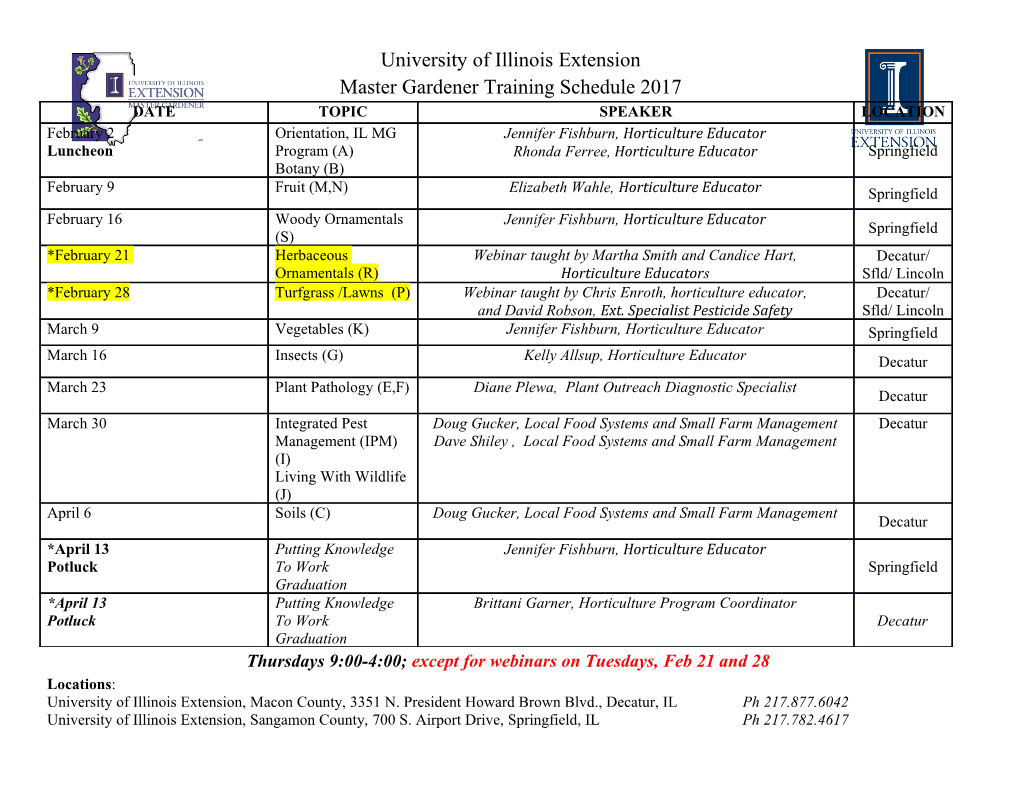
Europaisches Patentamt European Patent Office © Publication number: 0 582 114A1 Office europeen des brevets EUROPEAN PATENT APPLICATION © Application number: 93111456.5 © Int. CI.5: C07F 17/00 @ Date of filing: 16.07.93 © Priority: 03.08.92 US 923646 © Applicant: ETHYL CORPORATION 451 Florida Boulevard @ Date of publication of application: Baton Rouge, Louisiana 70801 (US) 09.02.94 Bulletin 94/06 @ Inventor: Lee, John Yuchu © Designated Contracting States: 1524 Stoneleigh Drive BE DE FR GB IT Baton Rouge, Louisiana 70808(US) Inventor: Diefenbach, Steven Paul 1457 Bullrush Drive Baton Rouge, Louisiana 7081 0(US) © Representative: Schwabe - Sandmair - Marx Stuntzstrasse 16 D-81677 Munchen (DE) © Process for preparing metallocenes. © A process is provided for preparing a transition metal compound of the formula: (RC5r-U)2MX2, where R is hydrocarbyl or silahydrocarbyl of 1 to 10 carbon atoms, M is titanium or zirconium and X is halogen. The process comprises the steps of: (a) reacting Na(C5H5) with RX, where R and X are as defined above, in an organic solvent so as to form a reaction product mixture which includes RC5 m and C5 H5 ; (b) vacuum stripping the product mixture at am- bient temperatures so as to remove substantially all of said C5 H5 from said product mixture; (c) deprotonating the RC5H4; and (d) adding MX+, where M and X are as defined < above, to the product mixture so as to react the RC5H4 and the MX+ and form said transition metal compound, the transition metal compound being substantially free of C5H5 containing impu- CM rities. 00 Rank Xerox (UK) Business Services (3. 10/3.09/3.3.4) 1 EP 0 582 114 A1 2 This invention relates generally to the prepara- said deprotonated RC5H4 and said MX+ and tion of metallocene derivatives which are useful as form said transition metal compound, said com- olefin polymerization catalysts and more specifi- pound being substantially free of C5H5 contain- cally to an improved process for preparing bis- ing impurities. (monosubstituted cyclopentadienyl) transition metal 5 According to the alkylation process, NaCp is metallocenes which are substantially free of unsub- reacted with an alkyl halide in a solvent. The NaCp stituted cyclopentadienyl impurities. is commercially available and can be prepared by Metallocene derivatives represented by the for- cracking cyclopentadiene dimer and reacting the mula (RCp)2MX2, where R is hydrocarbyl or cyclopentadiene with sodium metal as is known in silahydrocarbyl of 1 to 20 carbon atoms, Cp is 10 the art. The preferred alkyl halides are represented cyclopentadienyl (C5H4-), M is titanium or zirco- by the formula RX, where R is C1 to C2o (and more nium and X is halogen are known to be useful preferably C+ to C10) hydrocarbyl or silahydrocar- catalysts for olefin polymerization. They can be byl such as, for example, methyl, ethyl, n-propyl, prepared by reacting a deprotonated RCp com- isopropyl, n-butyl, tert-butyl, isobutyl, pentyl, hexyl, pound with MX4. As noted in the literature, how- 15 heptyl, or trimethylsilyl and X is halogen. Bromine ever, the generation of RCp by the alkylation of is the preferred halogen. Chlorine can be used but cyclopentadiene