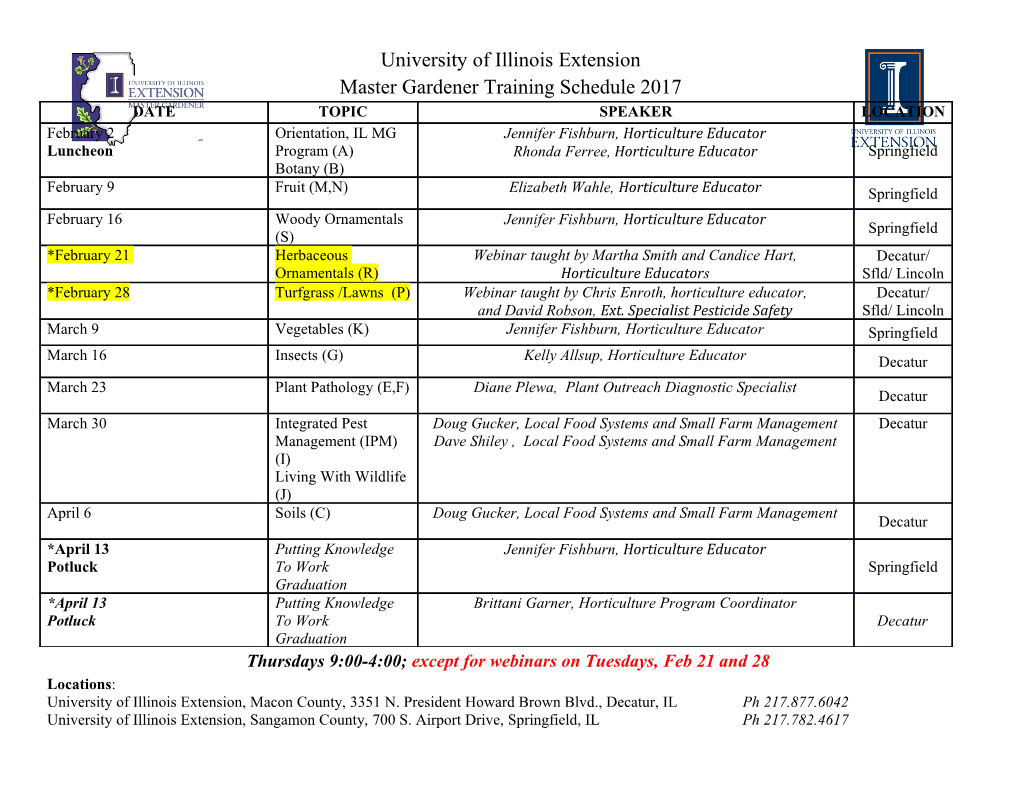
中国科技论文在线 http://www.paper.edu.cn Applied Catalysis A: General 260 (2004) 19–24 Synthesis of diphenyl carbonate by transesterification over lead and zinc double oxide catalyst Zhou Weiqing a, Zhao Xinqiang a, Wang Yanji a,∗, Zhang Jiyan b a School of Chemical Engineering and Technology, Hebei University of Technology, Tianjin 300130, PR China b School of Chemical Engineering and Technology, Tianjin University, Tianjin 300072, PR China Received in revised form 13 September 2003; accepted 1 October 2003 Abstract A new heterogeneous catalyst, lead–zinc double oxide, has been prepared for the synthesis of diphenyl carbonate (DPC) by transesterification of dimethyl carbonate (DMC) and phenol. The effects of preparation method, calcination temperature, precursor and molar ratio of Pb/Zn on the catalytic activity have been investigated. XRD, TPR and atomic absorption spectroscopy were employed for the catalyst characterization. The results show that Pb3O4 is the main active species, and that amorphous ZnO plays a role as the promoter. Under the conditions of calcination temperature of 500 ◦C and Pb/Zn = 2:1, the highest activity of the catalyst, DPC yield of 45.6%, was achieved. The reason for deactivation of the catalyst was the vanishing of Pb3O4. © 2003 Published by Elsevier B.V. Keywords: Diphenyl carbonate; Dimethyl carbonate; Phenol; Transesterification; Lead–zinc double oxide 1. Introduction of DPC was reported within 34–52% over the two best catalysts (C4H9)2SnO and Ti(OC4H9)4 [2–4]. More and Diphenyl carbonate (DPC) is used to produce many more attention has been paid to heterogeneous catalysts organic compounds and polymer materials, particularly because homogeneous catalysts are difficult both to sep- as an intermediate for synthesis of polycarbonate with- arate from products and to recover for reuse. There are out using phosgene. The methods for preparation of DPC some reports of useful heterogeneous catalysts. Akinobu include phosgenation technique, oxidative carbonylation and Takoshi [5] reported that DPC yield became 13.6 and of phenol, and transesterification of phenol and dimethyl 8.5%, respectively over mixed oxide catalysts of titanium carbonate (DMC) [1]. Owing to both the use of severely and subgroup IIIB metals, or iron and subgroup IIIB met- toxic phosgene as raw material and the formation of cor- als. Kim and Lee [6] prepared some supported oxides rosive hydrogen chloride as a by-product, the phosgenation of subgroup IIIB, IVB, VB, and VIB metals including technique will have to be eliminated soon. The oxidative (MoOx, CrOx,WOx,VOx,TiO2)/(Al2O3, SiO2, MgO, C). carbonylation of phenol is considered to be a prospective TiO2/SiO2 was considered as the best catalyst; conversion route for synthesis of DPC, but the use of noble catalyst of phenol was 37.2% and yields of methylphenylcarbonate and the low yield of DPC limit its industrialization. The (MPC) and DPC were 31.7 and 1.7%, respectively. Fu and transesterification of DMC and phenol, however, is a route Ono [7] reviewed that MoO3/SiO2 was the best catalyst most suitable for commercial production, because it gets among