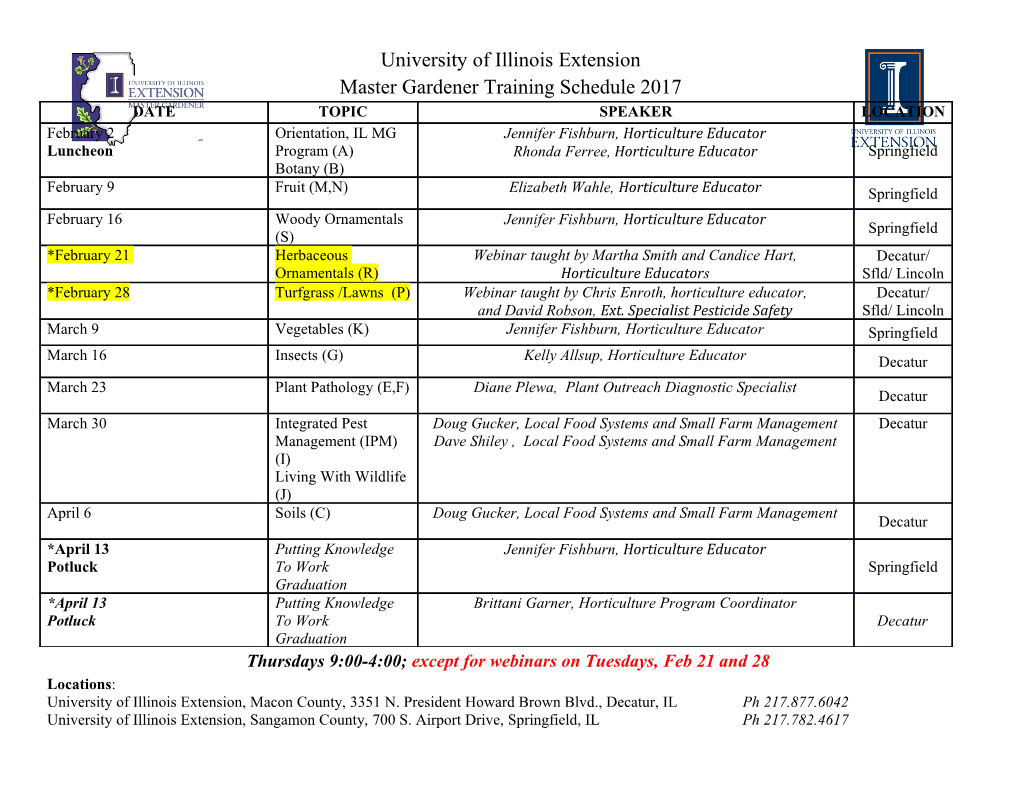
Optically Active Poly(Triphenylmethyl Methacrylate) Poly[1-methyl-1-(tripehnylmethoxycarbonyl)ethylene] Submitted by: Y. Okamoto1a and H. Yuki1b Checked by: M. Doherty and T. E. Hogen-Esch 2 1. Procedure A. Monomer Synthesis Method 1 (Notes 1 and 2)3 Methacrylic acid (200 g, 2.32 mol; Note 3) is placed in a 3-L three-necked flask equipped with a stirrer and a dropping funnel, and cooled in an ice bath. Then, aqueous 28% ammonium hydroxide (141 g, 2.32 mol) is added in the course of ca 30 min. To this solution, 395 g (2.32 mol) of silver nitrate dissolved in 100 mL of water is added with stirring, and the reaction is continued for 2 h. The precipitated silver methacrylate is separated by filtration, washed with cold water, and dried under reduced pressure. The yield is 377 g (84%). This is used for the next step without further purification (Note 4). Silver methacrylate (155 g, 0.80 mol) and dry ether (600 mL) are placed in a 3-L three-necked flask equipped with a reflux condenser, a stirrer, and a dropping funnel, and 187 g (0.67 mol) of triphenylmethyl chloride (Note 5) dissolved in 200 mL of dry ether is added dropwise with stirring at room temperature. After heating the mixture to reflux for 3 h, silver chloride is spearated by filtration. The concentration of the filtrate gives a crude product; 197 g (82%) which is recrystallized from ether and from hexane to give the pure monomer. The yield is 134 g (61%); m.p. 102-103o. The monomer is stored in a refrigerator and recrystallized from hexane just before use. 1 2 Macromolecular Syntheses, Collective Volume 2 Monomer Synthesis Method 24 Triphenylmethyl chloride (50.0 g, 0.179 mol) is dissolved in 400 mL of dry toluene in a 2-L three- necked flask equipped with a reflux condenser, a stirrer, and a three-way stopcock. To the solution, methacrylic acid (16.4 g, 0.189 mol) and triethylamine (42.8 g, 0.423 mol; Note 6) is added with a hypodermic syringe with stirring at room tempearature. After heating the reaction system to 80o with stirring for 3 h, triethylamine hydrochloride is separated by filtration. The concentration of the filtrate gives a crude product; 36.1 g (61%). The crude product is purified in the same manner as described in Method 1 to give the pure monomer. B. Catalyst5 N,N'-Dipehnylethylenediamine (0.50 g, 2.4 mmol; Note 7) is placed in a 30 mL glass ampule connected to a three-way stopcock through a ground glass joint under dry nitrogen (Note 8) and dissolved in 5 mL of dry toluene (Note 9). To this solution, 2.4 mL of butyllithium (1.0 M) in heptane are added with a syringe. The lithium salt of the amine is produced rapidly as a precipitate. A chiral ligand (-)-(2R, 3R)-dimethoxy-1,4-bis(dimethylamino)butane (0.57 g, 2.8 mmol; Note 10) is added to produce the homogeneous chiral catalyst immediately before use (Note 11). C. Polymerization5 A 300 mL glass ampule with a ground joint is dried by flaming with a gas burner under vacuum (10-2 - 10-3 torr). In this vessel, 10 g (30.5 mmol) of