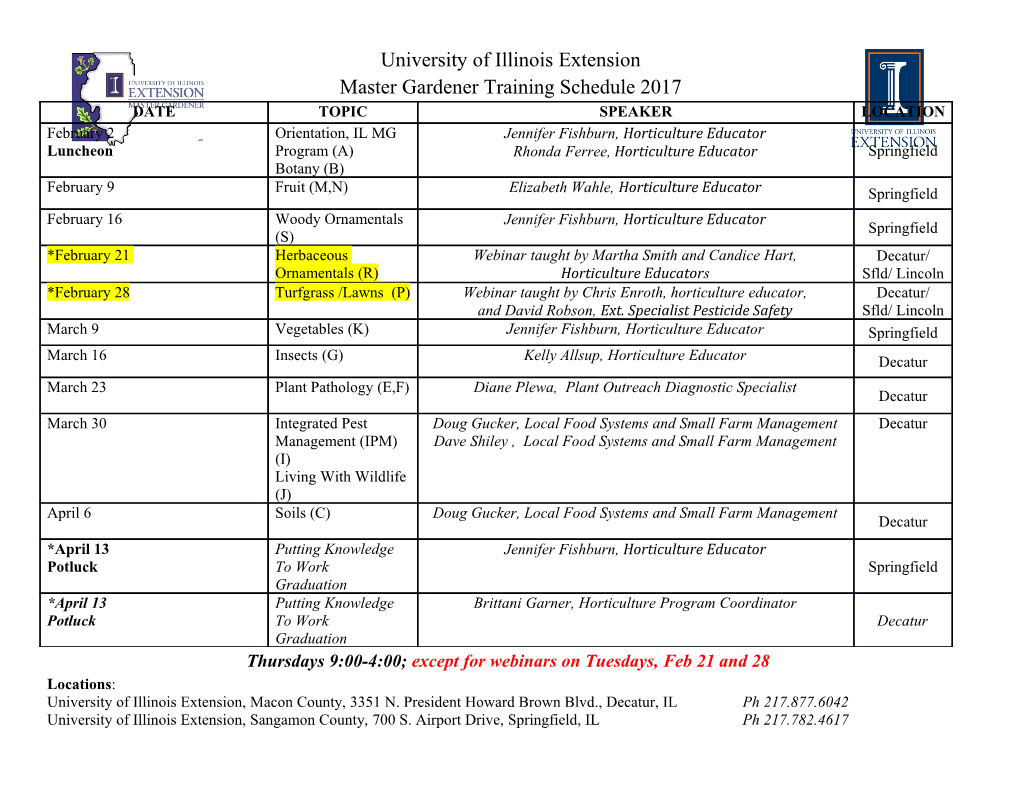
Volume Two Hydraulic Overload Protection The Silent Sentinel Author: Steve Overly, Vice President Domestic Sales, AIDA-America Corporation Where can I find it? What is HOLP? HOLP is nearly always located near the Hydraulic Over Load Protection (HOLP) lower end of each connection. The upper is a system that senses an overload portion of the HOLP system remains condition in a mechanical press and stationary during activation while the releases hydraulic pressure in a collapsible lower portion is free to push upward with cylinder, thereby allowing the slide to be the slide, thus relieving the overload. (See pushed upward by the overload force. The Figure#1) primary purpose of the system is to prevent damage to the press in the event of Why do I need it? overload. It is a standard feature on Your press is a major long-term modern, well-designed general-purpose investment and often is operated by presses. someone without extensive training. Overload can happen through What else does it do? unintentional error or by unnoticed In addition to protecting the press change in the die or material. Without components, HOLP can at times: HOLP, press overload can result in • Help protect a die damage to the press structure, bearings, • Stop operation in a dangerous gears or clutch. At a minimum, condition uncorrected overload results in reduced • Release a press that is stuck on press accuracy and service life. Worse, bottom repair of a broken press is expensive and • Sense a die that needs sharpening the loss of production can reduce profits or • Reduce connection clearances even cost you a contract. The inclusion of • Sense extreme off-center loads an effective HOLP in the press design provides an automatic protection that helps to keep the press in service. Additionally, HOLP provides a quick and easy method to release a press that has been stuck at the bottom of the stroke. This can happen easily if the shutheight setting is not correct for the die, occurring most frequently during die setup. Figure #1 Copyright © 2000 AIDA-America Corporation. ALL RIGHTS RESERVED. 1 Volume Two What causes an overload? which a spring-loaded check valve opens Overload can be caused by many and permits oil to drain away when conditions including: pressure exceeds a set limit. While simple • Setting the shutheight too low in design, it has performance drawbacks. • Loading a die that requires too much (See Figure #3) tonnage • Slugs or foreign material lodging in the die • Misfeed or buckling of the material • Wear in a die • Improper positioning of a die • Using incorrect material • Changes in material hardness or thickness It is important to remember that a press overload can occur on one side of a multi- Figure #3 point press and not the other. In fact, this is the most common overload condition. • It is difficult to adjust accurately The total tonnage requirement of the die is • It is slow to react • It must relieve the oil cavity through a small opening • It can be difficult to actuate HOLP units simultaneously in a multi-point press • It is prone to leakage as it nears the actuation point, causing sponginess Figure #2 not the only measure. For example, a 400- ton die will overload a 400-ton press if more than 200 tons of the load are under one connection. (See Figure #2) What types of HOLP are there? HOLP systems can be easily differentiated by the type of actuation mechanism utilized. There are several basic methods: Figure #4 CHECK VALVE – This is the oldest, SOLENOID VALVE – The most most inexpensive triggering method in common method of actuation, this system uses a solenoid valve to open a drain line when the oil pressure limit is exceeded. Copyright © 2000 AIDA-America Corporation. ALL RIGHTS RESERVED. 2 Volume Two (See Figure #4) It relies on a pressure the types of HOLP. The design eliminates sensor in the valve or a signal from an the possibility of sponginess and is the electronic load monitor for actuation. It is most suitable for multi-point presses. The faster triggering than a check valve, is Aida HOLP unit is located at the bottom more accurate, does not normally leak if of the connection(s), inside the slide. (See the seals are properly maintained, and can Figure #6) It is designed as an enclosed, relieve a multi-point slide overload evenly. self-contained unit to prevent It still must drain oil through a small contamination from outside fluids and orifice, and so is slow acting. debris. What happens in overload if I don’t have HOLP? Without HOLP, an overloaded press will give at its weakest point. This can cause a stretched tie-rod or upright, bent crank or eccentric shaft, crushed bearing, broken connection pin or adjustment screw, cracked bed, slide or crown, or a slipping or damaged clutch. Even if the press survives overload without