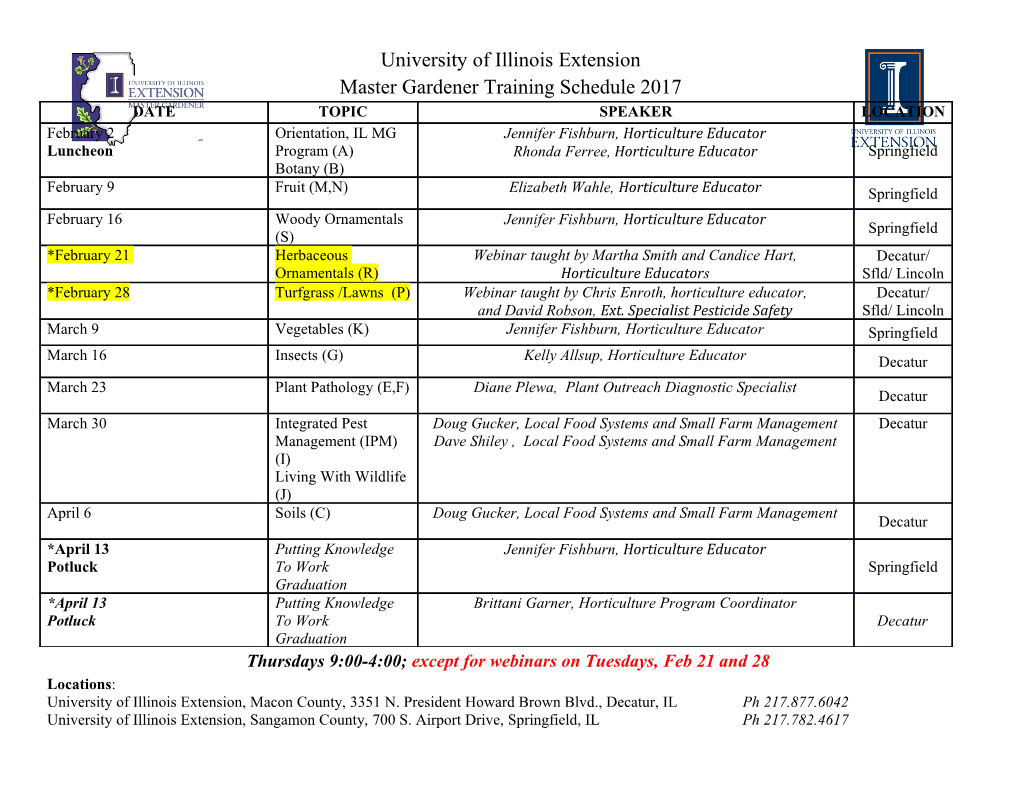
SUMMARY OF EXPERIMENTAL RESULTS FOR CERAMIC BREEDER MATERIALS N.Roux - CEA/C.E Saclay (France) G.Hollenberg - Battelle, PNL - Richland (USA) C.Johnson - ANL - Argonne (USA) K.Noda - JAERI - Tokai-Mura (Japan) R.Verrall - AECL Chalk-River (Canada) Abstract Lithium containing ceramics were quickly recognized as promising tritium breeding materials for fusion reactor blankets owing, in particular, to their safety advantages. Relevant material properties were investigated to further evaluate their suitability. An extensive R&D program complemented a conceptual blanket design activity either for near term machines or for power reactors. All aspects were addressed: fabricability, overall properties (baseline, thermal, mechanical), compatibility with structures and beryllium, tritium release characteristics, irradiation behavior, activation, reprocessing and waste disposal issues. As a result of this investigation, the lithium containing ceramics are considered to be excellent tritium breeding materials. I. Introduction In the development of tritium breeding blankets for fusion reactors the lithium containing ceramics were quickly recognized as promising tritium breeding materials. Their excellent thermal stability and chemical inertness indicate favorable safety characteristics which is a principal attribute of fusion power. Further, no MHD effect is to be feared using these compounds. An extensive international R&D program was established to confirm the suitability of these attractive materials. Issues closely related to the primary functions of the blanket, i.e., tritium breeding, tritium release, and energy conversion were addressed. Properties characteristics necessary for design analysis, for assessment of blanket concepts performance, lifetime, reliability, and safety were investigated. Thus, the research programs focused on fabrication, properties measurements, compatibility with other blanket materials, tritium release behavior, irradiation behavior, activation characteristics, reprocessing, and waste disposal issues. As a result of this international collaboration, lithium oxide and the ternary ceramics (lithium-aluminate, zirconate, silicate and titanate) were identified as promising candidates. The ceramic breeder research complemented conceptual blanket design activities. Two configurations of ceramics were considered, namely, sintered bodies and pebble beds. Following the lead of nuclear fission industry, blanket concepts using ceramics in pellet form were naturally envisaged. Thus, the EU DEMO BIT blanket concept is featured by rows of breeder modules containing annular LiA102 or Li2ZrO3 pellets.f I]. The pebble bed concept option is attractive as it partially alleviates cracking concerns. Also, loading of pebbles into complex geometries can be easier than with pellets, and intimate mixing of ceramic breeder and neutron multiplier can be facilitated by mixing pebbles of the two materials. For example, in the latest version of the EU DEMO BOT design pebbles of beryllium and Li4SiO4 are used. The larger 2 mm beryllium pebbles fill about 60% of the bed space. Spaces between the pebbles are filled with a mixture of 0.1 - 0.2 mm pebbles of Li4SiO4 and beryllium [2]. Likewise, the Japanese concept for ITER considers a layered pebble bed consisting of Imm Li2O pebbles separated from beryllium pebbles [3]. Blanket designs considered a lithium ceramic as a first option based upon its attractive properties. Complementary materials research developed the necessary data base and optimized the property characteristics as appropriate. Indeed, several properties of ceramics can be adjusted through material tailoring. 2. Experimental Results and Performance Analysis Experimental results recalled in this section illustrate the breadth of knowledge acquired and highlight the excellent performance of ceramic breeders. 2.1. Fabrication Fabrication of ceramic materials represents a determining step as it governs their performance. Fabrication includes preparation of powders and shaping to the required forms, i.e., pellets, or plates, and pebble beds. Pellets are porous, typically 75-80% T.D., in order to ease tritium release whereas pebbles are dense and porosity is that of the bed. Bed porosity can be adjusted through the number of pebble sizes and size ratios. The importance of microstructurefgrain size, density, pore morphology) and impurities on properties and performance has long been recognized. Thus, there is a general trend for fine materials as early in-situ tritium release experiments indicated their better tritium release performance. In addition, they are expected to exhibit better mechanical behavior. Impurities should be kept at the lowest level as they can have an adverse effect on properties such as compatibility behavior and activation characteristics. Several