supported catalysts of MoO3,Ga2O, V2O5, PbO, rid of the drawbacks of the two above-mentioned routes. ZrO2,TiO2, CdO, Sm2O3,Fe2O3, CuO, but their activ- Usually, the transesterification of DMC and phenol is car- ity and selectivity are very poor. The authors [8] studied ried out in the liquid phase using a homogeneous catalyst n-Bu2SnO catalyst supported on AC, ␥-Al2O3, ZSM-5, such as an organic tin or titanium compound. The yield bentonite and SiO2. It was found that DPC yield was 17.3% over n-Bu2SnO/SiO2 catalyst, and increased to 21.8% after ◦ ∗ Corresponding author. Tel.: +86-22-26564289; the catalyst was calcined at 150 C. In this paper, an en- fax: +86-22-26564287. vironmentally friendly solid metal oxide catalyst that we E-mail address: [email protected] (W. Yanji). developed will be introduced. 转载 0926-860X/$ – see front matter © 2003 Published by Elsevier B.V. doi:10.1016/j.apcata.2003.10.024 中国科技论文在线 http://www.paper.edu.cn 20 Z. Weiqing et al. / Applied Catalysis A: General 260 (2004) 19–24 2. Experimental detector (TCD). The chromatographic column was packed with PEG20M. Quantitative analysis of the product was car- 2.1. Chemical reagents ried out with a Beifen SQ-206 gas chromatograph, equipped with a flame ionization detector (FID) and a capillary col- Several chemical reagents with AR grade were used as umn packed with PEG20M. Identification analysis of the raw materials and for preparation of catalyst, e.g. lead nitrate, reaction system was conducted on a Finnigan Trace DSQ lead acetate, zinc nitrate, zinc acetate, zinc stearate, phenol, GC-Mass spectrometer. and dimethyl carbonate. 2.2. Catalyst preparation 3. Result and discussion Catalysts were prepared by two methods: co-precipitation On the basis of the previous experiment [8], the reaction and mechanical milling. In co-precipitation, lead and zinc temperature and reaction time were determined as 180 ◦C compounds were separately dissolved in distilled water to and 8 h, respectively. In the present paper, the yield of DPC obtain 10% (wt.) solutions, and ammonia solution was di- is calculated based on phenol. luted to a concentration of 0.45 wt.%. The three solutions were added into a beaker simultaneously, then the mixture 3.1. Catalytic activity of single metal oxides was stirred for 20 min and aged for 24 h. The sedimentation was filtrated at vacuum, then dried and calcined. In mechan- The transesterification of DMC and phenol was conducted ◦ ical milling, lead hydrate and zinc hydrate were prepared at 180 C over different precursors and their single oxides. separately, then mixed at a certain ratio, and finally the sam- The result is listed in Table 1. DPC yield was 6.1% over lead ple was milled uniformly and calcined. acetate, yet the yield was less than 0.4% over the other pre- cursors. Activity of lead compounds increased after calcina- 2.3. Characterization tion, but zinc compounds showed little activity after being calcined. X-ray diffraction (XRD) measurements were conducted on a Philip X’pert MPD X-ray diffractometer using a ra- 3.2. Lead–zinc double oxide diation source of Cu K␣ with a scanning rate of 8◦/min. Atomic absorption spectroscopy measurements