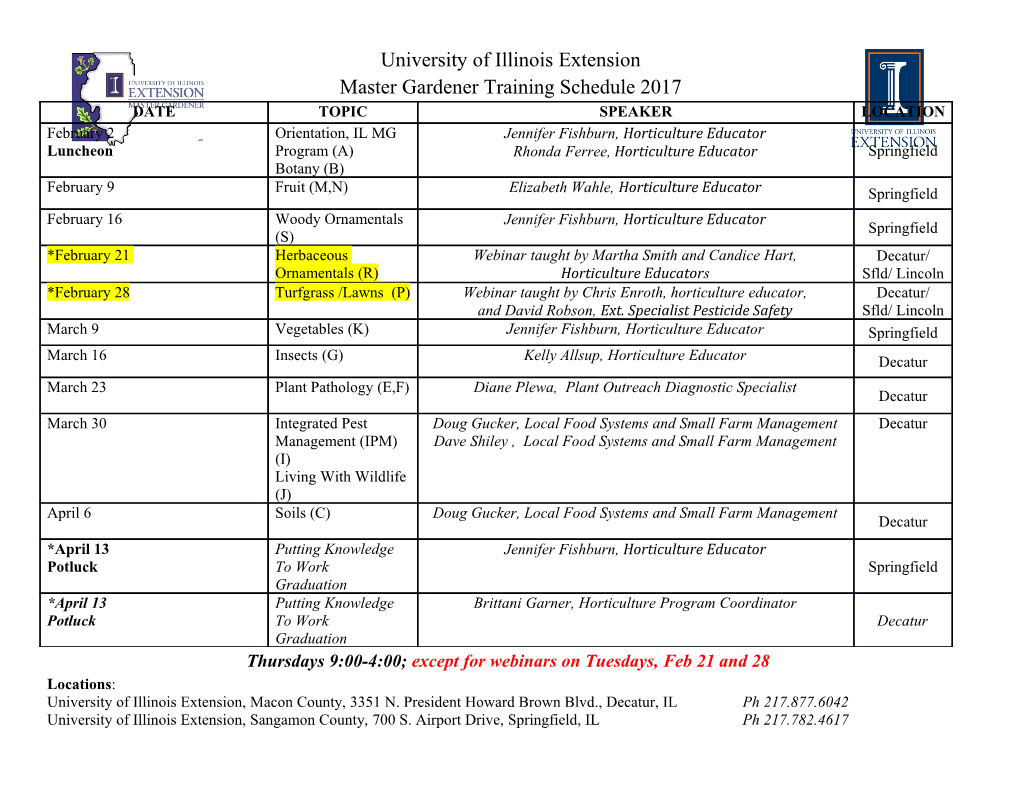
An Investigation in Gold-Plating Scaled Turbofan Engine Simulators through Means of Aerodynamic and Load Cell Thrust Measurements with Comparisons to Full-Scale Engine Results A Thesis Presented in Partial Fulfillment of the Requirements for the Degree of Master of Science in the Graduate School of The Ohio State University By Jacob T. Allenstein, B. Sci. Graduate Program in Aeronautical and Astronautical Engineering The Ohio State University 2013 Thesis Committee: Dr. Richard J. Freuler, Advisor Dr. Clifford A. Whitfield, Co-Advisor Copyright by Jacob T. Allenstein © 2013 ABSTRACT Model testing offers investigators a useful tool that can provide good insight into the aerodynamics behind full-scale engines and test facilities. Understanding the aerodynamics of a full-scale engine can help investigators update old test facilities and help design new facilities and engines. Gold-plating an engine is a process that the industry uses to compare the performance of an engine from the same family or class of engines in various facilities. The gold-plated engine can be used to determine a correlation factor of a testing facility or to determine the similarities in performance between a new or old engine to the gold-plated engine. The use of a correlation or correction factor can be used to correct a deviation in a measurement made in a test facility to bring the engine’s performance back to readings performed in a “free-air” environment. Model testing consists of the use of a simulator or scaled version of an engine that generates performance close to full-scale operation conditions. The simulator used in this study was constructed to not have any moving parts but rather be driven by a high pressure air system, providing a safe alternative to testing the full-scale engine. The objective of the study was to understand how to perform the gold-plate process to an engine simulator through the means of the aerodynamic and load cell thrust readings. The study examined the thrust that can be calculated from the exhaust mass flow of the engine simulator, or aerodynamic thrust, and compared the results to the load ii cell thrust from the load cell. This investigation will provide the framework to build and expand the knowledge of how an engine simulator works and how it can be used to understand the aerodynamics of an engine. The analysis was conducted at The Ohio State University’s Aeronautical and Astronautical Research Laboratories’ JETS facility. Two simulators went through the gold-plating process: the GE HF-120 and the GE90-B4 turbofan simulators. Each simulator used a high pressure, ejector driven system which does not require any moving parts. Both simulators were set up in a free-air environment and were tested at a variety of different pressures. The first simulator investigated was the GE HF-120 turbofan engine. The HF-120 used two types of inlet cowls: a flight cowl and a bellmouth testing cowl. The second simulator investigated was the GE90-B4 turbofan engine, which has two ejector stages: the fan and core. These tests have contributed to an improved understanding of the thrust measurements obtained from these engine simulators. These results will create the foundation of operating the simulator to verify data produced in a model scale test of a full-scale facility. The setup provided a reliable test environment for the engine simulator as seen through multiple, repeatable test runs. This knowledge and these techniques could help predict full-scale test results with use of scaled engine simulators with a higher degree of accuracy, providing investigations an inexpensive and safe environment for determining the full-scale facility’s performance. iii Dedicated to my family iv ACKNOWLEDGMENTS I would like to thank Dr. Rick Freuler for his guidance and his patience. Thank you for your dedication of time and providing me the valuable experiences out at the labs. I cannot thank you enough for your support and your help over the past few years. Thank you! To Dr. Whitfield, I want to thank you for helping me since our NASA competition. I want to thank you for all the “great opportunities” and learning experiences you have presented to me. I also want to thank all my friends; Ivan and Cara Dusper, Nick Higgins, Elliot Howell, Greg Padgett, and Zach and Jill Webster, for encouraging me to continue my education and their aid throughout my studies. A special thanks to Heather Barthelme for editing my thesis and our love/hate relationship. Also want to thank Ryan Winfree for laying down the foundation of my research and for the help in the collection of my data. Finally, I thank my Mother and Father, and my siblings; Josh, Krista, Kalley, and Brianna for their loving support in everything I do. VITA June 7, 1987 Born, Idaho Falls, Idaho, USA June 11, 2011 B.Sc., Aeronautical and Astronautical Engineering, The Ohio State University September 2011 – Present Graduate Research Associate, Mechanical and Aerospace Engineering, The Ohio State University August 2013 – Present Graduate Teaching Associate, Engineering Education Innovation Center, The Ohio State University PUBLICATIONS Whitfield, C.A., Allenstein, J.T., Freuler, R.J., “GE LML Athens Inlet 1/5th Scale Model Hardware and Testing.” The Ohio State University Aeronautical and Astronautical Research Laboratories. 