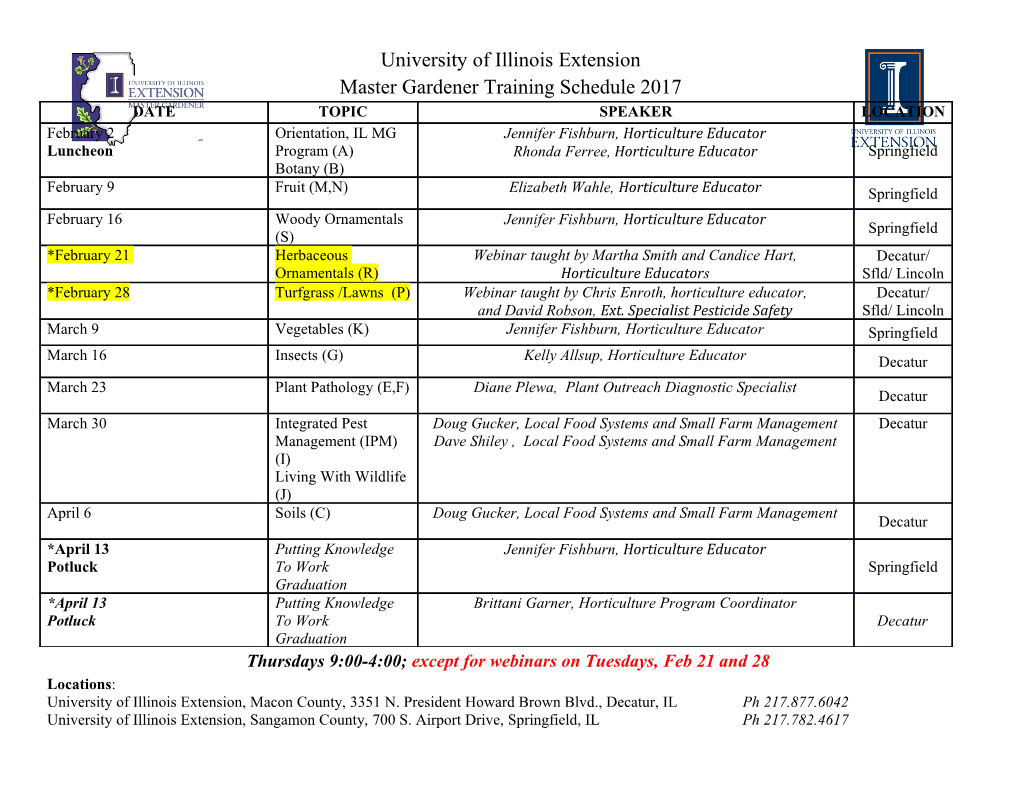
Table of Contents 1 Introduction………………………………………….………………………………………………………..…… .4 2 What is a checkweigher………………………….…………………………………………………………..…5 2.1 Belts of a checkweigher………………………….…………………………………………………………..…6 2.1.1 Infeed belt………………………….……………………………………………….……………………………..…6 2.1.2 Reject belt………………………….……………………………………………..………………………………..…6 2.1.3 Weigh belt………………………….………………………………………………………………..……………..…6 3 Uses of a checkweigher…………………………...…………………………………………………………..…7 3.1 Regular………………………………………………………………….…………………………………..…………..7 3.2 Statistical………………………………………….………………………………………...……….………….…..…7 4 Importance of checkweighers…………………………………………………………………………………8 4.1 Keeps Brand Secure……………………………………………………………………………………………..…8 4.2 Meets Regulatory Norms……………………………………………………………………………………...…8 4.3 Improves Plant Efficiency………………………………………………………………………………………8 4.4 Enables Proper Weight Control……………………………………………………………………………….8 4.4.1 Meet Specifications………………………………………………………………………………………………...8 4.4.2 Underweight Net Content…………………………………………………………………………………….…8 4.4.3 Overweight Net Content…………………………………………………………………………………………9 4.4.4 Contaminants…………………………………………………………………………………………………………9 4.4.5 Missing Elements……………………………………………………………………………………………………9 4.4.6 Classification…………….……………………………………………………………………………………………9 4.4.7 Control………………………………………………………………………………………………………………..…9 4.4.8 Dismal Products…………………………………………………………………………………………………..…9 4.4.9 Lot Deviation……………………………………………………………………………………………………….…9 4.4.10 Missing Secondary Components…………………………………………………………………………...…9 5 Regulatory Norms on Net Contents…………………………………………………………………………9 6 Legal Actions Against Erring Companies………………………………………………………………….9 7 How does a checkweigher work…………………………………………………………………………….10 7.1 How a checkweigher weighs products…………………………………………………………………..10 7.2 Movement of Products ….………………………………………………………………………..........…….......10 7.3 Rejection of Products…………………………………….……………………………………......................10 8 Weighing Accuracy……………………………………………………………………………...........................11 8.1 Checkweigher Accuracy…………………………………………………………………………….................11 8.2 Importance of Weighing Accuracy…………………………………………………………………………11 8.3 Ways to Achieve Weighing Accuracy……………………………………………………………………..11 9 Difference between an Automatic Checkweigher and a Static Scale….……………………..11 10 How to keep the checkweigher performing to its best……………………………………………12 10.1 Belts and chains……………………………………………………………………………………………………12 10.2 Mechanical alignment…………………………………………………………………………………………..12 10.3 Rejectors and photo eyes……………………………………………...………………………………………12 10.4 Transfer of products…………………………………………………………….………………………………12 10.5 Product separation……………………………………………………………………………………………….12 10.6 Calibration…………………………………………………………………………………………………………...12 10.7 Product specifications…………………………………………………………………………………………..13 10.8 Grey Zone Check…………………………………………………………………………………………………..13 10.9 Reports………………………………………………………………………………………………………….........13 10.10 Alarms………………………………………………………………………………………………………………....13 11 Do’s and Don’ts of Checkweighers…………………………………………………………………………13 11.1 Do’s of checkweighers………………………………………………………………………………………..