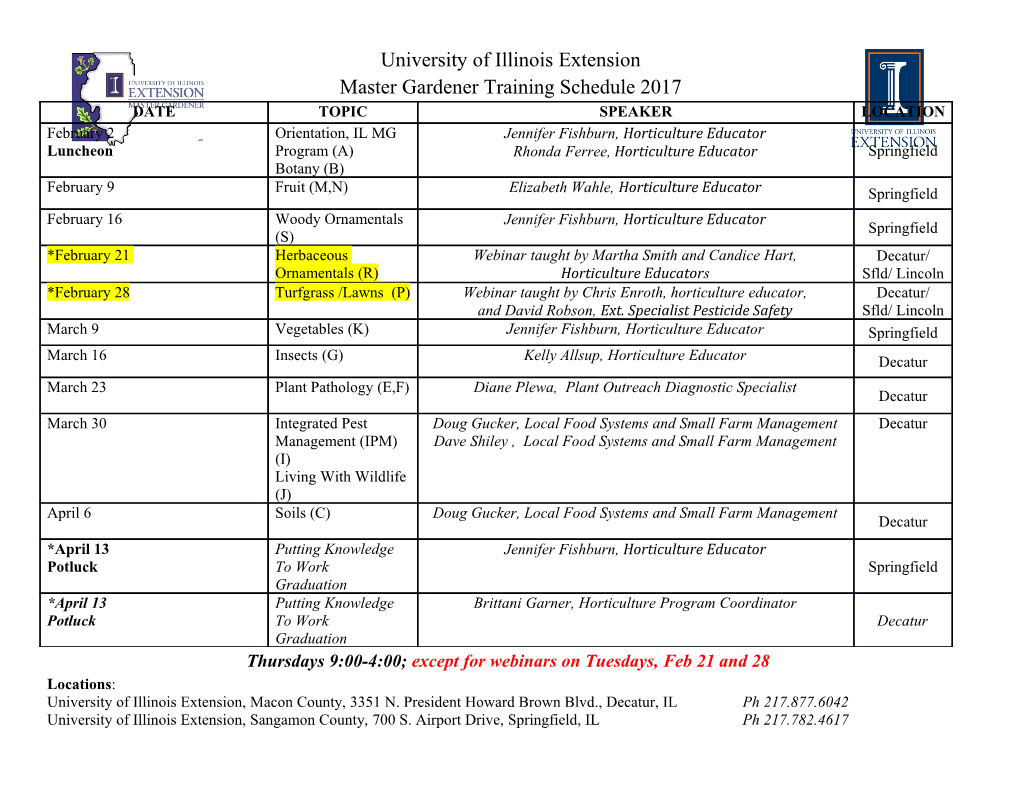
H 1 active anti-roll bar control to prevent rollover of heavy vehicles: a robustness analysis van Tan Vu, Olivier Sename, Luc Dugard, Peter Gáspár To cite this version: van Tan Vu, Olivier Sename, Luc Dugard, Peter Gáspár. H 1 active anti-roll bar control to prevent rollover of heavy vehicles: a robustness analysis. SSSC 2016 - 6th IFAC International Symposium on System Structure and Control, Jun 2016, Istanbul, Turkey. pp. 099 – 104, 10.1016/j.ifacol.2016.07.503. hal-01314500 HAL Id: hal-01314500 https://hal.univ-grenoble-alpes.fr/hal-01314500 Submitted on 11 May 2016 HAL is a multi-disciplinary open access L’archive ouverte pluridisciplinaire HAL, est archive for the deposit and dissemination of sci- destinée au dépôt et à la diffusion de documents entific research documents, whether they are pub- scientifiques de niveau recherche, publiés ou non, lished or not. The documents may come from émanant des établissements d’enseignement et de teaching and research institutions in France or recherche français ou étrangers, des laboratoires abroad, or from public or private research centers. publics ou privés. H1 active anti-roll bar control to prevent rollover of heavy vehicles: a robustness analysis Van-Tan Vu ∗ Olivier Sename ∗ Luc Dugard ∗ Peter Gaspar ∗∗ ∗ Univ. Grenoble Alpes, GIPSA-lab, F-38402 Grenoble Cedex, France CNRS, GIPSA-lab, F-38402 Grenoble Cedex, France. E-mail: fVan-Tan.Vu, olivier.sename, [email protected] ∗∗ Systems and Control Laboratory, Institute for Computer Science and Control, Hungarian Academy of Sciences, Kende u. 13-17, H-1111 Budapest, Hungary. E-mail: [email protected] Abstract: Rollover of heavy vehicle is an important road safety problem world-wide. Although rollovers are relatively rare events, they are usually deadly accidents when they occur. In order to improve roll stability, most of modern heavy vehicles are equipped with passive anti-roll bars to reduce roll motion during cornering or riding on uneven roads. This paper proposes an H1 approach to design active anti- roll bars using the yaw-roll model of a single unit heavy vehicle. The control signals are the torques generated by the actuators at the front and rear axles. Simulation results in both frequency and time domains are provided to compare two different cases: passive anti-roll bars and H1 active anti-roll bars. It is shown that the use of two H1 active (front and rear) anti-roll bars drastically improves the roll stability of the single unit heavy vehicle to prevent rollover. Keywords: Vehicle dynamics, Active anti-roll bar control, Rollover, Roll stability, H1 control, µ-analysis. 1. INTRODUCTION steering, electronic brake mechanism,...) but they are beyond the scope of this paper. 