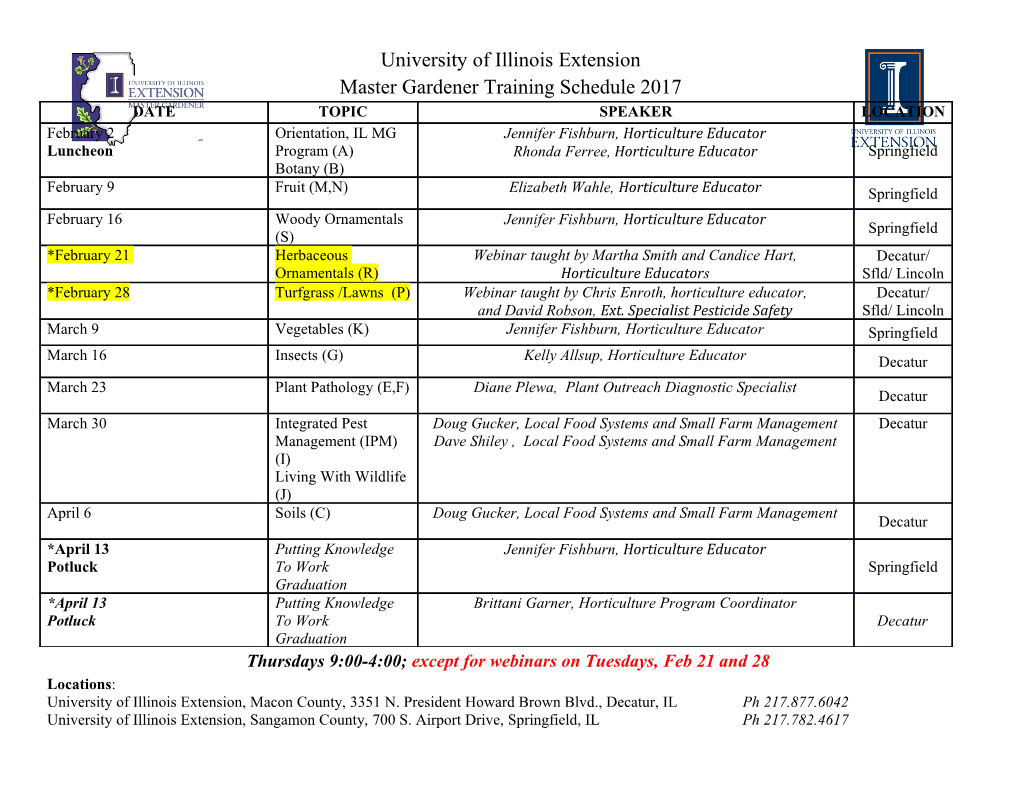
NBSIR 75-757 A TECHNIQUE FOR THE MEASUREMENT OF FLASH FIRE POTENTIAL OF POLYMERIC MATERIALS James E. Brown and John J. Comeford Center for Fire Research Institute for Applied Technology National Bureau of Standards Washington, D. C. 20234 December 1975 Progress Report Feb. 1 - Aug. 31, 1974 Sponsored in part by: Department of Transportation Federal Aviation Administration National Aviation Facilities Experimental Center Atlantic City, N. J. 08405 U.S. DEPARTMENT OF COMMERCE, Rogers C.B. Morton, Secretary James A. Baker, ill, Under Secretary Dr. Betsy Ancker- Johnson, Assistant Secretary for Science and Technology NATIONAL BUREAU OF STANDARDS, Ernest Ambler. Acting Director CONTENTS Page LIST OF TABLES iv LIST OF FIGURES v 1. INTRODUCTION 1 2. EXPERIMENTAL 3 2.1. Materials 3 2.2. Flash-Fire Cell 3 2.3. Pyrolysis Rate Apparatus 3 2.4. Procedure - Flash-Fire Cell Experiments 4 2.5. Procedure - Evolution Rates of Pyrolysis Products . 4 3. RESULTS AND DISCUSSION 4 3.1. Flash-Fire Cell Experiments 4 3.2. Rate of Pyrolyzate Evolution 7 4. CONCLUSION 10 5. ACKNOWLEDGEMENTS 11 6. REFERENCES 11 iii LIST OF TABLES Page Table 1. Properties of Polyurethane Foams 13 Table 2. Results of Pyrolysis with Furnace at 500 °C and Conditions of the Flash-Fire Cell at the Initial Flash Fire for Sample No. 16. 14 Table 3. Pyrolysis of Polyurethane No. 16 at Low Temperatures Where Flash Fires Were Not Observed 15 Table 4. The Results at the Initial Flash Fire of a Fire Retarded Foam, No. 42 and Unretarded Foams No. 18 and 8 When Pyrolyzed With the Furnace Preset to 500 °C 16 Table 5. Minimum Weights of Foams for Production of Flash Fires In the Flash-Fire Cell When the Pyrolysis Furnace was Preset at About 500 °C 17 iv LIST OF FIGURES Page Figure 1. Schematic of Flash-Fire Cell 18 Figure 2. Typical Recordings of Sample Temperature and Oxygen Content In Flash-Fire Cell During the Production of Flash Fires. 19 Figure 3. Typical Recording of Sample Temperature and Oxygen Content During Pyrolysis of Sample 16 in the Flash-Fire Cell Without the Production of Flash Fires. 20 Figure 4. Effect of Temperature and Sample Weight on Production of Flash Fires 21 Figure 5. Recording of the Catalytic Detector Response to Two Major Stages of Combustible Pyrolyzate Evolved from Sample 16 as the Temperature is Increased at About 60 "'C/min 22 Figure 5a. A Recording Showing the Catalytic Detector Response to The Pyrolyzate Evolved from a Conventional Flexible Foam as the Temperature was Raised at about 60 °C/min 23 Figure 6. A Typical Recording Showing the Effect of Temperature on the Two Major Stages of Evolution of Total Combustibles from a Polyurethane Shown in Figure 5a. 24 Figure 7. An Arrhenius Plot of the Results Obtained from the Second Major Stage of the Combustible Pyrolyzate Shown in Figure 6 25 Figure 8. A Recording Showing a Reduced First Major Stage as a Result of Removing the "Cracking Coil." 26 Figure 9. A Recording Showing the Total Mass-Flow Rate of Pyrolyzate from the Conventional Polyurethane as the Temperature was Increased at a Rate of 60 °C/min. 27 V . A TECHNIQUE FOR THE MEASUREMENT OF FLASH FIRE POTENTIAL OF POLYMERIC MATERIALS James E. Brown and John J. Comeford This report summarizes work for the period February - August 1974 on a continuing program