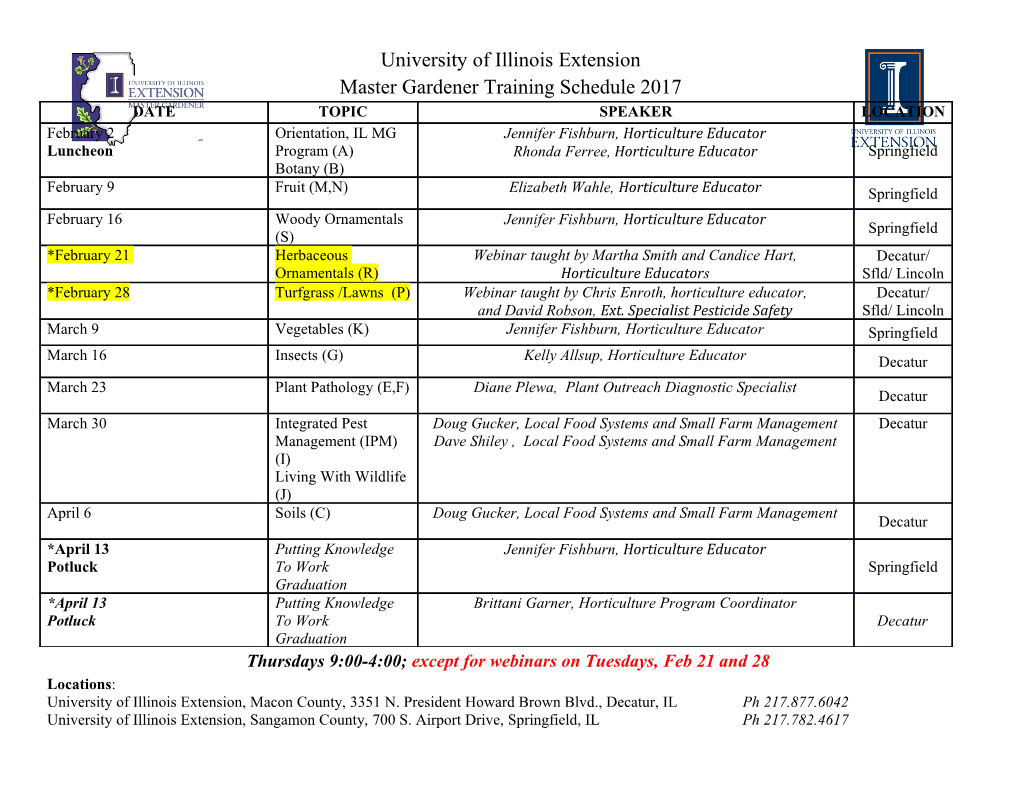
View metadata, citation and similar papers at core.ac.uk brought to you by CORE provided by Elsevier - Publisher Connector Egyptian Journal of Petroleum (2011) 20, 25–31 Egyptian Petroleum Research Institute Egyptian Journal of Petroleum www.elsevier.com/locate/egyjp www.sciencedirect.com Upgrading of coker distillate under variable hydrotreating operating conditions H.A. Elsayed *, H.S. Ahmed, M.F. Monufy Refining Department, Egyptian Research Institute, Nasr City, Cairo, Egypt Received 28 February 2010; accepted 2 January 2011 Available online 19 October 2011 KEYWORDS Abstract Studies on hydrotreating coker distillates, produced from a delayed coker unit were done Hydrotreating; using a commercially available CoMo/c-Al2O3 catalyst, on which 0.2 wt% P2O5 was added in order Hydrotreating catalyst; to improve its characteristics. The experimental studies were conducted in a fixed-bed continuous- Coker distillate; reactor (cata-test unit) at temperatures (300–400 °C) and total hydrogen pressure (40–65 bar). These Hydrodesulfurization conditions have affected the feedstock characteristics and great reduction of sulfur, aromatics and boiling ranges. Other improvements were obtained in diesel index (DI) due to hydrogenation reac- tion of aromatics and desulfurization of its sulfur contents. ª 2011 Egyptian Petroleum Research Institute. Production and hosting by Elsevier B.V. Open access under CC BY-NC-ND license. 1. Introduction in fuels and gas oil or diesel to <0.01 wt%. The removal of sulfur containing compounds, such as thiophenes, mercaptans, In recent years, sulfur reduction from light gas oil or diesel fuel dibenzothiophene and especially its alkyl substituted deriva- using catalytic hydrodesulfurization (HDS) is a routine opera- tives is necessary in order to minimize the polluting effects of tion in petroleum refining process due to environmental regu- containing gases such as SO2 that may be released into the lations and to improve the combustion qualities of automotive atmosphere during combustion [1]. engines. These regulations limit the amount of sulfur permitted It is well known that hydrotreating processes are aimed at upgrading petroleum distillates used in the refining industry * Corresponding author. Tel.: +20 0101633178. in order to remove or reduce their contamination of sulfur, E-mail address: [email protected] (H.A. Elsayed). nitrogen and heavy metals. The reactions during hydrotreat- ments are hydrodesulfurization (HDS), hydrodenitrogenation 1110-0621 ª 2011 Egyptian Petroleum Research Institute. Production (HDN) and hydrodemetalization (HDM) [2]. and hosting by Elsevier B.V. Open access under CC BY-NC-ND license. Industrial hydrotreating catalysts temporally consist of c- Peer review under responsibility of Egyptian Petroleum Research Al2O3 as support and loaded with molybdenum (Mo) which Institute. is promoted with cobalt (Co) or nickel (Ni) and these catalysts doi:10.1016/j.ejpe.2011.06.001 are in situ or ex situ sulfided prior to use as active hydrotreat- ing catalysts [3]. The addition of 0.2 wt% P2O5 increases the HDS (98%) Production and hosting by Elsevier activity and reduction on sulfur/nitrogen was observed as an indication of the increase of the hydrogenation activity. This 26 H.A. Elsayed et al. makes CoMo