were carried Different factors influencing the catalytic activity of out using a Hitachi 180-80 spectrometer. Temperature pro- lead–zinc double oxide, such as calcination temperature, grammed reduction (TPR) was taken on the temperature pro- precursor, and molar ratio of lead and zinc, have been in- grammed reduction/desorption apparatus assembled by the vestigated. When Pb(NO3)2 and Zn(OAc)2 were used as authors. the precursors and the molar ratio of lead and zinc was 1:1, DPC yield varied within a calcination temperature range of ◦ ◦ 2.4. Reaction procedure 350–600 C, and reached the maximum (40.8%) at 500 C, as shown in Table 2. The reaction was carried out in a 250 ml four-neck The structure and the components of lead–zinc double round-bottomed flask equipped with a fractionating col- oxide have been characterized by means of XRD, TPR and umn connected to a liquid dividing head. Phenol (15.0 g) atomic absorption spectroscopy (AAS). Fig. 1 shows the re- and catalyst was added under an atmosphere of nitrogen. sults of XRD analyses for the lead–zinc double oxide cal- And n(phenol):n(catalyst) is 1:0.02. After the mixture was cined at different temperatures. The components and weight heated to 180 ◦C, DMC (17.0 ml) was added drop-wise. content of lead and zinc are shown in Table 2. ZnO was not During the reaction, a distillate of DMC and methanol was detected in most samples tested by XRD, but the analysis of collected for analysis. AAS shows that the Zn content was about 9%. The result indicates that ZnO may exist in microcrystalline structure or 2.5. Product analysis amorphous state. Additionally the fact that the temperature of the reduction peak of the catalysts increased with calci- Distillate of DMC and methanol was analyzed on a Beifen nation temperature (Fig. 2) shows that crystal form of the Model 3420 gas chromatograph with a thermal conductivity catalyst may become more uniform. Table 1 Catalytic activity of different precursors and their single oxides 1 2 3 4 PbO PbO PbO2 ZnO ZnO Pb(NO3)2 Pb(OAc)2 Zn(NO3)2 Zn(OAc)2 Zinc stearate 9.5 9.3 10.1 0.38 0.48 0.36 6.1 0.02 0.13 0.22 ◦ Precursor: 1, Pb(OAc)2; 2, Pb(NO3)2; 3, Zn(OAc)2; 4, zinc stearate; Calcination temperature: 500 C. Reaction conditions: n(phenol):n(DMC):n(catalyst) = 1:1.25:0.02; reaction temperature 180 ◦C; reaction time 8 h. 中国科技论文在线 http://www.paper.edu.cn Z. Weiqing et al. / Applied Catalysis A: General 260 (2004) 19–24 21 Table 2 Catalytic activity and results of XRD and atomic absorption spectroscopy of the catalysts calcined at different temperatures Calcination temperature (◦C) Content of Pb and Zn in catalyst Component Y (DPC) (%) Lead (wt.%) Zinc (wt.%) 350 65 8.5 Pb10O7(NO3)6–Pb3O2(NO3)2 23.2 450 66 9.0 ZnO–ZnxPb1−xO–Pb(OH)2 35.6 500 69 8.9 Pb(OH)2–Pb3O4–PbO1.44 40.8 550 66 8.6 Pb3O4 24.0 600 74 9.2 Pb3O4–Pb3O2CO3 22.5 Catalyst precursor: Pb(NO3)2–Zn(OAc)2, n(Pb)/n(Zn) = 1:1, reaction conditions are the same as in Table 1. When the molar ratio of lead and zinc in precursor was promoter, though it has little activity.
Details
-
File Typepdf
-
Upload Time-
-
Content LanguagesEnglish
-
Upload UserAnonymous/Not logged-in
-
File Pages6 Page
-
File Size-