1.1 Context The disadvantage of the active anti-roll bars is that the maxi- mum stabilizing moment is limited physically by the relative The rollover is a very serious problem for heavy vehicle safety, roll angle between the body and the axle (Sampson and Cebon which can result in large financial and environmental conse- (2002)). quences. The aim of preventing rollovers is to provide the vehicle with an ability to resist overturning moments generated 1.2 Related works during cornering and lane changing to avoid obstacle. In order to improve roll stability, most of modern heavy ve- Some of the control methods applied for active anti-roll bar hicles are equipped with passive anti-roll bars to reduce roll control on heavy vehicle are briefly presented below: motion. The passive anti-roll bar force is a function of the differ- a- Optimal control: Sampson et al (see Sampson and Cebon ence between right and left suspensions deflections. The force (1998), Sampson and Cebon (2002)) have proposed a state is applied by the bar on each side of the vehicle so that the left feedback controller which was designed by finding an optimal force has the same magnitude but the opposite direction than the controller based on a linear quadratic regulator (LQR) for sin- right one. The passive anti-roll bar has the advantages to reduce gle unit and articulated heavy vehicles. They used the control the body roll acceleration and roll angle during single wheel torques acting between the axle groups and the sprung mass as lifting and cornering maneuvers. However, the passive anti-roll the input control signal. bar also has drawbacks. During cornering maneuvers, anti-roll The LQR has been also applied to the integrated model includ- bar transfers the vertical forces of one side of suspension to the ing an electronic servo-valve hydraulic damper model and a other one, creating therefore a moment against lateral force. yaw-roll model of a single unit heavy vehicle. The input control In order to overcome the drawbacks of the passive anti-roll bar signal is the input current of the electronic servo-valve (Vu systems, several schemes with possible active intervention into et al., 2016). the vehicle dynamics have been proposed. One of these meth- b- Neural network control: Boada et al. (2007) have proposed ods employs active anti-roll bars, that is, a pair of hydraulic a reinforcement learning algorithm using neural networks to actuators which generate a stabilizing moment to balance the improve the roll stability for a single unit heavy vehicle. The overturning moment. Lateral acceleration makes vehicles with input control signals are the torques at the axles. However this conventional passive suspension tilt out of corners. The center kind of approach is not suitable for embedded control. of the sprung mass shifts outboard of the vehicle centerline, c- Robust control (LPV): Gaspar et al (see Gaspar et al. which creates a destabilizing moment that reduces roll sta- (2005a), Gaspar et al. (2004) and Gaspar et al. (2005b)) have bility. The lateral load response is reduced by active anti-roll applied Linear Parameter Varying (LPV) for the active anti-roll bars which generate a stabilizing moment to counterbalance bar combined with an active brake control on the single unit the overturning moment in such a way that the control torque heavy vehicle. They also used a Fault Detection and Identifica- leans the vehicle into the corners (see Sampson and Cebon tion (FDI) filter, which identifies different actuator failures. The (2003), Gaspar et al. (2004)). Other methods can be used (active forward velocity is considered as the varying parameter. 