…13 11.2 Don’ts of checkweighers……………………………………………………………………………………….13 12 Types of Packages………………………………………………………………………………………………...14 13 Customizing a checkweigher…………………………………………………………………………………14 14 Multi-Lane Checkweigher Solutions Are Efficient…………………………………………………...14 15 IP65 Washdown Requirements…………………………………………………………………………..…15 16 How To Check Whether A Checkweigher Is In Top Condition…………………………………15 17 How To Choose A Reliable Checkweigher………………………………………………………………16 17.1 Solutions that match the problem accurately…………………………………………………………16 17.2 Do not avoid problems…………………………………………………………………………………………16 17.3 Value instead of mere attractive features………………………………………………………………16 17.4 Best technology provider…………...…………………………………………………………………………16 17.5 Great in promise and delivery both……………………………………………………………………….17 17.6 Quality and security……………………………………………………………………………………………...17 17.7 Avoid generalists………………………………………………………………………………………………….17 17.8 Checkweigher literature……………………………………………………………………………………….17 17.9 Living up to the promise………………………….……………………………………………………………17 17.10 Ease of use………………………………………………………………………………...…………………………17 17.11 Display functions……………………………………………………………………………………………….…18 17.12 Ease of connectivity…………………………………………………………………………………………...…18 17.13 Fieldbus network needs……………………………………………………………………………………..…18 17.14 OPC Requirements…………………………………………………………………………………………….…18 17.15 Fill quantity checking……………………………………………………………………………………………19 17.16 Product handling………………………………………………………………………………….………………19 17.17 Additional weight zones………………………………………………………….……………………………19 17.18 Data security…………………………………………………………………………………….…………………19 17.19 Traceability…………………………………………………………………………………………………………20 17.20 Data handling flexibility…………………………………………………………………………….…………20 17.21 Secondary functions…………………………………………………………………….………………………20 17.22 Statistics functions…………………………………………………….…………………………………………20 17.23 Program details……………………………………………………………………………………………………20 18 Checkweigher feedback system……………………………………………………………………………..20 19 Data management on cloud and its analysis…………………………………………………………...21 20 Checkweigher Market Trends………………………………………………………………………………..21 20.1 Strain gauge technology-based automatic checkweighers will become popular………21 20.2 EMFR technology-based automatic checkweighers will grow better in global market ……………………………………………………………………………………………………………21 20.3 Pharma industry will register the highest demand for automatic checkweighers…….21 20.4 APAC will be the fastest-growing market for checkweighers…………………………………22 21 Future of checkweigher……………………………………………………………………………………...22 References………………………………………………………………………………………………..…………………………233 3 Introduction A checkweigher is one of the most important elements of the production process. It helps you with ensuring regulatory compliance, improve productivity, increase profits, avoid costly product giveaways, and meet consistent results. Prompt Equipments brings to you this white paper that explains how a checkweigher can simplify your production process and bring you better profits. In this white paper, we address the advantages of checkweighers, their varied uses, working pattern, and tips on selecting the right checkweigher for your business. We also take a look at the quality control aspects, issue of product giveaways, operational