catalyst attractive in HDS of unsaturated hydro- Table 2 Total saturates via chromatographic analysis (GC) of carbon streams like fluid catalytic cracking (FCC) naphtha. coker feedstock. Therefore, hydrotreating process removes various contami- nants from the crude oil or distillates and results in finished oil Component wt% Component wt% Component wt% products having improved odor, color and stability characteris- Decanes 1 Nonadecanes 2 Octaicosanes 0.2 tics and also increases the production of more valuable oil frac- Undecanes 2.2 Eicosanes 1.6 Nonaicosanes 0.21 tions [4]. Dodecanes 3.3 Eneicosanes 1.01 Tricontanes 0.1 To increase the activity and stability of the hydrotreating Tridecanes 5.2 Dodeicosanes 1.2 Entricontanes 0.11 catalysts a large number of elements are used as additives. Tetradecanes 5.4 Tricosanes 0.9 Dodetricontanes 0.1 Among all these elements, phosphorus is mostly used as a third Pentadecanes 5.2 Tetraicosanes 0.6 Tritricontanes 0.03 element in hydrotreating catalysts, several effects in the addi- Hexadecanes 3.7 Petaicosanes 0.5 Tetratricontanes 0.02 Heptadecanes 3.5 Hexaicosanes 0.4 Pentatricontanes 0.01 tion of phosphorous in hydrotreating catalysts have been re- Octadecanes 2.8 Heptaicosanes 0.3 ported in the literature [5]. The addition of phosphorus is known to promote the activ- ity of conventional CoMo and NiMo hydrotreating catalysts, feedstock in this investigation. Its characteristics are indicated especially the latter [6–14]. Phosphorus promotion has been in Tables 1 and 2. attributed to several effects including stabilization of the impregnating solution. An increase in the dispersion of the ac- 2.2. Catalyst tive compound on the carrier, surface phosphate formation which in turn reduces spinal formation and retains a higher A commercially CoO3MoO3/Al2O3 hydrotreated catalyst that surface concentration of Ni or Co [15]. was impregnated with an aqueous solution of H2PO4 acid and The present work studies the effects of operating condi- dried in air at 110 °C for 12 h was used. The chemical and phys- tions, such as reactions temperatures and total hydrogen pres- ical characteristics of the catalyst are illustrated in Table 3. sure on hydrotreating coker gas oil, using the sulfided CoMo/ c-Al2O3 catalyst, and also the addition of 2% phosphorus to 2.3. Apparatus and procedure this catalyst. The improvements of qualities and characteristics of the produced gas oil are discussed. High pressure micro-reactor unit (cata-test unit) was used. The unit consists of a stainless steel reactor (internal diameter 2. Experimental 19 mm, external diameter 27 mm, length 50 cm) and divided into three zones, each of them is heated and separately temper- 2.1. Feedstock ature controlled. 100 cc of the catalyst is charged in the middle zone of the reactor (40 cm as a catalyst bed), whereas the upper A coker distillate kindly, supplied by the Suez Oil Processing and lower zones are filled, each with 5 cc of glass beads. After Company, Suez, (boiling range 130–380 °C) has been used a charging the reactor with the predetermined quantity of the catalyst, the leakage of the unit was checked by putting the unit under hydrogen pressure (100 bars) for 4 h. Table 1 Characteristics of the used coker distillate feedstock. The catalyst sulfiding is carried out before starting all the