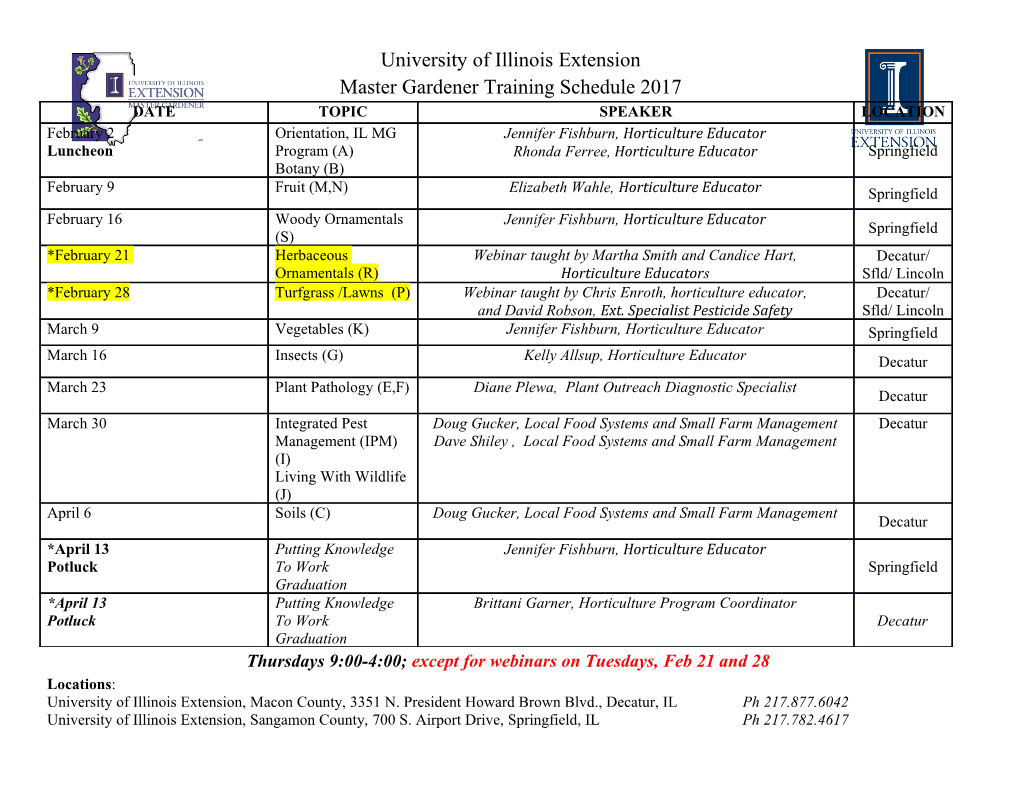
Patentamt JEuropaischesEuropean Patent Office Publication number: 0 240635 B1 Office europeen des brevets EUROPEAN PATENT SPECIFICATION Date of publication of the patent specification : mtci- C01B 25/30 07.03.90 Application number: 86304443.4 Date of filing: 10.06.86 Process for the manufacture of disodium phosphate. Priority: 30.03.86 IL 78325 Proprietor: NEGEV PHOSPHATES LTD., P.O. Box 435, Dimona(IL) Date of publication of application: 14.10.87 Bulletin 87/42 Inventor: losef, Alexander, 5/12 Hakanaim St., Arad(IL) Inventor: Bar-On, Menachem, 53/15 Elazer Ben-Yair St., Arad(IL) Publication of the grant of the patent: 07.03.90 Bulletin 90/10 Representative: Bankes, Stephen Charles Oigby et al, BARON & WARREN 18 South End Kensington, London Designated Contracting States: W8SBU(GB) AT BE CH DE FR GB IT LI NL References cited: FR-A-655062 GB-A-228220 US-A-3697246 US-A-4191734 m 10 CO <o o CM Q Note: Within nine months from the publication of the mention of the grant of the European patent, any person may give notice to the European Patent Office of opposition to the European patent granted. Notice of opposition shall be filed in a written reasoned gk statement. It shall not be deemed to have been filed until the opposition fee has been paid (Art. 99(1) European patent SS convention). ACTORUM AG EP 0 240 635 B1 Description The present invention relates to an improved process for the manufacture of disodium phosphate. More particularly the invention relates to an improved process for the manufacture of hydrated diso- 5 dium phosphate of a high purity, which does not involve the use of organic solvents. Disodium phosphate is an important industrial chemical used in detergent industry and other products. It is normally made by reacting H3PO4 with alkali metal hydroxide -or carbonate. The naturally occurring alkali metals, such as sodium or potassium, are most commonly mined and recovered as a salt, such as chloride. Thus in order to create phosphoric acid with an alkali metal hydroxide or carbonate, the alkali 10 metal must first be converted to the corresponding hydroxide or carbonate. It is thus readily apparent that a process for penetrating disodium phosphate which employs NaCI directly, eliminating expensive in- termediate processing, would be a highly desirable and economically attractive process. In principle, the primary reaction between sodium chloride and phosphoric acid may result in a sodium phosphate salt, such as NaH2PO4 and hydrochloric acid. The practice of this reaction by heating the 15 two reagents, will result in the expulsion of hydrogen chloride, but at the same time would cause a dehy- dration of the orthophosphate to form the metaphosphate salt (NaPC>3). Furthermore, this system is ex- tremely corrosive at the temperatures necessary to expel the hydrogen chloride. The corrosion problem is quite severe and can not be readily overcome and will also result the incorporation of various impuri- ties in the product. 20 In order to obviate the corrosion problem, some processes were suggested in the last twenty years, in which organic solvents are utilized for removing the hydrogen chloride and thus temperatures in the range of 40 to 100 degrees centigrade may be utilized. Thus according to U.S. Patent Number 3,443,889 a method is described for the manufacture of disodium phosphate, from sodium chloride and phosphoric acid in the presence of a water immiscible primary alkyl amine containing from 8 to 22 carbon atoms and a 25 water immiscible liquid organic solvent. The organic phase containing the hydrogen chloride is separated from the reaction mixture, the amine being regenerated by treating the organic liquid with an alkaline rea- gent and its recovery from the remainder reaction mixture. Although the process seems to be quite inter- esting from a theoretical point of view, in practice its exploitation is quite doubtful, in view of the expen- sive solvents required and losses thereof which are inherent during the extraction and regeneration. It 30 should be borne in mind that large amounts of solvents are required in the process, these solvents hav- ing molecular weights in the range of 180 to 315, and even small losses of solvent will increase apprecia- ble the overall costs of the process. According to U.S. Patent Number 3,661,513 sodium phosphate hav- ing the formula Na1.5H1.5PO4 is obtained by reacting sodium chloride with phosphoric acid in the pres- ence of a secondary or tertiary amine containing from 6 to 24 carbon atoms. The steps are quite similar 35 to those of the previous patent and has the same disadvantages. In order to complete the state of the art in respect to the manufacture of sodium phosphate, it should perhaps be interesting to mention its preparation from sodium chloride and phosphoric acid (as de- scribed in Israeli Patent Number 9539) carried out at ambient temperature. According to this