efficiencies, and product consistency. With the advancements in technology, a checkweigher can help you understand in minutes if your products meet the specifications listed on the label. These include product weight and components. Furthermore, production data helps you in making your processes efficient to achieve the highest standards. Browse through this whitepaper to understand how a reliable checkweigher can give you quick and accurate packaging and achieve the desired results. 2 What is a checkweigher? Checkweighers are systems that help in weighing items when they pass through a production line. They also classify items according to their predefined weight zones. When the items do not meet the defined classifications, checkweighers sort or eject them accordingly. A checkweigher will ensure that it weighs all of the items on a production line. Many sections comprise a physical checkweighing system. They include scale section, infeed section, discharge section, computerized control, and rejector or line divider. It is common to have different checkweighers and components based on their usage. The other factors that influence the design of a checkweigher include the surrounding environment and the types of an item being weighed. When it comes to an automatic checkweigher, there are a series of conveyor belts. These checkweighers are thus known as belt weighers, dynamic scales, conveyor scales, in-motion scales, and in-line scales. They are known as check scales in filler applications. 2.1 Belts of a checkweigher A checkweigher usually has three belts. Here is an overview of them: 2.1.1 Infeed belt: It changes the speed of packages if they need to be brought down or up to the desired speed for weighing. It also acts as an indexer to create a necessary gap between items that ensure optimal weighing distance. The positioning of items happens through special chains or belts. 2.1.2 Reject belt: When any package does not meet the tolerance levels, it gets removed from the conveyor through the reject belt. The reject function depends on the application as well. Heavy items require radial or linear actuators, while smaller products need only an air-amplifier to blow them away. In the case of fragile products, they get dropped from the belt to slide easily into another conveyor or bin. 2.1.3 Weigh belt: They get mounted on a weight transducer. It can be a servo-balanced, strain-gauge, or split-beam load cell. In the case of old machines, the belt might get paused before the weight measurement. This directly affects the throughput and line speed. When it comes to high-speed precision scales, EMFR (electromagnetic force restoration) load cell becomes relevant. When the inductive coil gets charged, the weigh bed gets floated in an electromagnetic field. Vibrating wire load cells and strain gauges are other technologies used here. To ensure an accurate weight reading, the built-in computer needs multiple weight readings from the transducer. The next critical factor here is calibration. Lab products not in motion. When in motion, there scales can usually weigh objects
Details
-
File Typepdf
-
Upload Time-
-
Content LanguagesEnglish
-
Upload UserAnonymous/Not logged-in
-
File Pages20 Page
-
File Size-