , . I as an inert shield. The gas flow rates .. .. .. .. are typically very low which canbe important for controlling vapor phase L L reactions and condensation phenom- Figure 2a. Nontransferred Arc Figure 2b. Transferred Arc ena. Transferred arc heaters typically nperate at up to several thousand Center for Materials OTHER PLASMA AND ELECTRODELESS ARC DISCHARGES ProductionRole In 1988, CMP published “A Survey of In additionto arc discharges between electrodesit is possibleto sustain plasma Thermal Processing Research Facili- discharges by high-frequency powered induction coils. These electrodeless induction- ties“ as an aid to planning research coupled plasmas (ICP)have the unique capabilityof producing an ultraclean arc and activities. In March 1990, CMP plasma with no contamination. These systems, which can operate at atmospheric or organized the first EPRI-sponsored reduced pressures, are ideal as a heat source for chemical analysis instruments, and plasma symposium on “Industrial and also for powder treatment. Conventional Systems operate upto about 30 kW, but Environmental Applicationsof Plasma” developmental lCPs have operated on air at900 kW. attended by specialists from plasma Plasma arc discharges are typically produced at normal pressures. Plasma discharges vendors and developers, as well as also can be produced at low pressures such as the familiar fluorescent lamp. Low- from electrical utilities and industry. pressure discharge devices are in wide commercial use in microelectronic fabrication for etching patterns in integrated circuits. CMP has supported laboratory, pilot plant, and industrial scale plasma CMP’s activities have been focusedon the development of plasma arc processes activities for treating electric arc rather than on induction-coupled or low-pressure plasmas. furnace dust and specialty steelmaking dusts, smelting of silicon metal and increased steelmaking vessel(oxygen FeMn , FeCr ferrosilicon production from taconite converter, electric arc furnace)refrac- In South Africa the plasma remelting of fines, melting of aluminum scrap, tory life due to lower steeltap tempera- ferroalloy crush finesof melting / separation of aluminum from tures, ferromanganese and ferrochromiumin scrap melter dross, and the heating/ (2) improved steel quality, e.g., preven- 4 MW and 14 MW plasma furnaces, refining of steel ladle melts. In addition, tion of center segregationsfor high- respectively, was initiated in 1983. EPRl has funded the development of carbon steels such ashard-drawn wire, the plasma-assistedcupola for iron (3) higher yields due toelimination of Titanium melting and recycling of mill scale (iron strand freeze-off and lessmold powder United States-fosteredplasma technol- oxide). related product defects. ogy is used at five locations for “inert gas”- melting and remeltingof Plasma heatingof steel ladles has titanium scrap and sponge, see Figure Applications of Plasma Arcs been developed industrially on melts 3. Plasma heaters rangefrom 300 kW The plasma processing of gases, from 30 - 220 tons and heaters from 1 - to 2.25 MW. In one case Oregon liquids, and solids coversa wide range 15 MW. CMP has funded the develop- Mejallurgical Corp. melts titanium scrap of applications including both physical ment of heating and refiningof foundry and sponge using an 800 kW Retech and chemical changes with increasing ladle melts. heater to produce 6 million pounds per specific energy requirements. The year of titanium electrodes for least energy-demanding systemis that remelting. A unique cost saving of heating solids, liquids, or gases, with Melting and Remelting of High- feature of this installation is the inert no change of state. For a change of Alloy and Refractory Metals
Details
-
File Typepdf
-
Upload Time-
-
Content LanguagesEnglish
-
Upload UserAnonymous/Not logged-in
-
File Pages6 Page
-
File Size-