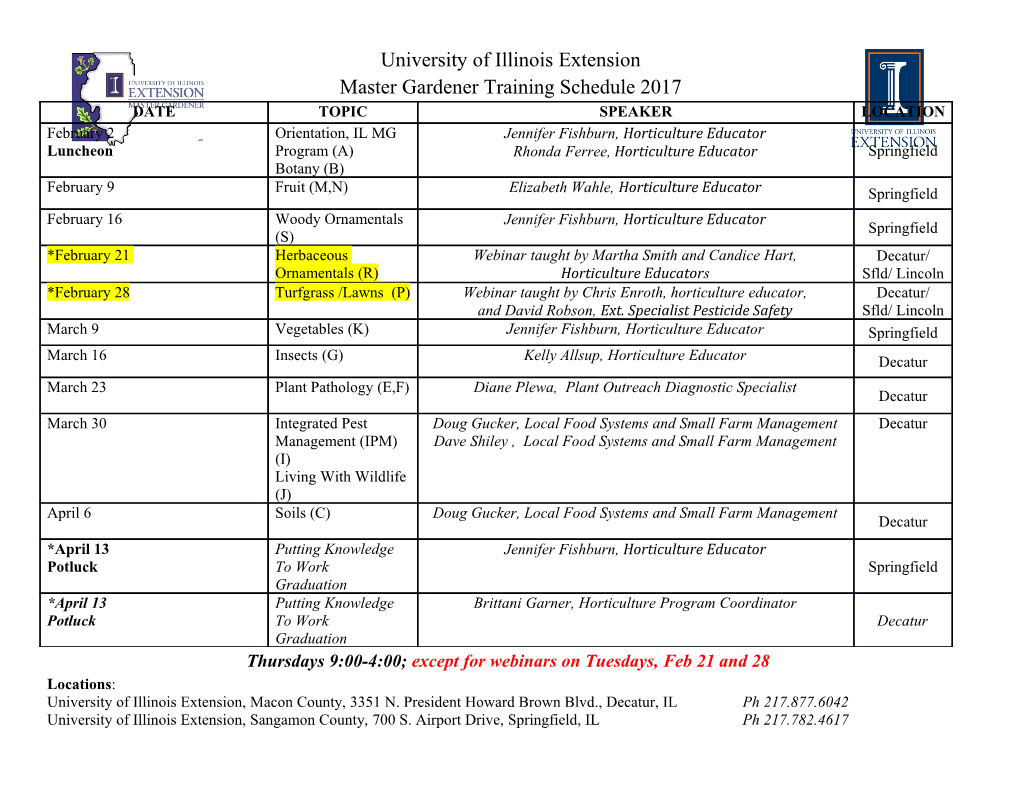
Home Search Collections Journals About Contact us My IOPscience Significance tests on the output power of a thermally driven rotary nanomotor This content has been downloaded from IOPscience. Please scroll down to see the full text. 2017 Nanotechnology 28 215705 (http://iopscience.iop.org/0957-4484/28/21/215705) View the table of contents for this issue, or go to the journal homepage for more Download details: IP Address: 130.56.64.29 This content was downloaded on 04/05/2017 at 15:52 Please note that terms and conditions apply. Nanotechnology Nanotechnology 28 (2017) 215705 (8pp) https://doi.org/10.1088/1361-6528/aa6961 Significance tests on the output power of a thermally driven rotary nanomotor Likui Yang1, Kun Cai1,2,3, Jiao Shi1 and Qing H Qin2,3 1 College of Water Resources and Architectural Engineering, Northwest A&F University, Yangling 712100, People’s Republic of China 2 Research School of Engineering, the Australian National University, ACT, 2601, Australia E-mail: [email protected] and [email protected] Received 2 March 2017, revised 19 March 2017 Accepted for publication 27 March 2017 Published 4 May 2017 Abstract Many factors canhave a significant influence on the output power of a thermallydriven rotary nanomotor made ofcarbon nanotubes (CNTs). Making use of a computational molecular dynamics approach, we evaluate for the first time the output power of a nanomotor,consideringsome of the main factors including temperature, the diameter of the rotor and the number of IRD atoms (N) on thestator. When applying extra-resistant torque tothe rotor to let the stable value of the rotational frequency of the rotor fluctuatenearzero, the value of the resistant torque can be considered as the output power of the rotor. The effects of these factors on the output power of a motor are roughly predicted via a fitting approach. Using stepwise regression analysis, we discover that N has the greatest influence on the output power. The second and the third main factors that affect the output power of a nanomotor are the diameter of the rotor, and the interaction between N and the diameter, respectively. To improve the output power of a nanomotor, one can place more IRD atoms in the system and/or employ CNTs with larger diameters. Supplementary material for this article is available online Keywords: nanomotor, nanotube, significance test, regression model, output power (Some figures may appear in colour only in the online journal) 1. Introduction multi-walled CNTs forthe shaft of the rotor. Fennimore et al [2] used CNTs to support a plate which can be made to rotate In recent years, thefabrication of nanodevices [1–5] from low- by applying direct current. Bourlon et al [17] arranged a plate dimensional materials [6–10] has attractedmore and more on the outer tube of multi-walled CNTs, wherebythe plate can attentionfrom researchers. It should be mentioned that the be driven to rotate by an external electric field. In the work by Nobel prize for chemistry in 2016 was issued to three scientists Barreiro et al [18], CNTs were employed as an axis through fortheir contributionstomolecular machines [11].Carbon which the motion of a cargo can be driven by a thermal gradient nanotubes (CNTs), since being discovered bytransmission along the tube axis. Besides experiments, amolecular dynamics electron microscopy in the early 1990s [7], have been studied simulation approach is also a powerful tool for investigating widely fortheirphysical properties. Due to their excellent high this category of nanodevices [19, 20, 27]. modulus [12], high ductility [13]and ultra-low inter-tube fric- In 2014, the thermally-driven rotary nanomotor (TRnM) tion [1, 14–16], CNTs are ideal candidate materials in fabri- was created usingdouble-walled CNTs[28]. In the nanomotor, cating various nanomachines such as nanomotors [1, 2, 17–21], the outer shell of the CNTis fixed as astator after relaxation, nano strain sensors [22] and nano-oscillators [23–27].Inpart- and the inner tube is actuated to rotate at∼100 GHz. The icular, Cumings and Zettl [1] developed a nanomotor by using mechanism involves the asymmetry of the stator leading to a torque moment on the rotor during their thermal vibration- 3 Authors to whom any correspondence should be addressed. induced collision. When the double-walled CNTs with a radii 0957-4484/17/215705+08$33.00 1 © 2017 IOP Publishing Ltd Printed in the UK Nanotechnology 28 (2017) 215705 L Yang et al difference of 0.335 nm (theequilibrium distance between on the condition that the stators have lost geometric symmetry, neighboring tubes) are chosen to act as a TRnM, the rotational e.g., by setting IRD on some end carbon atoms on the stators frequency of the rotor is commonly lower than that of the (e.g., figure 1(b)). If we apply a torsional moment on the left