Properties Value Method experiments, by using spiked feed stock methods, where di- Specific gravity at 60/60 °F 0.86 ASTM D289-65 methyl disulfide (DMDS) is used as a spiking agent and gas API gravity 33.0349 ASTM D287-92 oil as a spiked feed. The spiked feed containing 6% DMDS, Refractive index at 20 °C 1.47742 ASTM D2503-82 is passed through the reactor with a flow rate of 50 ml/h under Aniline point, °F 136.5 ASTM D611-82 20 bars hydrogen pressure and reaction temperature 300 °C for Sulfur content, wt% 2.55 ASTM D4294-90 12 h. (X-ray fluorescence) After sulfiding, the operating conditions are: Nitrogen content, wt% 0.24 Diesel index 43.7 Calculated from aniline Reaction temperature: 300–400 °C. point and API gravity Hydrogen pressure: 40–60 bar. Hydrocarbon analysis, wt% ASTM STP224 Total saturates 55 Total aromatics 41 Asphalted resins 4 Table 3 Physical and chemical properties of the hydrotreating Distribution of aromatics (%) EPA610 catalysts. Di-aromatics 3.5 Physical characteristics Tri-aromatics 20.6 Tetra-aromatics 16.4 CoMo/Al PCoMo/Al Penta-aromatics 0.5 Surface area, m2/g 232 Surface area, m2/g 241 ASTM-distillation at °C °C ASTM D2887 Pore volume, cm3/g 0.37 Pore volume, cm3/g 0.4 IBP 130 10% 190 Chemical composition, wt% Chemical composition, wt% 50% 240 CoO3 3.1 CoO3 3.1 80% 290 MoO3 10.5 MoO3 10.5 Recovery, 90% 360 Al2O3 86.4 Al2O3 86.2 E.P. 380 P2O5 0.2 Upgrading of coker distillate under variable hydrotreating operating conditions 27 À1 Liquid hourly space velocity (LHSV): 0.5 h . 96 94 Hydrogen – to feed ratio: 500 L/L. The stability of the catalyst was reached when the density of 92 the reactor effluent (liquid product) was measured continu- 90 ously during the test, until it became constant after which 88 the samples of the reactor effluent were collected every hour 86 and the total period of time was 4 h for each condition. % wt yield, Total 84 82 2.4. Product analysis 275 300 325 350 375 400 425 Temperature, °C During the operation, liquid products and gas samples were collected from the high pressure separator in order to be ana- Figure 1 Effect of reaction temperature on product yield of lyzed. The gas samples were analyzed by gas chromatography treated coker distillate during hydrotreating process at À1 À1 while liquid products were analyzed and characterized accord- LHSV = 0.5 h , pressure = 55 bars, H2/oil ratio = 550 ml m . ing to the recommended standard methods. Sulfur compounds were characterized and identified by using Clarus 500. Gas chromatograph equipped with Flame Photometric Detector 100 (FPD). 80 3. Results and discussion 60 3.1. Effect of reaction temperature 40 Table 4 and Figs. 1–4 represent the effect of reaction temper- 20 HDS atures on the product qualities of hydrotreated coker distillate Hydrogenation (HDS, Hydrogenation) wt.% at reaction temperatures (300–400 °C). It was shown that the 0 yield of the treated coker distillates was clearly affected by 275 300 325 350 375 400 425 the reaction temperature, i.e. decreased by increasing the tem- Temperature, °C perature, and the activity of the sulfided CoMo/c-Al O cata- 2 3 Figure 2 Effect of reaction temperature on hydrodesulfurization lyst increased (Fig.
Details
-
File Typepdf
-
Upload Time-
-
Content LanguagesEnglish
-
Upload UserAnonymous/Not logged-in
-
File Pages7 Page
-
File Size-