triphenylmethyl methacrylate which is recrystallized from hexane before use is placed under an atmosphere of nitrogen and the vessel is evacuated to dry the monomer. After filling the vessel with dry nitrogen, it is fitted with a three- way stopcock. Then, 200 mL of dry toluene is added with a syringe. The monomer solution thus obtained is cooled to -78o in a dry-ice-methanol bath and 6.7 mL (1.52 mmol as lithium salt) of the above chiral catalyst solution is added with a syringe. The stopcock is closed and the reaction is continued at -78o. After 2 h, a small amount of methanol is added to terminate the reaction (Note 12), and the polymer is precipitated in methanol (2 L). The resulting polymer is separated with a o centrifuge as rapidly as possible to avoid the methanolysis of ester groups and dried at 60 for 25 o several hours. A quantitative yield of polymer is obtained [á]D -300 to -330 (tetrahydrofuran c 2 g/dL). The polymer obtained is dissolved in tetrahydrofuran (200 mL) and added dropwise into 2 L of benzene-hexane (1:1) mixture. The precipitated polymer is separated with a centrifuge and o 25 o dried under high vacuum at 60 . Yield is about 9.0 g (90%), [á]D - 320-350 (tetrahydrofuran, c 2 g/dL; Notes 13, 14). 2. Characteriztion The GPC of the polymer obtained shows a bimodal curve from which Mn is estimated to be about 15,0006 3. Notes 1. The reaction of sodium or lithium alkoxides with methacryloyl chlorde also conveniently gives bulky methacrylate monomers having tertiary ester groups such as diphenyl-2-pyridylmethyl7, phenyl-2-pyridyl-o-tolylmethyl8, phenyl-2-pyridyl-m-tolylmethyl9, cyclopropyldiphenylmethyl10, cyclohexyldiphenylmethyl10, and (S)-diphenyl(1-methylpyrrolidin-2-yl)methyl11. 2. The reactions of silver nitrate and methyacrylate must be conducted in the dark to avoid discoloration of the products. Poly(triphenylmethyl methacrylate) 3 3. Methacrylic acid is purified by distillation. 4. The checkers recrystallized silver methyacrylate from hot water. 5. Commercial triphenylmethyl chloride is used without purification after checking for the absence of triphenylmethyl alcohol by FTIR. The alcohol shows a strong absorption at 3680 cm-1 due to the hydroxy group. The checkers recrystallized trityl chloride from a 4/1 benzene/acetyl chloride mixture. 6. Triethylamine is distilled and dried over sodium hydroxide. 7. Commercial amine is purified by recrystallization from hexane. The purified amine still contains a small amount of N,N'-diphenylpipreridine as an impurity but is used without further purification. Other N-substituted anilines such as N-benzylaniline and (+0-N-(1-phenylethyl)aniline can be used in place of N,N'-diphenylethylenediamine.5 8. Nitrogen gas is dried by passing through a trap packed with molecular sieves 4A cooled in a dry-ice-methanol bath. 9. Toluene is purified in a usual manner, mixed with a small amount of butyllithium, and distilled under vacuum just before use. 10. The chiral ligand is obtained from Aldrich Chemical Co. and purified by distillation after being dried over CaH2. 