breaking, its Figure #5 clearances can be increased and parallelism destroyed. If the overload DIRECT VALVE – The Aida HOLP occurs under one connection in a multi- system utilizes a direct-acting, lapped seat point press, the gibs can be damaged by valve that is integral to the suspension the cocking of the slide. point. Sensing and relief are directly accommodated by a full 360-degree Can hydraulic tie rod nuts act as opening around the base of the ball HOLP? connection, not requiring an external No. Hydraulic tie-rod nuts make it easier sensor, a drain line or a restrictive orifice. to pre-stress tie-rods during press (See Figure #5) This method provides the assembly by eliminating the long and fastest reacting and quickest relief of all inaccurate process of heating and cooling them. They are not an effective or desirable method of overload protection. They can, however, be useful to relieve a non-HOLP press that is stuck on bottom. Figure #6 Copyright © 2000 AIDA-America Corporation. ALL RIGHTS RESERVED. 3 Volume Two Can I save my die? Is HOLP retrofitable to a non-HOLP Maybe, but don’t depend on it. HOLP is press? primarily intended to protect the press For the best performance, the HOLP from overload and may, depending upon system should be an integral part of the many variable conditions, also save a die press connection design and construction. as a secondary benefit. To have the best Such systems are not easily and very opportunity to save a die in overload, rarely installed in machines not originally specify the fastest acting HOLP available. designed for them. What is “unstick”? Which type is best? A press becomes stuck on bottom when The best HOLP system is the one that the slide encounters the work piece with actuates the quickest and drains the oil insufficient force, energy or clutch torque reservoir the fastest. The Aida direct to complete the revolution. The machine valve, non-orifice system is both the crunches to a halt with the punch still in fastest reacting and fastest draining system the material. Since the slide is stuck in on the market today. compression against the tool and bed, the clutch may have insufficient torque to How important is speed in HOLP? allow the slide to move in either direction. Speed is critical to HOLP in several ways. This happens most frequently during setup, when the stroke speed is too slow to Since overload occurs in a dynamic permit the press to generate its full energy. situation with the slide in downward motion, any delay in sensing allows the On older design straight-side presses slide to move closer to the bottom of the without HOLP, it is usually necessary to stroke, thus increasing the overload. The heat and release tension on the tie-rods to faster the sensing, the quicker the relief free a stuck press. This is a long and portion of HOLP can start. laborious process that takes the press out of production while the tie-rods cool to Speed is also critical in the dumping of oil regain tension. The use of hydraulic tie- in the HOLP cavity. The draining and rod nuts eliminates the need for heating collapse of this cavity is what gives the and cooling tie-rods, but it still requires slide the extra room to move downward releasing tension that may affect frame without increasing the load while the alignment when retightened. brake is actuating. If the cavity is not drained quickly enough, overload force can actually increase as the slide continues downward, even though the system has been activated. Additionally, in a multi-point press, speed in dumping the non-overloaded HOLP cavities is critical to prevent the slide from tipping when the HOLP is activated under one connection. Copyright © 2000 AIDA-America Corporation. ALL RIGHTS RESERVED. 4 Volume Two Figure #7 Since it has no tie-rods, sticking a gap Figure #8 frame press without HOLP often results in the need to use a torch to cut die or press A typical comparison is shown in Figure components to unstick the machine. This #8 where two presses were overloaded at results in very expensive repairs to the die the same point in the stroke. This or press and means substantial loss of illustration shows the value of a faster production. (See Figure #7) HOLP system. Under equal conditions, the faster Aida HOLP relieved the In a modern press with a HOLP system, pressure in 10 milliseconds allowing only releasing a stuck-on-bottom condition is four degrees of crankshaft rotation. The done by pushing the “unstick” button, conventional solenoid valve type required quickly draining the HOLP cavity. The 70 milliseconds or twenty-eight degrees of pressure on the slide is thereby released rotation to go to zero pressure under the and the press is unstuck.
Details
-
File Typepdf
-
Upload Time-
-
Content LanguagesEnglish
-
Upload UserAnonymous/Not logged-in
-
File Pages7 Page
-
File Size-