process, a great excess of phosphoric acid is utilized, and the mixture of phosphoric acid and hydrochloric acid is 40 removed by solvent extraction using water immiscible organic solvents. The sodium phosphate salt is crystallized from the aqueous solution resulted after removal of the acids. The process is indeed quite elegant, but its implementation on a commercial scale is questionable particularly in view of the high costs involved concerning the organic solvents and energy required to separate the phosphoric acid from hy- drochloric acid. 45 It is an object of the present invention to provide a simple process for the manufacture of disodium phosphate. It is another object of the present invention to provide a simple process for the manufacture of disodium phosphate which does not require temperatures above 100 degrees C and thus avoids com- pletely the danger of metaphosphate production. Thus the invention consists of a process for the manu- facture of disodium phosphate which comprises the steps of: (a) reacting monosodium sulfate with a 50 phosphate constituent selected from the group consisting of phosphate rock, dicalcium phosphate or mixtures thereof in the presence of phosphoric acid, and separating the formed calcium sulfate; (b) a two stage neutralization of the filtrate obtained in step (a), first by a calcium constituent selected from calci- um carbonate, calcium hydroxide or mixtures thereof and separating the formed dicalcium phosphate, fol- lowed by a further neutralization by an alkali sodium constituent selected from sodium hydroxide, sodium 55 carbonate and sodium bicarbonate or mixtures thereof at a pH in the range of 8.0 to 9.5; and (c) crystal- lizing from the filtrate obtained in step (b) substantially pure hydrated disodium phosphate. The phos- phoric acid to be present at the end of step (a) should be in the range of 5%-20% by weight of the total P2O5 present the system. Above 20% the process is still operable, but any excess above this value is actually a waste of P2O5. The concentration of the P2O5 in the above mixture of phosphoric acid and so- 60 dium salt is not critical and can be selected in a very broad range. It was found that by using the above steps, the product obtained will not be accomplished by phosphoric acid (double salt monosodium phos- phate-phosphoric acid) as encountered in the prior art methods. One of the characteristics of the system is the absence of monocalcium phosphate. This is a result of an excess of the sulfate ion which is present therein, which excluded the formation of monocalcium phos- 65 EP 0 240 635 B1 phate, due to the formation of the insoluble calcium sulfate. The excess of sulfate ion has also a benefi- cial effect on the generation of well-shaped crystals of gypsum with the consequence of their easy fil- tration. The starting reagent for the present invention is momosodium sulfate. As known this salt is easily ob- 5 tained in the reaction between sodium chloride and sulfuric acid occurs in two distinct steps: (1) NaCI + H2SO4 -> NaHSO4 + HCI (2) NaCI + NaHSO* -> Na2SO4 + HCI The first reaction for the formation of monosodium phosphate occurs smoothly and is much more easi- 10 ly performed (being exothermic) than the second one of disodium sulfate formation (which is endother- mic). The proper conditions for the preparation of monosodium sulfate are well known from the prior art, its preparation being not considered part of the present invention. As known, the temperatures at which it takes place are low enough to permit the use of corrosion-resistant plastics, thus reducing the capital costs. 15 The temperatures involved in the process according to the present invention are generally in the range of between 40 to 100 degrees centigrade and preferably in the range of between 60 to 80 degrees centigrade. The above relatively low temperatures range, compared with the temperatures of about 160 degrees centigrade mentioned in the prior art, excludes completely the possibility of co-producing the in- soluble sodium metaphosphate. As known, the prior art references are utilizing temperatures above 160 20 degrees C in order to complete the expulsion of HCI resulting from the reaction of sodium chloride with phosphoric acid: (3) H3PO4 +2NaCI -> Na2HPC-4 + 2HCI Other advantages from utilizing the lower temperature range in the process according to the present invention are of course connected with the saving of energy, as well as with the less corrosive condi- 25 tions which prevail during the process for the equipment. According to a preferred embodiment, which enables to obtain a maximum yield of P2O5 and Na2O re- covery, it is suggested to carry out the first step according to the present invention in two or more stag- es which also enables a better control of the process.
Details
-
File Typepdf
-
Upload Time-
-
Content LanguagesEnglish
-
Upload UserAnonymous/Not logged-in
-
File Pages8 Page
-
File Size-