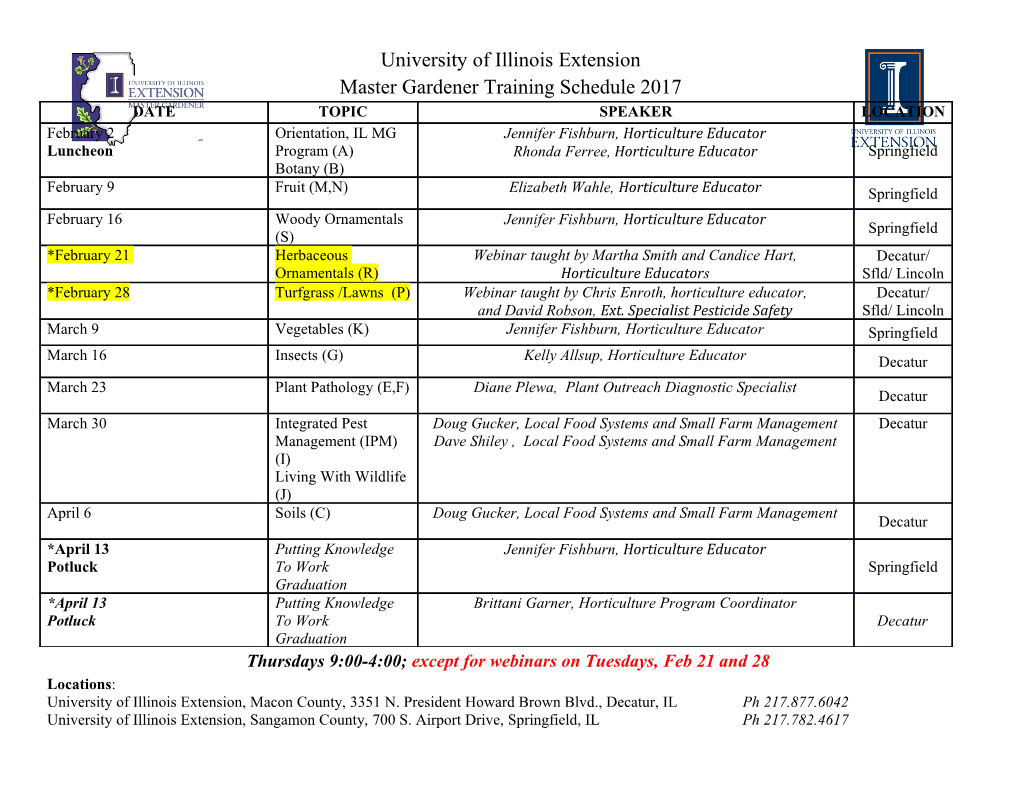
Indian Journal of Textile Research Vol. 3, December 1978, pp. 124-128 \ ...-' Preparation of Chlorendic Acid Based Polyester Resins S.K. GUPTA Materials Group, Vikram Sarabhai Space Centre, Trivandrum-22 & M. KRISHNAN & R.T.THAMPY Shri Ram Institute for Industrial Research,Delhi 110007 Received 22July 1978;accepted 5 November 1978 Four polyesters were prepared by stepwise condensation of isopbthalic acid, cblorendic acid and maleic anhydride with propylene glycol using p-toluenesulpbonic acid as catalyst and xylene as entrainer. The quantities of maleic anbydride and propylene glycol used were 1 and 2.2 moles respectively and tbe molar ratios of cblorendic acid to isopbtbalic acid were 0.2: 0.8. 0.4: 0.6, 0.6: 0.4 and 0.8:0.2 for tbe four polyesters prepared. The polyesters obtained bad better colour and relatively more uniform distribution of cblorendic acid over tbe polymer cbain compared to the polyester made in one step. They were crosslinked using 30% by weigbt of styrene and were cbaracterized tbrougb the determination of viscosity, gel time, peak exotherm and acid value. They were evaluated by measuring viest softening point, beat distortion temperature, rate of flammability and rate of bydrolysis. The data reveal that the polyester obtained using chlorendic acid and isopbthalic acid in molar ratio 0.6:0.4 is tbe best among the four polyesters prepared. In an ear.lierwork 1 on chlorendic acid based polyesters Isophthalic acid-Commercial isophthalic acid reported from this institute, Gupta et al.l identified the having melting point 352°C and purity 98% was used. factors which contribute to thermal stability, flame The impurity was terephthalic acid. resistance and chemical resistance by comparing Preparation of polyester based on chlorendic acid and chlorendic acid based polyesters with commercial isophthalic acid by one step condensation-To a 1 litre polyesters. Gupta et al.l did not discuss the selection of three -necked round bottomed flask, fitted with a Dean method for preparing chlorendic acid based polyesters and Stark apparatus and condenser, thermometer and did not evaluate properties like thermal stability, pocket and a gas inlet, were added isophthalic acid flame resistance and chemical resistance thoroughly. (83 g, 0.5 mole), chlorendic acid (195g, 0.5 mole), maleic Studies2-6 were also conducted at this institute on the anhydride (98 g, 1 mole), propylene glycol (167 g, 2.2 synthesis of polyesters having the desired combination mole), p - toluenesulphonic acid (2 g) and xylene (100 of properties like chemical resistance, heat and flame ml).The mixture was refluxed at 140°Cin an oil bath in resistance, dimensional stability, good mechanical a stream of carbon dioxide and 36 ml of water of properties, high energy radiation stability and esterification was removed by Dean and Stark insulating property. This work necessitated thorough apparatus under vacuum in CO2 atmosphere. The investigation of these aspects in order to meet the reaction mixture was heated at 180-190°C for 90 min technical challenge posed by several