to characterize the chemi- cal and physical parameters of importance in a flash fire and to develop laboratory scale methods for measuring the flash fire potential of materials. Significant modifications have been made to a flash fire cell developed earlier to measure the flash fire potential of materials by characterizing the conditions required to pro- duce an ignitable pyrolyzate-air mixture by thermally degrading a polymer. The furnace temperature, cell geometry and orien- tation, and sample size are specified. These modifications have resulted in an improved technique, especially in terms of reproducibility, for evaluation of flash fire potential of materials Experiments have been conducted on rates of combustible gas formation from flexible polyurethanes to assist in the optimization of the flash-fire cell operating conditions. In the rate study, two successive major stages of degrada- tion were found for polyurethane as the temperature approached 500° at a rate of about 60 °C/min. It was also found that the products of the second stage appear to be responsible for flash fires in the flash-fire cell. A minimum polyurethane weight to enclosure volume ratio greater than 0.2 g/1 and a sample pyroly- sis temperature greater than 380 °C were required to produce a flash fire in this apparatus. Key words: Aircraft fires; fire hazard; flash fire; poly- urethane; pyrolysis. 1 . INTRODUCTION This report describes the research from February, 1974 to August, 1974 on a joint National Bureau of Standards — Federal Aviation Admin- istration program directed towards ultimately reducing flash fire hazards in inhabited enclosures such as aircraft cabins. The purpose of this study was to evaluate the parameters which may produce flash fires as a result of thermal degradation of polymeric materials in an enclosed environment. We define a flash fire as a fire (flame front) which propagates through a fuel-air mixture as a result of the energy release from the combustion of that fuel, having required only an ignition source. Since most organic polymers produce combustible 1 products during thermal degradation, we set out to determine the condi- tions under which a flash fire would result from the products of thermal degradation in air of a variety of polyurethane foams, which are recog- nized to be susceptible to this fire hazard. A laboratory flash fire cell was developed to permit observation of flash fires resulting from the products of thermal degradation of poly- meric material in an enclosed environment. Observations of flash fires were made using a variety of flexible polyurethane foams. The experimental technique for a given material in- volved heating the foam in a pyrolysis chamber while allowing the evolved products of pyrolysis to pass into the cell. During the pyrolysis, the temperature of the sample and the oxygen concentration in the cell are recorded. From the change in the oxygen concentration, the volume frac- tion of the pyrolysis products is inferred. Essentially then, the lower limit of flammability of the pyrolyzate-air mixtures is also recorded when a flash occurs. Investigations on the products of pyrolysis as a function of tem- perature were carried out in nitrogen atmospheres by Wooley [l]"*". He reported that at low temperatures (200 to 300 °C) there is a rapid and