using alkyl halides is difficult due gives slower reaction rates and iodine is more to the generation of a complex mixture of products expensive. The NaCp and RX reactants are prefer- (Inorg. Chem. 1991, 30, 856-858). This reference ably used in NaCp:RX mole ratios of about 1:1, in proposes the use of either a liquid ammonia (low 20 order to minimize the amount of dialkyl substituted temperature) reaction medium or a highly reactive or unsubstituted Cp and Cp2 (cyclopentadiene alkylating agent, such as ethyl trifluoromethane- dimer) by-products, but ratios of 1:0.8 to 1:1.2 can sulfonate. Furthermore, the use of alkylhalides al- be used. The preferred solvents for the reaction are ways results in a product which contains, due to ethers (e.g., THF or diethylether but hydrocarbon the reaction equilibrium, cyclopentadiene and 25 solvents can also be used such as benzene or cyclopentadiene dimer. The dimer is inert in the toluene. Preferably, combined reactant concentra- subsequent metallocene preparation, but the tions of from 5 to 20 wt. percent in the solvent, are cyclopentadiene must be removed. Otherwise, it used. The reaction can be conducted at ambient will form (Cp)2MX2 impurities which adversely temperatures with the reaction being exothermic. change the molecular weight distributions of the 30 Generally, the reaction temperature will range from polymers produced when the (RCp)2MX2 metal- 20° to 50° C. The by-products of the alkylation locene product is used to catalyze olefin poly- reaction typically include besides NaCI, minor por- merization. Heretofore, complete removal of tions of R2Cp and Cp/(Cp2). Surprisingly, we have cyclopentadiene has not been achieved because of found that the Cp can be substantially completely the generation of additional cyclopentadiene due to 35 removed (less than about 1 wt. percent) by reduc- the cracking of the cyclopentadiene dimer. We ing the volume of the reaction mixture under vacu- have now discovered an economical, one-pot pro- um (2-15 mm Hg) at temperatures of 0° to 25° C. cess for making such transition metal metallocenes The cyclopentadiene dimer remains, but is inert so which are free of Cp impurities. Furthermore, the long as the subsequent reactions and product process can be conducted at ambient temperatures 40 work-up procedures avoid elevated temperatures which avoids the cost of refrigeration cooling sys- which would cause cracking to form additional tems. cyclopentadiene. The metallocene by-products re- In accordance with this invention there is pro- sulting from the presence of some disubstituted vided a process for preparing a transition metal cyclopentadiene (R2Cp) can be easily separated compound of the formula: (RC5r-U)2MX2, where R 45 from the final metallocene product by solvent sepa- is hydrocarbyl or silahydrocarbyl of 1 to 20 carbon ration. The vacuum treatment also removes any atoms, M is titanium or zirconium and X is halogen, unreacted alkyl halide which can then be recycled. said process comprising the steps of: Reduction of the volume of the reaction mixture to (a) reacting Na(C5H5) with RX, where R and X about 25% is sufficient to remove substantially all are as defined above, in an organic solvent