strategical under 50 mm Hg pressure in a stream of CO2, until the applications. In this paper, the results of studies arrived required acid number was reached. A black mass at by modifying the methods of preparing chlorendic insoluble in styrene was obtained. acid based unsaturated polyesters, their characteri• Preparation of polyester 1 based on chlorendic acid .. zation and evaluation with respect to vicat softening and isophthalic acid-To a 1 litre three-necked round point, heat distortion point, flame resistance and bottomed flask, fitted with a Dean and Stark apparatus hydrolytic stability are reported. and condenser, thermometer pocket and a gas inlet were added isophthalic acid (132.8 g, 0.8 mole), Materials and Methods propylene glycol (129.0 g, 1.7 mole) and p • Chlorendic acid-Chlorendic acid supplied by toluenesulphonic acid (0.5g).The mixture was refluxed 'Hooker Chemical Corp. Ltd, U.S.A. was used. It had at 160°C in an oil bath in a stream of carbon dioxide melting point (sealed tube) 208-210°C and melting and 28.6 ml of water of esterification was removed by point (open tube) 230-235°C, as it gets converted to Dean and Stark apparatus. After this chlorendic acid anhydride in open tube. Its purity was 99.5%. (78 g, 0.2 mole), propylene glycol (32 g, 0.41 mole) and 124 I GUPTA et al.: PREPARATION OF CHLORENDIC ACID BASED POLYESTER RESINS xylene (100 ml) were added to the flask and the esterification was collected. Then maleic anhydride (98 temperature was brought to 140°C; 7.2 ml water of g,·l mole) was added to the resulting solution and the esterification was collected. Then maleic anhydride (98 temperature was again raised to 140°C; 18 ml water of g, 1 mole) was added to the resulting solution and the esterification was removed. Xylene was removed ~d temperature was again brought to 140°C; 18 ml water polycondensation was carried out to give a base resin of esterification was removed. Xylene was removed of the required acid number. This resin (70 g) was under vacuum in CO2 atmosphere. The reaction mixed with sytrene 00 g) as above. mixture was heated at 180-190°C for 90 min under 50 l)etermmation of gel time and peak exotherm-A test rom Hg pressure in a stream of CO2, until the required tube (19 x 72.5mm) was filled with the resin containing acid number was reached. This resin (70 g) was mixed 1% benzyol peroxide to a height of 3 cm. The test tube with styrene (30 g)in the presence ofO.02%p-tert.-butyl was placed In a constant temperature bath (180°C).The' catechol, 0.02% UV light absorber and 0.005% SPI gel tittle, which is the time interval for the hydroquinone. temperature ofthe resin to rise from 150°to 190°F was noted. The Peak isotherm values obtained are gi~ in Preparation of polyester 2 based on chlorendic acid Table 1. and isophthalic acid-A mixture of isophthalic acid Determination of acid value1-About 2.5 g polyester (99.5g, 0.6 mole), propylene glycol (99 g, 1.3mole) and resin was dissolved in 50 ml benzoyl alcohol. This p-toluenesulphonic acid (0.5 g) was refluxed at 160°C solution was titrated against standard alcoholic KOH and 21.6 ml water of