11. The catalyst decomposes slowly at room temperature. 12. The polymerization system is almost homogeneous after 2 h, if the reaction is properly carried out, and the polymer obtained is soluble in tetrahydrofuran. However, if the system is contaminated with a small amount of reactive impurities like water, it becomes heterogeneous, and much of the polymer is insoluble in tetrahydrofuran because of high molecular weight and crystallinity of the polymer. 25 o 13. The checkers found [á]D = -282 . 14. (+)-Polymer is obtainable with (+)-(2S, 3S)-dimethoxy-1,4-bis(dimethylamino)butane as a chiral ligand. The optically active polymers are useful as chiral packing materials for liquid chromatographic resolution of racemic compounds12,13. 15. A calibration curve was made with polystyrene standards and Mn was estimated as an average of the two peaks without any correction. 4. Methods of Preparation Optically active poly(triphenylmethyl methacrylate) may be prepared with the complex of butyllithium with (-)-sparteine which mostly forms the insoluble polymer6,14 and the complexes of 9- fluorenyllithium with (-)-sparteine, (+)-(2S, 3S)-dimethoxy-1,4-bis(dimethylamino)butane, and (+)- (S)-1-(2-pyrrolidinylmethyl)pyrrolidine which form the soluble (+)-polymers with a narrow molecular weight distribution.15 The detailed structure of the polymer and the oligomer obtained with the 9- fluorenyllithium complexes has been reported.15 5. References 1. a. Department of Applied Chemistry, Faculty of Engineering, Nagoya University, Nagoya, 464 Japan; b. Department of Chemistyr, Faculty of Engineering Science, Osaka University, Toyonaka, Osaka, 560, Japan. 2. Lower Hydrocarbon Research Institute, Department of Chemistry, University of Southern California, Los Angeles, CA 90089-1661. 3. Adrova, N. A.; Prokhorova, L. K. Vysokomol. Soedin, 1961, 3, 1509. 4. Yuki, Y. Japan Kokai, 560-8117, 1981. 5. Okamota, Y.; Shohi, H.; Yiki, H. J. Polym. Sci., Polym. Lett. Ed., 1983, 21, 601. 6. Okamoto, Y.; Suzuki, K.; Yuki, H. J. Polym. Sci., Polym. Chem. Ed., 1980, 18, 3034. 7. Okamoto, Y.; Ishikura, M.; Hatada, K.; Yuki, H. Polym. J., 1983, 15, 851. 4 Macromolecular Syntheses, Collective Volume 2 8. Yashima, E.; Okamoto, Y.; Hatada, K. Polym. J., 1987, 19, 897. 9.Okamoto, Y.; Nakano, T.; Asakura, T.; Mohri, H.; Hatada, K. J. Polym. Sci., Part A, Polym. Chem. 1991, 29, 287. 10. Okamoto, Y.; Nakano, T.; Fukuoka, T.; Hatada, K. Polym. Bull., 1991, 26, 259. 11. Okamoto, Y.; Nakano, T.; Ono, E.; Hatada, K. Chem. Lett., 1991, 525. 12. Okamoto, Y.; Okamoto, I.; Yuki, H. Chem. Lett., 1981, 835. 13. Okamoto, Y.; Honda, S.; Okamoto, I.; Yuki, H.; Murata, S.; Noyori, R.; Takaya, H. J. Am. Chem. Soc., 1981, 103, 6971. 14. Okamoto, Y.; Suzuki, K.; Ohta, K.; Hatada, K.; Yuki, H. J. Am. Chem. Soc., 1979, 101, 4763. 15. Nakano, T.; Okamoto, Y.; Hatada, K. J. Am. Chem. Soc., 1992, 114, 1318..
Details
-
File Typepdf
-
Upload Time-
-
Content LanguagesEnglish
-
Upload UserAnonymous/Not logged-in
-
File Pages4 Page
-
File Size-