15 February 2012. Whitfield, C.A., Kawecki, R., J. Roscoe, Allenstein, J.T., Freuler, R.J., “GE/ASE Caledonian 1/11.5 Scaled Test Cell Facility – Phase II.” The Ohio State University Aeronautical and Astronautical Research Laboratories. 27 February 2012. Whitfield, C.A., Kawecki, R, Allenstein, J.T., Freuler, R.J., “GE Winnipeg Icing 1/11.5 Scaled Facility.” The Ohio State University Research Foundation Project No. 60032560. The Ohio State University Aeronautical and Astronautical Research Laboratories. 5 March 2012. Allenstein, J.T., Rhoads, B., Whitfield, C.A., “From the Industry to the Student: Project Management of an Industry-Sponsored Multidisciplinary Capstone Project,” American Society of Engineering Education 2012 Annual Conference and Exposition. Allenstein, J.T. Rhoads, R., Rogers, P., Whitfield, C.A., “Examining the Impacts of a Multidisciplinary Engineering Capstone Design Program,” American Society of Engineering Education 2013 Annual Conference and Exposition. Whitfield, C.A., Freuler, R.J., Allenstein, J.T., Cochran, R., “GE Site 5D Test Cell Facility Scale Model Hardware and Testing.” The Ohio State University Aeronautical and Astronautical Research Laboratories. 24 September 2013. FIELD OF STUDY Major field: Aeronautical and Astronautical Engineering vii TABLE OF CONTENTS ABSTRACT ............................................................................................................ ii DEDICATION ........................................................................................................ iv ACKNOWLEDGMENTS .......................................................................................... v VITA ..................................................................................................................... vi LIST OF TABLES ................................................................................................... x LIST OF FIGURES ................................................................................................. xi NOMENCLATURE ................................................................................................. xiii CHAPTERS 1. INTRODUCTION ........................................................................................ 1 1.1 Background .................................................................................. 1 1.2 Objectives and Goals .................................................................. 4 2. EXPERIMENTAL SETUP ............................................................................ 6 2.1 Experimental Facility ................................................................... 6 2.2 Engine Simulators ........................................................................ 7 2.2.1 General Electric/Honda HF-120 ................................ 9 2.2.2 General Electric GE90-B4 ......................................... 12 2.3 Experimental Setup ...................................................................... 17 2.4 Experimental Equipment ............................................................. 19 2.4.1 Pressures .................................................................... 19 2.4.2 Temperatures.............................................................. 21 2.4.3 Force Measurement .................................................... 22 2.4.4 Air Supply .................................................................. 23 3. CALIBRATION AND DATA ACQUISITION ................................................. 25 3.1 Data Acquisition........................................................................... 25 3.2 Calibration.................................................................................... 26 viii 3.3 Measurement Validity .................................................................. 29 3.3.1 Measurement Uncertainty Analysis ........................... 30 3.3.2 Hysteresis Effects....................................................... 31 3.4 Data Reduction............................................................................. 34 4. RESULTS FOR THE GENERAL ELECTRIC HF-120 ................................... 37 4.1 HF-120 Engine Simulator Test Matrix and Raw Results............. 37 4.2 HF-120 Engine Simulator Induced Flow
Details
-
File Typepdf
-
Upload Time-
-
Content LanguagesEnglish
-
Upload UserAnonymous/Not logged-in
-
File Pages111 Page
-
File Size-