1.3 Paper contribution Table 1. Parameters of the yaw-roll model (see Gaspar et al. (2004)) Based on the model presented in (Gaspar et al. (2004)), this paper proposes an H1 control method for active anti-roll bar, Symbols Description Value Unit and focuses on the uncertainties due to the vehicle forward m Sprung mass 12487 kg velocity and the sprung mass variations. Hence the following s mu; f Unsprung mass on the front axle 706 kg contributions are brought: mu;r Unsprung mass on the rear axle 1000 kg - We design a H1 robust controller for active anti-roll bar m The total vehicle mass 14193 kg Km system on the single unit heavy vehicle. The aim is to maximize v Forward velocity - h Km the roll stability to prevent rollover of heavy vehicles. The nor- vwi Components of the forward velocity - h malized load transfer and the limitation of the torque generated h Height of CG of sprung mass from roll axis 1.15 m by actuators in various maneuver situations are considered. hu;i Height of CG of unsprung mass from ground 0.53 m r Height of roll axis from ground 0.83 m - Performance analysis made in frequency domain shows that m ay Lateral acceleration - 2 the H1 active anti-roll bar control drastically reduces the nor- s β Side-slip angle at center of mass - rad malized load transfer compared to the passive anti-roll bar. It Heading angle - rad also shows that the H1 active anti-roll bar control is robust w.r.t. ˙ rad Yaw rate - s the forward velocity and the sprung mass variation. The robust α Side slip angle - rad stability analysis of the designed controller is performed using φ Sprung mass roll angle - rad the µ- analysis method. φt;i Unsprung mass roll angle - rad - In time domain, we use a double lane change as the heavy δ f Steering angle - rad vehicle maneuver. The simulation results indicate that the Root ui Control current - A kN Mean Square (RMS) of the H active anti-roll bar control have C f Tire cornering stiffness on the front axle 582 rad 1 kN Cr Tire cornering stiffness on the rear axle 783 rad dropped from 15% to 50% compared to the passive anti-roll kNm k f Suspension roll stiffness on the front axle 380 rad bar with all of the forward velocity considered in interval from kNm kr Suspension roll stiffness on the rear axle 684 rad 50Km=h to 110Km=h. kN b f Suspension roll damping on the front axle 100 rad kN br Suspension roll damping on the rear axle 100 rad The paper is organised as follows: Section 2 gives the model kNm kt f Tire roll stiffness on the front axle 2060 rad of a single unit heavy vehicle. Section 3 presents the design of kNm ktr Tire roll stiffness on the rear axle 3337 rad 2 the passive anti-roll bar. Section 4 gives the H1 robust control Ixx Roll moment of inertia of sprung mass 24201 kgm 2 synthesis to prevent rollover of heavy vehicles. Section 5 illus- Ixz Yaw-roll product of inertial of sprung mass 4200 kgm 2 trates the robustness analysis in the frequency domain using the Izz Yaw moment of inertia of sprung mass 34917 kgm µ- tool.
Details
-
File Typepdf
-
Upload Time-
-
Content LanguagesEnglish
-
Upload UserAnonymous/Not logged-in
-
File Pages9 Page
-
File Size-