nanomotor with the same stator,but the radii difference end of the rotor and the directional sense of the moment is isnear0.335 nm. The reason for thisis that the collision opposite to that of the rotation, the value of ω wouldchange. between the stator and the rotor is reduced when the radii For example, if the value of Mr is low, the value of ω will- difference is much lower or higher than that at equilibrium. It reduce,but the directional sense remainsunchanged. If we should be mentioned that the TRnM from the double-walled provide a higher value of Mr on the rotor, it may rotate in CNTs with unsaturated ends may stop rotating suddenly, even theopposite way. Hence, we predict that there must exist a if it has a longstable rotation time [29]. From molecular value of M which leads to ω=0 on time average. Corre- dynamics experiments, the reason was found that the drastic r spondingly, the value of M is called a critical value and is vibration with high centrifugal force on the atoms attached r labeled as M cr. tothe rotor may leadto the formation ofnew carbon-carbon r In the present study, the major task is to find the sig- covalent bonds between the rotor and the stator. Under thi- fi sextremely strong bonding interaction, the rotational speed of ni cance of one factor or multiple factors on the output power ( cr) the rotor drops tozero within a few picoseconds. In early 2016, torque, reaction quantity of Mr of the thermally driven fi amodel of the TRnM with a specified rotational direction was rotary nanomotor, as shown in gure 1. Hence, before con- presented [30]. In the model, one or more unsaturated atoms at ducting a factor analysis, the critical value of the resistant cr fi oneend of the stator areinitially set to have an inwardly radial torque (Mr ) should be obtained under speci c conditions. In deviation (IRD). When the collision between the rotor and a factor analysis, fourmajor steps are required: stator happens, torque with a direction corresponding to the (a) Choose samples for analysis according to the factor to type of IRD is generated to actuate the rotation of the rotor. be estimated. For instance, when the factor is temper- Due to the extremely small size of the nanomotor and ultra- ature, we need to obtain the critical values of torque of highspeed of the rotor, observation of the rotation is highly the same system at a different temperature. challenging. To deal with this difficulty, we suggestedadding a (b) Build the related models involved in the factor analysis. piece of graphene nanoribbon tothe rotor [31].Whenthe (c) Obtain the critical value of resistant torque for each case rotoris actuated, the nanoribbon will expand from the tube. of simulation by abi-section method. The size of the rotor is enlarged and the rotational speed of the ( ) d Collect the critical values of the resistant torque of the rotor reduced, simultaneously. This phenomenon is useful for ( ) experimental observation of the rotation. Based on thisidea, system with respect to different values of the factor s , we proposed a probe-based approach to measure the rotational and carry out factor analysis using a software statistical ( ) [ ] frequency of a nanomotor [32, 33]. analysis system SAS 35 . Having completed the measurement of the rotation, we now focuson the output power of theTRnM from CNTs when considering the function of the former in driving the 2.3. Method for molecular dynamics simulation motion of other components in a nanomachine. In the experiments above, the stable rotational frequency (SRF) of The simulation is carried out in an open source code large-scale the rotor still shows high dependence onfactors such as the atomic/molecular massively parallel simulator (LAMMPS) geometry of the nanomotor and the temperature of the system. [36]. The interaction among the carbon and/or hydrogen atoms In the present study, we investigate the effects offactors is described by the AIREBO potential [37]. In each simulation, including temperature, the diameter of the rotorand the the time step is 0.001 ps and there are fivemajor stepsrequired: number ofIRD atoms on the output power of the TRnM, as Step (1) Build the geometry model of the system, adjust shown in figure 1. the positions of the IRD atoms at the external ends of the stators. Step (2) Reshape the nanosystem by minimizing the 2. Models and methodology potential energy of the system using the steepest decent algorithm with atolerance of 10−4 and 10−6 units for energy 2.1. Models of thermallydriven nanomotor and force, respectively. The maximal iterations are 100 and 1000, respectively. See figure 1. Step (3) Initiate the velocities of the atoms on the system with a specified temperature, e.g., 300 K.
Details
-
File Typepdf
-
Upload Time-
-
Content LanguagesEnglish
-
Upload UserAnonymous/Not logged-in
-
File Pages9 Page
-
File Size-