esterification was removed as using methyl red as indicator. The acid value w~ above. Mter this, chlorendic acid (156 g, 0.4 mole~ calculated as follows. propylene glycol (64 g, 0.82 mole) and xylene (100 mIl were added to the flask and the temperature was again Acid value 56.1 x NV brought to 140°C; 14.4 ml water of esterification was W collected. Maleic anhydride (98 g) was added to the resulting reaction mixture and the temperature was where N is the normality of alcoholic KOH; V, the -again raised to 140°C; 18.0 ml water of esterification volume (mI) of KOH used; and W, the weight of the was removed. Xylene was removed and the. resin taken. polycondensation was carried out to give a base resin The results are given in Table 1. 7()01o 1 of the required acid number. This resin (70 g) was Determination of viscosity2- The viscosity of mixed with styrene (30 g), as described earlier. solution of resin in styrene was determined with the Preparation of polyester 3 based on chlorendic acid help of a Gardener tube. In this case, the Gardener tube and isophthalic acid-A mixture of isophthalic acid was filledwith the syrupy resin up to the lower mark on l (66.4 g, 0.4 mole), propylene glycol (64.5 g, 0.85 mole) it. It was corked up to the upper mark and was kept and p-toluenesulphonic acid (0.25 g) was refluxed at vertically in a thermostat maintained at 30°C.The tube 160°C and 14.4ml water of esterification was removed was inverted and the time taken for the air bubble to as described earlier. Mter this, chlorendic acid (234 g, come up was recorded. Corresponding to this time, the 0.6 mole), propylene glycol (96 g, 1.26mole) and xylene viscosity of the resin was noted from the Gardener (150 ml) were added and the mixture was heated to graph. The results are given in Table 1. 140°C; 21.6 ml water of esterification was collected. Rate of hydrolysis of base polyester resins2-Ten Maleic anhydride (98 g, 1 mole) was added .to the flasks of 100ml capacity were charged with 0.5 g of the resulting solution and the mixture was again refluxed base resin each and were clamped in a thermostat at 140°C; 28 ml water of esterification was removed. maintained at 50°C. To each flask, 10 mI of a sodium Xylene was removed and polycondens{ltion was done hydroxide solution previously heated to sooC was to get the polyester of the required a~id number in the added with constant _shaking. Mter known time/ same manner as above. This resin (70g)was mixed with intervals, the flasks were taken out and an excess of a styrene (30 g) as described earlier. standard suIphuric acid solution was added to stop the Preparation of polyester 4 based on chlorendic acid reaction. The excess of acid left was back titrated and isophthalic acid-In the same manner as above, a against standard alkali. From the amount of alkali mixture of isophthalic acid (33.2g, 0.2 mole),propylene consumed to hydrolyse the resin, the rate of hydrolysis glycol (32.25 8, 0.425 mole) and p-toluenesulphonic was determined.
Details
-
File Typepdf
-
Upload Time-
-
Content LanguagesEnglish
-
Upload UserAnonymous/Not logged-in
-
File Pages5 Page
-
File Size-