preparation methods using liquid or solid routes were worked out and yielded powders with satisfactory purity levels [4-17]. Batch scale production C10-I00 Kg)was easily accomplished at KfK, Ceramics Kingston. Uranium Pechiney, and Temav. Likewise, fabrication into the required configurations was successfully accomplished using well proven processes in the ceramic industry in general and in the nuclear fission industry in particular. Scalability of the fabrication processes was explored. For example. L1AIO2 pellets prototypical of the first row breeder modules of the EU DEMO BIT concept were produced by cold uniaxial pressing and sintering by Temav/ENEA [18]. The pellets fulfill the micro structural specifications as defined in the material research, i.e.. - 0.5 |im grain size and 80% T.D and the geometrical specifications optimized in the design work, i.e., annular pellets with an aspect ratio (outside/inside diameter) of 1.8. Several hundreds of pellets were fabricated for laboratory tests and irradiation experiments. Likewise, Li2ZrO3 BIT pellets were produced in batches of hundreds by Uranium Pechiney [19,20] by uniaxial pressing of a spray dried Li2ZrO3 powder and sintering. Adjusting the process parameters allowed spanning the 75 - 85% T.D range while maintaining the grain size at -1 |im to preserve tritium release behavior. The process was transposed to the fabrication of LiAlCn pellets too. Fabrication of Li4SiO4. Li2ZrO3, and Li2O pebbles was successfully accomplished and scaled up to batch level [15.21-231. Thus. 10 Kg batch quantities were produced of a) 1.2 mm Li?ZrO3 spheres at AECL by extrusion, tumbling, and sintering, b) 0.4 - 0.6mm and 0.1 - 0.2 mm Li4SiO4 pebbles at Schott Glaswerke Mainz using a melt spraying process, c) 1 mm Li2O spheres at Kawasaki Heavy Industries using a rotating granulation method, and d) Li2TiO3 spheres at AECL. To date, fabrication scaleup has not raised any major problem, however, when industrial quantities become necessary further development will be required and sufficient lead time will have to be provided. Attention must be paid to storage of the finished product as ceramic breeders, especially Li2O, are sensitive to H2O and CO2 contamination. Irreversible alteration of the materials may result in degradation of material performance. In parallel, improvement of material properties was pursued through composition tailoring and micro structural tailoring. For example.'a) improvement of Li4SiO4 spheres mechanical stability was obtained by the addition of SiO2 [24]. b) lowering tritium release temperature of LiAlCo was obtained by Si substitution on the LiAlCn lattice (25], and c) thermal cycling performance of Li2ZrC>3 pellets was enhanced by density adjustment [20]. 2.2 Properties characteristics A wide spectrum of properties characteristics necessary for blanket design analysis were determined. An overview is given here. Lithium atom density, which has an impact on tritium breeding ratio (TBR) and lithium burnup at end-of-life should be as high as possible. In this respect L12O is the most attractive ceramic. However, this factor is not as critical as previously thought since there is evidence that beryllium neutron multiplier and 6Li enrichment are necessary to achieve a TBR greater than unity. DEMO blanket designs do achieve a TBR > 1 even with ternary ceramics. Stability of the lithium ceramics at high temperature is obviously attractive from a safety perspective. In addition, the capacity for blanket operation at higher temperatures is beneficial to thermal efficiency. Melting points for candidate ceramics are all above 12000C indicative of good thermal stability. High temperature phases are considered so that physical changes cannot occur during operation. Vapor pressures of the compounds and their constituents are sufficiently low at the temperatures of interest so that no chemical change can occur either. Total panial pressures over the ceramic remain below 10"- Pa at anticipated blanket operating temperatures and even under limited upside transient conditions ensuring no significant material transport by the purge gas . Thermal properties, i.e.. thermal conductivity and linear thermal expansion, and their dependencies on temperature and. for the former, on microstructure were determined. Thermal conductivity of monolithic lithium ceramics is relatively low. in the range of 0.8 to 3.5 W/mK at 600°C for materials at 80% T.D. and could be'a drawback were it not for the skill of designers at accounting for this property in the design process. Pebble bed thermal conductivity and heat transfer coefficients between the walls and the pebble bed are important because they determine the operating temperatures and
Details
-
File Typepdf
-
Upload Time-
-
Content LanguagesEnglish
-
Upload UserAnonymous/Not logged-in
-
File Pages17 Page
-
File Size-