complete loss of the toluene diisocyanate (TDI) units of the polyurethane as a yellow smoke leaving a residue derived from the comonomer polyol. This suggests that below 500 °C and perhaps below 750 °C the initial re- action involves ure thane linkage rupture to produce TDI and other aromatic compounds. The familar yellow smoke which contains virtually all of the nitrogen of the polyurethane, was reported to be stable at temperatures up to 750 °C where other compounds including hydrogen cyanide are formed. Thermal degradation of polyurethane was also studied by Tilley and co-workers [2] and Napier and Wong [3], The mechanism of degradation appears to closely follow the mechanism demonstrated by well characterized monomeric urethane compounds [4,5]. Thermal degradation of urethanes gen- erally produced isocyanates, amines, carbon dioxide and alkenes. It was suggested that polyure thanes also produce the nitrogen compounds, carbon dioxide from the urethane groups in the polymer, and unsaturated compounds as well as carbonyl compounds from the polyether-polyol fraction of the copolymer. These latter compounds were identified in an earlier report from our laboratories [6]. We report the technique and results of pyrolyzing several polyurethane foams in the flash-fire cell. We also report an exploratory study of the rate of production of combustible products from polyurethane pyrolysis in nitrogen and the rate of production of volatile combustibles when polyure- thane is pyrolyzed in air. "Slumbers in brackets correspond with the literature references listed at the end of this paper. 2 2 . EXPERIMENTAL 2.1. Materials The polyurethane foams used in this study were all of the flexible polyether type although the molecular weight of the polyether-polyol and method of polymerization differed. The foams, their general formulations and some physical properties are listed in table 1. The formulations and densities were supplied by the manufacturers. The oxygen indices (01) were kindly supplied by Dr. Robert McCarter [7]. 2.2. Flash-Fire Cell A diagram of the flash-fire cell is shown in figure 1. The cell is constructed of a Pyrex cylinder 50 cm in length and 5 cm in diameter. The volume of the cell is approximately one liter. Each end of the cylinder has integral "0" ring flanges fitted with neoprene "0" rings and poly (methyl methacrylate) windows which are fastened with spring- loaded clamps. The cell is equipped with a pyrolysis chamber which is connected to the main cell body by an "0" ring flange. The chamber is heated by a regulated electric furnace. The cell also contains an ignition source consisting of a lOKV AC arc 5 to 10 mm in length between platinum electrodes and a continuous polarographic oxygen analyzer. The ignition source and detector of the oxygen analyzer are located near the ' end of the cell farthest from the pyrolysis chamber. During the experi- ments chromel-alumel thermocouples are used to measure the temperatures of the sample and the furnace. 2.3. Pyrolysis Rate Apparatus The pyrolysis apparatus is designed so that the kinetics of the pyrolysis of polymeric materials may be derived from the evolution of the pyrolysis products.
Details
-
File Typepdf
-
Upload Time-
-
Content LanguagesEnglish
-
Upload UserAnonymous/Not logged-in
-
File Pages36 Page
-
File Size-