so 50 of the cyclopentadiene (no Cp was detected by GC as to form a reaction product mixture which such that the Cp content was less than about includes RC5H4 and C5H5; 0.1%.) (b) vacuum stripping said product mixture at The product RCp can then be deprotonated in ambient temperatures so as to remove substan- situ with, for example, Na powder, BuLi, NaH, LiH tially all of said C5H5 from said product mixture; 55 or a Grignard reagent (RMgX). Solvent can be (c) deprotonating said RC5H4; and added back to the reaction mixture prior to de- (d) adding MX+, where M and X are as defined protonation. Preferably, about a 1:1 mole ratio of above, to said product mixture so as to react RCp to deprotonating agent is used. No more than 2 3 EP 0 582 114 A1 4 a 10% excess of deprotonating agent is necessary ml) was added slowly at 22 to 40 °C into above or desirable as we have found that salt formation BuBr/THF solution over a period of 15 minutes. with the mono-alkyl product is favored over the The reaction mixture was stirred at 22 ° C for 3 hrs. dialkyl (R2Cp) impurity. The deprotonation can be to form a mix-ture of BuCp (58 mol %), Bu2Cp (21 carried out at ambient temperatures and cooling is 5 mol %), Cp/(Cp)2 (21 mol %) based on NaCp unnecessary, although higher or lower tempera- charged, and a trace of BuBr. The volume of the tures of -30° C to 60° C can also be used. If above mixture was reduced under vacuum (0° to sodium is used as the deprotonating agent, then 22°C/2mm Hg) to 25% of its original volume. GC excess sodium metal must be filtered from the showed that all the cyclopentadiene and BuBr had reaction mixture prior to the further reaction with io been removed and there was 40 mol % of BuCp the transition metal halide to form the product bis- based on NaCp charged in the product mixture. (mono-alkylcyclopentadienyl) transition metal About 20 ml of THF were then added. Deprotona- metallocene. tion with a 10% excess amount of Na powder was The (RCp)2MX2 metallocene derivatives are performed. The Na was slowly added into above prepared by adding a transition metal halide of is solution at 22 °C over a period of 1/2 hr. Hydrogen titanium or zirconium, e.g., TiCk or ZrCk, to the formation was observed. The mixture was then deprotonated mono-alkylsubstituted cyclo-pen- stirred at 22 °C for an additional 2 hrs. 1HNMR of tadiene ligand, preferably in nearly stoichiometric the product showed a > 95% yield of NaBuCP. proportions of ligand to transition metal halide After the Na and NaBr were filtered out, the (mole ratios of 1 :0.4 to 0.5 ligand to transition metal 20 NaBuCp was further reacted with ZrCk (0.46 g, 2 halide and, more preferably, 1.0:0.5) so as to mini- mmol, dissolved in 4 g. of glyme) at 22 °C which mize the formation of RCpMX3 impurities and the was slowly added into the THF solution of NaBuCp amount of unreacted transition metal halide which in 5 minutes to form a > 90% yield (by 1HNMR) of may be difficult to remove from the product. The (BuCp)2ZrCb which contained no cyclopentadienyl process can be carried out at ambient temperature.
Details
-
File Typepdf
-
Upload Time-
-
Content LanguagesEnglish
-
Upload UserAnonymous/Not logged-in
-
File Pages5 Page
-
File Size-