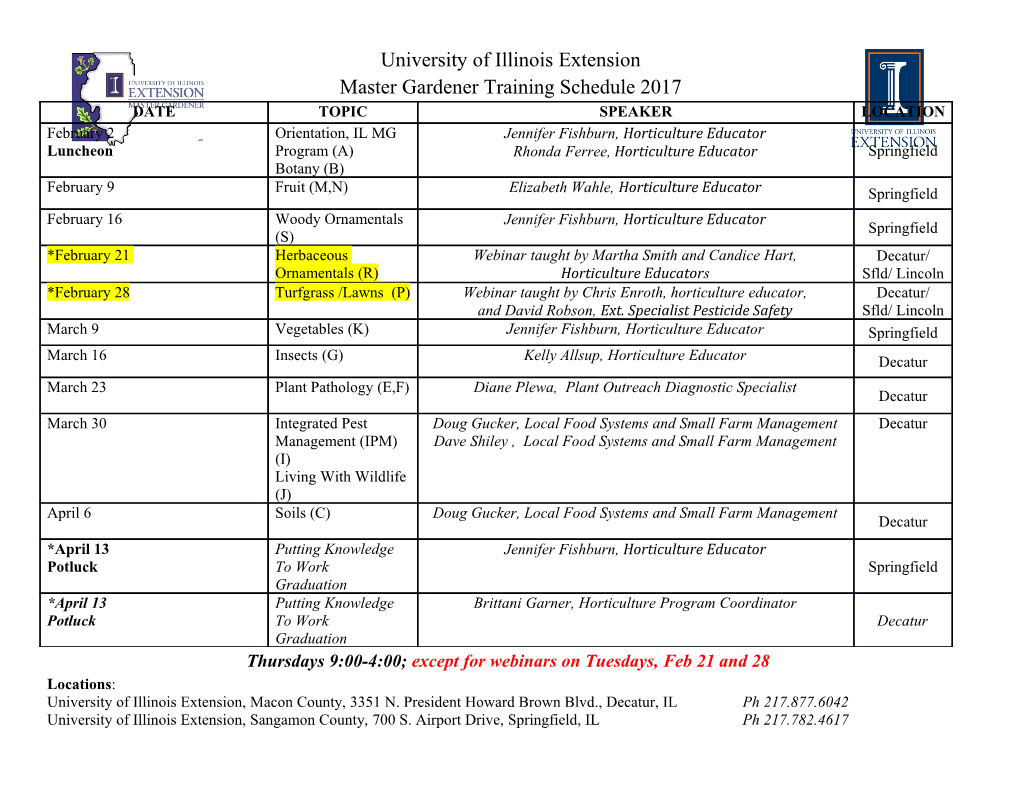
Turbomachinery ME 322 Lecture Slides, Winter 2007 Gerald Recktenwald∗ February 15, 2007 ∗Associate Professor, Mechanical and Materials Engineering Department Portland State University, Portland, Oregon, [email protected] Overview Turbomachines Turbomachines are mechanical devices that extract energy (turbine) or add energy (pump) to a fluid. The interaction between the fluid and the machine is dynamic. Energy is added by increasing or decreasing the inertia of the fluid as is passes open passages inside the machine. Learning Objectives • Understand and correctly use basic terminology. • Be able to use and interpret simple models of performance. • Be able to read and use standard performance charts and tables for pumps. • Be able to match pump performance to simple piping systems. • Be able to apply basic similarity laws for pump scaling. Boundary Layer Analysis: February 15, 2007 page 1 Positive Displacement versus Dynamic Machines Positive Displacement Pumps • Fluid is captured in a confined space. • Energy transfer to fluid is quasistatic. • Basic operating principle works in limit as machine speed goes to zero. • Examples: bicycle pump, reciprocating compressor, screw compressor, peristaltic pumps. Dynamic Pumps – Turbomachines • Fluid moves through open passages. • Interaction between the machine and fluid relies on dynamic effects. Energy is transfered by increasing the inertia of the fluid inside the machine. • As machine speed (flow rate) approaches zero, the net output goes to zero before speed equals zero. • Examples: window fan, compressor stage of jet engine, furnace blowers Boundary Layer Analysis: February 15, 2007 page 2 Positive Displacement Pumps Source: Munson, Young and Okiishi, Figure 12.1 Boundary Layer Analysis: February 15, 2007 page 3 Dynamic Pumps Source: Munson, Young and Okiishi, Figure 12.2 Boundary Layer Analysis: February 15, 2007 page 4 Basic Pump Peformance (1) See MYO §12.4.2 Actual Head: ha = hs − hL inside the pump. hs = shaft work transfered to fluid inside the pump hL = head loss inside the pump Flow rate: Q is measured Source: Munson, Young and Okiishi, Figure 12.10 Boundary Layer Analysis: February 15, 2007 page 5 Basic Pump Peformance (2) Source: Munson, Young and Okiishi, Figure 12.10 Apply the steady-flow energy equation 2 2 p2 − p1 V2 − V1 ha = + z2 − z1 + γ 2g p2 − p1 d2 = d1, z2 ≈ z1 =⇒ ha = γ Boundary Layer Analysis: February 15, 2007 page 6 Basic Pump Peformance (3) • Pump manufacturers analyze flow inside pump passages. • Pump manufacturers provide pump performance curves: ha = f(Q). • We will study very simple models of pump performance, and then use manufacturer’s data Boundary Layer Analysis: February 15, 2007 page 7.
Details
-
File Typepdf
-
Upload Time-
-
Content LanguagesEnglish
-
Upload UserAnonymous/Not logged-in
-
File Pages8 Page
-
File Size-